图书介绍
船舶工艺技术pdf电子书版本下载
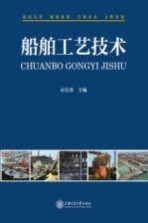
- 应长春主编 著
- 出版社: 上海:上海交通大学出版社
- ISBN:9787313091697
- 出版时间:2013
- 标注页数:1068页
- 文件大小:478MB
- 文件页数:1089页
- 主题词:船舶技术
PDF下载
下载说明
船舶工艺技术PDF格式电子书版下载
下载的文件为RAR压缩包。需要使用解压软件进行解压得到PDF格式图书。建议使用BT下载工具Free Download Manager进行下载,简称FDM(免费,没有广告,支持多平台)。本站资源全部打包为BT种子。所以需要使用专业的BT下载软件进行下载。如 BitComet qBittorrent uTorrent等BT下载工具。迅雷目前由于本站不是热门资源。不推荐使用!后期资源热门了。安装了迅雷也可以迅雷进行下载!
(文件页数 要大于 标注页数,上中下等多册电子书除外)
注意:本站所有压缩包均有解压码: 点击下载压缩包解压工具
图书目录
第一篇 概论篇 3
第1章 船舶工艺技术概论 3
1.1船舶工艺技术内涵 3
1.2船舶工艺技术的地位和作用 3
1.2.1船舶工艺技术的地位 3
1.2.2船舶工艺技术的作用 4
1.3造船技术沿革和船舶产品分类 5
1.3.1造船技术沿革 5
1.3.2造船产业的兴起与转移 6
1.3.3现代船舶产品分类 7
1.4船舶工艺技术的发展进程 7
1.4.1现代造船工艺技术的发展 7
1.4.2我国造船工艺技术的发展历程 11
1.5船舶工业工艺技术体系 14
1.5.1船舶工艺技术体系 15
1.5.2船舶制造工艺技术体系的演化和特征 17
1.5.3“船舶工业科学技术体系”中的船舶工艺技术体系 18
1.6我国船舶工艺技术现状与水平分析 24
1.6.1现状与差距 24
1.6.2造船技术水平评价和分析 25
1.7船舶工艺技术发展思路、目标和措施 27
1.7.1发展思路 27
1.7.2发展原则 27
1.7.3发展目标 27
1.7.4措施和建议 28
第二篇 技术篇 33
第2章 现代造船模式 33
2.1概述 33
2.1.1造船模式的内涵及其演变过程 33
2.1.2现代造船模式的内涵及其概念形成的背景 34
2.2现代造船模式的理论基础及其主要特征 37
2.2.1现代造船模式的理论基础 37
2.2.2现代造船模式的特征 40
2.3现代造船模式的构成要素及其相关要求 41
2.3.1面向生产的设计技术 41
2.3.2均衡连续的作业流程 43
2.3.3严密精细的工程管理 44
2.3.4高效合理的生产组织 48
2.3.5信息集成 52
2.4加快建立现代造船模式的指导意见 54
2.4.1指导方针 54
2.4.2基本方向和总体要求 54
2.4.3实施要点 55
2.4.4相关保障措施 57
2.5现代造船模式的发展趋势 58
第3章 造船方法和造船主流程 59
3.1概述 59
3.2造船方法分类及特征 59
3.2.1造船方法分类 59
3.2.2主要造船方法特征 60
3.3船体建造方法 61
3.3.1船体建造方法的选择 62
3.3.2分段(总段)建造方法 63
3.3.3船台(坞)搭载(建造)方法 69
3.3.4船体建造阶段的划分和作业内容 72
3.4舾装方法 72
3.4.1舾装方法分类 72
3.4.2舾装作业阶段划分 73
3.4.3区域舾装法 75
3.5涂装方法 76
3.5.1区域涂装和作业阶段 76
3.5.2涂装计划和生产管理 77
3.6造船作业主流程 77
3.6.1造船作业主流程的内涵 77
3.6.2造船作业主流程的演变 79
3.6.3造船总装作业主流程 79
3.6.4船厂造船作业主流程布置基本形式 81
3.7流程再造和流程优化 81
3.7.1产品导向型工程分解(PWBS) 81
3.7.2船体加工装焊流程优化 82
3.7.3壳舾涂一体化作业流程 85
3.8造船方法和造船主流程发展趋势 86
第4章 造船生产设计 88
4.1概述 88
4.1.1生产设计的由来 88
4.1.2生产设计的内涵 88
4.1.3生产设计的基本原则与设计理念 89
4.1.4生产设计的主要特点和作用 90
4.2船舶设计与工程计划管理相结合的设计工作模式 91
4.2.1船舶设计阶段的划分 92
4.2.2船舶设计各阶段的设计协调方式 92
4.2.3船舶设计与工程计划管理的结合方式 94
4.3生产设计前的准备 98
4.3.1作业阶段、作业区域和作业类型的划分 98
4.3.2按作业性质、区域划分的生产设计组织机构 100
4.3.3生产设计标准体系 100
4.3.4建立船舶建造编码体系 103
4.3.5计算机辅助生产设计软硬件的配置 107
4.4船体生产设计 109
4.4.1船体生产设计的内涵及基本要求 109
4.4.2船体生产设计的主要内容 110
4.4.3船体生产设计工作图的出图模式 113
4.4.4船体生产设计的程序与方法 117
4.5舾装生产设计及舾装综合布置 118
4.5.1舾装生产设计概述 118
4.5.2舾装综合布置的内涵及其主要作用 119
4.5.3舾装综合布置的主要内容 120
4.5.4各专业在综合布置中的相互关系 123
4.5.5舾装综合布置的设计程序与方法 124
4.6舾装托盘及托盘化设计 127
4.6.1托盘的定义与划分 127
4.6.2托盘管理的基本概念与管理流程 129
4.6.3托盘化设计的主要内容 131
4.6.4托盘化设计的程序与方法 133
4.7壳舾涂一体化分段的生产设计 136
4.7.1壳舾涂一体化分段的内涵与作业流程 136
4.7.2壳舾涂一体化分段完工技术状态的设定 136
4.7.3壳舾涂一体化分段的生产设计内容 137
4.7.4壳舾涂一体化分段的生产设计方法 138
4.8生产设计技术的发展趋势 142
第5章 造船精度管理技术 146
5.1概述 146
5.1.1精度管理的内涵和作用 146
5.1.2船体建造精度管理的发展过程 147
5.1.3船体建造精度管理体系 148
5.1.4船体建造精度管理的关联技术 150
5.2船体建造精度管理的基础理论和方法 151
5.2.1基础理论 151
5.2.2基本方法 153
5.3船体建造精度标准 153
5.3.1名词术语定义 153
5.3.2标准的分类 153
5.3.3标准的作用 154
5.3.4标准的制订 156
5.3.5精度标准内容 157
5.4船体建造精度控制 162
5.4.1船体精度控制系统 162
5.4.2船体结构的尺寸基准 169
5.4.3船体建造精度过程控制 171
5.4.4重点分段精度控制实例 177
5.5船体建造尺寸精度补偿 180
5.5.1精度补偿的先决条件和经济性原则 180
5.5.2精度补偿的方法和推荐值 181
5.6船体建造精度检测技术 186
5.6.1船体精度检测技术的发展过程 186
5.6.2检测工具的分类和使用 186
5.6.3船体建造精度检测方法 187
5.6.4全站仪检测和应用 188
5.7精度管理技术发展趋势 192
第6章 船舶制造数字化技术 194
6.1概述 194
6.1.1船舶制造数字化技术的内涵 194
6.1.2船舶制造数字化技术的发展历程 197
6.1.3船舶制造数字化技术的国内外发展概况 197
6.1.4现代造船模式与数字化技术 201
6.2船舶制造数字化技术的理论与技术基础 201
6.2.1现代制造的基本哲理 202
6.2.2数字化技术基础 204
6.3船舶制造数字化技术体系和集成系统功能架构 207
6.3.1船舶制造数字化技术体系 207
6.3.2船舶制造集成系统 209
6.4船舶生产设计系统 209
6.4.1船舶三维建模技术 209
6.4.2船体结构设计系统 211
6.4.3船舶管系设计系统 213
6.4.4船舶风管设计系统 214
6.4.5船舶电气设计系统 215
6.4.6船舶铁舾件设计系统 216
6.4.7船舶涂装生产设计系统 217
6.4.8焊接工艺规划系统 217
6.4.9船舶精度控制系统 218
6.5船舶虚拟制造技术 219
6.5.1虚拟制造技术 219
6.5.2船舶虚拟制造技术 220
6.6船舶制造数字化管理技术 223
6.6.1船舶制造数字化管理系统架构及功能 224
6.6.2船舶制造数字化管理系统的业务流程 225
6.7船舶制造数字化装备 232
6.7.1造船数字化装备发展综述 232
6.7.2典型数控装备 234
6.8船舶制造数字化的若干关键技术 237
6.8.1问题和关键 237
6.8.2船舶制造数字化关键技术 238
6.9船舶制造数字化技术发展趋势 242
第7章 船体构件加工工艺技术 246
7.1概述 246
7.1.1船体构件加工工艺体系 246
7.1.2船体构件加工方法分类 246
7.1.3船体构件加工分道技术 246
7.2船体放样工艺 247
7.2.1船体型面特点和船体放样的内涵 247
7.2.2船体放样工艺的演化和发展 248
7.2.3船体放样的内容 249
7.2.4船体数学放样(Mathematical Lofting) 251
7.3船体构件号料工艺 257
7.3.1船体构件号料的内涵 257
7.3.2船体构件的套料 258
7.3.3船体号料技术的演化和发展 258
7.4船体构件边缘加工(切割)工艺 258
7.4.1船体构件边缘加工(切割)工艺体系 258
7.4.2船体构件切割工艺 258
7.4.3焊接坡口加工工艺 265
7.5船体构件成形工艺 266
7.5.1船体构件成形加工工艺体系 266
7.5.2船体型材构件的成形工艺及装备 266
7.5.3船体板材构件的成形工艺及装备 271
7.6船体构件加工技术的发展趋势 276
7.6.1切割技术的发展趋势 276
7.6.2成形加工技术的发展趋势 277
第8章 船体装配工艺技术 279
8.1概述 279
8.1.1船体装配工艺技术体系 279
8.1.2船体分道建造技术 279
8.1.3船体装配作业技术依据 283
8.1.4船体建造基准及检测 284
8.2部件装配(小组立、中组立)工艺 286
8.2.1部件装配工艺流程 287
8.2.2部件装配基准 287
8.2.3板材拼装与焊接工艺 288
8.2.4 T型材装焊工艺 291
8.2.5框架装焊工艺 293
8.2.6平面型板架装焊工艺 295
8.2.7主、辅机基座装焊工艺 298
8.2.8艏柱和艉柱装焊工艺 301
8.3分段(大组立)装配工艺 303
8.3.1分段类型 303
8.3.2分段建造和装配方法 304
8.3.3底部分段装焊工艺 306
8.3.4舷侧分段装焊工艺 312
8.3.5顶(底)边水舱分段装焊工艺 316
8.3.6甲板型分段装焊工艺 319
8.3.7上层建筑分段装焊工艺 321
8.3.8艏、艉立体分段装焊工艺 322
8.3.9胎架 330
8.3.10分段装配焊接变形及控制技术 334
8.4分段总组(总组立)工艺 335
8.4.1立体分段总组 335
8.4.2上层建筑总组 339
8.5船体总装工艺技术 340
8.5.1船台(坞)总装(搭载)工艺流程 340
8.5.2船台(坞)总装(搭载)准备工作 341
8.5.3分/总段的船台(坞)搭载技术 343
8.5.4典型分/总段的船台(坞)搭载工艺流程和技术要领 345
8.5.5船台(坞)装配焊接变形及控制技术 348
8.6船体装配工艺技术的发展趋势 351
8.6.1按现代造船模式的要求建立总装造船工艺流程 351
8.6.2建立船体部件、分段机械化与自动化装焊流水线 351
8.6.3全面实施造船精度管理 351
8.6.4数字虚拟装配技术的研究和应用 352
8.6.5造船工法研究和应用 353
第9章 船舶焊接技术 355
9.1概述 355
9.1.1船舶焊接技术特点 355
9.1.2船舶焊接技术的演化历程 355
9.2船舶焊接技术体系和管理一体化流程 356
9.2.1船舶焊接技术体系 356
9.2.2船舶焊接工艺、设计、施工管理一体化流程 356
9.3船体结构用钢及匹配的焊接材料 358
9.3.1船体结构用钢 358
9.3.2船体结构用钢匹配的焊接材料 359
9.4船舶焊接工艺规程 360
9.4.1焊接工艺规程的内涵和作用 360
9.4.2焊接工艺规程编制的原则 360
9.4.3焊接工艺规程编制的依据 361
9.4.4焊接工艺规程的主要内容 361
9.5船舶焊接标准及体系 361
9.5.1船舶焊接标准现状 361
9.5.2船舶焊接标准体系 361
9.6船用材料焊接工艺性 362
9.6.1薄板及厚板结构焊接工艺性 362
9.6.2铝及其合金的焊接工艺性 366
9.6.3钛与钛合金焊接工艺性 369
9.7常规焊接工艺及装备 370
9.7.1手工电弧焊工艺及装备 370
9.7.2普通埋弧焊工艺及装备 371
9.8船舶高效焊接工艺及装备 373
9.8.1手工高效焊条焊接工艺及装备 373
9.8.2高效埋弧焊工艺及装备 374
9.8.3焊剂垫单面埋弧焊(RF法)焊接工艺及装备 376
9.8.4焊剂铜衬垫多丝单面埋弧焊(FCB法)焊接工艺及装备 378
9.8.5软衬垫单面埋弧焊(FAB法)焊接工艺及装备 383
9.8.6 CO2气保护焊焊接工艺及装备 389
9.8.7双丝单面MAG焊焊接工艺及装备 390
9.8.8 TIG、MIG焊工艺及装备 392
9.8.9气电垂直自动焊工艺及装备 395
9.8.10气电横向自动焊工艺及装备 399
9.9碳弧气刨工艺及设备 399
9.9.1碳弧气刨原理及应用 399
9.9.2碳弧气刨工艺参数 400
9.9.3碳弧气刨设备 400
9.10焊接质量管理 400
9.10.1焊接缺陷分类 400
9.10.2焊接变形及控制技术 401
9.10.3焊接接头缺陷及防止措施 404
9.10.4焊缝外观质量要求 410
9.10.5焊缝内部质量要求 411
9.11船舶焊接发展趋势 411
9.11.1船舶焊接技术发展面临的机遇与挑战 411
9.11.2船舶焊接技术发展趋势 411
9.11.3船舶焊接技术发展展望 412
9.11.4船舶焊接技术发展对策 414
第10章 船舶无损检测技术 416
10.1无损检测概述 416
10.1.1船舶无损检测技术的内涵 416
10.1.2船舶无损检测技术体系 416
10.1.3船舶无损检测技术人员资格的认证 417
10.2船舶无损检测标准 417
10.3船舶无损检测方法的选择 418
10.3.1材料表面或近表面检测方法 418
10.3.2全熔透焊接接头检测方法 418
10.3.3船体结构的无损检测 419
10.4船舶无损检测技术及设备 421
10.4.1船舶超声波检测工艺及设备 421
10.4.2船舶射线检测工艺及设备 429
10.4.3船舶磁粉检测工艺及设备 432
10.4.4船舶渗透检测工艺及设备 439
10.4.5船用复合材料(玻璃钢)无损检测技术 443
10.5无损检测新技术 446
10.5.1奥氏体不锈钢焊缝超声波检测 446
10.5.2相控阵超声波检测 447
10.5.3对接焊缝TOFD技术 447
10.5.4磁记忆检测技术 448
第11章 船舶舾装工艺技术 449
11.1概述 449
11.1.1舾装工艺的内涵 449
11.1.2船舶舾装工艺的演化 450
11.1.3舾装工艺技术体系 450
11.2区域舾装工艺 451
11.2.1单元组装工 艺(Unit Outfitting) 451
11.2.2分段舾装工艺(Section Outfitting; Block Outfitting) 452
11.2.3总段正反转舾装工艺 453
11.2.4盆舾装工艺(Plate Outfitting) 453
11.3专业舾装工艺 454
11.3.1机装工艺(Machinery Fitting) 455
11.3.2电装工艺(Electric Fitting) 463
11.3.3外舾装工艺(Deck Outfitting) 467
11.3.4内(舱室)舾装工艺(Accommodation Outfitting) 471
11.3.5特装工艺 477
11.4舾装托盘集配技术 481
11.4.1舾装托盘(Outfits Pallet)的形成 481
11.4.2托盘管理表 481
11.4.3集配中心 486
11.5舾装技术发展方向 487
第12章 船舶管件制造与安装工艺技术 488
12.1概述 488
12.2船舶管路系统 488
12.2.1含义 488
12.2.2分类及用途 489
12.3船用管材及管路附件和设备 490
12.3.1船用管子 490
12.3.2管路附件 492
12.3.3管系设备 494
12.4管系生产设计 496
12.4.1管系生产设计的基本要求 496
12.4.2管系综合布置 496
12.4.3管系综合布置图 497
12.4.4管系安装图的设绘 498
12.4.5管子零件图的设绘 498
12.4.6管子开孔委托及开孔图的设绘 503
12.4.7管理图表的编制 503
12.4.8管子加工与安装编码系统 504
12.5基于成组技术(GT)的管件加工生产系统 508
12.5.1基本原理 508
12.5.2管件成组加工工艺流程 508
12.5.3管件成组加工单元 509
12.5.4设备选择与车间布置 509
12.5.5管件生产管理 511
12.6管子加工工艺和工艺装备 515
12.6.1切割工艺与装备 515
12.6.2弯管工艺及装备 516
12.6.3校管 519
12.6.4焊接工艺与装备 522
12.6.5管子的化学清洗与表面防腐 526
12.6.6管子柔性加工生产线 528
12.7船舶管系安装工艺技术 530
12.7.1船舶管系安装工艺要求 530
12.7.2管系安装方法 536
12.7.3管系安装的技术要求 540
12.7.4管系安装的质量检验 541
12.8管系加工与安装技术的发展趋势 545
12.8.1管子材料与管系连接工艺 545
12.8.2管件成组生产系统和信息化管理 546
12.8.3现代造船模式对管系安装工艺的推动 547
第13章 船舶涂装工艺技术 548
13.1概述 548
13.1.1船舶的腐蚀与防护 548
13.1.2船舶涂装工艺技术体系 549
13.1.3船舶涂装技术的进步 551
13.2船舶涂料 552
13.2.1涂料 552
13.2.2船舶涂料及其分类 553
13.2.3车间底漆 553
13.2.4防锈涂料 554
13.2.5防污涂料 555
13.2.6船用面层涂料 557
13.2.7液舱涂料 558
13.3船舶除锈涂装工艺技术 559
13.3.1钢材表面处理工艺 559
13.3.2船舶涂装作业 564
13.3.3船舶涂装管理 567
13.3.4船舶涂装生产设计 569
13.3.5特种(殊)涂装 570
13.4船舶除锈涂装工艺装备 577
13.4.1钢材抛丸预处理装置 577
13.4.2抛丸技术的最新进展 578
13.4.3船体分段除锈涂装设施 579
13.4.4船舶除锈涂装辅助工艺装备 581
13.5 IMO保护涂层性能标准(PSPC) 582
13.5.1 PSPC标准适用范围、实施时间和基本目标 582
13.5.2涂层系统的基本要求 583
13.5.3涂层检查要求 584
13.5.4 PSPC标准的实施 585
13.5.5 IMO其他涂层性能标准 586
13.6船体阴极保护 588
13.6.1阴极保护原理及基本参数 588
13.6.2牺牲阳极保护 589
13.6.3外加电流阴极保护 590
13.7现代船舶涂装技术发展趋势 591
13.7.1适应国际船舶涂装的新要求 591
13.7.2适应绿色造船的要求 591
13.7.3适应快速造船的需求 592
第14章 船舶舱室绝缘工艺技术 595
14.1概述 595
14.1.1船舶舱室绝缘材料及工艺技术发展历程 595
14.1.2热的三种传递方式 595
14.2舱室绝缘材料 596
14.2.1舱室常用绝缘材料结构与导热系数 598
14.2.2舱室绝缘材料燃烧性能的三大参数 600
14.2.3舱室常用绝缘材料 602
14.3 SOLAS公约 607
14.3.1与舱室绝缘材料有关的SOLAS公约及相关规范 608
14.3.2 SOLAS公约及规范对舱室绝缘的规定和要求 608
14.4舱室绝缘工艺技术 610
14.4.1绝缘材料固定工艺 610
14.4.2一般舱室绝缘工艺技术 611
14.4.3特殊舱室绝缘工艺技术 613
14.5防火门和防火封堵 614
14.5.1防火门 614
14.5.2防火封堵 616
14.6 LNG船液化天然气储舱绝缘技术 617
14.6.1独立球型(MOSS)液货舱的绝缘技术 617
14.6.2 GTT薄膜型液货舱的绝缘技术 617
14.6.3 LNG日蒸发速率与绝热层材质及厚度控制 618
14.7舱室绝缘材料与工艺发展展望 619
14.7.1轻质节能与绿色环保型舱室绝缘材料的发展方向 619
14.7.2新型绝缘工艺技术展望 620
第15章 船用复合材料成形技术 621
15.1概述 621
15.1.1树脂基复合材料成形工艺概况 621
15.1.2复合材料成形工艺技术体系 622
15.1.3复合材料成形工艺技术特征和选择 625
15.2复合材料/树脂基复合材料/玻璃纤维增强塑料 625
15.2.1内涵 625
15.2.2特性 626
15.2.3命名和分类 626
15.2.4原材料 627
15.2.5模具、模具材料和脱模剂 630
15.3复合材料成形工艺 631
15.3.1手糊成形工艺 631
15.3.2喷射成形工艺 633
15.3.3树脂传递模塑成形(RTM) 635
15.3.4低压接触成形工艺 636
15.3.5模压成形工艺 638
15.3.6缠绕成形工艺 640
15.3.7拉挤成形工艺 642
15.3.8真空辅助成形工艺 645
15.3.9其他成形工艺 648
15.4复合材料船体结构制造技术 648
15.4.1 FRP/CM船艇船体的典型结构型式 648
15.4.2 FRP/CM船体的设计 649
15.4.3 FRP/CM船体的制造技术 649
15.5复合材料无损检测技术 650
15.5.1复合材料无损检测技术分类 650
15.5.2常用复合材料无损检测方法 651
15.6船用复合材料成形技术的发展趋势和展望 652
第16章 船舶下水(进出坞)及起重工艺技术 653
16.1概述 653
16.1.1我国船舶下水和起重技术的发展历程 653
16.1.2船舶下水设施和起重技术在船厂中的地位和作用 653
16.1.3船舶下水方式分类 654
16.2纵向倾斜船台滑道下水 654
16.2.1纵向倾斜船台滑道分类 654
16.2.2纵向倾斜船台滑道的主要尺度 654
16.2.3纵向倾斜船台滑道下水工艺 656
16.2.4纵向倾斜船台滑道下水工艺的改进 657
16.2.5气囊下水 657
16.3纵向机械化滑道上墩下水工艺 658
16.3.1纵向船排滑道 658
16.3.2纵向两支点滑道 661
16.3.3纵向斜船架滑道 662
16.3.4纵向栈桥滑道 663
16.3.5典型多船位纵向滑道上墩下水工艺流程 664
16.4横向机械化滑道上墩下水工艺 665
16.4.1横向高低轨滑道 665
16.4.2横向高低腿滑道 666
16.4.3横向梳式滑道 666
16.4.4横向整体斜船架滑道 667
16.4.5典型多船位横向滑道上墩下水工艺流程 669
16.5升船机上墩下水工艺 669
16.6船坞及进出坞工艺 672
16.6.1船坞的型式 672
16.6.2船坞的工艺设施 676
16.6.3进出坞操作工艺流程 679
16.6.4船坞建设的进展 679
16.7平地造船及下水技术 681
16.7.1平地造船的历史沿革 681
16.7.2国内外平地造船概况 681
16.7.3平地造船的移船技术 682
16.8起重技术 685
16.8.1起重设备 685
16.8.2船坞、码头区常用起重设备 685
16.8.3起重设备的配置 689
16.8.4大型起重工艺及设备的合理化 690
第三篇 产品篇 695
第17章 主要运输船舶制造工艺 695
17.1概述 695
17.1.1运输船舶的分类 695
17.1.2主要运输船舶及其分类 695
17.2主要运输船舶制造工艺流程 699
17.2.1船舶制造典型工艺流程 699
17.2.2壳舾涂一体化制造工艺流程 701
17.3散货船制造工艺 702
17.3.1散货船船型和结构特征 702
17.3.2船体建造工艺 703
17.4油船制造工艺 714
17.4.1油船船型和结构特征 714
17.4.2油船专用设备及系统 719
17.4.3油船制造工艺技术 721
17.4.4油船制造关键技术 724
17.5集装箱船制造工艺 730
17.5.1集装箱船的船型和结构特征 730
17.5.2集装箱船制造关键技术 733
17.6主要运输船舶发展趋势 746
17.6.1散货船发展趋势 746
17.6.2油船发展趋势 746
17.6.3集装箱船发展趋势 747
17.7主要运输船舶制造工艺技术发展趋势 747
17.7.1分段总段划分技术 747
17.7.2船舶建造标准化(SDP)技术 748
17.7.3分段组立详细装配程序(DAP)技术 749
17.7.4综合工程图(WSD)规划和设计 751
17.7.5新工艺新技术的推广应用 752
17.7.6运输船舶制造工艺技术发展方向 756
第18章 液化气船制造工艺 757
18.1概述 757
18.1.1液化气船及其分类 757
18.2 LPG(液化石油气)船制造工艺 761
18.2.1 LPG船及其液货舱布置和结构特征 761
18.2.2 LPG船液舱(罐)型式和结构 763
18.2.3液舱(罐)制造工艺及关键技术 765
18.2.4液货舱(罐)制造关键技术 770
18.3 LNG(液化天然气)船制造工艺 772
18.3.1 LNG船及其液货舱结构特征 772
18.3.2 LNG船围护系统制造工艺 776
18.3.3液货舱系统制造关键技术 780
18.4液化气船制造工艺发展趋势 788
18.4.1 LPG船及其制造工艺发展趋势 788
18.4.2 LNG船及其制造工艺发展趋势 789
第19章 高性能船制造工艺 791
19.1概述 791
19.2分类及其特征 791
19.2.1高性能船分类 791
19.2.2高性能船特征 792
19.3布置和结构特征 795
19.3.1地效翼船布置和结构特征 795
19.3.2气垫船布置和结构特征 797
19.3.3水翼船布置和结构特征 798
19.3.4船体材料 799
19.4高性能船制造工艺流程 800
19.4.1地效翼船制造工艺流程 800
19.4.2气垫船制造工艺流程 800
19.4.3水翼船制造工艺流程 800
19.5关键技术和专用工艺 801
19.5.1铝合金冷、热加工工艺 801
19.5.2铝合金船装焊工艺 801
19.5.3铝合金焊接工艺 802
19.5.4气垫船制造关键技术 802
19.5.5地效翼船制造关键技术 803
19.5.6水翼船制造关键技术 803
19.6新工艺应用发展趋势 804
第20章 海洋工程装备制造工艺 805
20.1概述 805
20.2海洋工程装备发展史及其分类 806
20.2.1海洋工程装备发展史 806
20.2.2海洋工程装备的分类 809
20.3海洋工程装备的功能和结构形式 812
20.3.1油气勘探钻井装置的功能和结构形式 812
20.3.2油气生产装置的功能和结构形式 812
20.3.3存储装备和外输系统的功能和组成 825
20.3.4海洋工程船 826
20.3.5水下工程装备 826
20.3.6配套设备 827
20.4海洋工程装备的材料选用和焊接要求 827
20.4.1海洋工程装备的设计建造标准 827
20.4.2海工装备结构用钢及其性能要求 828
20.4.3海工结构钢的焊接工艺要求 836
20.5导管架平台(Jacket Platform)制造工艺 838
20.5.1导管架平台的布置和结构形式 839
20.5.2导管架平台制造工艺流程 840
20.5.3导管架平台制造关键技术 842
20.6半潜式平台(Semi-Submersible Drilling Platform)制造工艺 847
20.6.1半潜式平台的布置和结构形式 847
20.6.2半潜式平台制造工艺流程 849
20.6.3半潜式平台制造关键技术 855
20.7自升式平台(Jack-up Drilling Platform)制造工艺 867
20.7.1自升式平台布置和结构形式 867
20.7.2自升式平台制造工艺流程 870
20.7.3自升式平台的系统调试 876
20.7.4自升式平台制造的关键技术 876
20.8张力腿平台(Tension Leg Platform, TLP)制造工艺 880
20.8.1 SeaStar系列张力腿平台的布置和结构形式 880
20.8.2 SeaStar系列张力腿平台制造工艺 882
20.8.3 SeaStar系列张力腿平台海上安装工艺 884
20.8.4张力腿平台制造安装工艺流程 885
20.9 SPAR平台制造工艺 885
20.9.1 SPAR平台的布置和结构形式 886
20.9.2 SPAR平台制造工艺流程 887
20.9.3 SPAR平台海上定位安装工艺 892
20.10浮式生产储油装置(Floating Production Storage and Offloading Unit, FPSO)制造工艺 893
20.10.1 FPSO的船型布置和结构形式 893
20.10.2单点系泊系统装焊工艺 897
20.10.3模块支墩的形式和装焊工艺 908
20.10.4总承包技术 911
20.11海洋工程装备及制造工艺技术发展趋势 915
20.11.1海洋工程装备的发展趋势 915
20.11.2新颖海工装备概念设计 916
20.11.3海工装备制造工艺技术的发展趋势 917
20.11.4规划和展望 918
第四篇 管理篇 923
第21章 船舶工艺管理 923
21.1概述 923
21.1.1船舶工艺管理的基本内涵 923
21.1.2工艺管理的主要内容 923
21.2工艺过程质量控制 925
21.2.1工艺过程管理要素 926
21.2.2工艺过程质量控制的主要内容 926
21.2.3 ISO9000的贯彻和企业质量体系的建立 927
21.2.4船体建造工艺过程的质量控制 928
21.2.5工艺过程质量控制的文档管理 934
21.3现场工艺管理 935
21.3.1现场工艺管理的目的 935
21.3.2现场工艺管理的内容 935
21.4工时管理 937
21.4.1工时计划管理体系 938
21.5材料消耗工艺定额管理 943
21.5.1主体钢材消耗 943
21.5.2辅助钢材消耗 944
21.5.3焊接材料消耗 945
21.5.4涂料消耗 947
21.6工艺纪律 949
21.6.1工艺纪律的内涵 949
21.6.2工艺纪律的制定和执行 949
21.7文明生产和“5S”管理 953
21.7.1文明生产 953
21.7.2 “5S”管理 954
21.8工法研究和持续改进 958
21.8.1工法研究的内涵 958
21.8.2工法研究的主要内容 958
21.8.3工法的持续改进 958
21.9造船工艺管理的发展趋势 960
21.9.1精细化管理 960
21.9.2精益化管理 961
21.9.3大趋势 962
第22章 船舶工艺标准化 963
22.1概述 963
22.1.1船舶工艺标准化的定义和内涵 963
22.1.2船舶工艺标准化的意义和作用 963
22.1.3船舶工艺标准化的任务和分类 964
22.2船舶工艺技术标准体系 965
22.2.1船舶工艺技术标准体系的内涵 965
22.2.2船舶工艺技术标准体系的作用 966
22.2.3船舶工业标准体系 966
22.3船舶工艺标准的制定、剪裁与实施 968
22.3.1标准的制定和修订 968
22.3.2标准的剪裁 970
22.3.3标准的实施 972
22.4船舶和造船企业工艺标准化工作内容和成果 972
22.4.1设计建造阶段工艺标准化的工作内容 972
22.4.2造船企业标准化的工作内容 973
22.4.3造船企业生产中的工艺标准化工作内容 974
22.4.4造船企业标准化的成果 975
22.5船舶工艺标准化的发展趋势 976
22.5.1船舶标准化的新趋势 976
22.5.2船舶工艺标准化的新发展 976
22.5.3造船企业提高标准化水平的应对措施 977
第23章 船厂建设工艺设计 981
23.1概述 981
23.1.1工艺设计概念、地位和作用 982
23.1.2工艺设计的主要内容 982
23.1.3工艺设计基本方法 984
23.2工艺设计应遵循的基本理念 984
23.2.1建厂要盈利是工艺设计的基本出发点 984
23.2.2工艺设计应顺应现代造船理念的发展趋势 984
23.2.3设计要贯彻国家的有关方针政策 985
23.3前期准备工作和总图设计 985
23.3.1工艺设计的前期准备 985
23.3.2生产纲领和代表产品 987
23.3.3工艺设计基本原则 987
23.3.4总图设计 988
23.4船体工程工艺设计 991
23.4.1船体加工车间工艺设计 992
23.4.2船体装焊车间工艺设计 995
23.5舾装工程工艺设计 998
23.5.1生产任务与物量 998
23.5.2协作关系 998
23.5.3主要舾装件工艺特征 999
23.5.4工艺设计原则 999
23.5.5设备配置 1000
23.5.6车间组成与面积 1000
23.5.7工作制度、年时基数和劳动量计算 1001
23.5.8人员配备 1002
23.6涂装工程工艺设计 1002
23.6.1生产任务与纲领 1003
23.6.2工艺设计原则 1003
23.6.3设备配置 1003
23.6.4车间组成与面积 1003
23.6.5人员配备 1003
23.7管装工程工艺设计 1004
23.7.1生产任务与纲领 1004
23.7.2产品主要工艺特征 1005
23.7.3工艺设计原则 1005
23.7.4设备配置 1007
23.7.5车间组成与面积 1007
23.7.6工作制度、年时基数与劳动量计算 1008
23.7.7人员配备 1008
23.8计算机工程工艺设计 1008
23.8.1任务目标与设计原则 1008
23.8.2系统总体构架与应用结构 1009
23.8.3基础网络系统 1010
23.8.4工程信息系统 1012
23.8.5管理信息系统 1014
23.8.6国产软件的推出 1015
23.9船厂工艺设计的历史回顾及发展趋势 1015
23.9.1传统造船技术的船厂工艺设计 1015
23.9.2以中间产品为导向的壳、舾、涂一体化造船 1016
23.9.3船厂工艺设计展现新趋势 1016
第24章 船舶工艺队伍建设 1018
24.1概述 1018
24.1.1船舶工艺队伍建设历程 1018
24.1.2船舶工艺队伍建设的重要性 1019
24.1.3船舶工艺队伍建设的目的 1019
24.1.4船舶工艺队伍建设的主要内容 1020
24.2船舶工艺工作岗位要求 1020
24.2.1岗位设置及主要职责 1020
24.2.2岗位业务素质和工作能力要求 1021
24.3船舶工艺队伍建设 1023
24.3.1船舶工艺队伍建设的目标 1023
24.3.2船舶工艺队伍建设的途径 1024
24.3.3船舶工艺人员配置原则 1025
24.3.4高技能工人队伍建设 1025
24.4船舶工艺队伍培训 1025
24.4.1培训原则和要求 1026
24.4.2建立并实施继续工程教育制度 1028
24.4.3船舶工艺队伍培训效果的评估 1030
24.5船舶工艺队伍建设展望 1031
第五篇 展望篇 1035
第25章 船舶工艺技术创新和发展规划 1035
25.1概述 1035
25.1.1工艺创新的内涵 1035
25.1.2工艺创新的意义和作用 1036
25.1.3工艺技术创新途径 1037
25.1.4工艺技术创新和工艺技术发展规划 1038
25.2船舶工艺技术创新体系和创新机制 1038
25.2.1船舶工艺技术创新体系的构建原则 1038
25.2.2船舶工艺技术创新机制 1039
25.3我国船舶工艺技术创新历程和实践 1040
25.3.1先进造船理念与模式的创新 1041
25.3.2造船方法创新 1041
25.3.3单项工艺技术创新 1042
25.3.4工艺装备自动化创新 1042
25.3.5数字化制造技术创新 1043
25.3.6造船工法创新 1043
25.4加强船舶工艺技术创新的措施 1044
25.5船舶工艺技术发展规划 1045
25.5.1船舶工艺技术发展规划的内涵和作用 1045
25.5.2规划的分类和编制 1046
25.5.3项目实施和管理 1049
25.3.3总结和验收 1053
第2章 船舶工艺技术发展展望 1054
26.1概述 1054
26.1.1科技革命前夜 1054
26.1.2科技革命引领海洋装备的发展趋势 1054
26.1.3科技革命引领船舶工艺技术发展趋势 1055
26.2现状和需求 1055
26.2.1我国船舶工艺技术现状 1055
26.2.2船舶工业的发展对工艺技术的需求 1056
26.3船舶制造技术的主要发展趋势 1057
26.3.1模块化造船 1057
26.3.2智能化造船 1057
26.3.3数字化造船 1058
26.3.4绿色造船 1058
26.4船舶工艺技术发展展望 1058
26.4.1船舶工艺技术发展方向 1058
26.4.2船舶工艺技术发展展望 1060
26.5未来5~10年需要突破的船舶工艺技术 1064
26.5.1构件加工成形技术 1064
26.5.2分段总组搭载技术 1065
26.5.3单元舾装技术 1065
26.5.4高效焊接技术 1066
26.5.5高效涂装技术 1066
26.5.6精度测量与控制技术 1066
26.5.7新材料应用技术 1067
26.5.8虚拟制造技术 1067
26.5.9节能减排技术 1068
26.6结束语 1068