图书介绍
表面工程手册pdf电子书版本下载
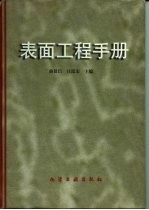
- 曲敬信,汪泓宏主编 著
- 出版社: 北京:化学工业出版社
- ISBN:7502519920
- 出版时间:1998
- 标注页数:895页
- 文件大小:74MB
- 文件页数:911页
- 主题词:
PDF下载
下载说明
表面工程手册PDF格式电子书版下载
下载的文件为RAR压缩包。需要使用解压软件进行解压得到PDF格式图书。建议使用BT下载工具Free Download Manager进行下载,简称FDM(免费,没有广告,支持多平台)。本站资源全部打包为BT种子。所以需要使用专业的BT下载软件进行下载。如 BitComet qBittorrent uTorrent等BT下载工具。迅雷目前由于本站不是热门资源。不推荐使用!后期资源热门了。安装了迅雷也可以迅雷进行下载!
(文件页数 要大于 标注页数,上中下等多册电子书除外)
注意:本站所有压缩包均有解压码: 点击下载压缩包解压工具
图书目录
1.1 概述 1
第1章 摩擦与磨损 1
1.2 摩擦 2
1.2.1 摩擦的定义和分类 2
1.2.2 古典摩擦定律 3
1.2.3 摩擦机理 3
1.2.4 影响摩擦的主要因素 7
1.3.1 磨损的定义 11
1.3.2 磨损的分类 11
1.3 材料的磨损 11
1.3.3 磨损的评定方法 12
1.4 磨料磨损 13
1.4.1 磨料磨损的定义和分类 13
1.4.2 磨料磨损机理和简化模型 14
1.4.3 磨料磨损的主要影响因素 15
1.5 粘着磨损 23
1.5.1 粘着磨损的定义和分类 23
1.5.2 粘着磨损的模型和粘着磨损方程式 24
1.5.3 机械零件的磨损特性 25
1.5.4 影响粘着磨损的主要因素 26
1.6 疲劳磨损 28
1.6.1 疲劳磨损的定义与特征 28
1.6.2 疲劳磨损的基本理论 28
1.6.3 影响疲劳磨损的主要因素 31
1.7 冲蚀磨损 32
1.7.1 冲蚀磨损的定义与特点 32
1.7.2 冲蚀磨损的基本理论 33
1.7.3 影响冲蚀磨损的主要因素 34
1.8.1 腐蚀磨损 38
1.8 腐蚀磨损与微动磨损 38
1.8.2 微动磨损 40
参考文献 42
第2章 金属的腐蚀 44
2.1 腐蚀的分类 44
2.2 电化学腐蚀机理 44
2.2.1 原电池作用 44
2.2.2 电解作用 45
2.3 电化学腐蚀的热力学判据和电位-pH图 46
2.3.1 利用金属标准电极电位和阴极反应平衡电位估计腐蚀的可能性 46
2.3.3 电位-pH腐蚀状态图 49
2.3.2 电位-pH图 49
2.3.4 实测的E-pH腐蚀状态图 50
2.3.5 电位-pH图的适用性和局限性 51
2.4 电化学腐蚀动力学与极化作用 51
2.5 钝化作用 52
2.6 金属与合金的耐蚀性特点 53
2.6.1 热力学稳定的金属材料的耐蚀性特点 54
2.6.2 钝性金属材料的耐蚀性特点 54
2.6.3 镀层金属的耐蚀性特点 54
2.7.2 介质pH值和溶氧浓度的影响 55
2.7.4 介质流速的影响 55
2.7.3 介质中特异离子的影响 55
2.7 环境因素对腐蚀的影响 55
2.7.1 介质氧化还原性的影响 55
2.6.4 应力、应变对金属腐蚀的影响 55
2.7.5 温度的影响 56
2.8 腐蚀过程的控制因素 56
2.9 防腐蚀途径的选择 57
2.10 金属材料或镀层的耐蚀性评价与试验方法 58
2.10.1 腐蚀速率或腐蚀程度的表示方法 58
2.10.2 耐蚀性评价 60
2.10.3 常用腐蚀试验方法简介 61
参考文献 63
第3章 金属的高温氧化 64
3.1 金属高温氧化原理 64
3.1.1 金属高温氧化的热力学判据 64
3.1.2 高温氧化机理 66
3.1.3 高温氧化速度 68
3.1.4 氧化物的比容 70
3.2 金属高温硫化 70
3.3.1 钒侵蚀 73
3.3 几种液态环境中的高温腐蚀 73
3.3.2 热腐蚀 74
3.3.3 熔盐腐蚀 76
3.3.4 液态金属中的腐蚀 77
3.4 防止高温腐蚀的途径 78
3.4.1 使用惰性气体或保护气氛 78
3.4.2 选用耐高温腐蚀的金属材料 79
3.4.3 使用高温防护涂层 79
3.5 高温氧化的评价与试验方法简介 81
参考文献 83
第4章 疲劳 84
4.1 疲劳强度与寿命 84
4.1.1 疲劳现象 84
4.1.2 应力疲劳寿命(S-N曲线) 84
4.1.3 应变疲劳寿命(Coffin-Ma-nson关系) 85
4.1.4 平均应力对疲劳寿命的影响 86
4.1.5 疲劳累积损伤 87
4.1.6 疲劳的多阶段过程 87
4.2.1 循环形变的硬化和软化 88
4.2 循环形变及其特征 88
4.2.2 循环应力应变曲线 89
4.2.3 驻留滑移带与循环应变局部化 91
4.2.4 循环形变的位错结构 92
4.3 疲劳裂纹的萌生和扩展 94
4.3.1 裂纹萌生的优先地点 94
4.3.2 裂纹扩展的第Ⅰ和第Ⅱ阶段 96
4.3.3 近门槛的疲劳裂纹扩展 98
4.3.4 裂纹的闭合现象及其机制 100
4.3.5 疲劳短裂纹行为 101
4.4.1 疲劳中的表面与内部形变 102
4.4 循环形变和疲劳中的表面效应 102
4.4.2 疲劳损伤的X射线测量 104
4.4.3 疲劳中的表面膜效应 106
参考文献 107
第5章 表面预处理 110
5.1 净化处理 110
5.1.1 表面沾污物 111
5.1.2 净化原理 111
5.1.3 净化剂 111
5.1.4 净化方法 115
5.1.5 净化度检验 116
5.2 除锈与活化 117
5.2.1 酸洗法除锈 118
5.2.2 电解法除锈 119
5.2.3 喷砂法除锈 119
5.2.4 活化处理 120
5.3 光饰与粗糙化 121
5.3.1 光饰处理 121
5.3.2 粗糙化处理 123
参考文献 124
第6章 电镀 125
6.1 基本理论 125
6.1.1 电沉积过程 125
6.1.2 阴极析出与极化 125
6.1.3 电结晶及其影响因素 126
6.1.4 共沉积 129
6.1.5 快速电沉积 130
6.2 单金属电镀 131
6.2.1 镀镉、锡、铅 131
6.2.2 镀锌、铜 134
6.2.3 镀镍、铁、钴 136
6.2.4 镀铬 138
6.2.5 镀贵金属及其他单金属 139
6.3 合金电镀 140
6.3.1 防护性合金电镀 141
6.3.2 耐磨性合金电镀 144
6.3.3 减摩性合金电镀 146
6.3.4 钎焊性合金电镀 148
6.3.5 装饰性合金电镀 148
6.4 复合电镀 151
6.4.1 防护性复合电镀 152
6.4.2 耐磨性复合电镀 153
6.4.3 减摩性复合电镀 155
6.5 电刷镀 157
6.5.1 概述 157
6.5.2 电刷镀装备 158
6.5.3 电刷镀溶液 159
6.5.4 电刷镀工艺及参数控制 162
6.5.5 电刷镀技术应用简介 163
6.6.2 流镀装备 164
6.6 流镀 164
6.6.1 概述 164
6.6.3 流镀工艺与应用 167
6.6.4 流镀非晶态合金 172
6.6.5 复合流镀 173
参考文献 175
第7章 自催化沉积 176
7.1 概述 176
7.1.1 自催化沉积条件 176
7.1.3 自催化沉积应用范围 177
7.1.2 自催化沉积特点 177
7.2 自催化镀液 178
7.2.1 主盐 179
7.2.2 还原剂 180
7.2.3 络合剂 181
7.2.4 稳定剂 182
7.2.5 其他添加剂 183
7.3 催化表面与参数控制 183
7.3.1 固体表面的催化活性 183
7.3.2 参数控制 184
7.4 磷系自催化沉积 185
7.4.1 磷系自催化镀镍 186
7.4.2 磷系自催化镀钴 189
7.4.3 磷系自催化镀贵金属 190
7.4.4 磷系自催化镀其他金属 191
7,4.5 磷系自催化镀多元合金 191
7.5 硼系自催化沉积 195
7.5.1 硼系自催化镀镍 195
7.5.2 硼系自催化镀钴 198
7.5.4 硼系自催化镀多元合金 200
7.5.3 硼系自催化镀贵金属 200
7.6 醛系及肼系自催化沉积 201
7.6.1 醛系自催化沉积 202
7.6.2 肼系自催化沉积 203
7.7 自催化复合沉积 204
7.7.1 软质点系自催化复合镀层 205
7.7.2 硬质点系自催化复合镀层 207
参考文献 209
8.1.1 表面转化膜的分类 210
8.1 概述 210
第8章 表面转化 210
8.1.2 表面转化处理方法 211
8.1.3 表面转化膜的用途 211
8.2 氧化处理 212
8.2.1 铝及铝合金氧化处理 212
8.2.2 钢铁氧化处理 215
8.2.3 其他金属的氧化处理 216
8.3 磷化处理 217
8.3.1 钢铁磷化 218
8.3.3 铝材磷化 220
8.3.2 锌材磷化 220
8.4 钝化处理 221
8.4.1 铜及铜合金钝化处理 221
8.4.2 不锈钢钝化处理 221
8.4.3 锌及锌合金钝化处理 222
8.4.4 其他金属的钝化处理 222
8.5 着色处理 223
8.5.1 不锈钢着色 223
8.5.2 铜及铜合金着色 223
8.5.4 锌及锌合金着色 224
8.5.3 银及银合金着色 224
参考文献 225
第9章 化学气相沉积 226
9.1 引言 226
9.2 化学气相沉积 226
9.2.1 化学气相沉积理论基础 226
9.2.2 化学气相沉积方法及装置 243
9.3 等离子体增强CVD 270
9.3.1 原理 270
9.3.2 等离子体CVD沉积装置 275
9.3.3 等离子体CVD沉积方法 278
9.4 激光CVD 280
9.4.1 原理 280
9.4.2 LCVD方法 281
9.5 金属有机化合物CVD 281
9.5.1 原理 281
9.5.2 金属有机化合物 282
9.5.3 MOCVD沉积装置及方法 283
9.5.4 安全性考虑 286
9.6.1 CVD硬质涂层 287
9.6 CVD硬质涂层和耐腐蚀涂层 287
9.6.2 抗摩擦磨损及耐腐蚀CVD涂层 290
9.6.3 CVD硬质涂层的工具应用 291
9.6.4 CVD耐腐蚀涂层 293
9.7 CVD金刚石膜 296
9.7.1 金刚石膜化学气相沉积 297
9.7.2 金刚石膜CVD工艺 298
9.7.3 类金刚石膜(DLC)的化学气相沉积 301
9.7.4 金刚石和类金刚石膜的应用 303
参考文献 307
10.2.1 蒸发热力学 315
10.2 真空蒸发的物理原理 315
第10章 真空蒸发 315
10.1 概述 315
10.2.2 蒸发动力学 325
10.2.3 薄膜厚度的均匀性 328
10.3 真空镀膜工艺 333
10.3.1 真空蒸发装置 333
10.3.2 蒸发源 334
10.4 真空蒸发技术的应用 345
10.5.1 多源蒸发 346
10.5.2 瞬时蒸发 346
10.5 特殊蒸发技术 346
10.5.3 反应蒸发 347
10.5.4 分子束外延 348
参考文献 356
第11章 溅射技术 357
11.1 溅射技术基础 357
11.1.1 溅射 357
11.1.2 溅射原理 357
11.1.3 溅射系数 358
11.1.4 溅射产物和溅射时靶表面的变化 363
11.2 溅射镀膜工艺与装备 368
11.2.1 直流辉光放电 369
11.2.2 射频辉光放电 371
11.2.3 等离子体电位、浮动电位和偏压 371
11.2.4 从二极溅射到磁控溅射 372
11.2.5 磁控溅射技术 376
11.2.6 磁控溅射的工作原理 378
11.2.7 各种磁控溅射源 380
11.2.8 反应溅射镀膜 385
11.2.9 离子束溅射镀膜 386
11.3 溅射镀膜技术的应用实例 389
11.3.1 纯金属与合金溅射镀膜的应用实例——集成电路(IC)芯片制造中的电极引线 391
11.3.2 化合物溅射镀膜的应用实例——硬质涂层溅射镀膜工艺 393
11.3.3 在幕墙玻璃产品上的应用实例 397
11.3.4 在透明导电玻璃生产方面的应用实例 400
参考文献 403
第12章 离子镀 406
12.1 概述 406
12.2 离子镀的物理原理 406
12.2.2 离子镀的离化率 407
12.2.1 离子镀的成膜条件 407
12.2.3 粒子轰击对薄膜生长的影响 408
12.2.4 离子镀的特点 409
12.3 离子镀的类型及应用 410
12.3.1 直流二极型离子镀 410
12.3.2 三极型离子镀 411
12.3.3 射频离子镀 413
12.3.4 磁控溅射离子镀 414
12.3.5 反应离子镀 414
12.3.6 空心阴极放电离子镀 421
12.3.7 多弧离子镀 426
12.3.8 离子束辅助沉积 431
12.3.9 离化团束沉积 437
参考文献 442
第13章 离子注入 444
13.1 科学意义和应用前景 444
13.2 离子注入的特点和离子注入机 445
13.2.1 离子注入原理 445
13.2.3 离子注入系统和离子注入机 446
13.2.2 离子注入的特点 446
13.3 射程和能量淀积 452
13.3.1 阻止本领和能量损失 452
13.3.2 离子射程 453
13.3.3 入射离子在固体中的分布 453
13.3.4 能量淀积和辐射损伤 454
13.4 溅射理论及其对保留注入量和注入原子分布的影响 455
13.4.1 离子溅射 455
13.4.3 饱和保留量的计算 456
13.4.2 溅射对杂质分布的影响 456
13.5 辐射相的形成 457
13.5.1 空位、间隙原子和无序相的形成 457
13.5.2 激烈的热峰碰撞与淬火相的形成 458
13.6 离子注入大规模集成电路微细加工技术 459
13.6.1 大规模集成电路与离子束微细加工技术的发展 459
13.6.2 离子注入半导体集成电路和器件 460
13.6.3 离子注入浅结工艺 462
13.7 金属离子注入 463
13.7.1 离子注入摩擦学特性 463
13.7.2 离子注入强化机理 464
13.7.3 离子注入强化规则 470
13.7.4 离子注入抗腐蚀特性 471
13.7.5 离子注入抗氧化研究 473
13.7.6 离子注入抗疲劳特性 474
13.7.7 离子注入的工业应用 476
12.8 离子注入陶瓷 477
13.8.1 离子注入陶瓷机械性能的变化 478
13.8.2 离子注入增强韧性 479
13.8.3 离子注入陶瓷的摩擦学特性 479
13.9 离子注入聚合物 480
13.9.1 离子辐照分子交联和降解 481
13.9.2 离子辐照下聚合物电特性变化 482
13.9.3 离子注入聚合物表面硬化 483
13.9.4 离子注入PN结的制备 485
13.10 离子注入SOI技术 486
13.10.1 SIMOX的制备 486
13.10.2 SIMNI的制备 487
13.10.5 SOI的应用 488
13.11 离子注入硅化物的合成 488
13.10.4 低能注入 488
13.10.3 多重注入 488
13.11.1 硅化物的特性 489
13.11.2 硅化物生长动力学 489
13.11.3 离子束混合硅化物的合成 490
13.11.4 离子注入合成硅化物 490
参考文献 491
第14章 电子束表面改性 493
14.1 电子束表面改性工艺 493
14.1.1 电子束表面淬火 493
14.1.2 电子束表面合金化 496
14.1.3 电子束表面熔凝处理 501
14.1.4 电子束表面熔覆 504
14.2 电子束表面改性装置 505
14.2.1 电子枪 505
14.2.2 高压油箱 506
14.2.3 聚焦系统 508
14.2.4 扫描系统 508
14.2.5 低真空工作室 509
14.2.6 真空系统 509
参考文献 510
14.2.7 监控系统 510
15.1 激光束表面改性的原理 511
15.1.1 激光及其特性 511
第15章 激光束表面改性 511
15.1.2 激光束与材料表面的交互作用 513
15.2 激光表面改性设备 519
15.2.1 激光器 519
15.2.2 激光器的外围装置 521
15.2.3 机械系统 522
15.2.4 辅助系统 522
15.3.2 激光表面改性的特点 523
15.3 激光表面改性的种类和特点 523
15.3.1 激光表面改性的分类 523
15.4 激光表面相变硬化 524
15.4.1 激光相变硬化的工艺基础 524
15.4.2 激光相变硬化的组织转变特点 525
15.4.3 表面预处理 526
15.4.4 激光扫描方式 528
15.4.5 激光相变硬化的工艺参数选择 528
15.4.7 激光相变硬化层的性能 529
15.4.6 常用钢铁材料的激光相变硬化 529
15.4.8 应用 531
15.5 激光表面熔凝处理 533
15.5.1 激光熔凝工艺 533
15.5.2 激光熔凝时的加热和冷却 534
15.5.3 激光熔凝组织 534
15.5.4 几种激光熔凝层的硬度及耐磨性 535
15.6 激光表面合金化 536
15.6.1 激光合金化工艺 537
15.6.3 硬度和耐磨性及应用 538
15.6.2 显微组织特征 538
15.7 激光表面熔覆 539
15.7.1 熔覆工艺 539
15.7.2 激光熔覆显微组织 540
15.7.3 激光熔覆层的性能 540
15.8 激光冲击硬化 541
15.9 激光表面改性技术展望 541
参考文献 542
16.1.2 快速加热的相变特点 544
16.1.1 表面热处理的特点与分类 544
第16章 表面热处理 544
16.1 表面热处理的基本原理 544
16.1.3 表面淬火的组织 545
16.1.4 表面淬火硬化层厚度的测定 545
16.1.5 零件表面淬火后的性能 545
16.2 感应加热淬火 546
16.2.1 感应加热的基本原理 546
16.2.2 感应加热淬火工艺 547
16.3.1 超高频脉冲感应加热淬火 556
16.3.2 大功率脉冲感应加热淬火 556
16.2.3 感应器 556
16.3 脉冲表面淬火 556
16.4 火焰淬火 557
16.4.1 火焰淬火特点 557
16.4.2 火焰淬火前的准备工作 557
16.4.3 火焰淬火工艺 558
16.5 电解液加热表面淬火 558
16.6 高频感应与电阻加热相结合的表面淬火工艺 559
参考文献 560
16.7 电接触加热表面淬火 560
第17章 化学热处理 562
17.1 化学热处理概论 562
17.1.1 化学热处理的分类与特点 562
17.1.2 化学热处理的基本过程 563
17.1.3 化学热处理过程的控制及加速 564
17.2 渗碳 565
17.2.1 渗碳的目的及应用范围 565
17.2.2 渗碳基本原理 566
17.2.3 渗碳方法 567
17.2.4 渗碳用钢及渗碳后热处理 576
17.2.5 渗碳件质量检验及常见缺陷的防止措施 578
17.3 碳氮共渗 579
17.3.1 碳氮共渗的特点 579
17.3.2 气体碳氮共渗 580
17.3.3 液体碳氮共渗 580
17.3.4 碳氮共渗用钢及渗后热处理 581
17.3.5 碳氮共渗层的组织与性能 582
17.3.6 碳氮共渗层的质量检查及常见缺陷与预防 583
17.4 渗氮 583
17.4.1 渗氮的特点与渗氮常用钢种 583
17.4.2 渗氮工艺 584
17.4.3 渗氮层的组织与性能 587
17.4.4 渗氮的常见缺陷与防止措施 588
17.5 氮碳共渗 588
17.5.1 氮碳共渗及其主要特点 588
17.5.2 氮碳共渗工艺 588
17.5.3 氮碳共渗后的性能特点 589
17.6 渗金属及渗硼 589
17.6.1 渗铝 589
17.6.2 渗铬 591
17.6.4 渗钒渗铌渗钛 592
17.6.3 渗硅 592
17.6.5 渗硼 593
17.6.6 渗硫 595
17.7 共渗、复合渗与复合处理 596
17.7.1 概述 596
17.7.2 含铝共渗、复合渗与复合处理 596
17.7.3 含铬共渗与复合渗 598
17.7.4 含硼共渗与复合渗 599
17.7.5 含硫共渗 602
17.7.6 碳氮硼三元共渗和氧硫碳氮硼五元共渗 604
17.7.7 氮碳共渗+氧化抛光复合处理 605
参考文献 606
第18章 热漫镀 607
18.1 概述 607
18.2 热镀锌 608
18.2.1 铁与熔融锌的反应 608
18.2.2 钢基体及锌液化学成分对镀锌层特性的影响 610
18.2.3 镀锌钢板 611
18.2.4 镀锌钢丝 615
18.2.5 镀锌钢管 618
18.2.6 玛钢件热镀锌 619
18.2.7 锌锅及其加热热源 620
18.2.8 硅镇静钢热镀锌 623
18.2.9 镀锌钢材的贮运 624
18.3 热镀铝 625
18.3.1 铁与熔融铝的反应 625
18.3.2 钢基及铝液的化学成分和镀铝工艺参数对镀层特性的影响 627
18.3.3 镀铝钢板 628
18.3.4 镀铝钢板的发展 630
18.3.5 镀铝钢丝 634
18.3.6 镀铝钢管 636
18.3.7 存在问题及对策 639
18.3.8 镀铝钢材的性能和用途 639
18.4 热镀锌铝合金 642
18.4.1 锌-铝合金状态图 642
18.4.2 镀层成分及第三组分 643
18.4.3 55%Al-Zn合金镀层钢板生产 644
18.4.4 55%Al-Zn镀层钢板的性能 644
18.4.5 55%Al-Zn镀层钢板的用途 647
18.4.6 Zn-5%Al-Re合金镀层钢板的生产 647
18.4.7 Zn-5%Al-Re合金镀层钢板的性能 648
18.4.8 Zn-5%Al-Re合金镀层钢板的用途 648
18.5 热镀铅 649
18.5.1 铁-铅合金状态图及镀铅层的形成 649
18.5.2 热镀铅锡合金钢板的生产工艺 650
18.5.3 镀铅层的性能 652
18.5.4 用途 653
18.6 热镀锡 653
18.6.1 铁-锡合金状态图及工艺因素对镀锡层的影响 653
18.6.2 钢材热镀锡生产工艺 654
18.6.3 马口铁生产 657
18.6.4 镀锡层的特性 657
18.6.5 用途 658
参考文献 659
第19章 热喷涂 661
19.1 概述 661
19.1.1 简介 661
19.1.2 热喷涂的分类 661
19.1.3 热喷涂的特点 662
19.2 热喷涂的原理、工艺及设备 662
19.2.1 电弧喷涂 662
19.2.2 等离子喷涂 663
19.2.3 火焰喷涂 665
19.2.4 爆炸喷涂 667
19.2.5 超音速火焰喷涂 668
19.2.6 激光喷涂 669
19.3 喷焊 670
19.3.1 喷焊的原理与特点 670
19.3.2 喷焊设备 670
19.4 喷涂方法的选用及工艺操作过程中的注意事项 672
19.5 喷涂前对零件基体表面的预处理 673
19.5.1 喷砂处理 673
19.5.2 机加工 673
19.6.2 车床切削 674
19.6.3 涂层的封孔处理 674
19.6 零件喷涂后的处理 674
19.6.1 手工打磨 674
19.6.4 涂层的高温扩散处理 676
19.6.5 热等静压处理 676
19.6.6 激光束处理 676
19.7 涂层材料及选择 676
19.7.1 涂层材料的分类 676
19.7.2 涂层材料的供应及特点 680
19.8.2 涂层的微观分析 682
19.8 涂层的性能及测定 682
19.8.1 影响涂层性能的因素 682
19.8.3 涂层机械性能的测定 684
19.8.4 涂层的热性能测定 686
19.8.5 耐腐蚀试验 686
19.8.6 涂层的无损检验 687
19.9 热喷涂的应用 687
19.9.1 航空工业上的应用 688
19.9.3 机械工业耐磨损的应用 689
19.9.4 用热喷涂的方法制造新材料 690
19.9.5 生物医学工程的应用 690
19.10 热喷涂设备与人身的安全防护 691
19.10.1 设备的防护 691
19.10.2 人身的安全防护 692
参考文献 693
20.1.1 堆焊的定义和类型 694
20.1 概述 694
20.1.2 堆焊在生产中的应用 694
第20章 堆焊 694
20.1.3 堆焊中的几个冶金问题 695
20.2 几种常用的堆焊方法 696
20.2.1 火焰堆焊 696
20.2.2 手弧堆焊 697
20.2.3 钨极氩弧堆焊(TIG堆焊) 699
20.2.4 熔化极气体保护电弧堆焊(MIG堆焊) 699
20.2.5 埋弧堆焊 702
20.2.6 等离子弧堆焊 704
20.2.7 电渣堆焊 707
20.2.8 堆焊方法选择 708
20.3 金属材料堆焊 711
20.3.1 堆焊合金的使用性 711
20.3.2 堆焊合金的分类 711
20.3.3 珠光体钢堆焊金属 713
20.3.4 马氏体钢堆焊金属 714
20.3.5 奥氏体钢堆焊金属 718
20.3.6 合金铸铁堆焊金属 722
20.3.7 镍基合金堆焊金属 724
20.3.8 钻基合金堆焊金属 727
20.3.9 铜基合金堆焊金属 728
20.3.10 碳化物复合材料堆焊金属 731
20.3.11 堆焊件的基材及其影响 734
20.3.12 堆焊合金的选择及应用实例 735
参考文献 737
21.1.1 引言 739
21.1 溶胶-凝胶法的基本概念 739
21.1.2 溶胶和凝胶化学 739
第21章 溶胶-凝胶法 739
21.1.3 干燥 741
21.1.4 煅烧与烧结 742
21.1.5 涂覆方法 742
21.1.6 溶胶-凝胶工艺的应用 744
21.2.1 金属基材涂层的内容及意义 747
21.2.2 单组分氧化物涂层 747
21.2 金属基材涂层 747
21.2.3 双组分氧化物涂层 757
21.2.4 多组分氧化物薄膜 758
21.3 非金属基材薄膜 760
21.3.1 非金属基材薄膜的内容及意义 760
21.3.2 单组分氧化物薄膜 761
21.3.3 双组分氧化物薄膜 767
21.3.4 多组分氧化物薄膜 769
21.4 碳纤维的包覆 770
21.4.1 二氧化硅包覆碳纤维 770
21.4.2 氧化铝包覆碳纤维 771
21.5.1 粉体与沉淀包覆的内容及意义 772
21.5 粉体与沉淀的包覆 772
21.5.2 粉体的包覆 772
21.4.3 SiO2/ZrO2包覆玻璃纤维 772
参考文献 781
22.1 概述 785
22.2 高分子涂装技术 785
第22章 高分子涂层 785
22.2.1 静电喷涂 786
22.2.2 电泳涂装 793
22.2.3 粉末涂装 801
22.3 特种高分子涂层 829
22.3.1 耐高温涂料 829
22.3.2 烧蚀涂料 830
22.3.3 伪装涂料 830
22.3.4 示温涂料 831
22.3.5 “隐身”涂料 832
22.3.6 防污涂料 834
参考文献 837
23.1 厚度测量 839
23.1.1 概述 839
第23章 镀层质量检验与测试 839
23.1.2 膜厚测量方法 840
23.2 硬度测量 856
23.2.1 概述 856
23.2.2 显微硬度测量原理 858
23.2.3 显微硬度测量仪器 860
23.2.4 显微硬度测量实验条件 862
23.3 表面粗糙度检测 865
23.3.1 概述 865
23.2.5 显微硬度的误差分析 865
23.3.2 粗糙度的取样长度与评定长度 867
23.3.3 评定基准及表征参数 867
23.3.4 粗糙度的标注方法 869
23.3.5 检测方法 869
23.4 附着力测量 873
23.4.1 镀层的附着力 873
23.3.6 检测中的注意事项 873
23.4.2 附着力的测量方法 875
23.5.1 内应力与热应力 885
23.5.2 内应力的测量方法 885
23.5 应力测量 885
参考文献 891
19.9.2 机械工业防腐工程的应用 8688