图书介绍
实用长输管道焊接技术pdf电子书版本下载
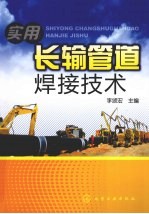
- 李颂宏主编 著
- 出版社: 北京:化学工业出版社
- ISBN:9787122036391
- 出版时间:2009
- 标注页数:286页
- 文件大小:81MB
- 文件页数:297页
- 主题词:长输管道-焊接
PDF下载
下载说明
实用长输管道焊接技术PDF格式电子书版下载
下载的文件为RAR压缩包。需要使用解压软件进行解压得到PDF格式图书。建议使用BT下载工具Free Download Manager进行下载,简称FDM(免费,没有广告,支持多平台)。本站资源全部打包为BT种子。所以需要使用专业的BT下载软件进行下载。如 BitComet qBittorrent uTorrent等BT下载工具。迅雷目前由于本站不是热门资源。不推荐使用!后期资源热门了。安装了迅雷也可以迅雷进行下载!
(文件页数 要大于 标注页数,上中下等多册电子书除外)
注意:本站所有压缩包均有解压码: 点击下载压缩包解压工具
图书目录
第1章 长输管道施工工艺简介 1
1.1长输管道施工工艺流程 1
1.2施工准备 1
1.2.1公共关系准备 1
1.2.2人员准备 2
1.2.3设备及物资准备 2
1.2.4编制施工进度计划及对施工任务进行划分 2
1.2.5技术准备 3
1.2.6对施工地区的自然状况进行调查 3
1.2.7营地建设 3
1.3测量放线及作业带清理 4
1.3.1接桩 4
1.3.2补桩 4
1.3.3测量放线及设立标志桩 4
1.3.4移桩 5
1.3.5施工作业带的清理 5
1.3.6施工便道的修筑 5
1.4管道的组装焊接 5
1.4.1布管 5
1.4.2钢管的组装 6
1.4.3钢管的焊接 6
1.4.4表面的清理及外观检查 7
1.4.5焊接接头的无损检测 7
1.4.6焊缝的返修 8
1.5管道的防腐补口 8
1.5.1金属腐蚀的基本原理和分类 8
1.5.2埋地管道的腐蚀 8
1.5.3防腐前对钢管表面的处理 9
1.5.4管道防腐的常用涂料 9
1.5.5防腐涂层的主要特性 9
1.5.6管道防腐补口的一般步骤 10
1.5.7管道防腐的一般要求 10
1.6管沟的开挖、管道下沟回填及地貌恢复 10
1.6.1管沟的开挖 10
1.6.2管道的下沟 10
1.6.3管道的回填及地貌的恢复 11
1.7压力试验及通球扫线 11
1.7.1压力试验 11
1.7.2通球扫线 11
第2章 长输管道施工焊接管理 12
2.1焊接性试验及焊接工艺评定 12
2.1.1焊接性试验 12
2.1.2焊接工艺评定 12
2.2焊接工艺规程的制定 14
2.2.1通用性焊接工艺规程 15
2.2.2专用性焊接工艺规程 15
2.2.3焊接工艺规程的内容 15
2.3焊工管理 16
2.3.1焊工培训 16
2.3.2焊工考试方法 17
2.3.3焊工资格证管理 17
2.3.4焊工档案管理 17
2.4材料及设备管理 18
2.4.1钢管管理 18
2.4.2焊接材料管理 18
2.4.3设备管理 19
2.5焊接过程控制 19
2.5.1焊前技术要求 19
2.5.2环境监测 20
2.5.3预热、后热和焊后保温缓冷 20
2.5.4施焊工艺参数 21
2.5.5层间清理及层间温度 21
2.6焊缝检查 22
2.6.1外观检查 22
2.6.2无损检测 23
2.6.3焊缝标志 23
2.7焊缝的修补及返修 23
2.8焊接资料的归档 24
第3章 管道工程焊接工艺评定及焊接工艺规程 25
3.1工程概况 25
3.1.1国外某天然气管道工程概况 25
3.1.2工程要求的焊接工艺评定项目 25
3.1.3焊接工艺评定检验项目 26
3.1.4编制焊接工艺评定程序文件 26
3.2人员组织及设备配备 26
3.2.1人员组织 26
3.2.2对人员的基本要求 26
3.2.3设备配备 27
3.3工艺评定用场地及对安全和环境保护的要求 28
3.3.1焊接工艺评定场地要求 28
3.3.2安全要求 28
3.3.3环境保护要求 28
3.3.4对焊接材料的要求 29
3.3.5钢管的管理 29
3.3.6管口的组装 30
3.3.7焊前预热 30
3.3.8焊接 30
3.3.9焊接工艺评定参数的测定和记录 32
3.3.10无损检测 32
3.3.11试样的切取 33
3.3.12试样的加工 33
3.3.13力学性能试验 33
3.3.14焊接工艺评定报告 34
3.3.15全过程接受监理的监督 34
3.3.16几点体会 34
第4章 管道焊接材料 36
4.1管道焊接材料的分类 36
4.1.1焊条的分类 36
4.1.2焊丝的分类 38
4.1.3焊剂的分类 40
4.1.4保护气体 41
4.2焊接材料的采购与验收、保管与管理 42
4.2.1总则 42
4.2.2采购 43
4.2.3验收 43
4.2.4入库 43
4.2.5库存保管 44
4.2.6出库 44
4.2.7使用过程中的管理 44
4.3管道施工常用焊接材料型号、牌号表示方法 45
4.3.1焊条的型号、牌号表示方法 45
4.3.2焊丝的型号、牌号表示方法 52
4.3.3埋弧焊焊剂型号、牌号表示方法 58
4.4管道施工常用焊接材料标准目录 60
第5章 管道焊接设备 62
5.1焊接设备的分类及型号 62
5.1.1焊接设备的分类 62
5.1.2我国焊接设备型号的表示方法 62
5.2常用弧焊电源及其技术特性 64
5.2.1焊接电源的空载电压和电源的外特性 64
5.2.2弧焊电源的主要技术指标 66
5.2.3弧焊电源类型 66
5.3焊接设备的特点及应用 70
5.3.1手工电弧焊设备 70
5.3.2气体保护焊设备 71
5.3.3埋弧焊设备 71
5.3.4电阻焊设备 71
5.3.5焊接机器人简介 72
5.3.6专用成套焊接设备 72
5.3.7管道全位置自动焊 72
5.4手工电弧焊对电源的要求 73
5.4.1对外特性的要求 73
5.4.2对弧焊电源空载电压的要求 75
5.4.3对弧焊电源调节特性的要求 75
5.4.4对弧焊电源动特性的要求 75
5.4.5对弧焊电源结构的要求 76
5.5DC-400焊接电源与LN-23P送丝机 76
5.5.1DC-400焊接电源 76
5.5.2LN-23P送丝机 78
5.6常用弧焊电源的选择、使用与维护 83
5.6.1弧焊电源的特点 83
5.6.2弧焊电源的选择 84
5.6.3弧焊电源的正确使用与维护 84
第6章 焊条上向焊焊接工艺 85
6.1焊条上向焊原理、特点及工艺参数的选择 85
6.1.1焊条上向焊的原理 85
6.1.2焊条上向焊的特点 85
6.1.3焊接工艺参数的选择 86
6.2焊条上向焊的基本操作技术 87
6.2.1引弧、运条和收弧 87
6.2.2单面焊双面成形技术 88
6.3板件的焊接 89
6.3.1板件的平焊 89
6.3.2板件的立焊 92
6.3.3板件的横焊 95
6.3.4板件的仰焊 96
6.4管件的焊接 98
6.4.1水平固定小径管对接焊 98
6.4.2垂直固定小径管对接焊 100
6.4.345°倾斜固定小径管的对接焊 102
6.4.4水平固定大径管对接焊 104
第7章 焊条下向焊焊接工艺 107
7.1概述 107
7.1.1焊条下向焊技术的应用与发展 107
7.1.2焊条下向焊的特点 108
7.1.3管道下向焊工艺过程 108
7.2培训管口的组对方法及清理 109
7.2.1培训用管圈的加工方法 109
7.2.2管圈的组对方法 110
7.2.3焊前清理 110
7.3纤维素型焊条下向焊操作技术 111
7.3.1根焊道操作技术 111
7.3.2热焊、填充、盖面焊道操作技术 113
7.4低氢型焊条下向焊操作技术 114
7.4.1焊接设备、焊接材料及母材的选择 115
7.4.2管口组对尺寸 115
7.4.3焊接工艺参数 115
7.4.4焊接技术要领 115
7.5焊条下向焊常见缺陷的危害及预防措施 117
7.5.1焊缝成形缺陷 117
7.5.2未熔合 119
7.5.3气孔与夹渣 119
7.5.4裂纹 120
第8章 药芯焊丝焊接工艺 121
8.1药芯焊丝气体保护焊接工艺 121
8.1.1工艺原理 121
8.1.2工艺特点 121
8.1.3气体保护药芯焊丝焊接工艺 122
8.2自保护药芯焊丝焊接工艺 125
8.2.1自保护药芯焊丝半自动焊的工艺特点 125
8.2.2自保护药芯焊丝半自动焊焊接工艺参数 126
8.2.3自保护药芯焊丝操作技术 126
8.3自保护药芯焊丝焊接常见缺陷及防止方法 129
8.3.1气孔的产生原因及防止方法 129
8.3.2夹渣的产生原因及防止方法 129
8.3.3未熔合的产生原因及防止方法 130
8.3.4咬边的产生原因及防止方法 130
8.3.5焊缝成形不良的产生原因及防止方法 130
第9章 STT焊接技术 132
9.1STT焊接技术的原理及特点 132
9.1.1STT焊接技术的工作原理 132
9.1.2STT焊接技术的特点 132
9.2STT焊接设备 133
9.2.1焊接电源 133
9.2.2气瓶 133
9.2.3气管 133
9.2.4气体流量计 133
9.2.5送丝机 133
9.2.6焊枪 133
9.2.7连接导线 134
9.3STT操作方法及焊接工艺 134
9.3.1坡口准备 134
9.3.2焊前预热 134
9.3.3根焊道的焊接 134
9.3.4填充焊道的焊接 135
9.3.5盖面焊道的焊接 136
9.3.6焊接工艺参数 136
9.4RMD焊接技术简介 136
9.4.1RMD的控制原理及特点 136
9.4.2RMD焊接工艺参数 137
第10章 双管联焊技术 138
10.1双管联焊施工工艺简介 138
10.1.1国内外双管联焊施工概况 138
10.1.2双管联焊施工的优势 138
10.1.3双管联焊施工的局限性 139
10.2双管联焊焊接工艺 139
10.2.1手工电弧焊(SMAW)+埋弧自动焊(SAW) 139
10.2.2STT+埋弧自动焊(SAW) 143
10.2.3双面埋弧自动焊接工艺 147
10.3双联管的运输 151
10.3.1一次倒管 151
10.3.2二次倒运 152
10.3.3布管 152
第11章 管道自动焊技术 153
11.1管道自动焊的分类及特点 153
11.1.1管道自动焊概述 153
11.1.2管道自动焊的分类 154
11.1.3管道自动焊的特点 154
11.2焊接坡口的制备及组装要求 156
11.2.1V形坡口 156
11.2.2U形坡口 156
11.2.3复合形坡口 157
11.2.4X形坡口 158
11.2.5I形坡口 159
11.3管道自动内焊机及焊接工艺 159
11.3.1概述 159
11.3.2管道自动内焊设备 159
11.3.3管道自动内焊坡口的准备 161
11.3.4管道内焊机焊接工艺 161
11.4管道自动外焊(根焊)设备及工艺 162
11.4.1概述 162
11.4.2管道自动外焊(根焊)设备 163
11.4.3焊接操作及焊接工艺 163
11.5管道自动外焊(填充、盖面)设备及工艺 165
11.5.1概述 165
11.5.2焊接设备 166
11.5.3焊接操作及焊接工艺 167
11.6双焊枪焊接工艺简介 169
11.6.1双焊枪焊接工艺的特点 169
11.6.2机组设备配备 169
11.6.3机组人员组织 170
第12章 管道无损检测方法 171
12.1无损检测概论 171
12.1.1无损检测的定义与分类 171
12.1.2无损检测的目的 171
12.1.3无损检测的应用特点 172
12.2管道焊缝中常见缺陷及其产生原因 173
12.2.1外观缺陷 173
12.2.2气孔 174
12.2.3夹渣 175
12.2.4裂纹 175
12.2.5未焊透 176
12.2.6未熔合 176
12.3管道的射线检测 176
12.3.1射线检测的基本原理 176
12.3.2通用射线检测设备 179
12.3.3管道爬行器 180
12.3.4射线检测操作步骤 182
12.3.5底片评定 183
12.3.6辐射防护 183
12.4管道的超声波检测 184
12.4.1超声波的发生及其性质 184
12.4.2超声波检测原理 186
12.4.3超声波检测方法的分类 187
12.4.4超声波试块 188
12.4.5超声脉中显示波检测程序 189
12.5管道的全自动超声波检测 190
12.5.1全自动超声波简介 190
12.5.2全自动超声波检测原理 191
12.5.3长输管道全自动超声波检测 191
12.6其它检测方法 195
12.6.1磁粉检测 195
12.6.2渗透检测 200
第13章 长输管道典型焊接工艺简介 204
13.1陕京输气管道工程焊接工艺简介 204
13.1.1工程概况 204
13.1.2焊接工艺的选择 204
13.1.3焊接工艺参数 205
13.2西气东输一线管道工程焊接工艺简介 206
13.2.1工程简介 206
13.2.2管道全位置自动焊工艺 207
13.2.3药芯焊丝半自动焊工艺 209
13.2.4连头返修焊工艺 211
13.2.5焊接工艺应用情况及影响 212
13.3西气东输冀宁支线工程焊接工艺简介 213
13.3.1工程简介 213
13.3.2Noreast内焊机根焊+Noreast外焊机填充、盖面焊工艺 213
13.3.3连头焊工艺(焊条上向根焊十焊条下向填充、盖面焊) 215
13.3.4返修焊工艺(焊条上向根焊+焊条下向填充、盖面焊) 215
13.3.5焊接工艺应用情况及影响 216
13.4国外某天然气管道工程 216
13.4.1工程简介 216
13.4.2药芯焊丝半自动焊 217
13.4.3手工焊接工艺 218
13.4.4手工焊返修工艺 219
13.4.5焊接工艺应用情况及影响 220
附录 221
附录1焊工培训考试及管理 221
附录2油气长输管道工程施工及验收规范(摘要)(GB50369—2006) 231
附录3管道及有关设施的焊接(摘要)(APIStd1104—2001) 244
附录4石油天然气金属管道焊接工艺评定(摘要)(SY/T0452——2002) 254
附录5现场设备工业管道焊接工程施工及验收规范(摘要(GB50236—1998) 259
附录6锅炉压力容器压力管道焊工考试与管理规则(摘要)(国质检锅[2002]109号) 265
附录7钢质管道焊接及验收(摘要(SY/T4103—2006) 276
参考文献 286