图书介绍
实用机械加工工艺手册pdf电子书版本下载
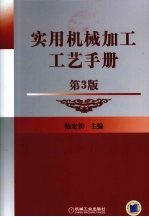
- 陈宏钧主编 著
- 出版社: 北京:机械工业出版社
- ISBN:9787111257714
- 出版时间:2009
- 标注页数:1785页
- 文件大小:508MB
- 文件页数:1816页
- 主题词:机械加工-工艺-技术手册
PDF下载
下载说明
实用机械加工工艺手册PDF格式电子书版下载
下载的文件为RAR压缩包。需要使用解压软件进行解压得到PDF格式图书。建议使用BT下载工具Free Download Manager进行下载,简称FDM(免费,没有广告,支持多平台)。本站资源全部打包为BT种子。所以需要使用专业的BT下载软件进行下载。如 BitComet qBittorrent uTorrent等BT下载工具。迅雷目前由于本站不是热门资源。不推荐使用!后期资源热门了。安装了迅雷也可以迅雷进行下载!
(文件页数 要大于 标注页数,上中下等多册电子书除外)
注意:本站所有压缩包均有解压码: 点击下载压缩包解压工具
图书目录
第1章 机械制造常用名词术语 1
1 机械制造工艺基本术语 1
1.1 一般术语 1
1.2 典型表面加工术语 1
1.3 冷作、钳工及装配常用术语 9
2 热处理名词术语 11
3 机械制造工艺管理名词术语 17
3.1 工艺管理术语 17
3.2 工艺装备管理术语 17
3.3 质量管理和质量保证术语 18
3.4 定置管理术语 22
第2章 机械加工工艺规程的设计及现场工艺管理 23
第1节 机械加工工艺规程的编制 23
1 机械加工工艺规程的作用 23
2 机械加工工艺过程的组成 23
3 机械加工工艺规程的制订 23
3.1 工艺规程制订原则 23
3.2 制订工艺规程所需原始资料 23
3.3 工艺规程制订程序 24
4 工艺过程设计中应考虑的主要问题 24
4.1 定位基准选择 24
4.2 零件表面加工方法的选择 25
4.2.1 加工方法选择的原则 25
4.2.2 各类表面的加工方案及适用范围 25
4.3 加工顺序的安排 27
4.3.1 加工阶段的划分 27
4.3.2 工序的合理组合 27
4.3.3 加工顺序的安排 27
5 工序设计 28
5.1 工序基准的选择 28
5.2 工序尺寸的确定 28
5.2.1 确定工序尺寸的方法 28
5.2.2 工艺尺寸链的计算参数与计算公式 28
5.2.3 工艺尺寸链的基本类型与工序尺寸的计算 30
5.3 加工余量的确定 36
5.4 机床的选择 37
5.5 工艺装备的选择 38
5.6 切削用量的选择 38
5.7 时间定额的确定 38
6 工艺文件格式及填写规则 38
6.1 机械加工工艺过程卡片格式及填写规则 38
6.2 机械加工工序卡片格式及填写规则 40
6.3 标准零件(或典型零件)工艺过程卡片格式及填写规则 40
第2节 零件图样的工艺性审查 43
1 产品结构工艺性审查 43
1.1 产品结构工艺性审查内容和程序 43
1.2 零件结构工艺性的基本要求 44
2 零件结构的切削加工工艺性 45
2.1 工件便于在机床或夹具上装夹的图例 45
2.2 减少装夹次数的图例 46
2.3 减少刀具调整与走刀次数的图例 46
2.4 采用标准刀具减少刀具种类的图例 46
2.5 减少切削加工难度的图例 46
2.6 减少加工量的图例 52
2.7 加工时便于进刀、退刀和测量的图例 52
2.8 保证零件在加工时刚度的图例 52
2.9 有利于改善刀具切削条件与提高刀具寿命的图例 52
3 一般装配对零部件结构工艺性的 要求 57
3.1 组成单独部件或装配单元 57
3.2 应具有合理的装配基面 58
3.3 考虑装配的方便性 59
3.4 考虑拆卸的方便性 59
3.5 考虑装配的零部件之间结构的合理性 60
3.6 避免装配时的切削加工 61
3.7 选择合理的调整补偿环 62
3.8 减少修整外形的工作量 62
4 零件结构的热处理工艺性 63
4.1 防止热处理零件开裂的结构要求 63
4.2 防止热处理零件变形及硬度不均的结构要求 65
4.3 热处理齿轮零件的结构要求 68
第3节 典型零件机械加工工艺过程举例 69
1 轴类零件 69
1.1 调整偏心轴 69
1.2 单拐曲轴 70
1.3 连杆螺钉 73
2 套类零件 75
2.1 缸套 75
2.2 活塞 76
2.3 偏心套 78
3 齿轮、花键、丝杆类零件 80
3.1 齿轮 80
3.2 锥齿轮 81
3.3 齿轮轴 82
3.4 矩形齿花键轴 84
3.5 矩形齿花键套 85
3.6 丝杆 86
4 连杆类零件 88
4.1 两孔连杆 88
4.2 三孔连杆 91
5 箱体类零件 93
5.1 减速器 93
5.2 曲轴箱 97
6 其他类零件 101
6.1 轴承座 101
6.2 带轮 102
6.3 轴瓦 103
第4节 生产现场工艺管理及工艺纪律 105
1 生产现场工艺管理 105
1.1 生产现场工艺管理的主要任务和内容 105
1.2 生产现场定置管理方法及考核 106
2 工艺纪律管理 106
2.1 基本要求 106
2.2 工艺纪律的主要内容 106
2.3 工艺纪律的考核 107
第3章 机械加工质量 108
第1节 机械加工精度 108
1 影响加工精度的因素及改善措施 108
1.1 影响尺寸精度的因素及改善措施 108
1.2 影响形状精度的因素及改善措施 108
1.3 影响位置精度的因素及改善措施 108
2 各种加工方法的加工误差 111
3 机械加工的经济精度 112
3.1 加工路线与所能达到的公差等级和表面粗糙度 112
3.2 各种加工方法能达到的尺寸经济精度 112
3.3 各种加工方法能达到的形状经济精度 118
3.4 各种加工方法能达到的位置经济精度 118
第2节 机械加工表面质量 121
1 表面粗糙度 121
1.1 各种加工方法能达到的表面粗糙度 121
1.2 影响加工表面粗糙度的因素及改善措施 122
1.3 表面粗糙度与加工精度和配合之间的关系 122
1.4 各种连接表面的粗糙度 125
2 加工硬化与残余应力 125
2.1 加工表面层的冷作硬化 125
2.2 残余应力 127
3 机械加工中的振动 127
3.1 强迫振动的特点、产生原因与消减措施 127
3.2 自激振动(颤振)的特点、产生原因与消减措施 127
第4章 机械制图 129
第1节 基本规定 129
1 图纸幅面和格式 129
1.1 图纸幅面尺寸 129
1.2 图框格式及尺寸 129
2 标题栏和明细栏 130
2.1 标题栏方位 130
2.2 标题栏 131
2.3 明细栏 131
3 比例 132
3.1 术语 132
3.2 比例系列 132
3.3 标注方法 132
4 字体 132
4.1 基本要求 132
4.2 字体示例 133
5 图线 135
6 剖面符号 139
第2节 图样画法 139
1 视图 139
1.1 基本视图名称及其投影方向的规定 139
1.2 视图的类型 140
2 剖视 142
2.1 剖视图 142
2.2 剖切面 142
2.3 剖切符号 144
2.4 剖视图的配置 144
2.5 剖切位置与剖视图的标注 144
3 断面图 145
4 局部放大图 146
5 简化画法 147
5.1 基本要求 147
5.2 特定简化画法 148
5.3 对称画法 150
5.4 剖切平面前、后结构及剖面符号简化画法 150
5.5 轮廓画法 151
5.6 相同、成组结构或要素的画法 152
5.7 特定结构或要素的画法 153
5.8 特定件画法 154
第3节 尺寸注法 156
1 基本规则 156
2 标注尺寸三要素 156
2.1 尺寸数字 156
2.2 尺寸线 157
2.3 尺寸界线 159
3 标注尺寸的符号 160
4 简化注法 162
4.1 简化注法基本规定 162
4.2 简化注法图例 162
第4节 常用零件画法 166
1 螺纹及螺纹紧固件 166
1.1 螺纹的规定画法 166
1.2 螺纹的标注 167
1.3 装配图中螺纹紧固件的画法 169
1.4 常用紧固件的简化画法 170
2 齿轮、齿条、蜗杆、蜗轮及链轮的画法 171
2.1 齿轮、齿条、蜗轮及链轮的画法 171
2.2 齿轮、蜗杆、蜗轮啮合画法 172
3 矩形花键的画法及其尺寸标注 173
4 弹簧的画法 174
4.1 螺旋弹簧的画法 174
4.2 碟形弹簧的画法 174
4.3 平面涡卷弹簧的画法 175
4.4 板弹簧的画法 175
4.5 装配图中弹簧的画法 175
5 中心孔表示法 175
5.1 中心孔符号 175
5.2 中心孔在图样上的标注 175
6 滚动轴承表示法 175
6.1 基本规定 175
6.2 简化画法 182
6.3 规定画法 187
6.4 应用示例 187
7 动密封圈表示法 188
7.1 基本规定 188
7.2 简化画法 188
7.3 规定画法 194
7.4 应用举例 194
第5章 机械零件 195
第1节 螺纹 195
1 普通螺纹(M) 195
1.1 普通螺纹牙型 195
1.2 普通螺纹直径与螺距系列 195
1.3 普通螺纹的基本尺寸 198
1.4 普通螺纹的公差 201
1.5 标记方法及示例 211
2 梯形螺纹(30°)(Tr) 212
2.1 梯形螺纹牙型 212
2.2 梯形螺纹直径与螺距系列 213
2.3 梯形螺纹基本尺寸 213
2.4 梯形螺纹公差 215
2.5 梯形螺纹旋合长度 220
2.6 梯形螺纹代号与标记 221
3 锯齿形螺纹(3°、30°)(B) 221
3.1 锯齿形(3°、30°)螺纹牙型 221
3.2 锯齿形螺纹的直径与螺距系列 222
3.3 锯齿形螺纹基本尺寸 222
3.4 锯齿形螺纹公差 224
3.5 锯齿形螺纹标记方法及示例 228
4 55°管螺纹 228
4.1 55°密封管螺纹 228
4.2 55°非密封管螺纹 231
5 60°密封管螺纹 232
5.1 螺纹术语及代号 232
5.2 螺纹牙型及牙型尺寸 232
5.3 圆锥管螺纹的基本尺寸及其公差 233
5.4 圆柱内螺纹的基本尺寸及公差 234
5.5 有效螺纹的长度 235
5.6 倒角对基准平面理论位置的影响 235
5.7 螺纹特征代号及标记示例 235
6 米制管螺纹(60°) 236
6.1 一般密封米制管螺纹(ZM、M) 236
6.2 非密封米制管螺纹(M) 237
7 英制惠氏螺纹 237
7.1 牙型 237
7.2 英制惠氏螺纹的标准系列 238
7.3 基本尺寸 238
7.4 公差 239
7.5 标记示例 241
第2节 齿轮 241
1 渐开线圆柱齿轮 241
1.1 基本齿廓和模数 241
1.2 圆柱齿轮的几何尺寸计算 242
1.3 齿轮精度 244
1.4 齿轮检验项目 263
1.5 齿厚 263
1.6 侧隙 263
1.7 中心距和轴线平行度 264
1.8 齿轮的接触斑点 264
1.9 齿面表面粗糙度的推荐值 265
1.10 齿轮坯的精度 265
1.11 GB/T 10095—1988版渐开线圆柱齿轮精度 267
2 齿条 276
2.1 齿条的几何尺寸计算 276
2.2 齿条精度 276
3 锥齿轮 282
3.1 锥齿轮基本齿廓尺寸参数 282
3.2 模数 282
3.3 直齿锥齿轮几何尺寸计算 282
3.4 锥齿轮精度 285
3.5 锥齿轮及锥齿轮副公差表 290
3.6 锥齿轮齿坯要求 302
4 圆柱蜗杆和蜗轮 303
4.1 圆柱蜗杆的类型及基本齿廓 303
4.2 圆柱蜗杆的主要参数 304
4.3 圆柱蜗杆传动几何尺寸计算 309
4.4 圆柱蜗杆、蜗轮精度 311
4.5 蜗杆、蜗轮及其传动的公差表 317
4.6 齿坯要求 324
第3节 键、花键和销 325
1 键 325
1.1 平键 325
1.2 半圆键 330
1.3 楔键 333
1.4 切向键 337
2 花键 339
2.1 花键连接的类型、特点和使用 339
2.2 矩形花键 340
2.2.1 矩形花键尺寸系列 340
2.2.2 矩形花键的公差与配合 342
2.2.3 标记示例 343
2.3 圆柱直齿渐开线花键 343
2.3.1 渐开线花键的模数系列 343
2.3.2 渐开线花键标准压力角 344
2.3.3 渐开线花键术语、代号及定义 344
2.3.4 渐开线花键的基本尺寸计算公式 345
2.3.5 外花键大径基本尺寸 346
2.3.6 渐开线花键公差与配合 349
2.3.7 图样标记示例 349
2.3.8 公差数值表 349
3 销 360
3.1 销的类型及应用范围 360
3.2 常用销的规格尺寸 362
第4节 链和链轮 366
1 滚子链传动 366
1.1 滚子链的结构形式和规格尺寸 366
1.2 滚子链用附件 367
1.3 滚子链链轮 367
1.3.1 滚子链链轮齿槽形状 367
1.3.2 三圆弧一直线齿槽形状和尺寸计算 370
1.3.3 滚子链链轮轴向齿廓及尺寸 371
1.3.4 滚子链链轮的基本参数和主要尺寸 371
1.3.5 链轮公差 371
1.3.6 滚子链链轮常用材料及热处理 373
2 齿形链传动 373
2.1 齿形链的基本参数和尺寸 373
2.2 齿形链链轮 373
2.2.1 链轮齿形与基本参数 373
2.2.2 齿形链链轮轴向齿廓尺寸 373
2.2.3 齿形链链轮检验项目及公差 373
2.2.4 齿形链链轮轮坯公差 373
第5节 滚动轴承 377
1 滚动轴承的分类 377
2 滚动轴承代号的构成 378
2.1 基本代号 378
2.2 前置、后置代号 383
2.3 轴承代号示例 386
3 常用滚动轴承型号及外形尺寸举例 386
3.1 深沟球轴承 386
3.2 调心球轴承 389
3.3 双列圆柱滚子轴承 390
3.4 圆锥滚子轴承 392
3.5 双列圆锥滚子轴承 393
3.6 角接触球轴承 394
3.7 推力球轴承 397
4 滚动轴承的配合 398
第6节 圆锥和棱体 399
1 锥度、锥角及基公差 399
1.1 圆锥的术语及定义 399
1.2 锥度与锥角系列 400
1.3 圆锥公差 402
2 棱体 404
2.1 棱体的术语及定义 404
2.2 棱体的角度与斜度系列 406
第7节 常用零件结构要素 406
1 中心孔 406
1.1 60°中心孔 406
1.2 75°、90°中心孔 408
2 各类槽 409
2.1 退刀槽 409
2.2 砂轮越程槽 411
2.3 润滑槽 413
2.4 T形槽 414
2.5 燕尾槽 416
3 零件倒圆与倒角 416
4 球面半径 417
5 螺纹零件 417
5.1 紧固件外螺纹零件末端 417
5.2 普通外螺纹收尾、肩距、退刀槽和倒角尺寸 418
5.3 普通内螺纹收尾、肩距、退刀槽和倒角尺寸 419
5.4 普通螺纹的内、外螺纹余留长度、钻孔余留深度和螺栓突出螺母的末端长度 420
5.5 紧固件用通孔和沉孔 422
5.6 梯形螺纹的收尾、退刀槽和倒角尺寸 424
5.7 米制锥螺纹的结构要素 425
5.8 圆柱管螺纹的收尾、退刀槽和倒角尺寸 426
第6章 常用材料及热处理 428
第1节 钢 428
1 金属材料性能的名词术语 428
2 钢的分类 429
3 钢牌号表示方法 430
3.1 牌号表示方法的基本原则 430
3.2 钢铁材料的名称及其符号 431
3.3 钢牌号表示方法的举例 432
4 常用钢的品种、性能和用途 435
4.1 结构钢 435
4.1.1 碳素结构钢 435
4.1.2 优质碳素结构钢 436
4.1.3 低合金高强度钢 439
4.1.4 合金结构钢 440
4.1.5 易切削结构钢 451
4.1.6 非调质机械结构钢 452
4.1.7 弹簧钢 452
4.2 工具钢 454
4.2.1 碳素工具钢 454
4.2.2 合金工具钢 455
4.2.3 高速工具钢 458
4.3 轴承钢 460
4.4 特种钢 461
4.4.1 不锈钢 461
4.4.2 耐热钢 467
5 型钢 471
5.1 热轧圆钢和方钢尺寸规格 471
5.2 热轧六角钢和八角钢尺寸规格 471
5.3 冷拉圆钢、方钢、六角钢尺寸规格 473
5.4 热轧扁钢的尺寸规格 474
5.5 优质结构钢冷拉扁钢的尺寸规格 476
5.6 热轧等边角钢的尺寸规格 476
5.7 热轧不等边角钢的尺寸规格 478
5.8 热轧工字钢的尺寸规格 479
5.9 热轧槽钢的尺寸规格 480
6 钢板和钢带 481
6.1 热轧钢板和钢带 481
6.2 冷轧钢板和钢带 483
6.3 不锈钢热轧钢板 484
6.4 不锈钢冷轧钢板 485
6.5 锅炉用钢板的牌号、板厚及力学和工艺性能 487
6.6 压力容器用钢板的牌号、板厚及力学和工艺性能 487
7 钢管 488
7.1 无缝钢管 488
7.2 结构用无缝钢管 495
7.3 结构用不锈钢无缝钢管 497
7.4 不锈钢冷拔(轧)小直径无缝钢管的尺寸规格 500
7.5 直缝电焊钢管 501
8 钢丝 504
8.1 重要用途低碳钢丝 504
8.2 优质碳素结构钢丝 505
8.3 合金结构钢丝 506
8.4 碳素工具钢丝 507
8.5 合金工具钢丝 507
8.6 高速工具钢丝 508
8.7 碳素弹簧钢丝 508
8.8 重要用途碳素弹簧钢丝 509
8.9 合金弹簧钢丝 510
8.10 油淬火—回火弹簧钢丝 510
8.11 熔化焊用钢丝 512
8.12 气体保护焊用钢丝 512
8.13 焊接用不锈钢丝 513
9 常用钢的火花鉴别法 513
10 钢材的标记 515
10.1 钢材的标记代号 515
10.2 钢材的涂色标记 515
第2节 铸钢 517
1 一般工程用铸造碳钢 517
2 焊接结构用碳素钢铸件 518
3 合金铸钢件 518
4 高锰钢铸件的牌号、力学性能和适用范围 520
5 工程结构用中、高强度不锈钢铸件 520
6 一般用途耐热钢和合金铸件 521
第3节 铸铁 522
1 铸铁的分类 522
2 铸铁牌号表示方法 522
2.1 铸铁名称、代号及牌号表示方法 522
2.2 铸铁牌号表示方法举例 523
3 常用铸铁的性能和用途 523
3.1 灰铸铁 523
3.2 球墨铸铁 523
3.3 可锻铸铁 525
3.4 蠕墨铸铁 526
3.5 耐热铸铁 526
3.6 高硅耐蚀铸铁 528
3.7 耐磨铸铁 528
3.8 抗磨白口铸铁 529
第4节 有色金属及其合金 530
1 有色金属及其合金产品代号表示方法 530
2 铜及铜合金 532
2.1 加工铜的牌号、代号及主要特性和应用举例 532
2.2 加工黄铜的牌号、代号及主要特性和应用举例 532
2.3 加工青铜的牌号、代号及主要特性和应用举例 532
2.4 加工白铜的牌号、代号及主要特性和应用举例 538
2.5 铜及铜合金力学性能 539
2.6 铜及铜合金工艺性能 541
3 铸造铜合金 542
4 铝及铝合金 547
4.1 变形铝及铝合金的新旧牌号对照 547
4.2 常用铝及铝合金加工产品的牌号及主要特性和应用举例 548
4.3 铝及铝合金热处理工艺参数 552
5 铸造铝合金 553
5.1 铸造铝合金的牌号、代号和力学性能 553
5.2 铸造铝合金的主要特性和应用举例 556
5.3 铸造铝合金热处理工艺规范 558
6 铸造轴承合金 558
第5节 粉末冶金材料 559
1 粉末冶金材料的分类及应用举例 559
2 粉末冶金铁基结构材料 560
3 粉末冶金摩擦材料 562
4 粉末冶金减摩材料牌号及力学性能 564
5 烧结不锈钢过滤元件 565
第6节 非金属材料 567
1 工程塑料及其制品 567
1.1 常用工程塑料的性能特点及应用 567
1.2 工程塑料棒材 567
1.3 工程塑料管材 569
2 橡胶、石棉及其制品 571
2.1 常用橡胶的特性及用途 571
2.2 橡胶、石棉制品 573
第7节 热处理 575
1 热处理工艺分类及代号 575
2 热处理工艺 576
2.1 钢件的整体热处理 576
2.1.1 退火 576
2.1.2 正火 577
2.1.3 淬火 577
2.1.4 回火 578
2.1.5 冷处理 579
2.2 钢的表面热处理 579
2.3 钢的化学热处理 579
3 常用金属材料热处理工艺参数 580
3.1 优质碳素结构钢常规热处理工艺参数 580
3.2 合金结构钢常规热处理工艺参数 582
3.3 弹簧钢常规热处理工艺参数 587
3.4 碳素工具钢常规热处理工艺参数 588
3.5 合金工具钢常规热处理工艺参数 590
3.6 高速工具钢常规热处理工艺参数 595
3.7 轴承钢常规热处理工艺参数 597
第7章 金属切削机床及辅具 599
第1节 金属切削机床型号编制方法 599
1 通用机床型号表示方法 599
1.1 型号表示方法 599
1.2 机床的分类及类代号 599
1.3 机床的特性代号 599
1.4 机床的组、系代号及主参数 600
1.5 通用机床的设计顺序号 600
1.6 主轴数和第二主参数的表示方法 600
1.7 机床的重大改进顺序号 600
1.8 其他特性代号及其表示方法 600
1.9 企业代号及其表示方法 600
1.10 金属切削机床统一名称和类、组、系划分 600
2 专用机床的型号 600
3 机床自动线的型号 600
第2节 通用机床技术参数与辅具 614
1 车床 614
1.1 常用车床的型号与技术参数 614
1.1.1 卧式车床的型号与技术参数 614
1.1.2 马鞍车床的型号与技术参数 614
1.1.3 立式车床的型号与技术参数 614
1.1.4 转塔车床、回轮车床的型号与技术参数 614
1.1.5 仿形车床的型号与技术参数 614
1.1.6 曲轴车床的型号与技术参数 614
1.1.7 数控卧式车床的型号与技术参数 614
1.2 普通车床辅具 624
1.2.1 刀杆 624
1.2.2 刀夹 627
1.2.3 加工螺纹用辅具 628
2 铣床 629
2.1 常用铣床的型号与技术参数 629
2.1.1 卧式升降台铣床的型号与技术参数 629
2.1.2 万能升降台铣床的型号与技术参数 629
2.1.3 立式升降台铣床、数控立式升降台铣床的型号与技术参数 629
2.1.4 工具铣床、数控工具铣床的型号与技术参数 629
2.1.5 龙门铣床的型号与技术参数 629
2.2 铣床辅具 636
2.2.1 中间套 636
2.2.2 铣刀杆 639
2.2.3 铣夹头 650
3 钻床 652
3.1 常用钻床的型号与技术参数 652
3.1.1 台式钻床的型号与技术参数 652
3.1.2 立式钻床的型号与技术参数 652
3.1.3 摇臂钻床的型号与技术参数 652
3.1.4 深孔钻床的型号与技术参数 652
3.2 钻床辅具 656
3.2.1 过渡套、接长套、夹紧套 656
3.2.2 接杆 661
3.2.3 刀杆 664
3.2.4 夹头 669
3.2.5 扁尾锥柄用楔 672
4 镗床 672
4.1 常用镗床的型号与技术参数 672
4.1.1 卧式铣镗床的型号与技术参数 672
4.1.2 数控卧式镗床的型号与技术参数 672
4.1.3 落地镗床、数控落地铣镗床的型号与技术参数 672
4.1.4 坐标镗床的型号与技术参数 672
4.1.5 精镗床的型号与技术参数 672
4.2 镗床辅具 677
4.2.1 镗刀杆 677
4.2.2 镗杆 689
4.2.3 镗刀架 690
4.2.4 接杆 692
4.2.5 镗套与衬套 694
4.2.6 其他 698
5 磨床 699
5.1 常用磨床的型号与技术参数 699
5.1.1 万能外圆磨床的型号与技术参数 699
5.1.2 无心外圆磨床的型号与技术参数 699
5.1.3 内圆磨床的型号与技术参数 699
5.1.4 卧轴矩台平面磨床的型号与技术参数 699
5.1.5 立轴矩台平面磨床的型号与技术参数 699
5.1.6 卧轴圆台平面磨床的型号与技术参数 699
5.1.7 立轴圆台平面磨床的型号与技术参数 699
5.1.8 万能工具磨床的型号与技术参数 699
5.1.9 曲轴磨床的型号与技术参数 699
5.1.10 花键轴磨床的型号与技术参数 699
5.2 磨床辅具 724
5.2.1 顶尖 724
5.2.2 接杆及螺钉 724
6 拉床 727
6.1 常用拉床的型号与技术参数 727
6.1.1 立式拉床的型号与技术参数 727
6.1.2 卧式拉床的型号与技术参数 727
6.2 拉床辅具 728
6.2.1 接头 728
6.2.2 夹头、扳手 729
6.2.3 导套、垫片及支座 732
7 齿轮加工机床 737
7.1 常用齿轮加工机床的型号与技术参数 737
7.1.1 滚齿机的型号与技术参数 737
7.1.2 插齿机的型号与技术参数 743
7.1.3 剃齿机的型号与技术参数 744
7.1.4 花键轴铣床的型号与技术参数 744
7.2 齿轮加工机床辅具 746
7.2.1 滚齿刀杆 746
7.2.2 刀垫 747
7.2.3 接套 747
8 螺纹加工机床 748
8.1 专用螺纹车床的型号与技术参数 748
8.2 螺纹铣床的型号与技术参数 748
8.3 螺纹磨床的型号与技术参数 748
8.4 攻丝机的型号与技术参数 748
8.5 滚丝机的型号与技术参数 752
8.6 搓丝机的型号与技术参数 752
9 刨床与插床 752
9.1 常用刨床、插床的型号与技术参数 752
9.1.1 牛头刨床的型号与技术参数 752
9.1.2 单臂刨床的型号与技术参数 752
9.1.3 龙门刨床、数控龙门刨床的型号与技术参数 752
9.1.4 插床的型号与技术参数 752
9.2 刨床辅具 752
9.2.1 槽刨刀刀杆 752
9.2.2 刨刀刀杆 752
10 锯床 755
10.1 带锯床的型号与技术参数 755
10.2 圆锯床的型号与技术参数 755
10.3 弓锯床的型号与技术参数 755
第8章 机床夹具 758
第1节 通用夹具 758
1 顶尖 758
1.1 固定顶尖 758
1.2 回转顶尖形式及规格 758
1.3 内拨顶尖 758
1.4 夹持式内拨顶尖 762
1.5 外拨顶尖 762
1.6 内锥孔顶尖 762
1.7 夹持式内锥孔顶尖 762
2 夹头 764
2.1 鸡心卡头 764
2.2 卡环 764
2.3 夹板 765
2.4 车床用快换卡头 765
3 拨盘 765
3.1 C型拨盘 765
3.2 D型拨盘 765
4 卡盘 767
4.1 三爪自定心卡盘 767
4.2 四爪单动卡盘 767
5 过渡盘 773
5.1 C型三爪自定心卡盘用过渡盘 773
5.2 D型三爪自定心卡盘用过渡盘 773
5.3 C型四爪单动卡盘用过渡盘 774
5.4 D型四爪单动卡盘用过渡盘 774
6 花盘 775
7 分度头 775
7.1 机械分度头 775
7.2 等分分度头 775
8 机床用平口台虎钳 775
8.1 机床用平口台虎钳规格尺寸 775
8.2 角度压紧机用平口台虎钳规格尺寸 775
8.3 可倾机用平口台虎钳规格尺寸 775
8.4 正弦机用平口台虎钳规格尺寸 780
9 常用回转工作台 781
10 吸盘 781
10.1 矩形电磁吸盘规格尺寸 781
10.2 圆形电磁吸盘规格尺寸 781
10.3 矩形永磁吸盘规格尺寸 781
10.4 圆形永磁吸盘规格尺寸 781
10.5 多功能电磁吸盘规格尺寸 781
11 铣头、插头、镗头 781
11.1 铣头规格尺寸 781
11.2 插头规格尺寸 781
11.3 镗头规格尺寸 781
第2节 专用夹具 789
1 机床夹具设计基本要求 789
1.1 工件定位原理及其应用 789
1.1.1 六点定位原理 789
1.1.2 工件的定位要求 790
1.1.3 常用定位方法和定位元件所能限制的自由度 790
1.1.4 常见加工形式中应限制的自由度 794
1.2 对夹紧装置的基本要求 796
1.3 夹具的对定 797
1.3.1 夹具对切削运动的定位 797
1.3.2 夹具对刀具的定位 799
1.3.3 夹具分度与转位的对定 805
2 机床夹具常用标准零部件 806
2.1 定位件 806
2.2 导向件 816
2.3 支承件 824
2.4 夹紧件 831
2.5 对刀件 844
3 专用夹具典型结构实例 846
3.1 车床夹具的典型结构 846
3.1.1 车床夹具的特点及设计要求 846
3.1.2 车床夹具典型结构的技术参数 847
3.1.3 车床夹具类型结构举例 849
3.2 钻床夹具 857
3.2.1 钻床夹具的特点和主要类型 857
3.2.2 钻(镗)床夹具典型结构的技术要求 857
3.2.3 钻夹具类型结构举例 861
3.3 镗床夹具 865
3.3.1 镗床夹具设计要点 865
3.3.2 镗床夹具典型结构的技术要求 865
3.3.3 镗床夹具类型结构举例 865
3.4 铣床夹具 866
3.4.1 铣床夹具典型结构的技术要求 866
3.4.2 铣床夹具类型结构举例 871
3.5 磨床夹具 873
第3节 可调夹具 875
1 可调整夹具的特点、适用范围与设计要点 875
2 可调整夹具结构示例 875
第4节 组合夹具 878
1 组合夹具的使用范围与经济效果 878
2 组合夹具的系列、元件类别及作用 878
3 组合夹具典型结构举例 880
3.1 钻夹具 880
3.2 车夹具 882
3.3 铣、刨夹具 886
3.4 镗模 886
3.5 组合夹具的扩大使用 886
第9章 机械加工工序间加工余量 890
1 装夹及下料尺寸余量 890
1.1 棒材、板材及焊接后的板材结构件各部分加工余量示意 890
1.2 夹持长度及夹紧余量 890
1.3 下料尺寸余量 890
2 轴的加工余量 900
2.1 外圆柱表面加工余量及偏差 900
2.2 轴端面加工余量及偏差 903
2.3 槽的加工余量及公差 903
3 内孔加工余量及偏差 905
3.1 基孔制7级精度(H7)孔的加工 905
3.2 基孔制8级精度(H8)孔的加工 906
3.3 用金刚石刀精镗孔加工余量 906
3.4 研磨孔加工余量 906
3.5 单刃钻后深孔加工余量 907
3.6 刮孔加工余量 907
3.7 多边形孔拉削余量 907
3.8 内花键拉削余量 907
4 平面加工余量及偏差 907
4.1 平面第一次粗加工余量 907
4.2 平面粗刨后精铣加工余量 908
4.3 铣平面加工余量 908
4.4 磨平面加工余量 908
4.5 铣及磨平面时的厚度偏差 908
4.6 刮平面加工余量及偏差 908
4.7 凹槽加工余量及偏差 908
4.8 研磨平面加工余量 908
4.9 外表面拉削余量 908
5 切除渗碳层的加工余量 910
6 齿轮和花键的精加工余量 910
6.1 精滚齿和精插齿的齿厚加工余量 910
6.2 剃齿的齿厚加工余量 910
6.3 磨齿的齿厚加工余量 910
6.4 直径大于400mm渗碳齿轮的磨齿齿厚加工余量 910
6.5 珩齿加工余量 910
6.6 交错轴斜齿轮精加工的齿厚加工余量 910
6.7 锥齿轮精加工的齿厚加工余量 910
6.8 蜗轮精加工的齿厚加工余量 910
6.9 蜗杆精加工的齿厚加工余量 910
6.10 精铣花键的加工余量 910
6.11 磨花键的加工余量 910
7 有色金属及其合金的加工余量 912
7.1 有色金属及其合金零件的加工余量 912
7.2 有色金属及其合金圆筒形零件的加工余量 912
7.3 有色金属及其合金圆盘形零件的加工余量 912
7.4 有色金属及其合金壳体类零件的加工余量 912
第10章 刀具和磨料磨具 916
第1节 刀具材料及刀片 916
1 刀具切削部分的材料 916
1.1 对刀具切削部分材料性能的要求 916
1.2 常用刀具材料 916
1.2.1 常用高速钢牌号、力学性能及适用范围 916
1.2.2 硬质合金 917
1.2.3 陶瓷刀具材料 925
1.2.4 超硬刀具材料 926
2 刀片 927
2.1 硬质合金焊接刀片 927
2.1.1 常用焊接车刀刀片 927
2.1.2 基本型硬质合金焊接刀片 927
2.2 可转位硬质合金刀片 940
2.2.1 可转位硬质合金刀片的标记方法 940
2.2.2 带圆孔的可转位硬质合金刀片形式及基本尺寸 943
2.2.3 无孔可转位硬质合金刀片形式及基本尺寸 950
2.2.4 沉孔可转位硬质合金刀片形式及基本尺寸 952
2.2.5 硬质合金可转位铣刀片 955
2.3 可转位陶瓷刀片的型号与基本参数 957
第2节 车刀 960
1 刀具切削部分几何角度及其选择 960
1.1 刀具切削部分的几何角度 960
1.1.1 刀具切削部分的组成 960
1.1.2 确定刀具角度的三个辅助平面名称和定义 960
1.1.3 刀具的切削角度及其作用 961
1.1.4 车刀的工作角度 961
1.2 刀具切削部分几何参数的选择 963
1.2.1 前角的选择 963
1.2.2 车刀前面切削刃和刀尖形状的选择 964
1.2.3 后角的选择 965
1.2.4 主偏角的选择 966
1.2.5 副偏角的选择 966
1.2.6 刃倾角的选择 967
1.2.7 过渡刃的选择 967
2 车刀类型及规格尺寸 967
2.1 高速钢车刀条 967
2.2 焊接车刀 970
2.2.1 硬质合金焊接车刀表示方法 970
2.2.2 硬质合金外表面车刀 971
2.2.3 硬质合金内表面车刀 977
2.3 可转位车刀 980
2.3.1 可转位车刀刀片的夹固形式 980
2.3.2 可转位车刀型号表示规则 981
2.3.3 优先采用的形式和尺寸 985
2.3.4 可转位内孔车刀 990
2.4 机夹车刀 994
2.4.1 机夹切断车刀 994
2.4.2 机夹螺纹车刀 995
第3节 孔加工刀具 997
1 麻花钻 997
1.1 标准麻花钻头的切削角度 997
1.2 高速钢麻花钻的类型、直径范围及标准代号 997
1.3 硬质合金麻花钻类型、直径范围及标准代号 1000
1.4 攻螺纹前钻孔用阶梯麻花钻 1001
2 可转位钻头类型、直径范围及标准代号 1002
3 扩孔钻 1003
4 锪钻 1004
5 中心钻 1005
6 扁钻 1007
7 深孔钻 1007
7.1 单刃外排屑深孔钻 1007
7.2 双刃外排屑深孔钻 1007
7.3 单刃内排屑深孔钻 1009
7.4 多刃错齿内排屑深孔钻 1010
7.5 机夹可转位内排屑深孔钻的形式及加工范围 1011
7.6 BTA内排屑深孔钻的形式及加工范围 1012
7.7 喷吸钻的结构形式及规格尺寸 1012
7.8 DF系统深孔钻的形式及规格尺寸 1013
7.9 常用深孔套料钻的类型及特点 1014
8 铰刀 1015
8.1 铰刀的主要几何参数 1015
8.2 常用铰刀形式、标准代号及规格范围 1015
第4节 铣刀 1019
1 铣刀切削部分的几何形状和角度的选择 1019
2 常用铣刀类型、规格范围及标准代号 1023
3 可转位铣刀 1029
3.1 可转位铣刀片的定位及夹紧方式 1029
3.2 可转位铣刀的类型和型号表示方法 1030
3.3 可转位铣刀的形式和基本尺寸 1032
第5节 螺纹刀具 1037
1 丝锥 1037
1.1 丝锥的结构和几何参数 1037
1.2 常用丝锥的规格范围及标准代号 1038
1.3 挤压丝锥 1046
1.4 惠氏螺纹丝锥 1046
2 板牙 1048
2.1 板牙的类型和使用范围 1048
2.2 圆板牙的结构和几何参数 1048
2.3 管螺纹板牙的结构 1049
2.4 常用板牙的规格范围及标准代号 1049
3 滚丝轮 1051
3.1 普通螺纹滚丝轮的形式及规格尺寸 1051
3.2 锥形螺纹滚丝轮基本尺寸 1051
4 搓丝板 1057
4.1 普通螺纹用搓丝板形式及规格尺寸 1057
4.2 60°圆锥管螺纹和55°密封管螺纹搓丝板形式及规格尺寸 1059
第6节 齿轮刀具 1060
1 盘形齿轮铣刀 1060
1.1 盘形齿轮铣刀形式和基本尺寸 1060
1.2 盘形锥齿轮铣刀的形式和基本尺寸 1062
2 渐开线齿轮滚刀的形式和基本尺寸 1062
2.1 小模数齿轮滚刀 1062
2.2 整体硬质合金小模数齿轮滚刀 1063
2.3 齿轮滚刀 1064
2.4 镶片齿轮滚刀 1065
2.5 剃前齿轮滚刀 1066
2.6 磨前齿轮滚刀 1067
2.7 双圆弧齿轮滚刀 1068
3 盘形剃齿刀的形式和主要尺寸 1069
4 插齿刀 1071
4.1 小模数直齿插齿刀的形式和主要尺寸 1071
4.2 直齿插齿刀的形式和主要尺寸 1073
5 直齿锥齿轮精刨刀 1078
第7节 花键和链轮刀具 1080
1 花键滚刀的形式和主要尺寸 1080
1.1 30°压力角渐开线花键滚刀 1080
1.2 45°压力角渐开线花键滚刀 1080
1.3 矩形花键滚刀的形式和主要尺寸 1081
1.4 渐开线内花键插齿刀 1082
2 滚子链和套筒链链轮滚刀基本尺寸 1083
第8节 拉刀 1084
1 圆推刀的形式和主要尺寸 1084
2 键槽拉刀 1092
2.1 平刀体键槽拉刀的形式和主要尺寸 1092
2.2 加宽平刀体键槽拉刀的形式和主要尺寸 1092
2.3 带倒角齿键槽拉刀的形式和主要尺寸 1096
2.4 带侧面齿键槽拉力 1098
第9节 磨料磨具 1101
1 普通磨料磨具 1101
1.1 磨料的品种、代号及其应用范围 1101
1.2 磨料粒度号及其选择 1102
1.3 磨具硬度代号 1103
1.4 磨具组织号及其适用范围 1103
1.5 结合剂的代号、性能及其适用范围 1103
1.6 磨具形状代号和尺寸标记 1104
1.7 砂轮的标记方法示例 1114
1.8 普通磨具的最高工作速度 1115
1.9 普通磨具形状和尺寸 1115
2 超硬材料 1122
2.1 超硬磨料的品种、代号及应用范围 1122
2.2 粒度 1122
2.3 超硬磨料结合剂及其代号、性能和应用范围 1124
2.4 浓度代号 1124
2.5 砂轮、油石及磨头的尺寸代号和术语 1124
2.6 砂轮、油石及磨头形状代号 1125
2.7 标记示例 1129
2.8 超硬材料制品形状代号及主要用途 1129
2.9 超硬材料制品 1130
2.9.1 金刚石或立方氮化硼磨具形状和尺寸 1130
2.9.2 金刚石修整笔 1140
3 涂附磨具 1141
3.1 页状砂布、砂纸规格尺寸和公差 1141
3.2 卷状砂布、砂纸规格尺寸和公差 1142
3.3 砂带规格尺寸和公差 1142
3.4 砂盘规格尺寸和公差 1145
第11章 切削加工 1146
第1节 车削加工 1146
1 车床加工范围及装夹方法 1146
1.1 卧式车床加工 1146
1.1.1 卧式车床加工范围 1146
1.1.2 卧式车床常用装夹方法 1146
1.2 立式车床加工 1146
1.2.1 立式车床加工范围 1149
1.2.2 立式车床常用装夹方法 1150
2 典型零件车削加工实例 1151
2.1 车刀的磨损和刃磨 1151
2.1.1 刀具磨损的形式 1151
2.1.2 车刀磨钝标准及寿命 1151
2.1.3 车刀的手工刃磨 1151
2.2 标准麻花钻头的磨损和刃磨 1153
2.2.1 钻头磨钝标准及寿命 1153
2.2.2 标准麻花钻头的刃磨方法及修磨 1153
2.3 中心孔的加工与修研 1155
2.3.1 中心孔的加工及质量分析 1156
2.3.2 中心孔的修研 1157
2.4 车削圆锥面 1157
2.4.1 锥体各部名称代号及尺寸计算 1157
2.4.2 车削圆锥面的方法 1158
2.4.3 车削标准锥度和常用锥度时小刀架和靠模板的转动角度 1159
2.4.4 车削圆锥面时的尺寸控制方法 1159
2.4.5 车削圆锥面时的质量分析 1159
2.5 车削偏心工件及曲轴 1160
2.5.1 车削偏心工件的装夹方法 1160
2.5.2 用专用夹具车削偏心工件 1162
2.5.3 测量偏心距的方法 1162
2.5.4 车削曲轴的装夹方法 1163
2.6 车削成形面 1163
2.6.1 成形面车削方法 1164
2.6.2 常用成形刀(样板刀)类型及应用 1165
2.7 车削球面 1166
2.7.1 用蜗杆副传动装置手动车削外球面 1166
2.7.2 用蜗杆副传动装置手动车削内球面 1166
2.8 车削薄壁工件 1167
2.8.1 工件的装夹方法 1167
2.8.2 刀具几何角度的选择 1168
2.8.3 精车薄壁工件的切削用量 1168
2.9 车削表面的滚压加工 1168
2.9.1 滚压加工常用工具及其应用 1168
2.9.2 滚轮式滚压工具常用的滚轮外圆形状及应用 1170
2.9.3 滚轮滚压的加工方法 1171
2.9.4 滚压质量分析 1171
2.9.5 滚花 1172
2.10 冷绕弹簧 1173
2.10.1 卧式车床可绕制弹簧的种类 1173
2.10.2 绕制圆柱形螺旋压缩弹簧 1173
2.10.3 绕制圆柱形螺旋拉伸弹簧 1174
2.10.4 绕制圆锥形螺旋压缩弹簧 1174
2.10.5 绕制橄榄形弹簧 1175
2.11 车削细长轴 1175
2.11.1 细长轴的加工特点 1175
2.11.2 细长轴的装夹 1175
2.11.3 车削细长轴常用的切削用量 1178
2.11.4 加工细长轴用车刀举例 1178
2.11.5 车削细长轴的质量分析 1179
2.12 卧式车床加工常见问题的产生原因及解决方法 1180
3 车削用量的选择 1180
3.1 硬质合金及高速钢车刀粗车外圆和端面的进给量 1180
3.2 硬质合金外圆车刀半精车的进给量 1181
3.3 硬质合金及高速钢镗刀粗镗孔进给量 1181
3.4 切断及切槽的进给量 1183
3.5 成形车削时的进给量 1183
3.6 用YT15硬质合金车刀车削碳钢、铬钢、镍铬钢及铸钢时的切削速度 1183
3.7 用YG6硬质合金车刀车削灰铸铁时的切削速度 1183
3.8 涂层硬质合金车刀的切削用量 1185
3.9 陶瓷车刀的切削用量 1185
3.10 立方氮化硼车刀的切削用量 1187
3.11 金刚石车刀的切削用量 1188
第2节 螺纹加工 1189
1 车螺纹 1189
1.1 螺纹车刀及安装 1189
1.1.1 螺纹车刀的类型及应用 1189
1.1.2 对三角形螺纹车刀几何形状的要求 1190
1.1.3 车螺纹车刀的刀尖宽度尺寸 1190
1.1.4 对螺纹车刀安装的要求 1190
1.2 卧式车床车螺纹交换齿轮计算 1191
1.2.1 车特殊螺距时的计算方法 1191
1.2.2 车模数或径节蜗杆时的计算方法 1192
1.2.3 车多线螺纹交换齿轮计算及分线方法 1192
1.3 螺纹车削方法 1194
1.4 常用螺纹车刀的特点与应用 1195
1.5 高速钢及硬质合金车刀车削不同材料螺纹的切削用量 1199
1.6 高速钢车刀车削螺纹时常用切削液 1199
1.7 车削螺纹常见问题、产生原因及解决方法 1200
2 旋风铣削螺纹 1201
2.1 旋风铣削螺纹的方式及适用范围 1201
2.2 旋风铣削螺纹的刀具材料和几何角度 1202
2.3 旋风铣削螺纹常用切削用量 1202
3 用板牙和丝锥切削螺纹 1203
3.1 用板牙套螺纹 1203
3.1.1 套螺纹工具 1203
3.1.2 工件圆杆直径的确定 1203
3.1.3 套螺纹时应注意的事项 1204
3.1.4 套螺纹常见问题及防止方法 1204
3.2 用丝锥攻螺纹 1205
3.2.1 攻螺纹工具 1205
3.2.2 攻螺纹切削液选择 1206
3.2.3 攻螺纹时应注意的事项 1206
3.2.4 攻螺纹前钻孔用麻花钻直径 1206
3.2.5 攻螺纹中常见问题 1208
4 挤压丝锥挤压螺纹 1210
4.1 挤压丝锥的结构、种类及适用范围 1210
4.2 挤压螺纹前底孔的确定 1210
4.3 挤压螺纹速度的选择 1210
5 磨螺纹 1210
5.1 螺纹磨削方法 1210
5.2 螺纹磨削砂轮选择和修整 1211
5.3 螺纹磨削工艺要求 1212
第3节 铣削加工 1213
1 铣削方式、铣削范围和基本方法 1213
1.1 铣削方式 1213
1.2 铣削范围和基本方法 1214
2 分度头及分度方法 1217
2.1 分度头传动系统及分度头定数 1217
2.2 分度方法及计算 1218
2.2.1 单式分度法计算及分度表 1218
2.2.2 角度分度法计算及分度表 1219
2.2.3 直线移距分度法 1219
3 典型零件的铣削加工 1220
3.1 铣削离合器 1220
3.1.1 齿式离合器的种类及特点 1220
3.1.2 矩形齿离合器的铣削 1221
3.1.3 尖齿(正三角形)离合器的铣削 1222
3.1.4 梯形收缩齿离合器的铣削 1222
3.1.5 锯齿形离合器的铣削 1222
3.1.6 梯形等高齿离合器的铣削 1224
3.1.7 螺旋齿离合器的铣削 1224
3.2 铣削凸轮 1225
3.2.1 凸轮传动的三要素 1225
3.2.2 等速圆盘凸轮的铣削 1226
3.2.3 等速圆柱凸轮的铣削 1226
3.3 铣削球面 1227
3.4 铣削刀具齿槽 1228
3.4.1 对前角γo=0°的铣刀开齿 1228
3.4.2 对前角γo>0°的铣刀开齿 1229
3.4.3 圆柱螺旋齿铣刀的铣削 1230
3.4.4 麻花钻头的铣削 1231
3.4.5 端面齿的铣削 1231
3.4.6 锥面齿的铣削 1232
3.4.7 铰刀的开齿 1232
3.5 铣削加工常见问题产生原因及解决方法 1233
4 铣削用量的选择 1234
4.1 铣刀磨钝标准及寿命 1234
4.2 铣削用量 1236
4.2.1 高速钢端铣刀、圆柱形铣刀和圆盘铣刀铣削时的进给量 1236
4.2.2 高速钢立铣刀、角铣刀、半圆铣刀、切槽铣刀和切断铣刀铣削钢的进给量 1236
4.2.3 硬质合金端铣刀、圆柱形铣刀和圆盘铣刀铣削平面和凸台的进给量 1237
4.2.4 硬质合金立铣刀铣削平面和凸台的进给量 1238
4.2.5 铣削速度 1238
4.2.6 涂层硬质合金铣刀的铣削用量 1239
第4节 花健、链轮加工 1239
1 花键的加工 1239
1.1 花键的定心方式及加工精度 1239
1.2 在铣床上铣削矩形齿花键轴 1240
1.2.1 用单刀铣削矩形齿花键轴 1240
1.2.2 用组合铣刀铣削矩形齿花键轴 1242
1.2.3 用硬质合金组合刀盘精铣花键轴 1242
1.2.4 用成形铣刀铣削花键轴 1242
1.3 铣削花键轴时产生误差的原因及解决方法 1243
2 铣削链轮 1244
2.1 铣削滚子链链轮 1244
2.1.1 直线端面齿形滚子链链轮主要尺寸及计算公式 1244
2.1.2 直线端面齿形滚子链链轮铣削方法 1244
2.1.3 滚子链链轮的测量 1246
2.1.4 链轮工作图标注要求 1247
2.2 铣削齿形链链轮 1247
2.2.1 用单角度铣刀铣削 1247
2.2.2 用三面刃铣刀铣削 1247
2.2.3 齿形链链轮的测量 1247
第5节 齿轮加工 1249
1 各种齿轮加工方法 1249
2 成形法铣削齿轮 1253
2.1 成形铣刀铣直齿圆柱齿轮 1253
2.2 成形铣刀铣削直齿条、斜齿条 1254
2.3 成形铣刀铣斜齿圆柱齿轮 1256
2.4 成形铣刀铣直齿锥齿轮 1257
3 飞刀展成铣蜗轮 1258
4 滚齿 1260
4.1 滚齿机传动系统 1262
4.2 常用滚齿机连接尺寸 1262
4.2.1 滚齿机主要相关尺寸 1262
4.2.2 工作台尺寸 1262
4.2.3 刀架及尾架尺寸 1263
4.3 常用滚齿夹具及齿轮的安装 1263
4.4 滚刀心轴和滚刀的安装要求 1264
4.5 滚刀精度的选用 1264
4.6 滚齿工艺参数的选择 1264
4.7 滚齿调整 1265
4.7.1 交换齿轮计算及滚齿机定数 1265
4.7.2 滚刀安装角度、工作台回转方向及中间轮装置 1265
4.8 滚切大质数齿轮 1267
4.8.1 滚切大质数直齿圆柱齿轮时各组交换齿轮计算 1267
4.8.2 滚切大质数斜齿圆柱齿轮时各组交换齿轮计算 1267
4.8.3 Y38滚齿机加工大质数直齿圆柱齿轮时,分度、差动交换齿轮表 1268
4.8.4 p的推荐值 1268
4.9 滚齿加工常见缺陷及解决方法 1268
5 交换齿轮表 1271
6 插齿 1275
6.1 插齿机的组成及传动系统 1275
6.2 插齿机的基本参数和工作精度 1277
6.2.1 插齿机的基本参数 1277
6.2.2 常用插齿机的工作精度 1277
6.3 常用插齿机连接尺寸 1277
6.4 插齿刀的调整 1278
6.5 插齿用夹具及调整 1280
6.6 常用插齿机交换齿轮计算 1281
6.7 插削余量及插削用量的选用 1281
6.8 插齿加工中常出现的缺陷及解决方法 1282
7 剃齿 1284
7.1 剃齿机及其精度要求 1284
7.2 剃齿刀的基本尺寸 1285
7.3 剃齿用心轴 1285
7.4 剃齿的切削用量 1286
7.5 剃齿加工余量 1287
7.6 剃齿方法 1287
7.6.1 剃齿机与刀具、夹具的调整精度 1287
7.6.2 轴交角的调整 1288
7.6.3 常用的剃齿方法 1288
7.7 剃齿误差与轮齿接触区偏差 1289
7.7.1 剃齿误差产生原因及解决方法 1289
7.7.2 轮齿接触区的偏差与修正方法 1290
第6节 磨削加工 1291
1 常见的磨削方式 1291
2 磨削加工基础 1292
2.1 砂轮安装与修整 1292
2.2 砂轮修整工具及其选用 1293
2.3 常用磨削液的名称及性能 1294
3 外圆磨削 1295
3.1 外圆磨削常用方法 1295
3.2 工件的装夹 1297
3.3 砂轮的选择 1299
3.4 外圆磨削切削用量的选择 1299
3.5 外圆磨削余量 1301
3.6 外圆磨削常见的工件缺陷、产生原因及解决方法 1302
4 内圆磨削 1303
4.1 内圆磨削常用方法 1303
4.2 工件的装夹 1305
4.3 内圆磨削砂轮的选择及安装 1306
4.4 内圆磨削切削用量的选择 1308
4.5 内圆磨削余量的合理选择 1312
4.6 内圆磨削常见的工件缺陷、产生原因及解决方法 1313
5 圆锥面磨削 1313
5.1 圆锥面的磨削方法 1313
5.2 圆锥面的精度检验 1315
5.3 圆锥面磨削的质量分析 1316
6 平面磨削 1317
6.1 平面磨削形式及特点 1317
6.2 平面磨削常用方法 1318
6.3 工件的装夹方法 1321
6.4 平面磨削砂轮的选择 1324
6.5 平面磨削切削用量的选择 1324
6.6 平面磨削余量的合理选择 1328
6.7 平面磨削的质量分析 1328
7 成形磨削 1329
7.1 成形磨削的几种方法 1329
7.2 成形砂轮的修整 1330
8 薄片工件磨削 1333
9 细长轴磨削 1334
10 刀具刃磨 1334
10.1 工具磨床主要附件及其应用 1334
10.2 刀具刃磨砂轮的选择 1336
10.3 砂轮和支片安装位置的确定 1338
10.4 刀具刃磨实例 1338
11 高效与低粗糙度磨削 1342
11.1 高速磨削 1342
11.2 宽砂轮磨削 1344
11.3 低粗糙度磨削 1345
第7节 光整加工 1347
1 研磨 1347
1.1 研磨的分类及适用范围 1347
1.2 研磨剂 1347
1.2.1 常用磨料及适用范围 1347
1.2.2 磨料粒度的选择 1348
1.2.3 研磨液 1348
1.2.4 研磨剂的配制 1348
1.3 研具 1349
1.3.1 研具材料 1349
1.3.2 通用研具 1350
1.4 研磨方法 1352
1.4.1 常用研磨运动轨迹 1352
1.4.2 研具的压砂 1353
1.4.3 研磨工艺参数的选择 1353
1.4.4 典型面研磨方法举例 1354
1.5 研磨的质量分析 1355
2 珩磨 1356
2.1 珩磨机 1356
2.2 珩磨头结构及连接方式 1361
2.2.1 常用珩磨头结构形式 1361
2.2.2 珩磨头的连接方式 1363
2.3 珩磨用夹具 1364
2.3.1 珩磨加工常用夹具结构形式 1364
2.3.2 珩磨加工中的对中 1364
2.4 珩磨油石的选择 1366
2.4.1 珩磨油石磨料的选择 1366
2.4.2 珩磨油石磨料粒度的选择 1366
2.4.3 珩磨油石硬度的选择 1367
2.4.4 结合剂的选择 1367
2.4.5 组织和浓度的选择 1367
2.4.6 珩磨油石长度的选择 1367
2.4.7 珩磨油石数量和宽度的选择 1367
2.5 珩磨工艺参数的选择 1367
2.5.1 珩磨速度和珩磨交叉角 1367
2.5.2 珩磨油石的工作压力 1368
2.5.3 珩磨油石的行程 1368
2.5.4 珩磨余量的选择 1369
2.5.5 珩磨液的选择 1369
2.5.6 对工件珩磨前的要求 1369
2.6 珩磨的质量分析 1369
3 抛光 1372
3.1 抛光轮材料的选用 1372
3.2 磨料和抛光剂 1373
3.3 抛光工艺参数 1373
第8节 钻削、扩削、铰削加工 1374
1 钻削 1374
1.1 典型钻头举例 1374
1.1.1 群钻 1374
1.1.2 几种典型钻头举例 1379
1.2 钻削方法 1380
1.2.1 常用装夹方法 1380
1.2.2 常用钻夹具(钻模)形式及特点 1381
1.2.3 钻削不同孔距精度所用的加工方法 1381
1.2.4 切削液的选用 1382
1.2.5 常用钻孔方法 1382
1.2.6 特殊孔的钻削方法 1382
1.3 钻削加工切削用量的选择 1384
1.3.1 高速钢钻头钻削不同材料的切削用量 1384
1.3.2 硬质合金钻头钻削不同材料的切削用量 1385
1.3.3 群钻加工钢件时的切削用量 1387
1.3.4 群钻加工铸铁件时的切削用量 1387
1.4 麻花钻钻孔中常见问题产生原因和解决方法 1388
2 扩孔 1390
2.1 扩孔方法 1390
2.2 扩孔钻的切削用量 1390
2.3 扩孔钻扩孔中常见问题产生原因和解决方法 1391
3 锪孔 1392
3.1 锪钻 1392
3.2 高速钢及硬质合金锪钻加工的切削用量 1393
3.3 锪孔中常见问题产生原因和解决方法 1393
4 深孔钻削 1393
4.1 深孔钻削的适用范围、加工精度与表面粗糙度 1393
4.2 深孔加工中每次进给深度 1394
4.3 内排屑深孔钻钻孔中常见问题产生原因和解决方法 1394
5 铰削 1395
5.1 铰削方法 1395
5.1.1 铰刀直径的确定及铰刀的研磨 1395
5.1.2 铰刀在使用中的修磨 1396
5.1.3 铰削余量的选择 1396
5.1.4 铰削时切削液的选用 1397
5.1.5 手工铰孔应注意的事项 1397
5.1.6 机动铰孔应注意的事项 1397
5.1.7 圆锥孔的铰削 1397
5.2 铰削加工切削用量的选择 1398
5.2.1 铰刀磨钝标准及寿命 1398
5.2.2 铰削用量 1398
5.3 多刃铰刀铰孔中常见问题产生原因和解决方法 1400
第9节 镗削加工 1402
1 镗刀 1402
1.1 单刃镗刀 1402
1.2 双刃镗刀 1402
1.3 复合镗刀 1404
1.4 微调镗刀 1406
1.5 镗床用攻螺纹夹头 1407
2 卧式镗床镗削 1407
2.1 卧式镗床基本工作范围 1408
2.2 卧式镗床基本定位方法 1409
2.2.1 主轴轴线与镗孔轴线重合方法 1409
2.2.2 主轴轴线与后立柱刀杆支架轴线重合方法 1409
2.3 导向装置布置的形式与特点 1409
2.4 工件定位基准及定位方法 1409
2.5 镗削基本类型及加工精度分析 1414
2.5.1 悬伸镗削基本方式及加工精度分析 1414
2.5.2 支承镗削基本方式及加工精度分析 1414
2.6 镗削加工 1417
2.6.1 镗刀安装与对刀 1417
2.6.2 粗镗、精镗 1417
2.6.3 基本镗削方法 1418
2.6.4 用镗模加工方法 1426
2.6.5 镗孔坐标尺寸的计算 1426
2.6.6 卧式镗床的镗削用量 1428
2.6.7 卧式镗床常用测量方法及精度 1429
2.6.8 卧式镗床加工中常见的质量问题与解决方法 1430
3 坐标镗床镗削 1431
3.1 坐标换算和加工调整 1431
3.2 找正工具与找正方法 1431
3.3 坐标测量 1431
3.4 坐标镗床的镗削用量 1436
3.5 镗削加工质量分析 1436
4 精镗床加工 1437
4.1 精镗床的加工精度 1437
4.2 精镗床镗刀几何参数的选择 1437
4.3 精镗床加工操作要求 1439
4.4 精镗床的精密镗削用量 1439
第10节 刨削、插削加工 1440
1 刨削 1440
1.1 刨削加工方法 1440
1.1.1 牛头刨床常见加工方法 1440
1.1.2 龙门刨床常见加工方法 1440
1.2 刨刀类型及切削角度的选择 1440
1.2.1 刨刀的结构形式 1440
1.2.2 常用刨刀的种类及用途 1440
1.2.3 刨刀切削角度的选择 1440
1.3 刨削常用装夹方法 1440
1.4 刨削工具 1440
1.5 槽类工件的刨削与切断 1440
1.6 镶条的刨削 1440
1.7 刨削的经济加工精度 1449
1.8 常用刨削用量 1449
1.9 刨削常见问题产生原因及解决方法 1449
1.9.1 刨平面常见问题产生原因及解决方法 1449
1.9.2 刨垂直面和阶台常见问题产生原因及解决方法 1449
1.9.3 切断、刨直槽及T形槽常见问题产生原因及解决方法 1449
1.9.4 刨斜面、V形槽及镶条常见问题产生原因及解决方法 1449
1.10 精刨 1449
1.10.1 精刨的类型及特点 1454
1.10.2 精刨加工对工艺系统的要求 1455
1.10.3 精刨表面常见问题产生原因及解决方法 1456
2 插削 1458
2.1 常用插削方式和加工方法 1458
2.2 插刀 1458
2.3 插平面及插槽的进给量 1458
2.4 插削键槽常见缺陷产生原因及解决方法 1458
第11节 拉削加工 1463
1 常见拉削加工分类的特点及应用 1463
2 拉削方式 1467
3 拉削装置 1468
4 拉刀 1469
4.1 拉刀的类型 1469
4.2 拉刀的基本结构及刀齿的几何参数 1469
5 拉削经济加工精度及表面粗糙度 1471
6 拉削工艺参数 1471
6.1 拉削前对工件的要求 1471
6.2 拉削余量的选择 1471
6.3 拉削用量 1471
6.4 拉削用切削液 1471
7 拉削中常见缺陷产生原因与解决方法 1474
第12节 难加工材料的切削加工 1476
1 常用的难切削材料及应用 1476
2 难切削金属材料的可加工性比较 1477
3 高锰钢的切削加工 1477
3.1 常用切削高锰钢的刀具材料 1477
3.2 切削高锰钢车刀与铣刀的主要角度 1477
3.3 常用硬质合金刀具车削、铣削高锰钢的切削用量 1478
4 高强度钢的切削加工 1478
4.1 常用的切削高强度钢用高速钢刀具材料 1478
4.2 常用的切削高强度钢用硬质合金 1478
4.3 切削高强度钢的车刀与铣刀的主要角度 1478
4.4 车削高强度钢的切削用量 1478
4.5 按工件硬度选择铣削用量 1479
5 高温合金的切削加工 1479
5.1 常用切削高温合金的刀具材料 1479
5.2 车削高温合金常用刀具的前角与后角 1479
5.3 车削高温合金切削用量举例 1480
5.4 铣削高温合金切削用量举例 1481
6 钛合金的切削加工 1482
6.1 常用切削钛合金的刀具材料 1482
6.2 切削钛合金的车刀与铣刀的主要角度 1482
6.3 车削钛合金切削用量 1483
6.4 铣削钛合金切削用量 1483
7 不锈钢的切削加工 1484
7.1 常用切削不锈钢的刀具材料 1484
7.2 切削不锈钢的车刀与铣刀的主要角度 1484
7.3 车削不锈钢的切削用量 1485
7.4 高速钢铣刀铣削不锈钢的切削用量 1485
第12章 钳工加工及装配 1486
第1节 钳工加工 1486
1 划线 1486
1.1 常用划线工具名称及用途 1486
1.2 划线常用的基本方法 1490
1.3 划线基准的选择 1493
1.3.1 划线基准选择原则 1493
1.3.2 常用划线基准类型 1493
1.4 划线时的校正和借料 1493
1.5 划线程序 1496
1.6 立体划线 1496
1.7 应用分度头划线 1498
1.8 几种典型钣金展开图举例 1499
1.8.1 一端斜截45°圆管 1499
1.8.2 圆管弯头 1499
1.8.3 直交等径三通管 1500
1.8.4 斜接等径三通管 1500
1.8.5 直交不等径三通管 1501
1.8.6 等角V形等径三通管 1501
2 锯削 1502
2.1 锯削工具 1502
2.1.1 锯架 1502
2.1.2 锯条 1503
2.2 锯削方法 1504
3 錾削 1506
3.1 錾子的种类及用途 1506
3.2 錾子切削部分及几何角度 1507
3.3 錾子的刃磨及淬火方法 1507
3.4 錾削方法 1508
4 锉削 1510
4.1 锉刀的各部名称 1510
4.2 锉刀的分类及基本参数 1510
4.3 常用锉刀形式及尺寸 1512
4.3.1 钳工锉 1512
4.3.2 整形锉 1515
4.3.3 异形锉 1520
4.4 锉刀的选用 1522
4.5 锉削方法 1523