图书介绍
高可靠性电子装备PCBA设计缺陷案例分析及可制造性设计pdf电子书版本下载
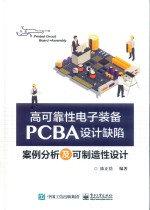
- 陈正浩编著 著
- 出版社: 北京:电子工业出版社
- ISBN:7121355875
- 出版时间:2019
- 标注页数:672页
- 文件大小:94MB
- 文件页数:693页
- 主题词:
PDF下载
下载说明
高可靠性电子装备PCBA设计缺陷案例分析及可制造性设计PDF格式电子书版下载
下载的文件为RAR压缩包。需要使用解压软件进行解压得到PDF格式图书。建议使用BT下载工具Free Download Manager进行下载,简称FDM(免费,没有广告,支持多平台)。本站资源全部打包为BT种子。所以需要使用专业的BT下载软件进行下载。如 BitComet qBittorrent uTorrent等BT下载工具。迅雷目前由于本站不是热门资源。不推荐使用!后期资源热门了。安装了迅雷也可以迅雷进行下载!
(文件页数 要大于 标注页数,上中下等多册电子书除外)
注意:本站所有压缩包均有解压码: 点击下载压缩包解压工具
图书目录
第1章 总则 1
1.1概述 1
1.2我国电子制造业面临的困境 2
1.2.1困境之一:高端芯片的缺失 2
1.2.2困境之二:DFM的严重缺失 4
1.2.3困境之三:不适应先进生产力发展的旧工艺管理体制 6
1.2.4困境之四:被严重低估了的工艺和制造价值 7
1.2.5被扭曲了的电子装联标准 8
1.3实现高可靠质量目标的因素 9
1.4中国制造需要“大国工艺” 10
1.4.1精湛的工匠技艺源自先进的工艺技术 10
1.4.2电子装联技术的重要性 11
1.5先进制造技术 12
1.5.1什么是先进制造技术 12
1.5.2电气互连先进制造技术 12
1.5.3新型元器件与高密度组装技术 12
1.5.4微组装先进制造技术 13
1.5.5可制造性设计是实现先进制造技术的前提和技术支撑 13
1.6可制造性设计理念的拓展 14
1.7结束语 15
第2章 PCB/PCBA设计缺陷案例分析 16
2.1焊盘尺寸设计缺陷 16
2.1.1片式元器件焊盘设计缺陷 17
2.1.2片式元器件错误的“常见病、多发病” 20
2.1.3焊盘两端不对称,走线不规范 21
2.1.4焊盘宽度及相互间距离不均匀 23
2.1.5 IC焊盘宽度间距过大 23
2.1.6 QFN焊盘设计缺陷 24
2.1.7安装孔金属化,焊盘设计不合理 25
2.1.8公用焊盘问题导致的缺陷 26
2.1.9热焊盘设计不合理 26
2.1.10片式电容器焊盘长度设计不合理 28
2.1.11其他焊盘设计缺陷 28
2.2丝网和阻焊膜设计不良 30
2.2.1丝网设计不良 30
2.2.2阻焊膜设计不良 33
2.3元器件布局不合理 35
2.3.1布局设计不良 35
2.3.2应用波峰焊工艺时,元器件布局没有采取克服“阴影效应”措施 37
2.3.3元器件的排布不符合工艺要求 37
2.3.4安放在PCB焊接面的QFP和SOIp没有设计成“菱形”和设计导流盘 37
2.3.5双面组装PCBA焊接面元器件焊盘或本体边缘与插件零件边缘距离过小 38
2.3.6元器件布放不符合自动化生产要求 38
2.3.7元器件布放位置距紧固件太近的设计缺陷 39
2.3.8波峰焊应用中的布局设计缺陷 40
2.3.9回流焊应用中的布局设计缺陷 42
2.3.10 PCB布局混乱,严重影响焊接可靠性 42
2.4拼板设计不正确 44
2.5 PCB材料与尺寸不合适 46
2.5.1翘曲与扭曲 46
2.5.2 PCB材质选用不当,制作质量低劣 48
2.6 BGA的常见设计问题 49
2.7通孔插装中元器件引线直径与金属化孔孔径和焊盘的不匹配 51
2.8“飞线”问题 54
2.9 PCB缺少工艺边或工艺边设计不合理 54
2.10插装元器件安装设计不良 59
2.11导通孔设计不良 61
2.11.1导通孔设计在焊盘上 61
2.11.2导通孔与焊盘或元器件距离过小 63
2.11.3导通孔在屏蔽罩位置 67
2.11.4导通孔尺寸过大 67
2.11.5导通孔在元器件底部 68
2.12电连接器接触偶与金属化孔间隙比 69
2.13 PCB缺少定位孔,定位孔位置不正确 70
2.14焊盘与导线的连接 71
2.15 PCB基准识别点缺失、设计不规范 72
2.16元器件装配设计不良 74
2.17设计缺陷所造成的焊接缺陷 95
2.17.1插装设计缺陷所造成的焊接缺陷 95
2.17.2贴装 97
2.18大面积接地和大面积PCB应用设计缺陷 99
2.19工艺设计错误 100
2.20镀金引线/焊端直接进行锡焊的缺陷案例分析 101
2.21多种设计缺陷 101
2.22因设计缺陷、物流控制失控和焊接温度不符合规定要求引起的焊接故障 102
2.22.1虚焊与冷焊 102
2.22.2金属化孔透锡率不符合要求 104
2.23设计缺陷对元器件返工返修的影响 105
2.24设计缺陷对检验检测的影响 106
2.25设计缺陷对清洗的影响 106
2.26印制电路板组件的反变形安装 106
2.27潮湿敏感元器件(MSD)损坏 110
2.28静电敏感元器件使用上的错误 111
2.29返工返修(电装整修,二次焊接) 112
2.30电子产品电路设计及制造缺陷实例 113
第3章 现代电子装联核心理念及发展趋势 117
3.1现代电子装联核心理念 117
3.1.1电子装联技术与产品质量的关系 117
3.1.2应用DFX实施军品可靠性设计 117
3.1.3基本概念 119
3.1.4现代电子装联核心理念 122
3.2电路设计现状 126
3.2.1引言 126
3.2.2概述 126
3.2.3电路设计功能的逐渐弱化 127
3.3电子装联技术的迅速发展 129
3.3.1电子装联工程的基本概念 129
3.3.2电子装联元器件的高速发展 132
3.3.3可制造性分析软件的应用 134
3.3.4国内电子研制生产企业可制造性分析软件应用严重滞后原因分析 149
3.3.5构建DFM平台 152
3.3.6可制造性分析与可制造性设计 153
3.4板级电路组装技术的发展趋势 154
3.4.1元器件级 154
3.4.2板级电路模块 154
3.4.3 post-SMT 155
3.4.4堆叠装配技术 157
3.4.5高密度组装中的“微焊接”工艺设计 159
3.4.6电子产品高密度小型化设计 159
3.5微波组件基本概念及应用技术标准现状 161
3.5.1微波组件基本概念 161
3.5.2微波电路应用标准现状 162
3.6微组装技术基本概念及标准应用现状 164
3.6.1微组装技术的特征 165
3.6.2微组装技术的定义及关键点 165
3.6.3微组装技术应用标准现状 166
3.6.4微组装结构 168
3.6.5微波组件微组装技术的应用 172
3.7整机级先进制造技术 175
3.7.1 3D线扎设计 175
3.7.2 立体建模的条件 176
3.7.3存在的问题 176
3.7.4 3D布线的核心 177
3.7.5整机/系统级“无线缆”连接技术 177
3.7.6刚-挠基板连接技术 178
3.7.7背板连接技术 179
3.7.8机架安装 179
3.7.9整机3D CAPP集成设计技术 180
3.7.10电子产品虚拟装配技术 182
第4章 电路可制造性设计基础 184
4.1概述 184
4.1.1电子产品电装生产质量问题的主要成因 184
4.1.2电路设计错误或缺乏可制造性给制造带来了什么 185
4.1.3不使用DFM可能面临高成本与高风险的巨大挑战 186
4.1.4可制造性设计的严重缺失是导致国内外电子产品质量差别的核心要素之一 186
4.1.5实施DFM提高核心竞争力 187
4.1.6在设计初期进行DFM 187
4.1.7 DFM是面向产品生命周期各环节设计的关键 187
4.1.8 DFM不是单纯的一项技术,它是一种思想,一个先进的理念 188
4.1.9引入DFM来提高利润和产量 189
4.1.10执行IPC、MIL或GJB、GB及行业标准的前提 189
4.1.11缺乏DFM到处存在 189
4.1.12对设计缺陷的错误认识 191
4.1.13产品的质量和可靠性是设计出来的 192
4.2电路可制造性设计是崭新的概念 192
4.2.1电路可制造性设计的概念 192
4.2.2可制造性设计应用的广泛性 192
4.3电路可制造性设计基本内容 193
4.3.1可制造性设计主要解决的问题 193
4.3.2电路、结构和工艺三者之间的关系 194
4.4电路可制造性设计基本文件 194
4.4.1电子装联用基本电路设计文件 194
4.4.2电子装联常用标准 195
4.4.3企业技术标准(典型工艺规范) 204
4.4.4电子装联常用产品工艺文件 205
4.5可制造性设计的基本理念 206
4.5.1可制造性设计与设计工艺性或可生产性是一致的 206
4.5.2 DFM的诞生 207
4.5.3 DFM的定义 208
4.5.4 DFM基本工作目标 208
4.5.5 DFM的职责 209
4.5.6 DFM的相关活动 210
4.5.7 DFM主要活动与原理 210
4.5.8 DFM团队与主要职责 210
4.5.9支持DFM工作的工具技能 210
4.5.10 DFM系统的主要元素 211
4.5.11 DFM的涵盖面及定义 211
4.5.12 SMT领域的DFM 211
4.5.13电路可制造性设计的基本理念及意义 212
4.5.14应用先进电子装联技术的电路可制造性设计 213
4.6关键在于理念的更新 215
第5章 PCB/PCBA可制造性设计 216
5.1概述 216
5.2 PCBA设计缺陷的影响 217
5.3印制电路板组件DFM的核心理念 218
5.4可制造性设计的组织保证措施 219
5.5可制造性设计实施方案 219
5.6电路设计文件可制造性审核(工艺性审核) 220
5.6.1电路设计文件工艺性审查的形式 220
5.6.2电路设计文件工艺性审查(以PCBA为例) 221
5.6.3电装工艺设计原则与依据 227
5.6.4工艺性审查存在的问题 228
5.7印制电路板组件可制造性设计基本概念 228
5.7.1印制电路板可制造性设计 228
5.7.2印制电路板可制造性设计目的 228
5.7.3印制电路板可制造性设计范围 229
5.7.4印制电路板可制造性设计重点 229
5.7.5印制电路板可制造性设计内容 229
5.7.6可制造性设计程序解析 229
5.7.7 PCBA组装方式决定焊接工艺流程 231
5.7.8印制电路板电路设计 239
5.8确保PCBA可制造性设计实施的物料要素 243
5.8.1总则 243
5.8.2高可靠印制电路板的可接受条件 244
5.8.3高可靠电子装备电子元器件选用要求 248
第6章 PCB元器件布局设计及焊盘设计 254
6.1表面组装技术元器件布局设计及片式元器件焊盘设计 254
6.1.1表面贴装元器件的焊接可靠性 254
6.1.2 SMT印制电路板电路设计一般要求 255
6.1.3 SMT工艺对元器件布局设计的要求 257
6.1.4采用回流焊工艺的元器件焊盘设计 261
6.1.5回流焊工艺导通孔设计 373
6.2波峰焊工艺元器件布局设计及焊盘图形设计 374
6.2.1采用传统波峰焊工艺的元器件布局设计 374
6.2.2采用传统波峰焊工艺的元器件焊盘设计 380
第7章 通用设计技术 385
7.1通用设计 385
7.1.1焊盘形状设计 385
7.1.2焊盘与印制电路板的距离 386
7.1.3焊盘的开口 386
7.1.4相邻焊盘设计 386
7.1.5大型元器件焊盘设计 386
7.1.6大导电面积设计 386
7.1.7采用传统波峰焊工艺时孔的设计规则 386
7.1.8焊盘设计 388
7.1.9焊盘与孔的关系 389
7.1.10导通孔与焊盘的连接设计 390
7.1.11元器件孔距设计 395
7.1.12环宽要求 395
7.1.13导体层的隔热设计 396
7.1.14 THT图形设计 397
7.1.15焊盘和印制导线的连接 398
7.1.16双列直插式(DIP)集成电路焊盘设计 401
7.1.17元器件的安装间距 403
7.1.18布线设计 415
7.1.19模板设计 428
7.2设备对设计的要求 441
7.2.1印制电路板外形、尺寸设计 442
7.2.2印制电路板定位孔的设计要求 444
7.2.3印制电路板夹持边设计 446
7.2.4光学定位基准标志(Mark)设计 446
7.2.5局部基准标志 449
7.2.6拼板设计 450
7.2.7选择元器件封装及包装形式 454
7.3阻焊、丝网的设计 454
7.3.1阻焊膜设计 454
7.3.2丝网图形设计 457
7.4印制电路板组件导热和散热设计 458
7.4.1概述 458
7.4.2印制电路板导热和散热设计工艺性要求 459
7.4.3元器件导热和散热设计要求 459
7.4.4元器件导热和散热设计的主要填充材料和使用 460
7.4.5印制电路板散热设计的内容和要求 464
7.5印制电路板制图的基本要素 470
7.5.1印制电路板的表面镀涂 470
7.5.2印制电路板的标记 471
7.5.3印制电路板图样的绘制 472
第8章 通孔插装元器件焊接工艺选择 483
8.1选择性波峰焊是PCBA焊接工艺流程的必然选择 483
8.2选择性波峰焊对比手工焊 484
8.3选择性波峰焊对比通孔回流焊 487
8.3.1通孔回流焊工艺的优点 488
8.3.2通孔回流焊工艺的缺点 488
8.3.3通孔回流焊工艺的适用条件 491
8.3.4结束语 492
8.4选择性波峰焊对比传统波峰焊 493
8.4.1双面混装焊工艺比较 493
8.4.2避免了传统波峰焊元器件布局的局限性 496
8.4.3使用带有治具的传统波峰焊工艺 500
8.4.4选用选择性波峰焊的优越性 503
8.4.5结束语 506
8.5焊接质量要求 507
8.5.1焊接润湿角 507
8.5.2良好的焊点要素 511
8.5.3通孔插装元器件手工焊与选择性波峰焊质量比较 515
8.6选择性波峰焊导流盘的设置 518
8.6.1传统双波峰焊原理 518
8.6.2传统双波峰焊DIP元器件的焊盘排列走向、桥连产生的原因及导流盘的设置 518
8.6.3桥连现象及其产生的原因 520
8.7高密度高可靠PCBA焊接工艺流程选择 521
8.8选择性波峰焊对PCB/PCBA设计的要求 522
8.8.1 PCB设计一般要求 522
8.8.2选择性波峰焊PCB设计特殊要求 525
8.8.3防止桥连工艺 528
8.9选择性波峰焊的局限性 530
8.10与波峰焊相关的禁限用工艺 531
第9章 PCBA元器件可组装性设计 532
9.1通孔插装元器件穿孔安装 532
9.1.1一般要求 532
9.1.2通孔插装元器件安装详细要求 535
9.2表面安装 563
9.2.1有引线的表面安装 563
9.2.2无引线的表面安装 564
9.2.3 GJB 3243、QJ 3086、QJ 3173A和QJ 165B规定的表面贴装元器件安装要求 565
9.3 THC/THD在微波基板上的安装焊接设计 573
9.3.1引线搭接 573
9.3.2圆形引线搭接 573
9.3.3扁平引线搭接 573
9.3.4通孔插装元器件引线的搭接焊接要求 574
9.4非返工返修PCBA的跨接线(飞线、跳线) 574
9.4.1跨接线的定义 574
9.4.2跨接线一般使用原则 575
9.4.3特殊情况下允许使用跨接线的原则 575
9.5 PCBA返修和返工中跨接线的处理 576
9.5.1增设跨接线原则 576
9.5.2跨接线所选用的导线的选择 577
9.5.3跨接线分类 577
9.5.4跨接线的布线 577
9.5.5跨接线的连接 579
9.5.6 THT跨接线焊接要求 580
9.5.7 SMT跨接线焊接要求 582
9.5.8跨接线的黏接固定 587
第10章 高可靠PCBA禁限用工艺及分析 589
10.1高可靠PCB/PCBA禁用设计与禁用安装工艺 589
10.1.1概述 589
10.1.2什么是禁用工艺 589
10.1.3什么是限用工艺 590
10.1.4高可靠PCB/PCBA禁用设计与禁用安装工艺72条 590
10.1.5高可靠电子设备禁用工艺与材料 592
10.1.6高可靠电子设备限用工艺与设计 593
10.2军品PCBA轴向引线元器件通孔插装安装方式——不允许轴向引线元器件垂直安装 596
10.2.1问题提出 596
10.2.2军品(3级或C级产品)PCBA轴向通孔插装元器件 597
10.2.3分析 598
10.3军品(3级或C级产品)PCBA通孔插装元器件要求 599
10.3.1轴向引脚水平安装 599
10.3.2径向引脚水平安装 602
10.3.3分析 603
10.3.4结束语 604
10.4 3级电子产品PCBA片式元器件堆叠安装分析 604
10.4.1概述 604
10.4.2问题提出 605
10.4.3军标对军用PCBA“片式元器件堆叠安装”的规定 606
10.4.4分析 606
10.4.5试验验证 610
10.4.6结束语 610
10.5 F型封装大功率管的安装焊接 610
10.6 QJ 3117A《导线在印制电路板上搭接焊接》质疑 611
10.7元器件镀金引线/焊端除金搪锡 614
10.7.1问题提出 615
10.7.2元器件引脚/焊端未除金搪锡导致的金脆化案例 615
10.7.3金脆化分析 619
10.7.4镀金引线/焊端的除金规定 621
10.7.5无须纠结的镀金引线/焊端除金处理 623
10.7.6元器件引线/焊端除金工艺 624
10.7.7射频电连接器焊杯除金工艺 627
10.7.8低频(多芯)电连接器焊杯除金工艺 627
10.7.9先进除金搪锡设备及工艺介绍 632
10.7.10镀金PCB焊接中产生的金脆化案例 637
10.7.11镀金引线除金的争议 639
10.7.12结束语 642
10.8军用PCBA通孔插装元器件“禁止双面焊” 643
10.8.1引言 643
10.8.2什么是禁限用工艺 644
10.8.3提出“禁止双面焊”的必要性 644
10.8.4基于Pro/Mechanical对透锡量的验证 649
10.8.5“禁止双面焊”可以做到 655
10.8.6影响通孔插装元器件金属化孔透锡率的主要因素 655
10.8.7如何提高印制电路板金属化孔透锡率 657
10.8.8实践验证 664
10.8.9结束语 664
附录A 参考、引用标准 665
A.1中华人民共和国国家标准(GB) 665
A.2中华人民共和国国家军用标准(GJB) 665
A.3中华人民共和国航天行业标准(QJ) 666
A.4中华人民共和国航空行业标准(HB) 668
A.5中华人民共和国电子行业标准(SJ) 668
A.6美国连接电子业协会标准(IPC) 669
参考文献 671