图书介绍
机械制造手册pdf电子书版本下载
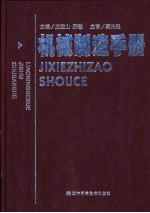
- 王宛山,邢敏主编 著
- 出版社: 沈阳:辽宁科学技术出版社
- ISBN:7538134050
- 出版时间:2002
- 标注页数:1042页
- 文件大小:42MB
- 文件页数:1060页
- 主题词:
PDF下载
下载说明
机械制造手册PDF格式电子书版下载
下载的文件为RAR压缩包。需要使用解压软件进行解压得到PDF格式图书。建议使用BT下载工具Free Download Manager进行下载,简称FDM(免费,没有广告,支持多平台)。本站资源全部打包为BT种子。所以需要使用专业的BT下载软件进行下载。如 BitComet qBittorrent uTorrent等BT下载工具。迅雷目前由于本站不是热门资源。不推荐使用!后期资源热门了。安装了迅雷也可以迅雷进行下载!
(文件页数 要大于 标注页数,上中下等多册电子书除外)
注意:本站所有压缩包均有解压码: 点击下载压缩包解压工具
图书目录
第1章 常用资料、计量单位和数学 1
1 常用资料 1
1.1 字母 1
1.2 标准分类编号及标准代号 2
1.3 化学元素符号 4
1.4 常用材料的参数 5
1.5 摩擦因数 7
1.6 机械传动效率的概略值 9
1.7 各种硬度对照表 10
2.1 国际单位制及其应用 11
2 计量单位和单位换算 11
2.2 可与SI单位并用的我国法定计量单位 12
2.3 法定计量单位与非法定计量单位的换算 13
3 常用数学 17
3.1 常用三角计算 17
3.2 常用几何图形的面积计算公式 18
3.3 常用几何体的面积、体积及形心位置 20
3.4 常用截面的几何特性计算公式 22
3.5 圆周等分系数 24
3.6 圆周均布孔的坐标尺寸 25
3.7 角度与弧度换算 27
1.1 图纸幅面和格式 28
第2章 技术制图与机械制图 28
1 制图的基本规定 28
1.2 比例、图线及剖面符号 29
2 投影法与图样画法 31
2.1 正投影法 31
2.2 图样画法 31
2.3图样简化画法 35
3 尺寸注法 46
3.1 尺寸注法 46
3.2 尺寸简化注法 50
4 尺寸公差与配合注法 58
5.1 螺纹及螺纹紧固件画法 59
5 螺纹及螺纹紧固件表示法 59
5.2 螺纹的标注方法 62
6 齿轮、花键及弹簧画法 64
7 装配图中零、部件序号及其编排方法 70
8 机构运动简图符号 71
第3章 公差与配合、形状和位置公差、表面粗糙度 74
1 极限与配合 74
1.1 极限与配合的基本术语及定义 74
1.2 标准公差 76
1.3 基本偏差 77
1.4 公差带与配合的选择 83
1.5 极限偏差值 87
4 全面质量管理 100
1.6 配制配合 103
1.7 一般公差线性尺寸的未注公差 103
2 圆锥、棱体的尺寸、公差与标注 104
2.1 圆锥的锥度与锥角 104
2.2 棱体的角度与斜度 106
2.3 圆锥公差 107
2.4 未注公差角度的极限偏差 109
2.5 圆锥的尺寸和公差注法 109
3.2 形状和位置公差标注要求及示例 114
3.1 形状和位置公差符号 114
3 形状和位置公差 114
3.3 形状和位置公差图样标注示例 118
3.4 图样上注出形状和位置公差数值及选用原则 119
3.5 图样上未注形状和位置公差的公差值 125
4 表面粗糙度 126
4.1 表面粗糙度评定参数 126
4.2 表面粗糙度的数值与应用 127
4.3 表面粗糙度符号、代号及其注法 131
1.1 材料的受力及变形 136
1.2 材料的力学性能指标 136
1 基本概念 136
第4章 工程材料 136
1.4 工程材料的分类 137
1.3 材料的热胀冷缩 137
2 钢及其热处理 138
2.1 钢的分类和钢产品牌号表示方法 138
2.2 常用钢材牌号、主要化学成分和基本特性 141
2.3 钢的热处理 145
2.4 金属零件的表面处理 156
2.5 钢的涂色标记及火花鉴别法 157
2.6 常用钢型材主要规格 158
2.7 钢型材理论质量(重量)计算公式 168
2.8 铸钢 169
2.9 常用钢号国内外对照 170
3 铸铁 171
3.1 铸铁牌号表示法 171
3.2 铸铁的主要性能及应用 171
3.3 常用铸铁牌号及力学性能国内外对照 173
4 有色金属 175
4.1 有色金属及合金产品牌号表示方法 175
4.2 铜及铜合金 177
4.3 铝及铝合金 183
4.4 铸造轴承合金 185
5 粉末冶金材料 186
6 工程塑料 188
6.1 塑料类型、特点及应用 188
6.2 常用塑料主要性能 191
6.3 有机玻璃板 192
6.4 聚氯乙烯(软、硬)管 193
6.5 酚醛层压布板 193
7 橡胶制品 194
7.1 工业用橡胶板 194
7.2 胶管 194
8 其他非金属材料 196
8.1 钢纸板 196
8.2 石棉橡胶板 196
8.3 工业用毛毡 197
9 复合材料和铝塑复合管 197
9.1 塑料—金属基多层复合材料 198
9.2 铝塑复合管 199
第5章 机械零件的毛坯 200
1 毛坯的制造方法及其工艺特点 200
2 毛坯余量 203
2.1 铸件机械加工余量与尺寸公差 203
2.2 锻件机械加工余量与尺寸公差 211
3 毛坯的选择 224
5.2 切割 224
4 对毛坯的要求 224
5.1 校直 224
5 毛坯的预备处理 224
5.3 打中心孔 229
5.4 清理 230
5.5 扒荒 230
5.6 毛坯的热处理 231
6 毛坯的检查 231
第6章 常用机械零件和结构要素 232
1 V带传动 232
1.1 V带的型号和尺寸 232
1.2 V带型号的选择和基准长度的计算 233
1.3 V带轮尺寸 234
1.4 V带轮技术要求 235
1.5 V带的使用与保养 235
2 滚子链 236
2.1 滚子链的基本参数和尺寸 236
2.2 滚子链的选用 238
2.3 滚子链链轮 239
3.1 渐开线直齿圆柱齿轮 241
3 圆柱齿轮 241
3.2 斜齿圆柱齿轮 250
3.3 变位齿轮 252
3.4 渐开线圆柱齿轮的精度 258
3.5 圆柱齿轮工作图 273
4 锥齿轮 274
4.1 锥齿轮的分类与特点 274
4.2 锥齿轮的各部名称、代号及计算 275
4.3 锥齿轮工作图 277
5 圆柱蜗杆传动 278
5.1 圆柱蜗杆传动各部名称及计算式 278
5.2 参数及计算实例 280
6.1 螺纹种类、特点及用途 281
6 螺纹 281
6.2 普通螺纹系列尺寸与公差 283
6.3 梯形螺纹系列尺寸及公差 307
6.4 锯齿形(3°,30°)螺纹 317
6.5 用螺纹密封的管螺纹系列尺寸及公差 323
6.6 非螺纹密封的管螺纹系列尺寸与公差 325
6.7 60°圆锥管螺纹系列尺寸与公差 327
6.8 米制锥螺纹系列尺寸与公差 329
7 机床梯形螺纹丝杠、螺母技术条件 331
6.9 管路旋入端用普通螺纹尺寸系列 331
8 键联接 334
8.1 普通平键 334
8.2 半圆键 336
8.3 矩形花键 337
9 零件结构要素 339
9.1 中心孔与中心孔表示法 339
9.2 球面半径 341
9.3 润滑槽 341
9.4 滚花 342
9.6 砂轮越程槽 343
9.5 零件倒角、倒圆 343
9.7 T形槽 345
9.8 螺纹收尾、肩距、退力槽和倒角 347
9.9 紧固件用通孔及沉孔 351
10 常用滚动轴承 352
10.1 常用滚动轴承类型及主要特点 352
10.2 滚动轴承代号表示法 354
10.3 滚动轴承主要名词术语 355
10.4 常用滚动轴承尺寸、性能参数 356
10.5 滚动体 392
1.1 计量与测试 395
1.2 计量器具和测量方法的分类 395
1 基本概念 395
第7章 计量与测试 395
1.4 计量器具的选择、使用与维护 396
1.3 常用计量名词术语和测量误差 396
2 量块 397
3.1 游标量具的类型、特点和读数原理 398
3 游标量具 398
3.2 常用游标量具结构、应用及参数 399
3.3 游标量具的使用与保养 401
4 测微量具 401
4.1 测微量具的类型、特点和读数原理 401
4.2 常用测微量具的结构、应用及参数 401
5 表类量具 406
5.1 百分表 406
5.2 其他表类量具 407
6 极限量规 409
6.1 光滑极限量规 409
6.2 其他量规 414
7 角度量具 415
7.1 万能角度尺 415
7.2 正弦规 417
7.3 水平仪 417
7.4 圆锥量规 420
8.1 检验平尺 422
8 其他量具 422
8.2 塞尺 423
8.3 半径、螺纹和表面粗糙度样板 424
8.4 量针 425
9 精密量仪 427
9.1 读数显微镜 427
9.2 平面度检查仪 427
9.3 电动轮廓仪 429
9.6 其他精密量仪 430
9.5 三坐标测量机 430
9.4 圆度仪 430
1 机床 432
1.1 机床的分类 432
1.2 机床型号的编制方法 432
第8章 机床、液压、电气 432
1.3 常用机床的主要参数 435
1.4 机床的传动 444
2 液压传动 447
2.1 液压传动原理及液压传动系统 447
2.2 常用主要液压元件 453
3.1 机床电气原理图及其绘制 456
2.3 液压系统的常见故障及排除方法 456
3 机床电气 456
3.2 电动机的选择 460
3.3 机床电气型号 462
3.4 安全用电与触电急救 463
第9章 数控机床及计算机辅助制造 464
1 数控机床的基本概念 464
1.1 数控技术与数控机床 464
1.2 数控机床的组成及工作原理 464
1.3 数控机床的特点、应用及分类 464
1.4 运动轨迹插补原理 466
2 数控机床加工程序编制基础 467
2.1 程序编制的一般步骤 468
2.2 程序编制的方法 468
2.3 程序编制的有关标准规定 468
3 伺服电机及位置检测元件 475
3.1 伺服电机的类型、特点及应用 475
3.2 步进电机的基本工作原理及常用规格 475
3.3 位置检测元件的类型及应用 478
5 数控机床的使用与维护要点 483
5.1 使用要点 483
4.2 数控机床附件的应用 483
4.1 数控机库附件的种类 483
4 数控机床附件 483
5.2 维护要点 484
5.3 国产主要数控机床规格 484
6 计算机辅助制造 487
6.1 计算机辅助制造(CAM)及其应用 487
6.2 群控系统(DNC) 488
6.3 计算机辅助工艺过程设计(CAPP) 489
6.4 计算机辅助设计与制造(CAD/CAM) 490
6.5 柔性制造单元(FMC) 491
6.6 柔性制造系统及其应用 492
6.8 工业机器人 494
6.7 计算机集成制造系统CIMS 494
6.9 自动化立体仓库 495
6.10 虚拟制造技术 497
第10章 机械加工工艺 498
1 机械加工工艺过程基本概念 498
1.1 生产过程与工艺过程 498
1.2 机械加工工艺过程的组成 498
2 生产类型、生产纲领与生产批量 498
2.1 生产纲领 498
2.2 生产批量 498
2.3 生产类型 498
3.2 机械加工精度 499
3.1 机械加工质量的内容 499
3 机械加工质量 499
4.1 基准的概念 501
3.3 机械加工表面质量 501
4 定位基准选择 501
5.1 工艺规程的作用、内容和格式 502
4.2 定位基准的选择 502
5 机械加工工艺规程制订 502
5.2 工艺规程的制订原则和程序 504
5.3 表面加工方案的确定 504
5.4 加工阶段的划分与加工顺序的安排 515
5.5 工序的合理安排 515
5.6 机械加工余量、工序尺寸及公差的确定 515
5.7 工序简图 529
5.8 时间定额的组成和确定 531
6 成组工艺 532
7 切削加工通用工艺守则 532
第11章 机床夹具与附件 534
1 机床夹具及作用、分类与组成 534
1.1 机床夹具及作用 534
1.2 机床夹具的分类与组成 534
2 工件在夹具中的定位 534
2.1 六点定位原理 534
2.2 常用定位方法及定位元件 537
2.3 定位误差的分析与计算 544
3.1 夹紧装置的组成和基本要求 545
3 工件的夹紧 545
3.2 典型夹紧机构及夹紧力的确定 547
4 夹具的对定 560
4.1 夹具与机床的连接方式和有关元件 560
4.2 对刀、导引元件 560
5 组合夹具与可调整夹具 567
5.1 组合夹具 567
5.2 可调整夹具 569
6 机床夹具零件及部件,机床附件 569
6.1 机床夹具零件与部件 569
6.2 机床夹具附件(通用夹具) 576
1 刀具几何参数与切削要素 586
1.1 切削运动和加工表面 586
1.2 刀具角度定义 586
第12章 金属切削原理 586
1.3 切削用量及切削层要素 588
2 刀具材料 589
2.1 刀具切削部分材料应具备的性能 589
2.2 工具钢 590
2.3 硬质合金 592
2.4 涂层刀具 594
2.5 其他刀具材料 594
3 金属切削变形 595
3.1 金属切削过程 595
3.2 变形程度的表示方法 595
3.3 切屑类型 596
3.4 积屑瘤 597
4 切削力 597
4.1 切削力的来源、合力及其分解 597
4.2 影响切削力的因素 598
4.3 常用切削方式的切削力公式 598
5 切削热与切削温度 600
5.1 切削热的产生与传出 600
5.2 影响切削温度的主要因素 601
6.1 刀具磨损形式及破损特点 602
6.2 刀具磨损的原因 602
6 刀具磨损及刀具耐用度 602
6.3 刀具磨损过程及磨钝标准 603
6.4 刀具耐用度 603
6.5 常用刀具的磨钝标准及耐用度 604
7 工件材料的切削加工性 606
7.1 切削加工性的概念和标志方法 606
7.2 影响材料切削加工性的因素及改善途径 606
8.2 切削液的种类与选用 607
8 切削液 607
8.1 切削液的作用 607
9.1 前角及倒棱的选择 608
9 刀具合理几何参数的选择 608
9.2 后角的选择 609
9.3 主偏角、副偏角及刀尖形状的选择 609
9.4 刃倾角的选择 609
10 切削用量选择原则与方法 610
10.1 切削用量选择的原则 610
10.2 切削用量选择方法 610
1.2 机夹可转位车刀 611
1 车刀 611
1.1 车刀类型与用途 611
第13章 车削 611
1.3 车刀切削部分几何形状及几何参数 627
2 车外圆 629
2.1 不同精度外圆车削工艺 629
2.2 典型外圆车刀特点及装夹要点 629
2.3 车外圆切削用量 631
3.1 不同精度内孔车削工艺 634
2.4 提高外圆车削质量的措施 634
3 车孔 634
3.2 典型车孔刀具及装夹方法 635
3.3 车孔的切削用量 636
3.4 提高车孔质量的措施 636
4.1 切断的特点 637
4 切断与切槽 637
4.2 切断刀的几何形状和典型切断刀 637
4.5 提高切断和切槽质量的措施 641
4.3 切断的切削用量 641
4.4 切断刀破损原因 641
5 车圆锥 642
6 车细长轴 643
6.1 工件的校直和装夹 643
6.2 细长轴车刀及切削用量 644
6.3 提高车削细长轴质量的措施 646
7 车螺纹 646
7.2 螺纹车刀 646
7.1 车螺纹时能达到的螺纹精度 646
7.3 车螺纹的切削用量 648
7.4 车多头螺纹 652
7.5 旋风铣螺纹 652
8 车特形表面 653
8.1 内、外球面车削 653
8.2 车成形面 654
9.5 金刚石刀具精密车削时的切削用量 655
9.4 进行精密车削的条件 655
9.1 精密车削的概念 655
9.2 精密车削常用刀具 655
9.3 金刚石刀具车削材料的种类 655
9 精密车削 655
10.1 数控车削工艺范围 657
10.2 数控车床的类型与选用 657
10.3 数控车床用刀具和刀夹 657
10.4 数控车削加工程序编制特点 657
10 数控车削加工 657
10.5 数控车床程序编制实例 658
第14章 铣削 660
1.1 铣削特点与铣削方式 660
1.2 常用铣刀规格 660
1 铣削特点和铣刀 660
1.3 铣刀参数选择 672
2 铣削用量 676
2.1 铣削用量四要素 676
2.2 铣削用量的选择 676
3.1 分度头的结构与计算 681
3.2 单式分度 681
3 分度头 681
3.3 差动分度 682
4.1 铣平面 684
4 铣削加工 684
4.2 铣正多边形 684
4.3 铣键槽 686
4.4 铣球面 688
4.5 铣螺旋槽 689
4.6 铣齿式离合器 690
4.7 铣齿轮 691
4.8 平面凸轮的铣削 692
5.1 数控铣床的类型及加工特点 694
5 数控铣削加工 694
5.3 数控铣削刀具与切削用量选择 695
5.2 对数控铣床夹具的要求 695
5.4 确定加工路线时应注意的问题 696
5.5 数控铣床编程举例 696
第15章 钻削、扩削、铰削和镗削 698
1 钻削、扩削、铰削和镗削的工艺特点 698
2 钻削 698
2.1 麻花钻 698
2.2 钻削用量 701
2.3 提高钻孔质量的措施 704
3.2 扩孔的切削用量 705
3 扩削 705
3.1 扩削的特点及常用扩削刀具 705
3.3 锪钻的类型与应用 710
4 铰削 712
4.1 铰刀的结构与规格 712
4.2 铰削用量 717
4.3 铰刀的合理使用 720
5 镗削 721
5.1 镗削的工艺特点 721
5.2 镗刀类型与镗刀的装夹 722
5.3 镗削用量的选择 724
5.4 在镗床上镗孔的基本方法 725
5.5 镗孔质量 726
6 复合刀具加工孔 728
6.1 孔加工复合刀具的特点 728
6.2 孔加工复合刀具的类型 728
第16章 刨削、插削和拉削 730
7.2 常用深孔钻 730
7.1 深孔加工特点 730
7 深孔加工 730
7.3 深孔加工切削用量 733
7.4 深孔钻削中常见的问题与解决方法 733
8.2 数控钻床的选用 734
8 数控钻削加工 734
8.1 数控钻床类型 734
8.4 刀具的选用及切削用量的确定 735
8.5 确定加工顺序及走刀路线 735
8.3 对夹具的要求 735
8.6 数控钻镗床的编程特点 737
8.7 数控钻镗床编程举例 737
6.3 复合刀具切削用量的选择原则 739
1 刨削 739
1.1 刨削用量及其选择 739
1.2 刨刀角度的选择及典型刨刀 739
1.3 精刨表面常见缺陷及消除措施 742
2 插削 742
3 拉削 743
3.1 拉削特点 743
3.2 拉刀结构及其切削部分几何参数 744
3.3 拉削方式、拉削层参数和拉削力 745
3.4 拉削余量及拉削前的要求 746
3.5 提高拉削质量的措施 747
第17章 齿面加工 749
2.1 滚齿加工特点及齿轮滚刀 749
1 齿面加工方法 749
2 滚齿 749
2.2 滚齿机及应用计算与调整 753
2.3 滚齿深度和切削用量 760
2.4 高速高效滚齿 762
2.5 滚齿常出现的误差与原因 762
3 插齿 763
3.1 插齿加工特点及插齿刀 763
3.2 插齿机及应用计算与调整 766
3.3 插齿切削用量 768
3.5 插齿常出现的误差及原因 770
3.4 剃前插齿与磨前插齿 770
4 剃齿 771
4.1 剃齿及剃齿刀 771
4.2剃齿余量及切削用量 775
4.3保证剃齿精度的要求 775
4.4 剃齿法的发展 776
4.5剃齿常出现的误差和原因 777
5.1 珩齿及测磨轮 778
5 珩齿 778
5.4 测齿常出现的误差及产生原因 781
5.2 珩齿用量和加工余量 781
5.3 珩齿精度 781
6 磨齿 782
6.1 磨齿及砂轮 782
6.2 磨齿余量和磨齿用量 784
6.3 提高磨齿精度和效率的措施 785
6.4 磨齿常出现的误差及原因 786
7 硬齿面齿轮的刮削加工 788
7.1 硬齿面圆柱齿轮刮削滚刀 788
7.2 硬齿面插齿刀 788
7.4 硬齿锥齿轮刮削刀具 789
7.3 硬齿面剃齿刀 789
1 磨削的特点及常见磨削类型 791
1.1 磨削的特点 791
1.2 常见磨削类型 791
第18章 磨削 791
2 磨料和磨具 792
2.1 磨具的结构与标志 792
2.2 主要磨具类型及其用途 793
2.3 磨料、磨具的选择 796
2.4 磨具的安全使用与保管 799
3 磨削参数的选择及磨削余量的确定 800
3.1 磨削参数的选择 800
3.2 磨削余量的确定 801
4 砂轮修整方法和修整工具的选择 803
4.1 砂轮修整的作用 803
4.2 砂轮修整方法和修整工具 803
5 常见磨削缺陷、产生原因及防止措施 805
6.2 低粗糙度高精度磨削对机床的要求 807
6 低粗糙度高精度磨削 808
6.1 低粗糙度高精度磨削特点 808
6.3 低粗糙度高精度磨削砂轮的选择 809
7 高效、强力磨削 811
7.2 缓进给强力磨削 812
7.1 高速磨削 812
7.3 砂带磨削 813
第19章 特种加工及超精密加工 814
1 电火花加工 815
1.1 电火花加工原理与特点 815
1.2 电火花加工电参数 818
1.3 线切割加工 820
1.4 电抛光加工 822
2.2 电解加工工艺参数 824
2 电解加工 824
2.1 电解加工的原理及工艺特点 824
2.3 电解磨削 827
3 电束加工 829
3.1 激光加工 829
3.2 电子束加工 831
3.3 离子束加工 831
4 超声波加工 835
4.1 超声波加工原理及工艺特点 835
4.2 超声波加工的应用 837
5 珩磨 838
5.1 珩磨的工作原理及特点 838
5.2 珩磨工艺参数的选择 839
6.1 超精加工的原理 842
6.2 超精加工示例 842
6 超精加工 842
6.3 超精加工切削参数的选择 843
7 研磨和抛光 843
7.1 研磨 843
7.2 抛光 845
7.3 液体抛光 846
8 其他特种加工 846
8.1 化学加工 846
8.2 等离子体加工 849
8.3 高速流体加工 850
1.2 划线常用的工具 852
第20章 钳工 852
1.1 划线的作用和步骤 852
1 划线 852
1.3 常用的平面划线 854
2 锯割 855
2.1 手锯 855
2.2 锯割方法 855
3.1 凿削工具 857
3 凿削 857
2.3 产生锯割废品和锯条损坏的原因 857
3.3 凿削安全技术 858
4 锉削 858
4.1 锉刀分类、编号规则 858
3.2 凿削方法 858
4.2 锉刀结构名称术语 859
4.3 锉刀型式及尺寸 860
4.4 锉削方法 863
4.5 锉削注意事项及产生废品的原因 863
5.1 刮削工具 864
5 刮削 864
5.2 刮削方法 865
6.1 攻螺纹和套螺纹工具 867
6 攻螺纹和套螺纹 867
6.2 攻螺纹和套螺纹的方法 869
6.3 攻螺纹和套螺纹常见废品形式及产生原因 873
7 型材及管材的弯曲 875
第21章 焊接、胶接与铆接 880
1 焊接 880
1.1 焊接方法特点及应用 880
1.2 金属材料的焊接性及焊接材料的选用 881
1.3 铸铁件焊补工艺方法选择 882
1.4 焊条及焊丝 883
1.5 焊缝符号表示法 885
2.1 胶接与胶粘剂 890
2 胶接 890
2.2 胶接接头设计 896
2.3 胶接工艺 897
3 铆接 899
3.1 铆接的种类、特点及应用 899
3.2 铆接结构设计 899
3.3 铆钉联接的强度计算 901
3.4 常用铆钉种类及应用 902
3.5 铆接方法、铆接缺陷及预防 903
1 装配工艺基础 906
第22章 装配工艺与尺寸链 906
1.1 装配生产类型及其特点 906
1.2 装配方法的选择 907
1.3 装配工艺规程的制订 908
2 装配前的准备工作 909
2.1 消洗 909
2.2 刮削 909
2.3 平衡 914
3 零部件的联接方法 918
3.1 螺纹联接 918
3.2 键、销联接 919
3.3 过盈联接 920
3.4 焊接、胶接与铆接 922
4 校准 922
5 典型部件的装配 926
5.1 滑动轴承的装配工艺要点 926
5.2 滚动轴承的装配工艺要点 927
5.3 齿轮及蜗轮的装配工艺要点 929
6 尺寸链 933
6.1 尺寸链基本术语 933
6.2 尺寸链的分类 934
6.3 尺寸链计算公式 934
6.4 尺寸链分析与计算 939
1 机床的使用与保养 941
第23章 机床使用保养与维修 941
1.1 机床的磨损 941
1.2 机床的保养 942
1.3 机床使用中注意事项 944
2 机床修理 944
2.1 修理工作类别及内容 944
2.2 机床大修工作程序 945
2.3 修理周期与修理周期结构 947
2.4 机床的拆卸与清洗 947
2.5 导轨、主轴、丝杠的修理 952
2.6 修复机床零件的新工艺 956
2.7 专用测量工具 957
2.8 修理尺寸链的分析与调整 958
第24章 润滑、冷却及防锈 961
1 润滑与润滑剂 961
1.1 润滑的作用 961
1.2 常见的润滑状态 961
1.3 润滑剂 962
2.1 金属腐蚀及其分类 973
2.2 金属锈蚀及其影响因素 973
2 金属腐蚀与锈蚀 973
3.2 水溶性缓蚀剂及其应用 974
3.3 油溶性缓蚀剂及其应用 974
2.3 防止金属锈蚀的主要措施 974
3.1 缓蚀剂的种类 974
3 缓蚀剂 974
3.4 气相缓蚀剂 976
4 防锈油脂 977
4.1 防锈油脂应具备的性能要求 977
4.2 防锈油脂的分类 977
4.4 防锈油脂的使用方法和注意事项 978
5 防锈切削冷却液 978
5.1 防锈切削冷却液的作用 978
4.3 选择防锈油脂的基本要点 978
5.2 防锈切削冷却液的分类 979
5.3 防锈切削冷却液的应用 979
6 工序间防锈 981
6.1 机械加工工序间防锈 981
6.2 热处理后工件的清洗防锈 981
6.3 成品工件(或成品)的清洗与防锈 981
7.1 鉴别锈蚀的一般方法 984
7 除锈 984
7.2 机械除锈法 985
7.3 化学除锈法 985
1.2 技术经济分析的性质和基本方法 988
1.3 费用的概念 988
第25章 技术经济与管理 988
1.1 技术经济分析工作的基本步骤 988
1 技术经济分析的基本原理 988
1.4 费用的估算 989
1.5 资金的时间价值 990
2 新产品开发的技术经济分析 991
2.1 新产品开发与产品更新换代 991
2.3 新产品设计的技术经济分析 991
2.2 新产品开发战略 991
2.4 新产品的成本估计与定价 992
2.5 新产品开发方案的技术经济评价 992
2.6 自行研制开发新产品的技术经济分析 993
3 设备更新的技术经济分析 995
3.1 设备的更新战略、磨损与补偿及寿命 995
3.2 设备的折旧 996
3.3 设备大修理经济界限的分析 998
3.4 设备更新的技术经济分析 998
4.1 全面质量管理的基本概念 1000
4.2 生产现场的质量管理 1001
4.3 全面质量管理常用统计工具 1004
5 看板管理 1008
5.1 应用看板管理的条件 1008
5.2 看板的形式 1008
5.3 看板使用规划 1009
5.4 看板周转张数的计算 1009
6 设备的管理 1009
6.1 设备的安装与验收 1009
6.2 设备的分类与编号 1009
6.4 设备的使用管理 1010
6.3 设备的技术档案管理 1010
6.5 闲置封存设备的管理 1011
6.6 设备的改进与改装 1011
6.7 设备的报废 1011
7 价值工程 1011
7.1 价值工程及其应用 1011
7.2 价值工程过程 1011
7.3 运用价值工程的组织工作 1017
附录 机械工人技术等级标准和国家职业标准 1018
主要参考文献 1042