图书介绍
机械制造工程pdf电子书版本下载
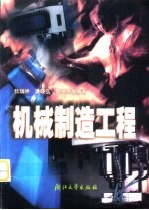
- 狄瑞坤等编著 著
- 出版社: 杭州:浙江大学出版社
- ISBN:7308026345
- 出版时间:2001
- 标注页数:350页
- 文件大小:18MB
- 文件页数:362页
- 主题词:
PDF下载
下载说明
机械制造工程PDF格式电子书版下载
下载的文件为RAR压缩包。需要使用解压软件进行解压得到PDF格式图书。建议使用BT下载工具Free Download Manager进行下载,简称FDM(免费,没有广告,支持多平台)。本站资源全部打包为BT种子。所以需要使用专业的BT下载软件进行下载。如 BitComet qBittorrent uTorrent等BT下载工具。迅雷目前由于本站不是热门资源。不推荐使用!后期资源热门了。安装了迅雷也可以迅雷进行下载!
(文件页数 要大于 标注页数,上中下等多册电子书除外)
注意:本站所有压缩包均有解压码: 点击下载压缩包解压工具
图书目录
第一章 绪论 1
1.1 机械制造业的地位及我国的现状 1
1.1.1 机械制造业的地位 1
1.1.2 我国机械制造业的现状 1
1.2 机械制造过程及机械制造系统 2
1.2.1 机械制造过程 2
1.2.2 机械制造工艺与流程 2
1.2.3 机械制造系统 4
1.3 机械制造工艺方法及选择 5
1.3.1 机械制造工艺方法分类 5
1.3.2 各种机械加工方法的特点与选择 6
1.4 机械制造领域的发展 8
1.4.1 先进机械制造技术的形成与特点 8
1.4.2 机械制造工艺的技术进展和发展趋势 8
1.4.3 机床技术的进展与发展趋势 10
1.4.4 切削加工技术的发展趋势 11
1.5 机械制造科学技术前沿 12
1.5.1 计算机集成制造 12
1.5.2 智能制造 12
1.5.3 并行工程 13
1.5.4 精益生产 14
1.5.5 快速原型制造 14
1.5.6 超高速切削和磨削 14
1.5.7 微米/纳米技术 14
1.5.8 智能机器人 14
第二章 机械制造基本概念 16
2.1 生产过程、生产类型和生产纲领 16
2.1.1 生产过程 16
2.1.2 生产纲领和生产类型 16
2.2 机械加工工艺过程 17
2.3.1 金属切削机床的分类 19
2.3 金属切削机床及金属切削过程的概念 19
2.3.2 金属切削机床的型号 20
2.3.3 机床的主要技术参数 22
2.3.4 表面成形运动分析 22
2.3.5 金属切削过程的基本定义 24
2.3.6 机床的运动 27
2.3.7 机床的传动原理 28
2.4 刀具 31
2.4.1 刀具的类型 31
2.4.2 刀具切削部分的基本定义 40
2.4.3 刀具角度的换算 43
2.4.4 刀具的工作角度 44
2.4.5 刀具材料 46
2.5.1 工件的装夹和机床夹具 50
2.5 机床夹具 50
2.5.2 夹具的分类 51
2.5.3 夹具的组成 52
第三章 金属切削的基本规律及应用 54
3.1 金属切削过程 54
3.1.1 切削变形 54
3.1.2 第二变形区的变形 56
3.1.3 积屑瘤的形成及其对切削过程的影响 58
3.1.4 切屑变形的变化规律 60
3.1.5 切屑的类型及其变化 60
3.1.6 已加工表面的形成过程 61
3.2 切削力 62
3.2.1 切削力的来源、合力、分解 62
3.2.2 切削力的理论公式 63
3.2.3 切削力的实验公式 64
3.2.4 切削功率 65
3.2.5 影响切削力的因素 65
3.3 切削热和切削温度 71
3.3.1 切削热的产生和传出 71
3.3.2 影响切削温度的主要因素 71
3.3.3 切削温度的理论计算 73
3.3.4 切削温度对工件、刀具和切削过程的影响 74
3.4 刀具磨损与耐用度 75
3.4.1 刀具磨损的形式 75
3.4.2 刀具磨损的原因 75
3.4.3 刀具磨损过程及磨钝标准 76
3.4.4 刀具耐用度及其与切削用量的关系 77
3.5 刀具合理几何参数的选择 78
3.5.1 前角及前刀面形状的选择 79
3.5.2 后角和副后角的选择 81
3.5.3 主偏角、副偏角及刀尖形状的选择 82
3.5.4 刃倾角的选择 83
3.6 切削用量的选择 85
3.6.1 选择切削用量的原则 85
3.6.2 ap、f、v 的确定 86
第四章 机床主要部件设计理论 88
4.1 机床的主轴组件 88
4.1.1 主轴组件的基本要求 88
4.1.2 主轴组件的布局 90
4.1.3 主轴轴承的选择和布置形式 93
4.1.4 滚动轴承间隙的调整和预紧 96
4.2 机床的支承件及导轨 98
4.2.1 支承件的基本要求 98
4.2.2 导轨的基本要求 99
4.2.3 滑动导轨的设计 100
4.2.4 滚动导轨简介 108
第五章 车床 111
5.1 概述 111
5.2 CA6140型普通车床 111
5.2.1 机床的布局 111
5.2.2 机床的主传动系统 112
5.2.3 进给运动传动系统 117
5.2.4 车床的主要结构 124
5.3 MJ-50数控车床 135
5.3.1 MJ-50数控车床的布局 136
5.3.2 MJ-50数控车床的传动系统 138
5.3.3 MJ-50数控车床的自动回转刀架和自动控制尾架结构 139
6.1.2 齿轮轮齿的加工方法 140
6.1.1 定义及分类 140
6.1 概述 140
第六章 齿轮加工机床 140
6.2 滚齿加工与滚齿机 141
6.2.1 滚齿原理 141
6.2.2 滚切直齿圆柱齿轮的运动分析 141
6.2.3 滚切斜齿圆柱齿轮的运动分析 143
6.3 Y3150E 型滚齿机 145
6.3.1 机床的用途及布局 145
6.3.2 机床的传动系统分析 146
6.3.3 Y3150E 型滚齿机的合成机构 150
6.4 插齿加工与插齿机 152
6.4.1 插齿原理 152
6.4.2 Y5132型插齿机 152
6.5 磨齿加工和磨齿机 155
6.5.1 磨齿加工原理 155
6.5.2 Y7132A 型磨齿机 156
7.1 概述 161
7.2 加工中心的特性分析 161
7.2.1 主传动系统 161
第七章 数控镗铣加工中心 161
7.2.2 进给系统 163
7.3 加工中心的自动换刀系统 163
7.3.1 自动换刀系统的结构 163
7.3.2 刀库的结构 165
7.3.3 刀库的容量及选刀方式 165
7.4 JCS-018A 立式加工中心 166
7.4.1 机床的用途及特点 166
7.4.2 机床的传动系统 167
7.4.3 机床的主要结构 169
8.1.1 工件定位的基本原理 175
第八章 机床夹具设计基础 175
8.1 工件的定位和定位元件 175
8.1.2 常用定位方法的定位元件 178
8.2 定位误差的分析与计算 184
8.2.1 定位误差及其产生的原因 184
8.2.2 定位误差的计算 185
8.2.3 定位装置设计示例 192
8.3 工件夹紧 193
8.3.1 夹紧力的确定 194
8.3.2 常用三种基本夹紧机构 198
8.4 几种常用典型夹具 208
8.4.1 联动夹紧机构 208
8.4.2 对中与定心夹紧机构 209
9.1 机械加工工艺规程的形式、作用及制订步骤 211
9.1.1 机械加工工艺规程的类型、型式和格式 211
第九章 机械加工工艺规程的制订 211
9.1.2 机械加工工艺规程的作用 214
9.1.3 机械加工工艺规程制订的步骤 214
9.2 零件工艺分析和毛坯的选择 215
9.2.1 零件的技术要求分析 215
9.2.2 零件的结构工艺性分析 216
9.2.3 毛坯的选择 217
9.3 定位基准及其选择 219
9.3.1 基准的概念及其分类 219
9.3.2 定位基准的选择 221
9.4 机械加工工艺路线的拟订 224
9.4.1 表面加工方法的选择 224
9.4.2 加工顺序的安排 228
9.4.3 工序集中与工序分散 230
9.5.1 加工余量及其影响因素 231
9.4.4 机床和工艺装备的选择 231
9.5 加工余量和工序尺寸的确定 231
9.5.2 确定加工余量的方法 234
9.5.3 工序尺寸及其公差的确定 234
9.6 计算机辅助工艺规程设计 235
9.6.1 CAPP 的基本结构 235
9.6.2 CAPP 的类型 236
9.7 机械加工的生产率和技术经济性分析 238
9.7.1 机械加工时间定额 238
9.7.2 提高机械加工中生产率的工艺途径 239
9.7.3 机械加工的技术经济性分析 242
9.8 机械加工工艺规程制订实例 244
9.8.1 零件的结构和技术要求分析 244
9.8.2 零件的加工工艺过程 245
9.8.3 基准选择分析 246
9.8.4 主要加工工序分析 247
10.1 尺寸链的基本概念 249
10.1.1 尺寸链的组成 249
第十章 机械制造中的尺寸链 249
10.1.2 尺寸链的特性和形式 250
10.2 尺寸链计算的基本公式 251
10.2.1 直线及角度尺寸链的计算公式 251
10.2.2 平面尺寸链的计算方法 257
10.3 工艺尺寸链的解算 259
10.3.1 定位基准与设计基准不重合时的尺寸换算 259
10.3.2 测量基准与设计基准不一致时的工艺尺寸链的计算 259
10.3.3 加工中需同时保证多尺寸的尺寸换算 261
10.3.4 需多次加工时设计基准标注尺寸时,工序尺寸的换算 262
10.3.5 需保证表面处理层的深度时工序尺寸的换算 263
10.3.6 用跟踪图解法解算工艺尺寸链 264
10.4.1 装配精度 268
10.4 装配尺寸链的计算方法 268
10.4.2 装配精度与零件精度的关系 269
10.4.3 装配尺寸链的建立 270
10.4.4 装配方法及其选择 274
第十一章 机械加工精度 287
11.1 概述 287
11.1.1 机械加工精度的概念 287
11.1.2 影响机械加工精度的因素 287
11.2 工艺系统的几何误差 288
11.2.1 原理误差 288
11.2.2 机床的几何误差 288
11.2.3 装夹误差和夹具误差 293
11.2.4 刀具误差 293
11.2.5 调整误差 293
11.3 工艺系统的受力变形 294
11.3.1 基本概念 295
11.3.2 工艺系统刚度的特点及影响因素 296
11.3.3 工艺系统受力变形对加工精度的影响 300
11.3.4 减小工艺系统受力变形的途径 306
11.4 工艺系统的热变形 309
11.4.1 概述 310
11.4.2 机床热变形对加工精度的影响 310
11.4.3 刀具热变形对加工精度的影响 311
11.4.4 工件热变形对加工精度的影响 312
11.4.5 减小工艺系统热变形的途径 314
11.5 工件残余应力 316
11.5.1 残余应力引起的变形 317
11.5.2 减少残余应力及其所引起变形的措施 318
11.6.2 加工误差的综合 319
11.6.1 加工误差的性质和分类 319
11.6 加工误差的统计分析 319
11.6.3 加工误差的统计分析法 320
第十二章 机械加工表面质量 332
12.1 概述 332
12.1.1 机械加工表面质量的概念 332
12.1.2 机械加工表面质量对零件使用性能的影响 332
12.2 影响加工表面质量的工艺因素 334
12.2.1 切削加工时的影响因素 334
12.2.2 磨削加工时的影响因素 337
12.3 提高机械加工表面质量的工艺方法 340
12.3.1 研磨 340
12.3.2 珩磨 343
12.3.3 超精加工 346
12.3.4 滚压加工和喷丸强化 348