图书介绍
微电子焊接技术pdf电子书版本下载
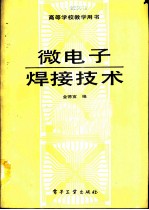
- 金德宣编 著
- 出版社: 北京:电子工业出版社
- ISBN:7505308661
- 出版时间:1990
- 标注页数:365页
- 文件大小:26MB
- 文件页数:374页
- 主题词:
PDF下载
下载说明
微电子焊接技术PDF格式电子书版下载
下载的文件为RAR压缩包。需要使用解压软件进行解压得到PDF格式图书。建议使用BT下载工具Free Download Manager进行下载,简称FDM(免费,没有广告,支持多平台)。本站资源全部打包为BT种子。所以需要使用专业的BT下载软件进行下载。如 BitComet qBittorrent uTorrent等BT下载工具。迅雷目前由于本站不是热门资源。不推荐使用!后期资源热门了。安装了迅雷也可以迅雷进行下载!
(文件页数 要大于 标注页数,上中下等多册电子书除外)
注意:本站所有压缩包均有解压码: 点击下载压缩包解压工具
图书目录
第一章 绪论 1
1.1 微电子器件的发展概况 1
1.1.1 晶体管和集成电路 2
1.1.2 半导体光电子器件 5
1.1.3 特种微电子器件 9
1.2 微电子器件焊接概况 15
第二章 焊区金属材料及相图 20
2.1 合金型器件的内电极金属材料 20
2.2 平面型器件的内电极金属材料 23
2.3 管芯焊接的金属材科 24
2.4 器件引线金属材料 25
2.5 常用金属材料的特性数据表 26
2.6 相图及其应用 29
2.6.1 一元系相图 29
2.6.2 二元系相图 30
2.6.3 三元系相图 49
第三章 焊区金属化制备技术 53
3.3 物理气相淀积技术 53
3.1.1 气体分子运动的基本理论 53
3.1.3 真空蒸发淀积技术 56
3.1.3 溅射技术 63
3.2 化学汽相淀积技术 68
3.2.1 氢还原汽相淀积技术 69
3.2.2 热分解汽相淀积技术 69
3.2.3 化学汽相淀积实例 70
3.3 金属属硅化物淀积技术 71
3.3.1.淀积方法 71
3.3.2 金属硅化物膜的性属 72
3.3.3 金属硅化物的应用 73
3.4 器件芯片金属化中的问题 74
3.4.1 台阶覆盖问题 74
3.4.3 P-n结尖峰问题 76
3.4.2 淀积膜的合金成份控制问题 76
3.4.4 杂质沾污问题 78
3.4.5 铝层腐蚀问题 79
3.4.6 金属电迁移问题 79
3.5 丝网漏印技术 81
3.5.1 基片的材料 81
3.5.2 掩摸原版的制备 82
3.5.3 漏印极的制备和安装 84
3.5.4 印浆的配制 85
3.5.5 焙烧工艺 85
3.5.6 应用 87
3.6 陶瓷金属化技术 87
3.6.1 钼锰粉末烧结法 87
3.6.2 钛粉末烧结法 88
3.7 电镀技术 89
3.7.1 镀铜技术 91
3.7.2 镀?技术 93
3.7.3 镀铬技术 95
3.7.4 镀银技术 99
3.7.5 镀金技术 102
3.7.6 光亮SnPb电镀技术 107
3.7.7 电镀层质量检测 108
3.8 淀积膜厚度的测量方法 109
3.8.1 石英晶体振荡法 109
3.8.4 光干涉法 110
3.8.3 探针法 110
3.8.2 微量天平法 110
3.8.5 电阻法及涡流法 111
第四章 钎焊技术 112
4.1 钎焊的基本原理 112
4.1.1 钎焊接头的形成过程 112
4.1.2 钎焊接头的金属学性质 115
4.2 钎料 116
4.2.1 钎料的基本要求及熔化特性 116
4.2.2 软钎料 117
4.2.3 硬钎料 120
4.3 钎剂 121
4.3.1 钎剂的作用和要求 121
4.3.2 软钎剂 122
4.3.3 硬钎剂 125
4.3.4 钎焊后钎剂的去除 127
4.4 电子级焊膏 127
4.4.1 电子级焊膏的成分和性能 128
4.4.3 应用 130
4.4.2 金属存留量的讨算 130
4.4.4 焊膏使用的注意事项 131
4.5 钎焊的方法 132
4.5.1 钎焊前零件表面的准备 132
4.5.2 电烙铁钎焊法 133
4.5.3 机械热脉冲劈刀钎焊法 134
4.5.4 电阻钎焊法 134
4.5.6 气体保护炉式钎焊法 135
4.5.5 光学及激光钎焊法 135
4.5.7 真空钎焊法 139
4.5.8 感应钎厚法 142
4.5.9 超声波钎焊法 144
4.5.10 扩散钎焊法 144
4.5.11 各种钎焊方法的比较和选择 144
4.6 影响钎焊强度的因素 145
4.6.1 钎焊温度和加热盱间的影响 145
4.6.2 母材强度及间隙的影响 146
4.6.3 钎缝缺陷及表面粗糙度的影响 147
4.7 钎焊的质量分析及检验方法 147
4.7.1 钎焊接头的缺陷和钎透率 147
4.7.2 钎焊缺陷的检查方法 149
4.7.3 钎焊接头的腐蚀和防护 150
4.8 钎焊的可焊性评价 152
4.8.1 可焊性的试验方法及试验标准 152
4.8.3 可焊性试验设备 155
4.8.2 可焊性评价的基准规定 155
4.8.4 可焊性试验结果和分析 156
第五章 熔焊技术 160
5.1 熔焊的冶金过程 160
5.1.1 金属的结晶组织 160
5.1.2 焊区的金相组织 161
5.1.3 熔焊的局部冶金过程 162
5.2 电子束焊接技术 162
5.2.1 电子柬的产生机理 163
5.2.2 电子束焊按的基本方法 163
5.2.3 电子束焊接的特点和应用 166
5.3 激光焊接技术 166
5.3.1 激光的特性和激光焊的特点 166
5.3.2 激光焊接机的工作原理 167
5.3.3 激光焊攒的工艺参数 169
5.3.5 激光焊接热稳定的建立及参效选择 172
5.3.4 激光脉冲波形测量的方法 172
5.3.6 激光封焊器件外壳的强度和密封性能 174
5.3.7 激光封焊可伐外壳的缺陷 175
5.4 钨极脉冲微氩弧焊技术 176
5.4.1 氩弧焊及钨极脉冲微氩弧焊 176
5.4.2 钨极脉冲微氩弧焊的设备 177
5.4.3 钨电极及焊接参数的选择 180
5.5 微等离子焊接技术 181
5.5.2 等离子弧的产生 182
5.5.1 等离子体的特性 182
5.5.3 等离子发生器——等离子枪 183
5.5.4 微等离子焊接 184
5.5.5 脉冲微等离子焊接 186
5.6 高频熔焊技术 186
5.6.1 高频电流的趋肤效应和邻近效应 186
5.6.2 高频熔焊基本的方法 187
6.1 压焊的理论基础 190
6.1.1 压焊接头的形成机理 190
第六章 压焊技术 190
6.1.2 压焊过程的特证和机理 191
6.2 接触焊技术 193
6.2.1 接触焊的基本原理及特征 193
6.2.2 点焊和滚焊的焊点电阻分析 194
6.2.3 点焊、滚焊时的热平衡 197
6.2.4 点焊、滚焊的形成过程及影响焊接的因素 198
6.2.5 不同厚度、不同材料的点焊和滚焊 200
6.2.6 焊点的缺陷及产生原因 202
6.2.7 焊点质量的检查方法 205
6.2.8 点焊、滚焊的设备 207
6.2.9 平行缝焊 210
6.2.10 平行微隙焊接 217
6.3 冷压焊技术 221
6.3.1 冷压焊的基本原理及影响冷压焊的因素 221
6.3.2 冷压焊应用例举 222
6.4.1 热压焊的基本原理 223
6.4 热压焊技术 223
6.4.2 热压焊的基本方法 224
6.4.3 其它热压焊方法 227
6.4.4 影响焊接的因素 229
6.4.5 “紫斑”现象的分析 230
6.4.6 半自动金丝球焊设备 232
6.5 超声波焊接技术 234
6.5.1 超声波焊的物理过程 235
6.5.2 超声波焊接设备 236
6.5.3 超声波焊接的几种方法 245
6.5.4 影响超声波焊的因素 247
6.5.5 引线键合的质量控制 249
6.6 真空扩散焊技术 250
6.6.1 扩散焊接头的物理过程 251
6.6.2 真空扩散焊的设备 251
6.6.3 真空扩散焊的主要工艺参数 253
6.6.4 不同膨胀系材料的真空扩散焊 254
6.6.5 真空扩散焊的优点 255
6.6.6 真空扩散焊的应用实例 255
6.6.7 真空扩散焊接头的质量检验 257
第七章 粘接技术 259
7.1 低温银浆粘接技术 259
7.1.1 银浆成份及配制 259
7.1.2 银浆烧结原理及粘接工艺 259
7.1.3 银浆粘接的质量控制 261
7.2 共晶焊技术 261
7.2.1 金—硅共晶焊原理 261
7.2.2 金—硅共晶焊的基本方法 262
7.2.3 金—硅共晶焊的质量控制 263
7.2.4 Au-Ag-Si系共晶焊 265
7.2.5 Au-Sn-Si系共晶焊 266
7.2.6 Au-Sn-GaAs系共晶焊 267
7.3.1 导电胶的组份及特性 268
7.3 导电胶粘接技术 268
7.3.2 导电胶粘接工艺 271
7.4 环氧树脂粘接技术 272
7.4.1 环氧树脂的合成固及化机理 272
7.4.2 环氧树脂的特性 274
7.4.3 环氧树脂粘按工艺 276
7.5 低熔点玻璃粘接技术 277
7.5.1 低熔点玻璃及重要参数 277
7.5.2 低熔点玻璃材料性能 280
7.5.3 低熔点玻璃粘接工艺 287
7.5.4 低熔点玻璃粘接可靠性 290
7.6 芯片粘接(或焊接)强度的测量方法 291
7.6.1 芯片粘按(或焊接)强度分析 291
7.6.2 芯片粘按(或焊接)强度的测试方法 293
7.7 芯片粘接(或焊接)设备 294
7.7.1 手动装片设备 294
7.7.2 半自动(自动)装片设备 294
第八章 梁式引线技术 297
8.1 淀积焊技术 298
8.2 梁式引线的冶金系统 299
8.2.1 接触金属 299
8.2.2 键接金属 300
8.2.3 阻挡扩散金属 300
8.2.4 “梁”金属 301
8.3 梁式引线金属化工艺 302
8.3.1 硅接触工艺 303
8.3.2 钦-钼-金系统工艺 303
8.3.3 铝-钛-钼-金系统工艺 304
8.3.4 钛-铂-金系统工艺 304
8.3.5 “梁”镀金工艺 305
8.3.6 “梁”腐蚀工艺 305
8.3.7 全铝系统工艺 306
8.4 器件芯片表面钝化工艺 307
8.4.1 二氧化硅钝化膜工艺 307
8.4.2 氮化硅钝化膜工艺 308
8.4.3 Al2O2介质钝化膜工艺 312
8.5 粱式引线器件制造 312
8.6 梁式引线焊接方法 314
8.6.1 振动焊接法 314
8.6.2 软压焊接法 314
8.6.3 机械和电热脉冲焊接法 315
8.6.4 其它焊接方法 316
8.7 衬底制备 317
8.7.1 衬底材料 318
8.7.2 衬底金属化 319
8.7.3 多层互连及保形涂层技术 320
8.8 梁式引线的设计 321
8.8.1 热阻 321
8.8.2 尺寸的标准化 322
8.9 梁式引线的结构 324
8.9.1 p-n结隔离结构 324
8.9.3 双层布线及迭层板结构 325
8.9.2 空气隔离结构 325
8.10 梁式引线的可靠性 326
第九章 面键合技术 329
9.1 面键合技术的基本方法 329
9.1.1 铜球焊法 329
9.1.2 可控塌扁法 330
9.1.3 多层金属凸点法 330
9.2 凸点的结构及制造 332
9.1.4 单金属凸点法 332
9.2.1 凸点的结构 333
9.2.2 凸点的制造工艺 334
9.2.3 凸点的其它结构 335
9.3 软凸点最佳几何结构的分析 336
9.4 面键合法的衬底 338
9.5 凸点芯片的焊接 339
9.6 其它组焊方法 339
第十章 自动载带组焊技术 341
10.1 器件大圆片加工与凸点的制造 343
10.2 载带设计与制造 345
10.2.1 载带的材料及结构 345
10.2.2 载带的制造工艺 347
10.2.3 载带引线图形设计 348
10.3 载带规格及应用 350
10.3.1 载带的规格 350
10.3.2 载带的应用 352
10.4.1 硅大圆片分割 354
10.4 自动载带组焊工艺 354
10.4.2 内引线焊接 355
10.4.3 内封装 358
10.4.4 检测与筛选 358
10.4.5 引线切断与引线成型 358
10.4.6 芯片安放与粘接 360
10.4.7 外引线焊接及外封装 360
10.5 带凸点的载带 362
参考文献 363