图书介绍
机械加工工艺手册pdf电子书版本下载
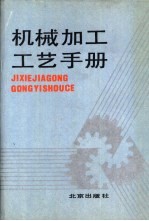
- 李洪主编 著
- 出版社: 北京:北京出版社
- ISBN:7200008133
- 出版时间:1990
- 标注页数:1492页
- 文件大小:62MB
- 文件页数:1512页
- 主题词:机械加工(学科: 手册)
PDF下载
下载说明
机械加工工艺手册PDF格式电子书版下载
下载的文件为RAR压缩包。需要使用解压软件进行解压得到PDF格式图书。建议使用BT下载工具Free Download Manager进行下载,简称FDM(免费,没有广告,支持多平台)。本站资源全部打包为BT种子。所以需要使用专业的BT下载软件进行下载。如 BitComet qBittorrent uTorrent等BT下载工具。迅雷目前由于本站不是热门资源。不推荐使用!后期资源热门了。安装了迅雷也可以迅雷进行下载!
(文件页数 要大于 标注页数,上中下等多册电子书除外)
注意:本站所有压缩包均有解压码: 点击下载压缩包解压工具
图书目录
目录 1
第一篇基础部类 1
第一章常用资料和数学 1
一、计量单位 1
1.法定计量单位 1
2.常用法定计量单位及其换算 3
二、常用数学 7
1.常用数学符号 7
2.三角函数公式 8
3.指数公式 9
4.对数公式 9
三、常用计算 10
1.常用几何图形计算公式 10
2.钢型材理论重量计算公式 12
3.圆周等分孔坐际尺寸计算 13
四、常用材料性能 14
2.常用切削液的分类及配方 18
1.切削液中添加剂的分类及构成 18
五、切削液 18
3.商品切削液 22
4.切削液的浇注流量 23
六、金属防锈 24
1.清洗剂的种类及性能 24
2.防锈油 24
3.气相防锈剂 28
4.防锈可剥塑料 28
5.防锈的具体措施 29
第二章工程材料 30
一、金属材料机械性能的名称、 30
代号及意义 30
二、金属材料的牌号表示方 30
法 30
1.钢牌号表示方法 30
法 32
4.有色金属及合金产品牌号表示方 32
3.铸钢牌号表示方法 32
2.铸铁牌号表示方法 32
三、金属材料热处理的基本概 34
念 34
1.常用热处理方式 34
2.钢的化学热处理 34
3.化学热处理的深度及应用范围 35
4.钢的热处理方式代号表示方法 35
四、钢材 36
1.钢材的涂色标记 36
2.常用钢材牌号及机械性能 37
3.型钢 50
4.钢管 52
5.钢板及钢带 55
五、常用钢号国内外对照 59
六、铸铁 63
国内外对照 66
七、常用铸铁牌号及机械性能 66
八、铸钢 68
九、铜及铜合金 70
十、铝及铝合金 79
十一、粉末冶金材料 86
十二、合成陶瓷材料 89
十三、工程塑料及其制品 90
十四、橡胶制品 95
十五、其它常用材料 99
第三章机械制图 100
一、一般规定 100
二、图样简化画法和规定画 102
法 102
三.尺寸注法 103
四、螺纹画法及其标注方法 105
五、中心孔表示法 107
六、花键画法及尺寸注法 108
七、焊缝符号表示法 108
主要差异 113
八、机械制图新、旧标准的 113
九、国内外机械制图标准的 115
主要区别 115
1.图线型式及用途 115
2.材料剖面符号 115
3.图样画法 116
4.尺寸注法 120
5.螺纹的表示方法 126
第四章尺寸公差与配合 136
一、标准公差、公差等级和 136
基本偏差 136
1.标准公差及公差等级 136
2.基本偏差系列 136
二、孔、轴公差带与配合 138
1.基本尺寸至500mm优先、常用 138
和一般用途的轴、孔公差带 138
差 139
2.基本尺寸至500mm轴的极限偏 139
3.基本尺寸至5C0mm孔的极限偏 144
差 144
4.基本尺寸至500mm基孔制与基 151
轴制常用、优先配合 151
5.基本尺寸至500mm基孔制常用、 153
优先配合的极限间隙或极限 153
过盈 153
过盈 158
6.基本尺寸至500mm基轴制常用、 158
优先配合的极限间隙或极限 158
7.基本尺寸至18mm孔轴公差带 163
8.基本尺寸至18mm部分轴、孔 163
极限偏差 163
9.基本尺寸>500~3150mm常 166
用轴、孔公差带 166
10.基本尺寸>500~3150mm轴、 167
孔极限偏差 167
差 170
三、未注公差尺寸的极限偏 170
四、基本尺寸至500mm公差 172
与配合新旧国标对照 172
第五章形状和位置公差 172
一、形位公差代号、术语及 172
定义 172
1.形位公差代号 172
2.形位公差带定义及示例说明 173
原则 186
2.形位公差值表 186
值 186
1.图样上标注形位公差值的选用 186
二、图样上标注的形位公差 186
三、图样上未注形位公差的 189
公差值 189
四、形位公差标注示例及要 190
点 190
五、形位公差检测规定 191
准符号 193
六、ISO及国外形位公差标 193
第六章表面粗糙度及磨削表面波 194
纹度 194
一、表面粗糙度 194
1.表面粗糙度评定参数及定义 194
2.表面粗糙度数值及应用 195
3.表面粗糙度新、旧国标对照表 196
4.表面粗糙度代号及其注法 197
系列对照 200
5.部分国家表面粗糙度评定参数 200
二、磨削表面波纹度 203
1.术语及解释 203
2.参数 205
3.分级 205
4.平均波幅值W?的评定 205
第七章锥度与角度公差 206
一、锥度、锥角系列及公差 206
1.锥度与锥角系列 206
2.圆锥公差(摘自GB11334-89) 207
3.未注公差角度的极限偏差 209
(GB11335-89) 209
二、棱体的角度、斜度系列及 209
公差 209
第八章螺纹公差 210
一、普通螺纹 210
1.普通螺纹直径和螺距 210
2.普通螺纹基本尺寸 212
3.普通螺纹公差带位置及基本偏 219
差数值 219
4.普通螺纹公差等级及公差值 221
5.普通螺纹的旋合长度 223
6.普通螺纹选用公差带与配合 224
7.普通螺纹偏差表 224
二、梯形螺纹 245
1.梯形螺纹牙型及尺寸 245
3.梯形螺纹基本尺寸 246
2.梯形螺纹直径与螺距 246
4.梯形螺纹公差带位置与基本偏 248
差 248
5.梯形螺纹公差等级及公差值 249
6.梯形螺纹旋合长度 252
9.梯形螺纹标记 253
三、锯齿形螺纹尺寸及公差 253
8.多线梯形螺纹 253
7.梯形螺纹精度与公差带的选用 253
四、管螺纹 257
1.英制55°圆柱管螺纹尺寸及公 257
差 257
2.英制60°圆锥管螺纹尺寸 258
3.米制锥螺纹尺寸 259
五、机床梯形螺纹丝杠、螺母 260
精度 260
1.误差、术语及定义 260
2.丝杠螺母精度等级及应用 260
3.丝杠螺母精度值及表面粗糙度 261
六、滚珠丝杠副 264
1.滚珠丝杠副术语及定义 264
2.滚珠丝杠副精度 266
3.滚珠丝杠副参数和代号 268
第九章渐开线圆柱齿轮精度 269
一、渐开线圆柱齿轮基本齿廓 269
及模数 269
计算 271
二、圆柱齿轮传动几何尺寸 271
三、常用检验尺寸数值 273
四、渐开线圆柱齿轮精度(摘自 282
GB10095—88) 282
1.误差定义和代号 282
2.精度等级 287
3.齿坯检验与公差 288
4.齿轮检验与公差 288
7.其它有关规定 289
6.侧隙 289
5.齿轮副的检验与公差 289
8.图样标注 290
9.齿轮精度数值表 290
10.补充规定 298
五、齿轮公差新、旧标准对 300
照 300
2.公差、偏差值 302
1.误差定义和代号 302
距偏差和轴线平行度公差 302
六、机床圆柱齿轮箱体孔中心 302
七、机床圆柱齿轮副侧隙和 303
齿轮齿厚偏差 303
1.齿轮副极限侧隙 303
2.齿厚极限偏差 303
3.图样标注 304
4.公法线平均长度极限偏差 304
5.应用示例 304
6.偏差和公差数值表 305
7.附录 310
一、直齿锥齿轮传动几何尺 314
寸计算 314
第十章锥齿轮精度 314
二、锥齿轮精度(摘自GB11365- 315
89) 315
1、误差定义及代号 315
3.齿坯要求与公差 318
4.齿轮的检验与公差 318
2.精度等级 318
5.齿轮副的检验与公差 319
6.齿轮副侧隙 319
7.图样标注 320
8.齿轮精度值 320
9.补充件 338
10.参考件 340
11.应用示例 341
几何尺寸计算 342
第十一章圆柱蜗杆蜗轮精度 342
一、普通圆柱蜗杆、蜗轮传动 342
二、圆柱蜗杆、蜗轮精度(摘 343
自GB10089-88 ) 343
1.误差定义和代号 343
2.精度等级 349
3.齿坯的要求与公差 349
4.蜗杆、蜗轮的检验与公差 349
5.传动的检验与公差 349
6.蜗杆传动副的侧隙规定 350
7.其它有关规定 350
8.图样标注 350
9.蜗杆、蜗轮精度值 351
10.参考件 364
11.应用示例 367
第十二章键和花键公差 367
一、平键型式尺寸与公差 367
三、楔键型式尺寸与公差 369
二、半圆键型式尺寸与公差 369
四、矩形花键 371
1.小径定心矩形花键尺寸系列与公差(GB1144-87) 371
2.矩形花键尺寸系列与公差(GB 373
1144-77) 373
五、渐开线花键(摘自GB3478. 376
1~2—83) 376
1.渐开线花键术语、代号及定义 376
3.基准齿形 379
2.基本参数 379
4.尺寸系列 380
5.公差等级及公差值 385
6.齿侧配合 388
7.新国标与ISO4156、旧国标对照 388
第十三章零件结构要素 390
一、中心孔 390
二、球面半径 391
三、润滑槽 392
五、零件倒圆与倒角 393
四、滚花 393
六、砂轮越程槽 394
七、普通螺纹收尾、肩距、 395
退刀槽及倒角尺寸 395
八、普通螺纹底孔尺寸 397
九、圆柱管螺纹收尾、退刀 400
槽及倒角尺寸 400
十一、米制锥螺纹收尾、肩距、 401
退刀槽及倒角尺寸 401
十、圆柱管螺纹底孔尺寸 401
十二、米制锥螺纹接头尾端 402
尺寸 402
十三、梯形螺纹收尾、退刀 402
槽及倒角尺寸 402
十四、梯形螺纹底孔尺寸 403
十五、紧固件—螺栓和螺钉 404
通孔 404
钉的末端型式与尺寸 405
十七、螺钉、螺栓及机器螺 405
十六、管路旋入端用普通螺 405
纹尺寸系列 405
第二篇机械加工工艺 406
第一章机械加工工艺规程的 406
制定 406
一、基本概念 406
1.工艺过程的组成 406
2.工艺规程制定的基本概念 407
3.生产纲领及生产类型 407
二、零件图的工艺审查 408
三、毛坯的选择 410
四、定位基准的选择 412
五、典型表面的加工方案 415
六、工艺文件 417
七、工序简图的绘制 427
八、典型零件的机械加工工 430
艺 430
1.轴的机械加工工艺过程 430
2.箱体的机械加工工艺过程 433
3.齿轮的机械加工工艺过程 436
九、典型机床的工艺编制 439
1.仿形车床的工艺编制 439
2.卡盘多刀半自动车床的工艺编 441
制 441
3.转塔车床的工艺编制 442
4.单轴自动车床的工艺编制 445
5.卧式多轴自动车床的工艺编制 449
一、切削加工能够达到的尺 453
寸经济精度 453
6.组合机床的工艺编制 453
和表面粗糙度 453
第二章切削加工的经济精度 453
二、切削加工能够达到的形 456
状经济精度 456
三、切削加工能够达到的相 457
互位置经济精度 457
位置的平均经济精度 458
四、各利机床加工的形状和 458
五、切削加工能够达到的表面粗糙 460
度 460
第三章机械加工余量 463
一、机械加工余量的分析计 463
算法 463
1.机械加工余量的概念 463
2.影响机械加工余量的因素 464
3.计算机械加工余量的基本公式 465
及其应用 465
二、毛坯机械加工余量的确 466
定 466
1.铸件机械加工余量 466
2.铸件尺寸公差及偏差 472
3.模锻件的机械加工余量及尺寸 474
偏差 474
寸偏差 480
4.自由锻件的机械加工余量及尺 480
5.轧制件轴类零件的机械加工余 489
量 489
6.钢冲压件的机械加工余量及尺 491
寸偏差 491
7.气割毛坯的机械加工余量及尺 491
寸偏差 491
1.轴加工的工序余量 492
三、工序余量的确定 492
2.孔加工的工序余量 494
3.平面加工的工序余量 497
4.齿轮精加工余量 498
5.花键精加工余量 499
6.热处理余量 499
7.攻丝及装配前的钻孔直径 501
四、工序尺寸及其偏差的确 504
定 504
2.车刀的磨钝标准及耐用度 506
1.切削要素 506
第四章切削用量 506
一、车削切削用量 506
3.车削进给量 507
4.车削时切削用量及功率 511
5.车削时各切削分力 514
6.使用条件改变时切削速度、切 520
削功率和切削力的修正系数 520
7.车削时切削速度、切削力和切削功 525
率的计算公式 525
1.龙门刨床的切削用量 528
二、刨削、插削切削用量 528
2.牛头刨床的切削用量 534
3.插床切削用量 538
4.使用条件改变时的切削速度及 540
切削力的修正系数 540
5.刨削、插削时切削速度、切削 543
力及功率的计算公式 543
2.钻削切削用量 544
1.孔加工切削要素 544
三、孔加工切削用量 544
3.扩孔切削用量 561
4.铰孔切削用量 567
5.深孔加工切削用量 572
6.镗孔切削用量 573
度、切削力及切削功率的计算 574
公式 574
8.钻孔、扩孔和铰孔的切削速 574
7.锪孔切削用量 574
四、铣削切削用量 578
1.铣削要素 578
2.铣刀的磨钝标准及耐用度 579
3.各种铣刀铣削进给量 580
4.各种铣刀铣削用量及功率 588
5.使用条件改变时切削速度、切 612
削力和切削功率的修正系数 612
和切削功率的计算公式 621
6.各种铣削切削速度、切削力 621
五、螺纹加工切削用量 626
1.车削螺纹切削用量 626
2.旋风切削螺纹的切削用量 630
3.丝锥、板牙切削螺纹的切削用 631
量 631
4.铣螺纹的切削用量 633
5.螺纹加工的切削速度、切削力 635
和切削功率的计算公式 635
六、拉削切削用量 639
1.拉削进给量 639
2.拉削速度 639
3.拉削力及拉削功率 641
七、齿轮、花键加工切削用 643
量 643
1.滚齿加工切削用量 643
2.蜗轮加工的切削用量 648
3.花键加工切削用量 649
4.插齿加工切削用量 651
5.剃齿加工切削用量 654
6.锥齿轮加工切削用量 654
7.磨削齿轮、花键的切削用量 658
8.齿轮加工切削速度及切削功率 662
的计算公式 662
八、普通磨削切削用量 663
1.外圆磨削切削用量 663
2.无心磨切削用量 669
3.内圆磨切削用量 675
4.平面磨的切削用量 681
九、组合机床切削用量 689
第五章机械加工时间定额 692
一、机械加工时间定额的组 692
成及其计算 692
1.机械加工时间定额的组成 692
二、机动时间的计算 693
2.机械加工时间定额的计算 693
1.车削和镗削 694
2.刨削和插削 695
3.钻削 696
4.铣削 698
5.磨削 700
6.齿轮加工 704
7.螺纹加工 707
时间的确定 709
1.卧式车床 709
8.拉削 709
三、中批以上生产类型其它 709
2.转塔车床 717
3.立式车床 719
4.镗床 721
5.钻床 724
6.铣床 725
7.刨床和插床 728
8.磨床 731
9.齿轮加工机床 736
10.拉床 737
四、单件小批生产类型其它时间 737
的确定 737
1.卧式车床 738
2.立式车床 739
3.镗床 740
5.铣床 741
4.钻床 741
6.刨床 743
7.插床 743
8.磨床 744
9.齿轮加工机床 745
第六章难加工材料的加工 747
一、难加工材料的切削加工 747
1.难切材料的切削特点 747
2.刀具材料的选择 748
3.不锈钢的切削 750
4.高温合金的切削 752
5.钛合金的切削 753
6.高锰钢的切削 756
7.高强度钢的切削 756
二、难加工材料的磨削加工 757
1.难磨材料的磨削特点 757
2.难磨材料的磨削措施 757
第七章高效磨削 759
一、常见高效磨削的主要特 760
点和适用范围 760
二、高速磨削 760
1.高速磨削对机床的要求 760
2.高速磨削砂轮的选择 761
3.高速磨削工艺参数的选择 762
三、缓进给磨削 763
1.缓进给磨削对机床的要求 763
3.缓进给磨削工艺 764
2.缓进给磨削砂轮的选择 764
削 765
5.缓进给磨削工件的常见缺陷及 765
防止措施 765
4.燃气轮机叶片根槽的缓进给磨 765
1.宽砂轮磨削及其对机床的要求 766
2.宽砂轮磨削砂轮的选择 766
3.宽砂轮磨削工艺参数的选择 766
削 766
四、宽砂轮磨削和多砂轮磨 766
4.宽砂轮磨削加工实例 767
5.多砂轮磨削 767
五、砂带磨削 767
1.砂带磨削设备 768
2.砂带的选择 771
3.砂带磨削工艺参数的选择 773
4.砂带磨削应用实例 774
基本概念 775
第八章高光洁度高精度磨削 775
一、高光洁度高精度磨削的 775
二、高光洁度高精度磨削砂 776
轮的选择 776
三、高光洁度高精度磨削工 777
艺参数的选择 777
四、高光洁度高精度磨削工 780
件常见的缺陷及防止措施 780
例 781
五、高光洁度高精度磨削实 781
第九章光整加工 782
一、珩磨 782
1.珩磨加工的特点和应用 782
2.珩磨机床和珩磨头 782
3.珩磨油石的选择及修整 783
4.珩磨工艺参数的选择 786
5.平顶珩磨法 788
6.珩磨常见的缺陷及产生的原因 788
1.超精加工的特点和应用 789
二、超精加工 789
2.超精加工机床和超精加工头 792
3.超精加工油石的选择及修整 793
4.超精加工艺参数的选择 793
5.电解超精加工 794
三、轮式超精珩磨 795
1.轮式超精珩磨的特点和应用 795
2.轮式超精珩磨头 795
因 795
6.超精加工常见的缺陷及产生原 795
3.珩磨轮的选择及修整 796
4.轮式超精珩磨工艺参数的选择 796
四、研磨 797
1.研磨加工的特点和应用 797
2.研具的选择 797
3.研磨剂的选择 799
4.研磨工艺参数的选择 800
3.液体抛光 801
2.砂纸抛光 801
五、抛光 801
1.抛光轮抛光 801
第十章表面冷压加工和修饰 802
一、常用的表面冷压加工 802
方法 802
1.表面冷压强化方法 802
2.螺纹滚压加工 804
3.齿轮齿形滚压加工 805
二、表面冷压加工工具和加工 806
参数 806
1.滚压工具和滚压参数 806
2.挤压工具和挤压参数 810
3.螺纹滚压工具和滚压参数 812
4.齿轮齿形滚压工具和滚压参数 814
三、修复性热喷涂 815
1.热喷涂方法及其应用 815
5.滚花工具和滚花参数 815
6.喷丸强化工具和参数 815
2.热喷涂材料 817
3.修复性热喷涂前的处理 818
4.修复性热喷涂的工艺过程 819
范围 820
2.电镀的一般工艺过程 820
1.常用修饰性镀层的特性及应用 820
四、修饰性电镀 820
第十一章特种加工 821
一、电火花加工 822
1.电火花加工的基本原理和特点 822
2.电火花加工机床类型、特点及 822
用途 822
3.电火花穿孔加工工艺 822
4.型腔电火花加工工艺 829
5.电火花线切割工艺 832
1.电解加工的基本原理及溶解量 835
计算 835
二、电解加工 835
2.电解液的配方及选用 836
3.混气电解加工 838
4.电解加工的工艺参数 839
三、电解磨削 841
1.电解磨削的基本原理 841
2.导电磨轮 841
3.电解液 841
4.电解磨削方式及工艺参数 842
四、超声加工 843
1.超声加工的基本原理和特点 843
2.超声加工的应用 844
五、激光加工 845
1.激光加工的基本原理和特点 845
2.激光加工工艺 845
一、成组工艺及其应用效果 847
第十二章成组工艺 847
二、零件的编码法则及应用 848
举例 848
三、零件的分类编组方法及 851
应用举例 851
四、编制成组工艺规程的方 853
法 853
五、成组生产组织形式 855
方法(摘自JB1838-85) 856
1.通用机床型号表示方法 856
第三篇机床 856
一、金属切削机床型号编制 856
第一章通用机床 856
2.专用机床编号方法 857
3.机床自动线编号方法 857
4.金属切削机床统一名称和类、 857
组、系划分表 857
1.车床 861
数 861
三、通用机床类型与技术参 861
二、新旧机床型号对比 861
2.钻床 879
3.镗床 882
4.磨床 885
5.齿轮加工机床 893
6.螺纹加工机床 898
7.花键轴加工机床 900
8.铣床 902
9.刨床、插床、拉床 910
10.特种加工机床 914
四、金属切削机床精度(摘录) 917
第二章组合机床 920
一、组合机床及其自动线型号 920
表示方法 920
二、组合机床加工精度 920
(GB3668.1~13-83、 921
JB 3557~8-83) 921
三、组合机床通用部件标准 921
四、组合机床“1字头”新系列 938
通用动力部件 938
1.通用动力部件的编号方法 939
2.1HY系列液压滑台 939
3.1HJ和IHJ?系列机械滑台 941
4.1HJ?系列机械滑台(三导轨、 944
高精度级) 944
5.1TZ系列钻削头 945
6.1TG系列攻丝头 948
7.1TX系列铣削头 950
8.1TA系列镗削头与车端面头 951
9.1TP系列偏心镗头 956
10.1TK系列多轴可调头 956
11.1TJ?系列静压镗头 960
12.1TJ系列机械精镗头 961
13.1AHY系列液压回转工作台 964
14.1AHJ系列机械回转工作台 966
台 967
15.1AYU系列多工位移动工作 967
16.1HYA系列长台面型液压滑 968
台 968
17.1HYS系列液压十字滑台 969
18.1LHJ系列机械滑套式动 970
力头 970
19.1LXJB系列箱体移动式机械 972
动力头 972
20.1NG系列主运动传动装置 973
21.LHF系列风动动力头 975
22.大走刀强力及高效高精度平 976
面铣削组合机床 976
第四篇刀具 982
第一章刀具材料 982
一、刀具切削部分的材料性 982
能 982
二、高速钢 982
三、硬质合金 984
的型号和尺寸 991
四、其它刀具材料 991
五、各种刀具材料刀片(条) 991
第二章车刀、刨刀和插刀 1010
一、车刀 1010
1.车刀切削部分的几何参数 1010
2.普通车刀的型式和尺寸 1013
3.转塔车床车刀型式尺寸 1020
二、刨刀和插刀 1021
1.刨刀的型式尺寸 1021
2.插刀的型式尺寸 1022
三、几种典型的车刀和刨刀 1022
第三章孔加工刀具 1024
一、孔加工刀具的分类及应 1024
用 1024
二、钻头 1025
1.中心钻 1025
2.麻花钻 1026
3.硬质合金钻头 1042
4.深孔钻头 1043
三、扩孔钻及锪钻 1045
1.扩孔钻 1045
2.锪钻 1048
四、铰刀 1052
1.铰刀的结构及几何参数 1052
2.手用普通铰刀 1052
3.机用普通铰刀 1054
4.硬质合金铰刀 1058
5.锥度销子铰刀 1061
6.莫氏圆锥和公制圆锥铰刀 1062
五、镗刀 1063
第四章铣刀 1066
一、铣刀的种类和用途 1066
二、铣刀的型式及尺寸 1067
1.圆柱铣刀和面铣刀(端铣刀) 1067
刀 1068
2.三面刃铣刀、槽铣刀和锯片铣 1068
3.立铣刀 1073
4.键槽铣刀、T形槽铣刀和燕尾 1078
槽铣刀 1078
5.凸、凹半圆铣刀、圆角铣刀和 1081
角度铣刀 1081
6.硬质合金可转位铣刀 1083
7.模具铣刀 1087
一、拉刀的种类和用途 1092
第五章拉刀 1092
二、拉刀柄部型式和尺寸 1094
三、几种典型拉(推)刀长 1096
度 1096
第六章螺纹刀具 1099
一、螺纹刀具的种类和用途 1099
二、丝锥 1100
1.机用和手用丝锥 1100
2.螺旋槽丝锥 1105
3.长柄机用丝锥 1106
4.螺母丝锥 1107
5.普通螺纹丝锥的切削角度及加 1110
工螺纹精度 1110
三、手用和机用圆板牙 1110
四、滚丝轮 1114
五、搓丝板 1115
第七章齿轮刀具 1117
一、齿轮刀具的种类及应用 1117
1.齿轮铣刀 1119
二、各类齿轮刀具的型式及 1119
尺寸 1119
2.齿轮滚刀 1120
3.插齿刀 1122
4.剃齿刀 1126
5.锥齿轮刀具 1127
6.花键滚刀及链轮滚刀 1128
1.磨具结构及标志 1129
及其应用 1129
一、磨具结构、标志、分类 1129
第八章磨具 1129
2.磨具分类及应用 1130
二、磨具选择 1132
1.磨料选择 1132
2.粒度选择 1133
3.硬度选择 1134
5.组织选择 1135
6.磨具的综合选择 1135
4.结合剂选择 1135
三、金刚石和立方氮化硼磨 1136
具 1136
1.金刚石和立方氮化硼磨具的结 1136
构和标志 1136
2.金刚石和立方氮化硼磨具的选 1138
择 1138
四、金刚石研磨膏 1139
具选择 1140
五、砂轮修整 1140
1.普通砂轮的常用修整方法和工 1140
2.金刚石滚轮磨削法成形修整 1142
3.金刚石和立方氮化硼磨具的修 1142
整 1142
六、砂轮平衡 1143
第九章刀具紧固部分的结构及 1144
尺寸 1144
一、直柄回转工具柄部、方 1144
头的结构和尺寸 1144
二、套式铰刀和套式扩孔钻 1145
用心轴 1145
三、铣刀紧固部分结构及尺 1147
寸 1147
四、工具柄自锁圆锥的尺寸 1151
一、工装设计的经济性 1153
二、定位误差的计算 1153
第五篇夹具及机床附件 1153
第一章夹具设计常用计算 1153
三、夹紧力的计算 1155
四、常用夹具结构中的计算 1160
第二章夹具标准零、部件 1161
一、定位元件 1161
1.工件以平面为定位基准的定 1161
位元件 1161
3.工件以内孔为定位基准的定 1166
位元件 1166
位元件 1166
2.工件以外圆为定位基准的定 1166
二、对刀元件 1169
1.直角对刀块 1169
2.钻套 1170
三、夹紧元件 1175
四、夹紧执行元件 1180
五、动力气缸 1188
2.常用夹具件公差和配合 1192
1.夹具零件材料及热处理 1192
六、对夹具零、部件的要求 1192
3.机床夹具零、部件技术条件 1193
第三章典型结构及组合夹具 1194
一、典型件及标准 1194
二、典型夹具 1202
三、组合夹具 1205
1.组合夹具的特点及应用 1205
2.组合夹具的分类及主要规格 1205
格 1206
3.组合夹具元件的分类编号 1206
4.组合夹具常用元件的类型及规 1206
5.组合夹具的组装及其提高精度 1214
和刚度的措施 1214
第四章机床附件 1216
一、分度头 1216
1.万能分度头和半万能分度头 1216
2.立卧等分分度头 1216
4.光学、旋转分度头 1217
3.数控、电动分度头 1217
1.三爪自定心卡盘 1218
二、卡盘 1218
2.四爪单动卡盘 1220
3.动力卡盘 1222
4.电动卡盘 1222
三、花盘和过渡盘 1223
1.花盘尺寸 1223
2.三爪、四爪卡盘用过渡盘 1223
1.固定顶尖 1226
四、顶尖及顶尖套 1226
2.回转顶尖 1227
3.拨动顶尖 1228
4.夹持式内锥孔顶尖 1228
5.顶尖套、变径套和莫氏中间套 1229
五、拨盘和鸡心卡头 1229
1.拨盘尺寸 1229
3.卡环 1231
2.鸡心卡头 1231
六、夹头 1232
1.板手夹紧式和自紧式钻夹头 1232
2.钻夹头尾柄 1233
3.快换钻夹头 1233
4.丝锥夹头 1234
5.铣夹头 1235
6.车床、磨床用快换夹头 1235
八、常用吸盘 1236
七、机床用平口虎钳 1236
九、常用回转工作台 1237
十、铣头、插头和镗头 1238
第六篇技术测量 1239
第一章技术测量基础 1239
一、常用计量名词、术语及定 1239
义 1239
二、尺寸、角度传递系统 1239
2.测量误差的分类 1240
1.测量误差和测量原则 1240
的分类 1240
四、测量误差和数据处理 1240
三、计量器具和测量方法 1240
3.测量结果的处理 1241
4.测量误差的来源及防止的方法 1241
五、计量器具的选择 1242
1.计量器具的选择方法 1242
2.测量能力指数M??的计算及评价 1245
3.计量(测量)工程效率指数η的计算及要求 1245
第二章通用量具和量仪 1246
一、量块及量块附件 1246
1.量块 1246
2.量块附件 1248
二、卡尺类型及基本参数 1250
三、千分尺类型及基本参数 1252
四、表类及基本参数 1255
2.测长机和测长仪 1258
1.工具显微镜类型及参数 1258
五、光学、气动、电动量仪 1258
3.光学计与干涉仪 1259
4.投影仪 1259
5.气动量仪 1260
6.电感式测微仪 1261
六、三坐标测量机 1262
第三章长度测量 1262
一、光滑极限量规 1262
1.光滑极限量规的型式、尺寸和 1262
公差 1262
1.光学分度头 1266
2.量规设计计算实例 1269
3.直线尺寸量规的型式、尺寸和 1270
公差 1270
二、一般尺寸的测量 1272
三、大尺寸的测量 1272
1.大尺寸的直接测量 1272
2.大尺寸间接测量的极限误差 1272
3.辅助基准的间接测量 1272
4.跨板式仪器的间接测量 1275
5.光学仪器的间接测量 1277
6.滚轮式仪器的间接测量 1278
四、小尺寸的测量 1279
五、键和花键的测量 1281
1.键和键槽的检验与量规 1281
2.矩形花键的检验及量规公差 1281
3.直齿渐开线花键量规 1285
第四章角度和锥度的测量 1286
二、角度量块及其附件 1286
一、多面棱体 1286
三、万能角度尺 1288
四、水平仪 1289
五、正弦规 1290
六、在平台上测量角度和锥度 1290
1.正弦规测量法 1290
2.标准球(柱)测量法 1291
七、90°角尺和其它类型角尺 1293
八、锥度量规 1295
2.光学转台和分度台 1296
九、光学仪器测量角度 1296
3.锥度测量仪 1297
4.坐标测量机 1297
5.光学倾斜仪 1297
6.自准直仪 1298
7.准线望远镜 1298
第五章螺纹测量 1298
一、普通螺纹量规 1298
二、三针、双针及单针量法 1299
1.普通螺纹、梯形螺纹和蜗杆中 1299
径的三针测量 1299
2.锯齿形螺纹中径三针测量 1302
4.双针和单针法测量螺纹中径 1303
3.圆锥螺纹中径三针测量 1303
1.螺纹千分尺 1304
2.螺纹样板 1304
三、螺纹千分尺和螺纹样板 1304
四、螺纹的各种单项测量法 1305
的测量极限误差 1305
五、丝杠的动态、静态测量 1306
第六章型面样板测量 1307
一、样板的分类 1307
二、样板公差 1308
三、样板的典型结构与要求 1310
一、齿轮的单项测量 1311
1.齿距(周节)误差(△Fp)和(△f?t)的测量和仪器 1311
四、半径样板 1311
第七章齿轮测量 1311
2.基节偏差(△f??)的测量和仪器 1314
3.齿形误差(△ft)的测量和 1314
仪器 1314
4.齿向误差(△Fβ)的测量和仪 1314
器 1314
5.公法线平均长度平均偏差(F△?)及其变动量(△Fw)的测量和仪器 1314
2.单面啮合综合测量 1315
二、综合测量齿轮误差及仪器 1315
1.双面啮合综合测量 1315
7.齿圈径向跳动(△F?)的测量 1315
6.齿厚的测量和仪器 1315
和仪器 1315
三、齿轮整体误差测量及仪 1316
器 1316
1.齿轮整体误差测量原理 1316
2.四种整体误差曲线的特点及用 1316
途 1316
四、齿轮综合检查仪型号及主要 1317
参数 1317
一、检验平面度和直线度的工 1318
1.铸铁平板和岩石平板 1318
具 1318
量 1318
第八章形状与位置公差的测 1318
2.刀口形直尺 1319
3.铸铁平尺 1319
4.钢平尺和岩石平尺 1320
5.平晶 1320
6.检验平直度用光学仪器类型及 1321
参数 1321
二、圆度和圆柱度的测量及 1322
工具 1322
1.圆度仪测量法 1322
2.三点法和二点法 1323
3.圆柱度误差的测量 1323
4.V形架 1323
四、同轴度和对称度的测量 1325
1.机加工表面粗糙度比较样块分 1326
类及参数 1326
二、表面粗糙度比较样块 1326
2.电火花加工表面粗糙度比较样 1326
块 1326
特点及应用 1326
一、表面粗糙度测量方法、 1326
第九章表面粗糙度测量 1326
三、干涉显微镜和光切显微 1327
及参数 1327
镜 1327
3.铸造表面粗糙度比较样块分类 1327
置 1328
第十章检测元件及数显、激光装 1328
一、光栅数显装置 1328
四、表面粗糙度检查仪 1328
二、磁栅数显装置 1329
三、感应同步器数显装置 1329
四、国产常用数显表及检测 1330
元件 1330
五、激光干涉仪 1331
一、冷冲压模具常用材料 1332
第一章冷冲压常用数据 1332
1.凸、凹模材料及热处理 1332
第七篇模具 1332
1.冷冲压零件的经济精度及经济 1333
二、冷冲压零件的经济精度 1333
粗糙度 1333
2.冲压模一般零件材料及热处理 1333
2.冲裁件的精度 1334
3.弯曲件的精度 1336
4.拉延件的精度 1336
一、冲裁工艺 1341
1.冲裁件工艺性 1341
第二章冲裁 1341
2.排样 1344
1.冲裁间隙 1345
2.凸、凹模工作部分尺寸确定 1345
二、冲裁模具参数 1345
3.凸、凹模的其它设计参数 1347
三、冲裁力 1349
1.冲裁力的确定 1349
2.冲裁合力中心的确定 1351
3.冲料退出力 1351
第三章弯曲 1354
一、弯曲工艺 1354
1.弯曲件的工艺性 1354
2.弯曲件毛坯尺寸的确定 1355
3.弯曲工序 1360
二、弯曲模参数 1361
1.弯曲件的回跳角 1361
2.凸、凹模圆角半径的确定 1361
3.凸、凹模的间隙 1367
4.凸、凹模工作部分的尺寸 1367
三、弯曲力 1368
二、拉延旋转体的毛坯尺寸 1369
一、拉延件的工艺性 1369
计算 1369
第四章拉延 1369
三、拉延系数 1377
四、拉延模凸、凹模的间隙 1378
和尺寸 1378
五、拉延力的计算 1383
第一章装配工艺基础 1386
一、装配尺寸链的计算 1386
第八篇装配工艺 1386
二、装配方法的选择 1387
三、编制装配程序 1387
四、装配工作注意事项 1388
五、装配工艺规程的制定 1388
六、钳工机械化修配工具 1391
一、零件的清洗 1394
1.零件的清洗方法 1394
第二章装配工作法 1394
2.常用清洗液配方及应用 1395
1.平衡类型及应用范围 1396
2.静平衡 1396
二、旋转件的平衡 1396
3.动平衡 1398
三、可拆联接装配方法 1400
1.螺纹联接 1400
四、不可拆卸联接装配方法 1402
1.过盈联接 1402
2.键、销联接 1402
2.铆接与焊接 1404
3.粘接 1406
五、校准 1408
六、典型部件的装配 1412
1.滑动轴承的装配工艺要点 1412
2.滚动轴承的装配工艺要点 1413
3.齿轮及蜗轮的装配工艺要点 1415
一般事项 1419
第一章工作地设计和布置的 1419
一、厂房的选择 1419
第九篇工作地设计和布置 1419
二、机械加工车间及装配车 1421
间的区划与布置 1421
1.加工跨与装配跨的布置组合 1422
形式 1422
2.生产工段的布置 1423
3.运输组织与通道设置 1423
三、孔中心距的测量 1424
三、恒温室(车间)的基本 1427
要求 1427
1.恒温室的一般要求 1427
2.恒温室的工艺要求 1427
四、机械加工车间及装配车 1428
间的动力计算 1428
第二章机械加工车间设计 1430
一.机械加工车间的组成与 1430
分类 1430
领 1431
二、机械加工车间的生产纲 1431
三、机械加工车间的机床布 1432
置 1432
1.机床布置的一般原则 1432
2.机床间的最小距离 1435
3.流水线的平面布置 1437
四、机械加工车间机床数量 1438
的确定 1438
的确定 1440
五、机械加工车间工人数量 1440
六、机械加工车间面积的确 1441
定 1441
七、机械加工车间的技术经 1443
济指标 1443
第三章装配车间设计 1444
一、装配车间的组成与分类 1444
1.装配工序的组织形式 1445
送装置 1445
三、装配的组织形式及传 1445
二、装配车间的生产纲领 1445
2.装配流水线的布局形式 1446
3.装配流水线传送装置的选择 1447
四、装配劳动量及工人数量 1450
的确定 1450
1.装配劳动量 1450
2.装配车间工人数量的确定 1451
五、设备台数及作业面积 1452
的确定 1452
1.设备台数 1452
2.工作地(台)数量 1452
3.装配车间面积 1452
六、装配车间的技术经济指 1453
标 1453
式 1454
二、质量管理体系的运转方 1454
念 1454
一、质量管理体系的基本概 1454
第一章质量管理体系 1454
第十篇工艺质量管理 1454
第二章质量数据的处理与 1457
分析方法 1457
一、计量值数据的处理与分 1457
析 1457
析 1459
二、计数值数据的处理与分 1459
第三章相关分析和回归分析 1460
一、相关分析 1460
1.相关图的作法 1460
2.相关系数及其计算方法 1462
二、回归分析 1464
第四章工序能力与机械能力 1465
一、工序能力 1465
二、机械能力 1469
法 1470
一、控制图的种类和制作方 1470
第五章工序质量控制 1470
二、控制图的判断标准和判 1476
断方法 1476
三、控制图的使用程序 1478
四、工序诊断与调节 1478
第六章参数设计与容差设计 1479
一、参数设计 1479
1.稳定性设计 1479
2.动态特性SN比的参数设计 1482
2.容差的确定 1485
二、容差设计 1485
1.质量损失函数 1485
第七章工艺管理技术 1486
一、正交试验法 1486
二、工艺方案的经济分析方 1488
法 1488
1.夹具经济效果分析法 1488
2.工艺方案比较法 1488
三、价值分析法 1489