图书介绍
实用机械加工工艺手册pdf电子书版本下载
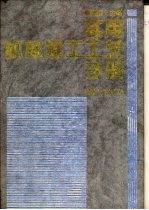
- 陈宏钧主编 著
- 出版社: 北京:机械工业出版社
- ISBN:7111052625
- 出版时间:1997
- 标注页数:1393页
- 文件大小:48MB
- 文件页数:1412页
- 主题词:
PDF下载
下载说明
实用机械加工工艺手册PDF格式电子书版下载
下载的文件为RAR压缩包。需要使用解压软件进行解压得到PDF格式图书。建议使用BT下载工具Free Download Manager进行下载,简称FDM(免费,没有广告,支持多平台)。本站资源全部打包为BT种子。所以需要使用专业的BT下载软件进行下载。如 BitComet qBittorrent uTorrent等BT下载工具。迅雷目前由于本站不是热门资源。不推荐使用!后期资源热门了。安装了迅雷也可以迅雷进行下载!
(文件页数 要大于 标注页数,上中下等多册电子书除外)
注意:本站所有压缩包均有解压码: 点击下载压缩包解压工具
图书目录
前言 1
第1章 机械加工工艺规程的制订 1
第1节 机械制造工艺基本术语 1
第2节 机械加工工艺规程的编制 3
l 机械加工工艺规程的作用 3
2 机械加工工艺规程的制订程序 4
3 零件图样的工艺审查 4
3.l 各种加工类型对零件结构工艺性的要求 4
3.2 零件结构的切削加工工艺性 5
4 工艺过程设计 18
4.1 定位基准的选择与定位夹紧符号 18
4.2 零件表面加工方法的选择 27
4.3 加工顺序的安排 27
5 工序设计 28
5.1 机床的选择 28
5.2 工艺装备的选择 28
6.1 工艺工作程序 29
6 工艺工作程序及工艺文件 29
5.3 时间定额的确定 29
6.2 工艺文件 30
第3节 工艺尺寸链 35
1 尺寸链的计算参数与计算公式 35
1.1 计算参数 35
1.2 计算公式 35
2 工艺尺寸链的基本类型 37
2.1 工艺尺寸换算 37
2.3 其他工艺尺寸的计算 39
2.2 同一表面需要经过多次加工时工序尺寸的计算 39
3 计算机辅助求解工序尺寸 43
3.1 计算机跟踪寻找尺寸链 43
3.2 计算机解算尺寸链的过程 46
第4节 典型零件加工工艺过程 49
1 主轴的机械加工工艺过程 49
2 曲轴的机械加工工艺过程 55
3 连杄的机械加工工艺过程 57
4 箱体的机械加工工艺过程 62
5 套类零件的机械加工工艺过程 63
6 齿轮的机械加工工艺过程 64
第1节 钢 66
1 钢牌号表示方法 66
1.1钢的名称及其代号 66
第2章 材料及热处理 67
1.2常用钢牌号表示方法 67
2.1碳素结构钢 68
2 常用钢材的牌号力学性能及用途 68
2.2优质碳素结构钢 70
2.3低合金结构钢 72
2.4合金结构钢 74
2.5易切削钢 80
2.6弹簧钢 81
2.7常用轴承钢的特点及用途 82
2.8不锈钢的特性及用途 84
2.9耐热钢的特性及用途 86
2.10 碳素工具钢 87
2.11 合金工具钢 89
2.12 高速工具钢 92
3 型材 93
3.1 热轧圆钢和方钢尺寸 93
3.2 热轧六角钢和八角钢的尺寸 94
3.3 热轧扁钢的尺寸规格 94
3.4 热轧角钢的尺寸规格 94
3.5 热轧普通工字钢的尺寸规格 103
3.6 热轧普通槽钢 104
3.7 冷拉圆钢尺寸规格 106
3.8 冷拉方钢尺寸规格 106
3.9 冷拉六角钢尺寸规格 106
3.10 不锈钢冷加工钢棒 107
3.11 热轧钢板尺寸规格 107
3.12 冷轧钢板和钢带尺寸规格 109
3.13 无缝钢管的尺寸 110
4 钢材的涂色标记 111
3.14 不锈钢无缝钢管 111
第2节 铸铁 113
1 铸铁牌号表示方法 113
2 灰铸铁 113
2.1 灰铸铁的力学性能 113
2.2 灰铸铁铸件的应用范围 114
3 球墨铸铁的力学性能及应用范围 115
4 可锻铸铁的力学性能及应用范围 115
5 特种铸铁 116
5.1 常用耐蚀铸铁的力学性能与应用 116
5.2 常用耐热铸铁的力学性能与应用 117
5.3 普通白口铸铁的成分、性能与应用 117
5.4 合金白口铸铁的性能与应用 119
5.5 冷硬铸铁的成分、性能与用途 119
5.6 高铬铸铁的成分、性能与用途 120
第3节 铸钢 120
1 铸钢牌号表示方法 120
3 合金铸钢的力学性能及应用 121
2 一般工程用铸钢的力学性能及应用 121
4 铸造高锰钢力学性能及应用 123
5 耐热铸钢的牌号、化学成分及应用 123
6 不锈耐酸钢铸件的力学性能及应用 124
第4节 有色金属及其合金 127
1 有色金属及其合金产品代号表示方法 127
2 铜及其合金 128
2.1 变形铜及铜合金的主要特点与用途 128
2.2 变形铜合金力学性能与物理性能 132
2.3 铜及其合金工艺性能与耐蚀性数据 134
2.4 铸造铜合金主要特点与用途 136
2.5 铸造铜合金力学性能与物理性能 138
3 铝及其合金 140
3.1 变形铝合金主要特点与用途 140
3.2 铝及其合金热处理工艺参数 142
3.3 铸造铝合金主要特点和用途 142
3.4 铸造铝合金热处理工艺参数 143
2 减摩零件用粉末冶金材料 145
第5节 粉末冶金材料 145
l 粉末冶金材料的应用范围 145
3 摩擦零件用粉末冶金材料的性能 146
4 粉末冶金铁基结构材料 147
5 作过滤用粉末冶金材料的性能与应用 148
第6节 非金属材料 148
1 常用工程塑料的性能特点及应用 148
2 生胶的类型、特性及其用途 151
第7节 热处理 153
1 一般热处理 153
1.1 一般热处理的工艺特点与应用 153
1.2 常用结构钢的完全退火与硬度值 155
1.3 常用工具钢、轴承钢退火和球化温度与硬度值 155
1.4 常用钢材的正火温度与硬度值 156
1.5 常用钢材淬火温度与硬度值 157
1.6 常用钢材淬火后不同硬度的回火温度 158
1.8 球墨铸铁的热处理规范 160
1.7 消除焊接与加工应力的低温退火 160
2 化学热处理的工艺特点与应用 161
3 表面热处理的工艺特点与应用 162
4 热处理与前、后工序的相关要求 163
5 影响工件热处理变形的主要原因,表现形式和解决方法 163
第3章 毛坯及余量 165
第1节 毛坯及加工余量的计算 165
1 基本术语 165
2.2 选择毛坯应考虑的因素 166
2 毛坯的类型及选择 166
2.1 各类毛坯的特点及应用范围 166
3 加工余量的确定 167
3.1 影响加工余量的因素 167
3.2 最大余量、最小余量及余量公差的计算 168
3 用分析计算法确定最小余量 169
4 工序尺寸、毛坯尺寸及总余量的计算 169
1.1.2 铸件尺寸公差等级 170
1.1.1 铸件的尺寸公差 170
第2节 毛坯机械加工余量 170
1.1 铸件的尺寸公差及公差等级 170
1 铸件 170
1.2 铸件机械加工余量 171
1.3 铸件结构单元的工艺尺寸 174
1.3.1 铸造孔的最小尺寸 174
1.3.2 铸造壁的最小厚度 175
1.3.3 铸造壁(或肋)间的最小距离 175
1.3.4 起模斜度 175
1.3.5 圆角半径 177
1.4 铸造工艺余量 177
2 锻件 178
2.1 自由锻件机械加工余量及公差 178
2.1.1 台阶轴类 178
2.1.2 圆盘类 179
2.1.3 带孔圆盘类 179
2.1.6 光轴类 182
2.1.5 圆环类 182
2.1.4 套筒类 182
2.1.7 黑皮锻件 187
2.2 胎模锻件机械加工余量及公差 188
2.2.1 型摔成形类 188
2.2.2 套模、垫模成形类 188
2.2.3 合模成形类 188
2.3.2 确定锻件公差及机械加工余量的主要因素 190
2.3.3 公差 191
2.3.l 公差及机械加工余量等级 196
2.3 钢质模锻件的公差及机械加工余量 196
2.3.4 机械加工余量 201
2.4 径向锻机上钢质轴类锻件公差及机械加工余量 203
3 冲压件 204
3.1 冲压件的结构要素 204
3.2 冷冲压件的公差 207
3.2.1 金属冷冲压件的公差 207
3.2.2 冲压剪切下料件公差 210
4 钢质冷挤压件公差 212
5 热切割件 213
5.1 气割质量和尺寸偏差 213
5.2 等离子弧切割质量和尺寸偏差 213
第3节 工序间加工余量 215
1 装夹及下料尺寸余量 215
2 轴的加工余量 226
2.1 外圆柱表面加工余量及偏差 226
2.2 轴端面加工余量及偏差 229
2.3 槽的加工余量及公差 230
3 内孔加工余量及偏差 231
4 平面加工余量及偏差 238
5 切除渗碳层的加工余量 240
6 有色金属及其合金的加工余量 241
7 齿轮和花键精加工余量 245
1.2 影响形状精度的因素及消除方法 247
1.1 影响尺寸精度的因素及消除方法 247
1 影响加工精度的因素及消除方法 247
第1节 机械加工精度 247
第4章 机械加工质量 247
1.3 影响位置精度的因素及消除方法 249
2 加工误差 249
2.2 加工误差的计算 250
第2节 机械加工的经济精度 257
1 加工路线与所能达到的加工精度和表面粗糙度 257
2 各种加工方法能达到的尺寸经济精度 259
3 各种加工方法能达到的形状经济精度 263
4 各种加工方法能达到的位置经济精度 264
第3节 机械加工表面质量与振动 266
1 影响加工表面粗糙度的因素及改善措施 266
1.1 影响切削加工表面粗糙度的因素及改善措施 266
1.2 影响磨削表面粗糙度的因素及改善措施 267
2 各种加工方法能达到的表面粗糙度 268
3 表面粗糙度与加工精度和配合之间的关系 269
5.1 加工硬化 271
4 各种联接表面的粗糙度 271
5 加工硬化与残余应力 271
5.2 残余应力 273
6 切削过程中的振动 273
第5章 技术测量 276
第1节 测量与测量误差 276
1 测量常用术语 276
2 测量方法的分类 276
3 测量误差的分类、产生原因及消除方法 276
第2节 常用计量器具 277
1 游标类量具 277
2 螺旋测微量具 277
3 机械式测微仪 281
4 角度量具 283
5 量块、量规 288
1.3 V形槽宽度、角度计算 293
1.2 内圆弧与外圆弧计算 293
1 常用测量计算举例 293
1.1 圆的弓形尺寸系数表 293
1.4 燕尾与燕尾槽宽度计算 297
1.5 内圆锥与外圆锥计算 297
2 形位误差的检测 298
2.1 形位误差的检测原则 298
2.2 直线度误差的常用测量方法 299
2.3 平面度误差的常用测量方法 300
2.5 轮廓度误差的常用测量方法 301
2.4 圆度误差的常用测量方法 301
2.6 定向误差的常用测量方法 302
2.7 定位误差的常用测量方法 305
2.8 跳动量的常用测量方法 307
3 表面粗糙度的检测 309
3.1 表面粗糙度的测量方法、特点及应用 309
3.2 表面粗糙度标准样块 309
3.3 机械加工表面粗糙度样块 310
4.1 螺纹量规的名称、代号、功能、特征及使用规则 311
4 螺纹的检测 311
4.2 螺纹单项测量方法及测量误差 312
4.3 用量针法测量螺纹中径 313
5 齿轮检测 314
5.1 公法线长度的测量 314
5.1.1 标准直齿圆柱齿轮公法线长度测量 315
5.1.2 斜齿圆柱齿轮公法线长度测量 317
5.1.3 公法线平均长度偏差及公差 319
5.2 分度圆弦齿厚的测量 322
5.3 固定弦齿厚的测量 323
5.4 齿厚上偏差及公差 324
5.5 内齿轮齿厚测量 326
1.1.1 型号表示方法 328
1.1.4 机床的组、系代号及主参数 328
1.1.3 机床的特性代号 328
1.1.2 机床的分类及类代号 328
1.1 通用机床型号表示方法 328
1 金属切削机床型号编制方法 328
第1节 金属切削机床 328
第6章 金属切削机床及附件 328
1.3 机床自动线的型号 329
1.2 专用机床的型号 329
1.1.10 金属切削机床统一名称和类、组、系划分 329
1.1.9 企业代号及其表示方法 329
1.1.8 其他特性代号及其表示方法 329
1.1.7 机床的重大改进顺序号 329
1.1.6 主轴数和第二主参数的表示方法 329
1.1.5 通用机床的设计顺序号 329
2 常用通用机床技术参数与联系尺寸 336
2.1 车床 336
2.1.1 立式车床 336
2.1.2 落地及卧式车床 337
2.1.3 回轮、转塔车床 346
2.1.4 曲轴车床 349
2.1.5 仿形车床 350
2.1.6 数控车床 353
2.2 铣床 355
2.2.1 龙门铣床 355
2.2.2 立式铣床 356
2.2.3 卧式铣床 359
2.2.4 万能工具铣床 362
2.3 钻床 363
2.3.1 摇臂钻床 363
2.2.5 数控铣床 363
2.3.2 台式钻床 366
2.3.3 立式钻床 366
2.4 镗床 368
2.4.1 坐标镗床 368
2.4.2 卧式镗床 368
2.4.3 金刚镗床 370
2.4.4 数控镗床 371
2.5.1 刨床 372
2.5 刨插床 372
2.5.2 插床 374
2.6 拉床 375
2.7 锯床 376
2.8 磨床 376
2.8.1 外圆磨床 376
2.8.2 内圆磨床 379
2.8.3 平面磨床 380
2.8.4 万能工具磨床 381
2.8.5 曲轴磨床 382
2.9 螺纹加工机床 382
2.10 齿轮加工机床 383
2.10.1 滚齿机 383
2.10.2 插齿机 385
2.10.3 剃齿机 386
2.10.7 弧齿锥齿轮铣齿机 387
2.10.6 直齿锥齿轮铣齿机 387
2.10.5 齿轮磨床 387
2.10.4 珩齿机 387
2.10.8 直齿锥齿轮刨齿机 388
2.10.9花键轴铣床 389
第2节 机床附件 390
1 分度头 390
1.1 机械分度头 390
1.2 等分分度头 390
1.3 数控分度头 391
2 卡盘与过渡盘 392
2.1 三爪自定心卡盘 392
2.2 四爪单动卡盘 392
2.3 楔式动力卡盘 392
2.4 卡盘用过渡盘 398
3 花盘及拨盘 400
3.1 花盘 400
3.2 拨盘 401
4.1 固定顶尖 403
4 顶尖及顶尖套 403
4.2 回转顶尖 405
4.3 拨动顶尖 406
4.4 锥孔顶尖 407
4.5 顶尖套 408
5 夹头 409
5.1 扳手式钻夹头 409
5.2 自紧式钻夹头 410
5.3 攻丝、丝锥夹头 411
5.4 快换夹头 412
5.5 弹簧夹头 413
5.6 铣夹头 414
5.7 鸡心夹头 415
6 机床用平口虎钳 416
7 常用回转工作台 418
8 吸盘 422
9 铣头、插头与镗头 424
1.1 常见各种牌号硬质合金的选用 427
1 硬质合金的选用 427
第7章 刃具 427
第1节 硬质合金刀片 427
1.2 几种新牌号硬质合金的性能及应用 428
2 硬质合金焊接刀片 430
2.l 常用焊接车刀刀片 436
2.2 基本型硬质合金焊接刀片 436
3 可转位硬质合金刀片 436
3.1 可转位硬质合金刀片的标记方法 436
3.2 带圆孔的可转位硬质合金刀片 439
3.3 无孔可转位硬质合金刀片 456
3.4 沉孔可转位硬质台金刀片 458
3.5 硬质合金可转位铣刀片 465
3.5.1 刀片型号表示方法 465
3.5.2 可转位铣刀刀片 465
3.6 可转位陶瓷刀片的型号与基本参数 469
1 可转位车刀型号表示规则 472
第2节 可转位车刀 472
2 可转位车刀型式 473
第3节 铣刀 486
1 立铣刀 486
2 键槽铣刀 489
3 T形槽铣刀 489
4 半圆键槽铣刀 489
5 直柄燕尾槽铣刀和直柄反燕尾槽铣刀 489
6 槽铣刀 496
7 锯片铣刀 498
8 三面刃铣刀 506
9 圆柱形铣刀 513
10 铲背成形铣刀 515
11 角度铣刀 518
第4节 孔加工刀具 522
1 钻头 522
2 铰刀 548
l 丝锥 565
第5节 螺纹刀具 565
2 板牙 575
3 螺纹滚轮 581
4 螺纹模板 584
1 盘形齿轮铣刀 586
2 盘形锥齿轮铣刀 587
3 齿轮滚刀 588
4 镶片齿轮滚刀 588
5 小模数齿轮滚刀 590
6 直齿插齿刀 590
7 30度压力角渐开线花键滚刀 596
8 45度压力角渐开线花键滚刀 596
第7节 拉刀 597
1 宽刀体键槽拉刀 597
2 平刀体键槽拉刀 599
1 普通磨料 602
第8节 磨具 602
2 硬度等级及其代号 604
3 以磨粒率表示的磨具组织及其适用范围 604
4 结合剂代号、性能及其适用范围 604
5 砂轮的标志方法示例 605
6 普通磨具 605
7 普通磨具最高工作线速度 621
1 夹具常用资料的选择 623
1.1 夹具零件常用材料及热处理 623
第l节 夹具设计基础资料 623
第8章 机床夹具 623
1.2 夹具常用公差与配合的选择 624
1.3 表面粗糙度在夹具零部件中的应用 625
1.4 夹具设计中所用的基本角度和圆锥度 627
2 夹具设计常用计算 629
2.1 夹具定位尺寸的计算 629
2.2 夹具定位精度的计算 633
2.3 常见典型夹紧形式所需夹紧力的计算 639
1.1 定位件 643
第2节 夹具零部件通用标准 643
1.2 支承件 653
1.3 夹紧件 660
1.4 导向件 679
1.5 对刀件 685
1.6 操作件 686
2.1 执行元件 687
2.1.1 QGB系列气缸 687
2 气动元件 687
2.1.2 LCZ系列气缸 690
2.1.3 QGv系列膜片气缸 693
2.1.4 双活塞回转气缸 693
2.2 控制元件 694
2.2.1 减压阀 694
2.2.2 单向节流阀 695
2.2.3 单向阀(A系列) 695
2.2.5 二位四通手拉阀 696
2.2.4 二位四通转阀(SF24—d) 696
2.2.6 脚踏气阀 697
2.3 辅助元件 697
2.3.1 空气过滤器 697
2.3.2 油雾器 698
2.3.3 消声器 699
第3节 夹具典型机构 699
1 可调支承 699
2 夹紧机构 700
2.1 斜楔夹紧机构 700
2.2 螺旋夹紧机构 701
2.3 偏心夹紧机构 703
2.4 铰链夹紧机构 704
2.5 联动夹紧机构 706
2.6 定心夹紧机构 707
3 分度装置 707
1.1 定位要则 711
1 机床夹具设计通用要则 711
第4节 机床夹具的设计要点及典型结构 711
1.2 夹紧要则 716
1.3 结构设计要则 721
2 车床夹具 722
2.1 设计要点 722
2.2 车床夹具典型技术要求 724
2.3 车床夹具典型结构 727
2.3.1 顶尖类 727
2.3.2 心轴类 727
2.3.3 拨盘类 727
2.3.4 卡盘类 730
2.3.5 其他车床夹具 732
3 钻床夹具 733
3.1 设计要点 733
3.2 钻(镗)床夹具典型技术要求 736
3.3.1 自定心钻夹具 740
3.3.2 分度转台 740
3.3 钻床夹具典型结构 740
3.3.3 钻模 742
4 镗床夹具 748
4.1 镗床夹具设计要点 748
4.2 镗床夹具典型结构 752
5 铣床夹具 752
5.1 铣床夹具设计要点 752
5.2 铣床夹具典型技术要求 756
5.3.1 铣床通用夹具 760
5.3 铣床夹具典型结构 760
5.3.2 铣床专用夹具 764
6 磨床夹具 764
第5节 可调夹具与组合夹具 766
1 可调夹具 766
1.1 可调整夹具的特点、适用范围与设计要点 766
1.2 可调整夹具结构示例 768
2 组合夹具 768
2.1 组合夹具的使用范围与经济效果 768
2.2 组合夹具的系列、元件类别及作用 769
2.3 组合夹具结构示例 770
第9章 切削加工 771
第1节 车削加工 771
1 车床加工范围及装夹方法 771
1.1 卧式车床加工 771
1.1.1 卧式车床加工范围 771
1.1.2 卧式车床常用装夹方法 772
1.2 立式车床加工 774
1.2.1 立式车床加工范围 774
1.2.2 立式车床常用装夹方法 775
2 车削圆锥面 775
2.1 锥体各部尺寸计算公式 775
2.2 车削圆锥面的方法 776
2.3 车削标准锥度和常用锥度时小刀架和靠模板转动角度 777
3 车削偏心工件的装夹方法 777
4 成形面车削方法 779
5 滚压加工 781
6 车削细长轴 783
6.1 车削细长轴的装夹方法 783
6.2 车削细长轴常用切削用量 784
6.3 车削细长轴车刀几何参数及特点 785
6.4 车削细长轴常见工件缺陷和产生原因 786
7 车削球面 787
9 卧式车床加工常见问题的产生原因及解决方法 789
8.2 统制圆柱形螺旋弹簧用心轴直径的计算 789
8.l 卧式车床可绕制弹簧的种类 789
8 冷绕弹簧 789
10 车刀切削部分的几何形状及应用 790
10.1 前刀面形状的选择 790
1o.2 前角及后角的选择 791
10.3 主偏角、副偏角、刃倾角的选挥 791
10.4 刀尖圆弧半径、过渡刃尺寸、倒棱前角及倒棱宽度的选择 792
10.5 卷屑槽尺寸 792
12 车削用量的选择 793
12.1 车削速度的计算公式 793
11 车刀的磨钝标准及寿命 793
12.2 硬质合金及高速钢车刀粗车外圆和端面的进给量 795
12.3 硬质合金外圆车刀半精车的进给量 796
12.4 硬质合金及高速铜镗刀粗镗孔进给量 796
12.5 切断及切槽进给量 798
12.6 成形车削时的进给量 798
12.7 用YTl5硬质合金车刀车削碳钢、铬钢、镍铬锥及铸钢时的切削速度 798
12.8 用YG6硬质合金车刀车削灰铸铁时的切削速度 798
12.9 涂层硬质合金车刀的切削用量 798
12.10 陶瓷车刀的切削用量 800
12.11 立方氮化硼车刀的切削用量 802
12.12 金刚石车刀的切削用量 802
第2节 铣削加工 804
1 铣削方式、铣削范围和基本方法 804
1.1 铣削方式 804
1.2 铣削范围和基本方法 805
2.1 分度头传动系统及分度头定数 807
2 分度头 807
2.2 分度方法及计算 808
2.2.1 单式分度法计算及分度表 808
2.2.2 差动分度法计算及分度表 809
2.2.3 近似分度法计算及分度表 810
2.2.4 角度分度法计算及分度表 812
3 铣削离合器 812
3.1 齿式离合器的种类及特点 812
3.3 分度扳角 814
3.2 商合器的铣削及计算 814
4 铣削凸轮 816
4.l 凸轮传动的三要素 816
4.2 等速圆盘凸轮的铣削 816
4.3 等速圆柱凸轮的铣削 817
5 铣削球面方法 818
6 铣刀、铰刀的开齿 819
6.1 前角γa=○o的铣刀开齿 819
6.2 前角γa>Oo的铣刀开齿 820
6.3 圆柱螺旋齿铣刀的开齿 821
6.5 锥面齿的铣削 822
6.4 端面齿的铣削 822
6.6 麻花钻头槽的铣削 823
6.7 铰刀的开齿 823
7 铣削加工常见问题产生原因及解决方法 824
8 铣刀切削部分的几何形状和角度选择 826
9 铣刀磨钝标准及耐用度 829
10 铣削用量的选择 830
10.1 铣削切削速度的计算公式 830
10.2 高速钢端铣刀、圆柱铣刀和盘铣刀加工时的进给量 832
10.3 高速钢立铣刀、角铣刀、半圆铣刀、切槽铣刀和切断铣刀铣削钢的进给量 833
10.4 硬质合金端铣刀、圆柱形铣刀和圆盘铣刀铣削平面和凸台的进给量 834
10.5 硬质合金立铣刀铣削平面和凸台的进给量 835
10.6 涂层硬质合金铣刀的铣削用量 835
第3节 刨削、插削加工 835
1 刨削 835
1.1 牛头刨床常见加工方法 835
1.2 龙门刨床常用加工方法 837
1.3 刨削常用装夹方法 839
1.4 槽类工件的刨削与切断 840
1.5 镶条的刨削 842
1.6 精刨 843
1.6.l 精刨的类型及特点 843
1.6.2 精刨刀常用的研磨方法 845
1.7 刨削常见问题产生原因及解决方法 845
1.7.1 刨平面常见问题产生原因及解决方法 845
1.7.2 刨垂直面和阶台常见问题产生原因及解决方法 846
1.7.3 切断、刨直槽及T形槽常见问题产生原因及解决方法 847
1.7.4 刨斜面、v形槽及镶条常见问题产原因及解决方法 848
1.7.5 精刨表面常见问题产生原因及解决方法 848
1.8 常用刨刀种类及用途 848
1.9 刨刀切削角度的选择 850
1.10 常用刨削用 850
2 插削 851
2.1 常用装夹和加工方法 851
2.2 常用插刀类型及主要几何角度 854
2.3 插平面及插槽的进给量 855
第4节 钻削、扩削、铰削加工 856
1 钻、扩、饺加工方法 856
1.1 不同孔距精度所用的加工方法 856
1.2 切削液的选择 857
1.3 特殊孔的钻削方法 857
1.4 深孔的钻削 858
1.4.1 深孔钻削的适用范围与加工精度、表面粗糙度 858
1.4.2 常用深孔刀具的特点及用途 859
2 麻花钻、群钻、铰刀的几何参数 861
2.1 通用型麻花钻的主要几何参数 861
2.2 常用群钻的几何参数 862
2.2.1 标准群钻切削部分几何参数 862
2.2.2 铸铁群钻切削部分几何参数 863
2.2.3 紫铜群钻切削部分几何参数 864
2.2.4 黄铜群钻切削部分几何参数 865
2.2.6 毛坯扩孔群钻切削部分几何参数 866
2.2.5 薄板群钻切削部分几何参数 866
2.3 铰刀的主要几何参数 867
3 钻头、扩孔钻和铰刀的磨钝标准及耐用度 868
4 常用钻削、扩削、铰削用量 868
4.l 高速钢钻头钻削不同材料的切削用量 868
4.2 硬质合金钻头钻削不同材料的切削用量 870
4.3 硬质合金可转位钻头钻孔的切削用量 871
4.5 群钻加工铸铁时的切削用量 872
4.4 群钻加工钢时的切削用量 872
4.6 高速钢及硬质合金锪钻加工的切削用量 873
4.7 高速钢饺刀加工不同材料的切削用量 873
4.8 硬质合金铰刀铰孔的切削用量 874
5 钻削、扩削、铰削加工中常见问题产生原因和解决方法 875
5.1 麻花钻钻孔中常见问题产生原因和解决方法 875
5.2 内排屑深孔钻钻孔中常见问题产生原因和解决方法 876
5.3 扩孔钻扩孔中常见问题产生原因和解决方法 877
5.4 多刃饺刀铰孔中常见问题产生原因和解决方法 878
1 卧式镗床基本工作范围 880
第5节 镗削加工 880
2 镗刀 881
2.1 单刃镗刀的装夹方式及用途 881
2.2 双刃镗刀的装夹方式及用途 881
2.3 微调镗刀的结构形式与安装 882
2.4 组合镗刀头结构形式及刀片安装位置 883
2.5 复合镗刀的形式及应用 884
2.6 单刃镗刀 886
2.7 整体式镗刀块 888
2.8 微调镗刀规格系列 889
2.9 镗床用攻丝夹头 890
3 刀杆、镗杆 890
3.1 刀杆 890
3.2 镗杆 891
4 卧式镗床定位方式及特点 893
5 工艺基准面校正方法 895
6 卧式镗床常用测量方法及精度 896
8.2 找正工具与找正方法 897
8.1 坐标换算与加工调整 897
8.3 坐标测量 897
7.1 金刚镗床的加工精度 897
8 坐标镗床加工 897
7.2 硬质合金金刚镗镗刀几何参数的选择 897
7 金刚镗床加工 897
9 镗削用量 903
9.1 卧式镗床的镗削用量与加工精度 903
9.2 金刚镗床的镗削用量 904
9.3 坐标镗床的镗削用量与加工精度 904
10 影响镗削加工质量的因素与解决方法 905
10.1 卧式镗床加工中常见的质量问题与解决方法 905
10.2 影响孔距加工精度的因素与解决方法 905
第6节 拉削加工 908
1 拉削方式及加工特点 908
2 拉削装置及辅具 908
2.2.2 外拉刀用拉削辅具 912
2.2.1 内拉刀用拉削辅具 912
2.2 拉削辅具 912
2.1 拉削装置 912
3 拉削余量的选择 918
4 拉刀几何角度的选择 918
5 常用拉削切削液 919
6 拉削速度的选用 919
7 拉削中常见缺陷产生原因与解决方法 919
第10章 磨削加工 923
第1节 磨削加工基础 923
1 常见的磨削方式 923
2 砂轮平衡与修整 924
2.1 砂轮安装与静平衡 924
2.2 砂轮修整的方法 925
3 常用磨削液的名称及性能 925
第2节 普通磨削 929
1 外圆磨削 929
1.1 外圆磨削常用方法 929
1.2 外圆磨削余量的合理选择 931
1.3 外圆磨削切削用理的选择 932
1.3.1 外圆磨削砂轮速度 932
1.3.2 纵进给粗磨外圆磨削用量 932
1.3.3 纵进给精磨外圆磨削用量 933
1.4 外圆磨削常见的工件缺陷、产生原因及解决方法 934
2 内圆磨削 935
2.1 内圆磨削常用方法 935
2.2 内圆磨削余量的合理选择 937
2.3 内圆磨削切削用量的选择 938
2.3.1 内圆磨削砂轮速度选择 938
2.3.2 粗磨内圆磨削用量 938
2.3.3 精磨内圆磨削用量 940
2.4 内圆磨削常见的工件缺陷、产生原因及解决方法 942
3 平面磨削 942
3.1 平面磨削常用方法 942
3.3 平面磨削切削用量的选择 946
3.3.1 平面磨削砂轮速度选择 946
3.2 平面磨削余量的合理选择 946
3.3.2 往复式平面磨粗磨平面磨削用量 947
3.3.3 往复式平面磨精磨平面磨削用量 947
3.3.4 回转式平面磨粗磨平面磨削用量 948
3.3.5 回转式平面磨精磨平面磨削用量 949
3.4 平面磨削常见的工件缺陷、产生原因及解决方法 950
4 无心磨削 950
4.1 无心外圆磨削常用方法 950
4.2 无心外圆磨削切削用量的选择 952
4.2.1 无心外圆磨粗磨磨削用量 952
4.2.2 无心外圆磨精磨磨削用量 952
4.3 无心外圆磨削常见的工件缺陷、产生原因及解决方法 953
4.3.l 无心外圆磨削常见的工件表面形状缺陷、产生原因及解决方法 953
4.3.2 无心外圆磨削常见工件表面外观缺陷、产生原因 954
1.1 高速磨削的特点 956
1.2 高速磨削对机床的要求 956
第3节 高效与低粗糙度磨削 956
1 高速磨削 956
1.3 高速磨削对砂轮的要求 957
1.4 高速外圆磨削钢材的磨削用量 957
2 宽砂轮磨削 957
2.1 宽砂轮磨削的特点 957
2.2 宽砂轮磨削对机床的要求 957
2.3 宽砂轮磨削砂轮的选择 957
2.4 宽砂轮磨削工艺参数的选择 957
3.1 低粗糙度磨削分类 958
3 低粗糙度磨削 958
3.2 低粗糙度磨削砂轮的选择 959
3.3 低粗糙度磨削对机床的要求 959
3.4 各种磨削方式低粗糙度磨削工艺参数 959
3.4.1 外圆低粗糙度磨削工艺参数 959
3.4.2 内圆低粗糙度磨削工艺参数 960
3.4.3 平面低粗糙度磨削工艺参数 960
1.1.1 常用珩磨头结构形式 961
1.1 珩磨头 961
1 珩磨 961
第4节 光整加工 961
1.1.2 常用珩磨头的联接杆 962
1.2.1 珩磨加工常用夹具结构形式 963
1.2.2 珩磨加工中的“对中” 965
1.3 珩磨油石的选择 965
1.4 珩磨工艺参数的选择 967
1.5 珩磨加工常见缺陷产生原因及解决方法 967
2 研磨 972
2.1 研磨的分类和适用范围 972
2.2 研具 972
2.3 研磨剂 975
2.4 研磨膏 976
2.5 研磨工艺参数选择 977
3 抛光 979
3.2 磨料和抛光剂 980
1 刀具刃磨的砂轮选择 981
第5节 刀具刃磨 981
2 砂轮和支片安装位置的确定 982
3 刀具刃磨实例 983
1.2 普通螺纹代号与标记 988
1.5 普通螺纹公差 988
1.3 普通螺纹直径与螺距系列 988
1.4 普通螺纹基本尺寸 988
1.1 普通螺纹基本牙型及尺寸计算 988
1 普通螺纹 988
第1节 螺纹基本尺寸及公差 988
2 英制螺纹 1023
2.1 英制螺纹基本牙型及尺寸计算 1023
2.2 英制螺纹基本尺寸 1023
2.3 英制螺纹公差 1024
3 梯形螺纹 1024
3.1 梯形螺纹牙型 1024
3.2 梯形螺纹代号和标记 1025
3.3 梯形螺纹直径与螺距系列 1025
3.4 梯形螺纹的基本尺寸 1026
3.5 梯形螺纹公差 1030
4 锯齿形螺纹 1036
4.1 基本牙型 1036
4.2 锯齿形(3°、30°)螺纹直径与基本尺寸 1037
4.3 锯齿形(3°、30°)螺纹公差 1038
4.4 锯齿形螺纹标记 1041
5 管螺纹 1041
5.1 用螺纹密封的管螺纹 1041
5.1.1 圆锥外螺纹基本牙型及尺寸计算 1041
5.1.2 圆柱内螺纹基本牙型及尺寸计算 1041
5.1.3 螺纹基本尺寸 1042
5.1.4 螺纹公差 1042
5.2 非螺纹密封的管螺纹 1043
5.2.1 基本牙型与尺寸计算 1043
5.2.2 基本尺寸及公差 1043
5.4 米制锥螺纹 1045
5.3 60度圆锥管螺纹 1045
6 螺纹新、旧国标对照 1046
6.1 新、旧国标螺纹名称及代号时照 1046
6.2 新、旧国标螺纹公差等级对照 1046
6.3 新、旧国标螺纹公差带位置的比较 1047
第2节 螺纹加工 1047
1 车螺纹 1047
1.1 车螺纹的刀尖宽度尺寸 1047
1.2.1 用无进给箱车床车螺纹 1048
1.2 车螺纹时的交换齿轮计算 1048
1.2.2 有进给箱车床的交换齿轮计算 1050
1.3 螺纹车削方法 1051
1.4 螺纹车刀、切削用量及切削液 1052
1.4.1 常用螺纹车刀的特点与应用 1052
1.4.2 高速钢及硬质合金车刀车削不同材料的切削用量 1056
1.4.3 高速钢车刀车削螺纹时常用切削液 1057
1.5 车削螺纹常见问题产生原因与解决方法 1058
2.3 旋风铣削螺纹常用切削用量 1059
2.2 旋风铣削螺纹的刀具材料和几何角度 1059
2 旋风铣削螺纹 1059
2.1 旋风铣削螺纹方式及适用范围 1059
3 攻螺纹 1061
3.1 普通螺纹丝锥的选择 1061
3.2 攻螺纹常用辅具 1061
3.3 攻螺纹前底孔直径的确定 1062
3.3.1 普通螺纹攻螺纹前底孔的钻头直径 1062
3.3.2 非螺纹密封的管螺纹攻螺纹前钻底孔的钻头直径 1062
3.3.3 英制锥管螺纹和英制锥螺纹攻螺纹前钻底孔的钻头直径 1062
3.4 攻螺纹切削液选择 1063
3.5 机用丝锥攻螺纹中常见问题产生原因与解决方法 1063
4 挤压丝锥挤压螺纹 1064
4.1 挤压丝锥的种类及使用范围 1064
4.2 挤压螺纹前螺纹底孔尺寸 1064
5.1 板牙种类和使用范围 1065
5.2 圆板牙的几何参数 1065
4.3 挤压螺纹切削速度的选择 1065
5 板牙套螺纹 1065
5.3 板牙架型式和尺寸 1066
5.4 套螺纹切削液的选择 1066
5.5 板牙套螺纹前螺杆直径的确定 1066
第3节 渐开线齿轮基本尺寸及精度 1067
1 齿轮基本齿廓 1067
2 齿轮模数系列 1067
3.2 内齿轮几何计算 1068
3.3 斜齿圆柱齿轮几何计算 1068
3.l 直齿圆柱齿轮几何计算 1068
3 圆柱齿轮 1068
3.4 齿条几何计算 1070
3.5 变位直齿圆柱齿轮 1070
3.5.1 高变位直齿圆柱齿轮几何计算 1070
3.5.2 角变位直齿圆柱齿轮几何计算 1070
3.6 齿轮精度 1071
3.6.l 齿轮和齿轮副误差及侧隙的定义和代号 1071
3.6.2 齿轮的公差组 1077
3.6.4 齿轮公差值 1078
3.6.3 新旧标准的误差及偏差名称和代号对照 1078
4 锥齿轮 1081
4.1 直齿锥齿轮几何尺寸计算 1081
4.2 锥齿轮精度 1083
4.2.l 锥齿轮、锥齿轮副的误差与侧隙 1083
4.2.2 锥齿轮及锥齿轮副公差 1088
5 蜗杆和蜗轮 1100
5.1 圆柱蜗杆和蜗轮常用计算 1100
5.2.1 蜗杆、蜗轮及其传动的误差和侧隙 1102
5.2 圆柱蜗杆、蜗轮精度 1102
5.2.2 蜗杆、蜗轮及传动的公差 1106
第4节 齿轮加工 1113
1 成形法铣削齿轮 1113
1.1 铣直齿圆柱齿轮 1117
1.2 铣直齿条的移距方法 1117
1.3 铣斜齿圆柱齿轮 1118
1.4 铣直齿锥齿轮 1119
3.1 滚齿机传动系统 1120
3 滚齿 1120
3.2 常用滚齿机联接尺寸 1120
2.1 交换齿轮计算及配置 1120
2.3 铣削方法 1120
2.2 飞刀各部尺寸计算 1120
2 飞刀展成铣削蜗轮方法 1120
3.3 常用滚齿夹具及齿轮坯安装 1123
3.4 滚刀心轴和滚刀的安装要求 1123
3.5 滚刀安装角度和工作台转动方向及中间轮装置 1125
3.6 交换齿轮计算及滚齿机定数 1129
3.7 滚铣大质数齿轮 1129
3.7.1 滚铣大质数直齿圆柱齿轮时各组交换齿轮计算 1130
3.7.2 滚铣大质数斜齿圆柱齿轮时各组交换齿轮计算 1130
3.7.3 Y38滚齿机加工大质数直齿圆柱齿轮时,分度、差动交换齿轮表 1131
3.8 滚齿加工常见缺陷及解决方法 1132
4 插齿 1132
4.1 插齿机传动系统及工作精度 1134
4.3 插齿用夹具及调整 1137
4.2 插齿刀具的调整 1137
4.4 常用插齿机交换齿轮计算 1139
4.5 插齿加上中常出现的缺陷及解决方法 1140
5 挂轮表 1141
6 剃齿 1145
6.1 剃齿机及其精度 1145
6.2 常用剃齿方法 1148
6.3 剃齿用心轴 1149
6.4 剃齿加工余量 1151
6.5 剃齿误差产生原因及解决方法 1151
第5节 花键 1153
1 矩形花键 1153
1.1 矩形花键基本尺寸系列 1153
1.2 矩形花键键槽的截面尺寸 1154
1.3 矩形花键公差 1155
2.1 标准压力角及模数 1156
2.2 渐开线花键的基准齿形及主要参数 1156
2 圆柱直齿渐开线花键 1156
2.3 渐开线花键尺寸 1158
2.4 渐开线花键公差 1160
第6节 花键加工 1171
1 花键的定心方式及加工精度 1171
2 成形铣削方法 1171
2.1 用三面刃和锯片铣刀加工花键轴铣削过程 1171
2.2 用成形铣刀铣削花键 1174
3 铣削花健轴时产生的误差及解决方法 1175
第12章 难加工材料加工及特种加工 1176
第l节 难加工材料的切削加工 1176
1 常用的难切削材料及应用 1176
2 难切削金属材料的切削加工性比较 1176
3 高锰钢的切削加工 1177
3.1 常用切削高锰钢的刀具材料 1177
3.2 切削高锰钢车刀与铣刀的主要角度 1177
3.3 常用硬质合金刀具车削、铣削高锰钢的切削用量 1177
4.4 车削加工高强度钢切削用量 1178
4.3 切削高强度钢的车刀与铣刀的主要角度 1178
4.5 按高强度钢工件硬度选择铣削用量 1178
4 高强度钢的切削加工 1178
4.2 常用切削高强度钢用硬质合金 1178
4.1 常用切削高强度钢用高速钢刀具材料 1178
5 高温合金的切削加工 1179
5.l 常用切削高温合金的刀具材料 1179
5.2 车削高温合金常用刀具的前角与后角 1179
5.3 车削高温合金切削用量举例 1179
5.4 铣削高温合金切削用量举例 1180
6 钛合金的切削加工 1181
6.1 常用切削钛合金的刀具材料 1181
6.2 车削钛合金的车刀与铣刀主要角度 1182
6.3 车削钛合金切削用量 1182
6.4 铣削钛合金切削用量 1182
7 不锈钢的切削加工 1183
7.1 常用切削不锈钢的刀具材料 1183
7.2 切削不锈钢车刀与铣刀的主要角度 1183
7.4 高速钢铣刀铣削不锈钢切削用量 1184
7.3 车削不锈钢切削用量 1184
第2节 特种加工 1185
1 电火花线切割 1185
1.1 常用国产电火花线切割机床 1185
1.2 导轮 1186
1.3 电极丝保持器形式及特点 1187
1.4 典型夹具及附件形式 1188
1.5 不同工作液对工艺参数的影响 1189
2.2 常用国产电解加工机床 1190
2 电解加工 1190
2.1 电解加工应用举例 1190
2.3 各种间隙的计算公式 1191
2.4 电解液 1192
3 电喷涂 1196
3.1 电喷涂修复方法的优缺点 1196
3.2 电喷涂修复工艺 1196
4.2 灰铸铁件刷镀工艺 1197
4.1 刷镀的一般工艺过程 1197
4 电刷镀 1197
5 浇铸巴氏合金及补焊巴氏合金 1198
5.1 清理轴瓦 1198
5.2 挂锡处理 1198
5.3 浇铸 1198
5.4 巴氏合金浇铸后的冷却 1198
5.5 补焊巴氏合金 1199
第13章 数控加工程序编制 1200
第l节 零件加工工艺分析 1200
1 零件结构设计与加工艺性 1200
1.1 改进零件结构工艺性的方法 1200
1.2 使用数控机床加工零件应避免的特殊表面 1204
2 零件加工工艺分析的基本原则和方法 1204
第2节 零件编程通用标准 1206
1 数控机床的坐标轴和运动方向 1206
1.1 坐标和运动方向命名原则 1206
1.2 机床坐标系简图 1208
2 数控机床的编码字符 1211
3 数控机床的程序段格式 1211
3.1 字符的意义 1211
3.2 穿孔带程序段格式中符号含义 1212
3.3 键盘中所用符号的含义 1212
4 准备功能G代码及其功能 1212
5 辅助功能M代码及其功能 1213
6 常用数控标准 1215
6.1 我国的数控标准 1215
6.2 ISO制订的数控标准 1216
第3节 程序编制及举例 1216
1 数值计算 1216
1.1 直线圆弧的基点和节点计算方法 1216
1.2 非圆曲线节点计算方法 1216
2 程序编制 1216
2.1 基本移动指令构成的程序段 1216
2.2 补偿指令的应用 1220
2.3 螺纹切削程序段 1221
2.4 固定功能循环 1222
2.5 尖角过渡处理方法 1224
2.6 切入程序的编制 1225
3 编程举例 1225
3.1 数控车床程序编制举例 1225
3.2 数控铣床程序编制举例 1227
第4节 数控常用术语 1228
第14章 装配工艺 1232
第1节 装配工艺基础 1232
1 工艺方法的选择 1232
1.1 装配的工艺配合方法 1232
1.2 装配尺寸链的基本计算公式 1232
1.3 各种装配的组织形式 1233
1 清洗 1234
1.1 常用清洗方法 1234
第2节 一般装配的工作方法 1234
2 装配工艺规程制订的基本原则 1234
1.2 清洗液的选用 1235
1.2.1 防锈汽油配方 1235
1.2.2 常用碱液清洗液 1235
1.2.3 水剂清洗液 1236
2 平衡 1237
2.1 静平衡方法及平衡装置 1237
2.2.1 动平衡精度等级 1238
2.2 动平衡 1238
2.2.2 动平衡机类型及用途 1239
3 校准 1240
3.1 常见校准方法 1240
3.2 校准实例 1241
4 刮削 1242
4.1 常见刮削的应用及刮削面种类 1242
4.2 刮削工具 1243
4.2.1 刮刀的种类及用途 1243
4.2.2 通用刮研工具 1244
4.3 各种显示剂 1245
4.5 刮削余量 1246
4.4 刮削精度检验 1246
第3节 典型部件装配 1247
1 螺纹联接 1247
1.1 螺钉(栓)联接的几种形式 1247
1.2 螺纹联接的防松方法 1247
1.4 有预紧力要求的螺纹联接装配方法 1249
1.5 一般螺纹拧紧力矩 1249
1.3 螺纹联接的拧紧顺序 1249
2 过盈联接装配方法的选择 1250
3 铆接 1251
3.1 铆钉的几种典型铆接方法 1252
3.2 铆钉 1252
3.3 铆接常见缺陷产生原因及防止措施 1252
4 环氧树脂胶粘接 1254
4.1 环氧树脂胶粘接剂 1254
4.2 环氧树脂胶粘接工艺 1257
3 常用金属材料的弹性模量 1258
2 国外部分标准代号 1258
第15章 常用技术资料 1258
1 国内部分标准代号 1258
第1节 常用资料 1258
4 常用材料的摩擦系数 1259
5 常用材料的密度 1259
6 常用金属材料的熔点 1260
7 常用材料线膨胀系数 1260
8 各种硬度对照表 1260
9 主要元素的化学符号、相对原子质量和密度 1261
第2节 法定计量单位及其换算 1262
1 国际单位制 1262
2 常用法定计量单位与非法定计量单位的换算 1263
第3节 工厂常用计算 1266
1 单位换算 1266
2 数的平方、立方、平方根、立方根、圆周长及圆面积 1269
4 常用几何图形计算公式 1274
3 π的重要函数及π、25.4的近似分数 1274
5 圆的几何图形计算 1277
5.1 圆周等分系数表 1277
5.2 圆弧长度计算表 1277
第4节 公差与配合、表面形状和位置公差、表面粗糙度 1277
1 公差与配合 1277
1.1 术语及定义 1277
1.2 基本规定 1281
1.3 尺寸至500mm孔、轴公差与配合 1291
1.4 未注公差尺寸的极限偏差 1325
1.5 新旧国家标准对照 1329
2 形状和位置公差 1330
2.1 形状和位置公差的分类及符号 1330
2.2 形状和位置公差标注与说明 1332
2.3 形状和位置公差未注公差的规定 1343
2.4 图样上注出公差值的规定 1344
3 表面粗糙度 1347
1 一般用途圆锥的锥度与圆锥角 1350
第5节 锥度、锥角及其公差 1350
2 特殊用途圆锥的锥度与圆锥角 1351
3 圆锥公差 1351
3.1 圆锥角公差 1351
3.2 圆锥的形状公差 1353
4 未注公差角度的极限偏差 1354
第6节 机械制图 1354
l 图纸幅面及格式 1354
2 比例 1355
3 图线 1355
4 剖面符号 1356
5 简化画法 1356
6 尺寸注法 1358
7 简化注法 1361
8 各种孔的尺寸标注 1363
9 尺寸公差的标注 1364
10 螺纹和螺纹紧固件画法及标注 1366
11 中心孔的符号及标注方法 1370
12 滚动轴承的简化画法 1371
第7节 零件结构要素 1372
1 中心孔 1372
1.1 60°中心孔 1372
1.2 75°、90°中心孔 1372
2 零件倒圆与倒角 1373
3 圆形零件自由表面过渡圆角半径和过盈配合联接轴用例角 1374
4 球面半径 1374
5 润滑槽 1375
5.1 滑动轴承上用的润滑槽形式和尺寸 1375
5.2 平面上用润滑槽形式和尺寸 1376
6 滚花 1376
7 普通螺纹收尾、肩距、退刀槽和倒角尺寸 1376
7.1 普通外螺纹收尾、肩距、退刀槽和倒角尺寸 1376
8 米制锥螺纹的结构要素 1379
8.1 米制锥螺纹的螺纹收尾、肩距、退刀槽和倒角尺寸 1379
7.2 普通内螺纹的螺纹收尾、肩距、退刀槽和倒角尺寸 1379
8.2 米制锥螺纹接头尾端尺寸 1380
9 圆柱管螺纹收尾、退刀槽和倒角尺寸 1381
10 梯形螺纹收尾、退刀槽和倒角尺寸 1382
11 普通螺纹的内、外螺纺余留长度、钻孔余留深度、螺栓突出螺母的未端长度 1382
12 紧固件用通孔和沉孔 1383
l2.1 螺栓和螺钉用通孔 1383
12.4 圆柱头紧固件用沉孔 1384
12.3 沉头紧固件用沉孔 1384
12.2 铆钉用通孔 1384
12.5 六角头螺栓和六角螺母用沉孔 1385
13 退刀槽 1386
l3.2 公称直径相同具有不同配合的退刀槽 1387
14 砂轮越程槽 1387
15 刨削、插削、珩磨越程槽及插齿空刀槽 1389
16 T形槽 1390
17 燕尾槽 1392
参考文献 1393