图书介绍
现代磨削技术pdf电子书版本下载
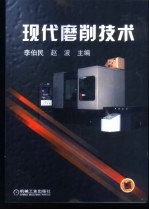
- 李伯民,赵波主编 著
- 出版社: 北京:机械工业出版社
- ISBN:7111110951
- 出版时间:2003
- 标注页数:538页
- 文件大小:33MB
- 文件页数:552页
- 主题词:
PDF下载
下载说明
现代磨削技术PDF格式电子书版下载
下载的文件为RAR压缩包。需要使用解压软件进行解压得到PDF格式图书。建议使用BT下载工具Free Download Manager进行下载,简称FDM(免费,没有广告,支持多平台)。本站资源全部打包为BT种子。所以需要使用专业的BT下载软件进行下载。如 BitComet qBittorrent uTorrent等BT下载工具。迅雷目前由于本站不是热门资源。不推荐使用!后期资源热门了。安装了迅雷也可以迅雷进行下载!
(文件页数 要大于 标注页数,上中下等多册电子书除外)
注意:本站所有压缩包均有解压码: 点击下载压缩包解压工具
图书目录
第1章 磨削加工技术概论 1
1.1 磨削加工技术发展概况 1
1.2 磨削加工方法与分类 2
1.3 磨削工艺系统 4
1.4 磨削加工技术发展趋势 5
1.4.1 磨削理论与工艺研究深入发展 5
1.4.2 磨床高速、高精度零部件单元制造技术 9
1.4.3 磨削自动化和智能化 10
1.4.4 磨削工艺过程监控与检测技术 11
1.4.5 磨削加工软件技术 11
第2章 磨削原理 12
2.1 磨削过程的特点及切屑形成 12
2.1.1 磨粒的切削刃形状与分布 12
2.1.2 磨削的特点 13
2.1.3 磨粒的切削作用与磨削过程 14
2.1.4 磨屑的形成 16
2.1.5 砂轮的有效磨刃数 16
2.2 表征磨削过程的磨削要素 18
2.2.1 接触弧长和磨削长度 18
2.2.2 磨粒磨削的磨屑厚度 22
2.2.3 砂轮的当量直径dse 26
2.2.4 磨削比G(Grinding Ratio) 27
2.2.5 被磨材料的磨除参数 28
2.3 磨削力 29
2.3.1 磨削力的意义 29
2.3.2 磨削力的理论公式 29
2.3.3 磨削力的尺寸效应 34
2.3.4 磨削力的测量与经验公式 38
2.4 磨削温度 44
2.4.1 磨削热的产生与传散 45
2.4.2 磨削区温度分布的理论解析 45
2.4.3 断续磨削时工件表面层温度解析 56
2.4.4 缓进给强力磨削的温度分布特征 62
2.4.5 磨削温度的测量 64
第3章 磨料磨具及其选择使用 70
3.1 普通磨料与磨具 70
3.1.1 普通磨具的结构与分类 70
3.1.2 磨具用磨料 71
3.1.3 磨料的粒度 73
3.1.4 磨具的硬度 75
3.1.5 磨具结合剂 78
3.1.6 磨具的组织 79
3.1.7 磨具形状尺寸 79
3.1.8 磨具的强度 80
3.1.9 磨具的静平衡度 80
3.2 普通磨料磨具的选择与使用 82
3.2.1 磨料的选择 82
3.2.2 磨料粒度选择 84
3.2.3 磨具的硬度选择 85
3.2.4 结合剂的选择 87
3.2.5 磨具组织的选择 88
3.2.6 磨具形状和尺寸的选择 88
3.2.7 按各种磨削条件选择普通磨具 89
3.2.8 按磨料对被磨削材料的适应性来选择磨具 90
3.2.9 磨具的安全使用 90
3.3 超硬磨料及其磨具 95
3.3.1 超硬磨料磨具的加工特点 95
3.3.2 金刚石的性质 96
3.3.3 超硬磨料立方氮化硼的性能 100
3.3.4 超硬磨料磨具的特性 100
3.4 超硬磨料磨具特性的选择 103
3.4.1 超硬磨料的选择 103
3.4.2 超硬磨料的粒度选择 103
3.4.3 超硬磨料磨具结合剂的选择 104
3.4.4 浓度的选择 105
3.4.5 超硬磨料磨具形状和尺寸的选择 106
3.4.6 超硬磨料磨具的使用 106
3.4.7 超硬磨料磨具的磨削用量选择 108
第4章 砂轮的磨损与修整 111
4.1 砂轮的堵塞 111
4.1.1 砂轮堵塞的形貌 111
4.1.2 砂轮堵塞的形成机理 112
4.1.3 影响砂轮堵塞的因素分析 114
4.2 砂轮的磨损 116
4.2.1 砂轮磨损形态与原因 116
4.2.2 砂轮磨损的特征 121
4.3 砂轮磨损的检测 124
4.4 普通磨料砂轮的修整 132
4.4.1 普通磨料砂轮的修整方法与工具 132
4.4.2 单颗粒金刚石笔修整法 133
4.4.3 金刚石滚轮修整 133
4.5 超硬磨料砂轮的修整 138
4.5.1 超硬磨料砂轮的整形法 138
4.5.2 超硬磨料砂轮修锐法 140
4.6 超硬磨料磨具修整技术的新进展 143
4.6.1 磨削修整法的改进——GC杯形砂轮研磨修整法 143
4.6.2 在线电解修整法(ELID) 149
4.6.3 简易的双电极在线修锐法 153
4.6.4 弹性修整法 155
4.6.5 超声波振动修整法 158
4.6.6 激光修锐法 158
第5章 磨削液 160
5.1 磨削液的性能和效果 160
5.1.1 磨削液的特性 160
5.1.2 磨削液的效果 161
5.2 磨削液的种类和组成 165
5.2.1 磨削液的种类 165
5.2.2 磨削液的组成 165
5.3 添加剂的种类和作用 167
5.3.1 磨削液中的极压添加剂 167
5.3.2 表面活性添加剂 168
5.3.3 无机盐类 169
5.3.4 磨削液中的添加剂对磨削效果的影响 169
5.4 磨削液的供给方法与效果 170
第6章 磨削加工表面质量 174
6.1 磨削加工表面质量的含义及其对使用性能的影响 174
6.1.1 表面质量的含义 174
6.1.2 磨削表面粗糙度与磨削加工精度的关系 174
6.1.3 表面质量对零件使用性能的影响 174
6.2 磨削表面纹理 175
6.2.1 磨削表面的创成机理 175
6.2.2 磨削表面粗糙度的理论分析 176
6.2.3 影响磨削加工表面粗糙度的因素 177
6.2.4 磨削加工表面粗糙度的经验公式 177
6.3 磨削表面层物理力学性能 178
6.3.1 磨削表面层加工硬化层的产生 178
6.3.2 磨削表面金相组织变化——磨削烧伤 178
6.3.3 表面层残余应力 180
6.4 磨削表面完整性参数综合影响及改善措施 182
6.4.1 磨削表面缺陷 182
6.4.2 磨削表面完整性参数间关系 182
6.4.3 改善磨削加工零件表面完整性的措施 182
6.5 磨削加工中的振动 183
6.5.1 磨削加工中的颤振现象 183
6.5.2 强迫颤振 184
6.5.3 再生颤振 185
第7章 固结磨具磨削工艺 187
7.1 外圆磨削 187
7.1.1 外圆磨削方式 187
7.1.2 数控外圆磨床加工 190
7.1.3 外圆磨削的工件装夹 190
7.1.4 砂轮的安装 191
7.1.5 轴类零件磨削工艺 192
7.1.6 台阶轴磨削 192
7.1.7 轴类零件的精度检验 193
7.1.8 外圆磨削的缺陷及消除方法 195
7.2 内圆磨削 195
7.2.1 内圆磨削的特点和应用 195
7.2.2 内孔的磨削方法 196
7.2.3 砂轮的选择和安装 198
7.2.4 内孔的精度检验 200
7.2.5 内孔磨削时的缺陷及消除方法 201
7.3 圆锥面磨削 202
7.3.1 圆锥面的磨削方法 202
7.3.2 圆锥的精度检验 204
7.3.3 圆锥面磨削的缺陷及消除方法 205
7.4 平面磨削 205
7.4.1 平面磨削方式 205
7.4.2 工件装夹 206
7.4.3 平行面的磨削 206
7.4.4 翘曲平面的磨削 207
7.4.5 垂直平面与斜面的磨削 207
7.4.6 台阶与直角形槽的磨削 208
7.4.7 平面的精度检验 208
7.4.8 平面磨削时的缺陷和消除方法 208
7.4.9 导轨的磨削 209
7.5 无心磨削 210
7.5.1 无心磨削基本原理和磨削方法 210
7.5.2 无心磨削的力学基础 211
7.5.3 工件成圆过程 213
7.5.4 导轮曲面形状及修整 214
7.5.5 无心磨削质量分析与控制 215
7.6 成形磨削 217
7.6.1 成形砂轮磨削 217
7.6.2 工件轨迹运动磨削法(靠模法) 217
7.6.3 展成磨削法 217
7.6.4 数控加工方法 217
7.7 齿轮磨削 218
7.7.1 磨齿加工原理 218
7.7.2 磨齿工艺 221
7.7.3 磨齿误差产生原因及消除方法 223
7.8 螺纹磨削 223
7.8.1 螺纹磨削特点和类型 223
7.8.2 螺纹磨削工艺要点 224
7.8.3 螺纹磨削砂轮选择 225
7.8.4 单线砂轮磨削用量 226
7.8.5 淬硬梯形螺纹长丝杠和滚珠丝杠磨削 226
7.8.6 内螺纹磨削 229
7.9 花键轴磨削 231
7.9.1 磨削矩形花键轴的方法 231
7.9.2 花键轴磨削时砂轮选择 232
7.9.3 花键轴磨削时的注意事项 233
第8章 高效及超精密磨削 234
8.1 高速磨削 234
8.1.1 高速磨削原理 234
8.1.2 高速磨削砂轮 237
8.2 缓进给磨削 239
8.2.1 缓进给磨削机理 239
8.2.2 砂轮与工件接触弧长度及接触时间 239
8.2.3 磨削力 240
8.2.4 磨削温度 241
8.2.5 砂轮磨损 241
8.2.6 表面完整性 241
8.2.7 缓进给磨削中温升控制 242
8.2.8 缓进给磨削过程中砂轮连续修整 242
8.3 高效深切磨削(HEDG) 243
8.3.1 高效深切磨削原理 244
8.3.2 HEDG的磨削力 246
8.3.3 HEDG对机床的要求 247
8.4 精密、高精密和超精密磨削工艺 247
8.4.1 概述 247
8.4.2 精密、高精密和超精密磨削磨料磨具 248
8.4.3 精密、高精密和超精密磨削工艺参数 250
8.4.4 精密、高精密和超精密磨削修整用量 251
8.4.5 精密、高精密和超精密磨削对机床、环境要求 251
8.5 镜面磨削加工工艺 252
8.6 电解磨削 253
8.6.1 电解磨削的原理 253
8.6.2 导电磨轮 254
8.6.3 电解液 256
8.6.4 电解磨削工艺 256
8.7 ELID镜面磨削法 258
8.7.1 平形砂轮的ELID镜面磨削系统 258
8.7.2 CIFB杯形砂轮外圆镜面磨削 258
8.8 其他高效磨削工艺简介 259
8.8.1 快速短行程磨削 259
8.8.2 大气孔宽砂轮磨削工艺 259
8.8.3 多砂轮磨削工艺 260
8.8.4 恒压力(定力)磨削工艺 260
8.8.5 冷风磨削工艺 261
8.8.6 单点磨削工艺 262
8.8.7 高速重负荷磨削工艺 262
第9章 涂附磨具磨削工艺技术 263
9.1 涂附磨具磨削加工工艺概述 263
9.1.1 涂附磨具定义、构成及分类 263
9.1.2 涂附磨具制造 263
9.1.3 砂带 264
9.1.4 涂附磨具加工应用范围 264
9.2 砂带磨削 265
9.2.1 砂带磨削机理与特点 265
9.2.2 砂带磨削方式 266
9.2.3 接触轮材料、形状、硬度选择 267
9.2.4 张紧与调偏机构 269
9.2.5 砂带磨削工艺参数 269
9.2.6 砂带磨床 275
9.2.7 砂带磨削加工实例 277
9.3 超精密砂带磨削 280
9.3.1 砂带 280
9.3.2 超精密砂带磨削方式 280
9.3.3 超声波砂带磨削运动与机理 281
9.4 强力砂带磨削 282
9.5 其他形状的涂附磨具与应用 283
9.5.1 张页式涂附磨具 283
9.5.2 卷状涂附磨具 283
9.5.3 圆筒状卷绕砂布带 283
9.5.4 砂盘 283
9.5.5 方形砂片和十字形砂片 283
9.5.6 砂布页轮 283
9.6 砂带堵塞与磨损 284
9.6.1 砂带堵塞 284
9.6.2 砂带磨损 286
第10章 精整加工技术 287
10.1 概述 287
10.1.1 精整加工的范畴及特点 287
10.1.2 精整加工机理 287
10.2 超精加工 287
10.2.1 超精加工机理和特点 288
10.2.2 超精加工方式 289
10.2.3 超精加工工艺参数 290
10.2.4 超精加工头和超精加工油石 291
10.2.5 无心外圆超精加工 291
10.2.6 轮式超精磨 293
10.2.7 超精加工机运动方式 294
10.3 普通珩磨 296
10.3.1 珩磨加工特点及原理 297
10.3.2 珩磨油石 299
10.3.3 珩磨头的结构形式 300
10.3.4 平顶珩磨头 303
10.3.5 珩磨头结构设计 306
10.3.6 珩磨夹具 308
10.3.7 珩磨用量 309
10.4 超声波振动珩磨 312
10.4.1 超声波振动加工的工艺效果 313
10.4.2 超声波振动珩磨的磨削机理 314
10.4.3 超声波振动珩磨装置结构 320
10.4.4 超声波振动珩磨装置的设计要点 322
10.5 超声波振动珩磨声学系统的局部共振设计原理 329
10.5.1 超声波振动珩磨声学系统的局部共振现象试验 329
10.5.2 油石座的长度参数变化对节点位置的影响 331
10.5.3 超声波振动珩磨系统的局部共振机理 332
10.5.4 超声波振动珩磨油石的等效硬度特性 336
第11章 游离磨粒加工技术 339
11.1 概述 339
11.1.1 游离磨粒加工机理 339
11.1.2 超精密研磨及超精密抛光加工环境 341
11.1.3 游离磨粒加工特点 342
11.2 研磨 342
11.2.1 研磨原理及过程 343
11.2.2 研磨加工特点 344
11.2.3 手工研磨与机械研磨 345
11.2.4 研磨工具 345
11.2.5 研磨剂 349
11.2.6 研磨运动轨迹 352
11.2.7 研磨工艺参数 356
11.2.8 研磨加工的应用 359
11.2.9 研磨机 364
11.3 研磨新工艺 366
11.3.1 动压浮起平面研磨 366
11.3.2 液中研抛 367
11.3.3 液体结合剂砂轮研磨 367
11.3.4 磨粒胶片带研磨 368
11.3.5 振动砂带研抛 369
11.4 超精研抛 369
11.4.1 超精研抛加工原理 369
11.4.2 超精研抛特性及研抛加工特点 369
11.4.3 超精研抛的四个阶段 370
11.4.4 超精研抛轨迹方程 371
11.4.5 超精研抛区表与最佳研抛轨迹的选择 373
11.5 磁性研磨与电徒动研磨 374
11.5.1 磁性研磨 374
11.5.2 电场电徒动研磨(Migration Polishing) 380
11.6 磨粒喷射加工与磨料流动加工 380
11.6.1 磨粒喷射加工 380
11.6.2 磨料流动加工 382
11.7 抛光(Polishing) 384
11.7.1 抛光方式 385
11.7.2 抛光机理 385
11.7.3 抛光剂 386
11.7.4 浮动抛光(Float Polishing) 387
11.7.5 修饰加工 389
11.7.6 端面非接触镜面抛光 389
11.7.7 “8”字流动抛光 389
11.7.8 刷光表面光整加工 389
11.8 复合抛光工艺 391
11.8.1 机械化学抛光(Progressive Mechanical And Chemical Polishing:P-MAC) 391
11.8.2 水合抛光(Hydration Polishing) 392
11.8.3 胶质硅抛光 392
11.8.4 非接触化学抛光 392
11.9 硬脆材料的抛光 393
11.9.1 陶瓷的金刚石微粉抛光 393
11.9.2 硅片的机械化学复合抛光 395
11.10 弹性发射(EEM)加工 396
11.10.1 EEM概念与加工原理 396
11.10.2 EEM加工装置及NC控制 396
11.10.3 EEM加工结果 398
第12章 硬脆材料与难加工材料磨削 399
12.1 工程陶瓷磨削 399
12.1.1 工程陶瓷的种类及材料特性 399
12.1.2 工程陶瓷磨削机理 400
12.1.3 工程陶瓷定压力磨削及定切深磨削特性 406
12.1.4 加工条件对磨削特性的影响 407
12.1.5 工程陶瓷的镜面磨削 409
12.1.6 加工表面变质层的评价 411
12.1.7 工程陶瓷的复合加工 413
12.1.8 超声波振动磨削工程陶瓷 413
12.2 玻璃的磨削 414
12.2.1 熔融石英玻璃的磨削 414
12.2.2 光学玻璃磨削 414
12.3 石材的磨削加工 414
12.3.1 大理石磨削表面形成机理 414
12.3.2 花岗石的磨削加工 417
12.3.3 蛇纹石的抛光 418
12.4 钛合金磨削 418
12.4.1 钛合金性能及磨削特点 418
12.4.2 钛合金磨削特性 419
12.4.3 磨削用量 421
12.5 高温合金磨削 421
12.5.1 高温合金的种类及物理力学性能 421
12.5.2 高温合金磨削特点 422
12.5.3 砂轮选择 422
12.5.4 磨削用量 422
12.5.5 DZ4高温合金磨削工艺优化 422
12.6 不锈钢磨削 425
12.6.1 不锈钢的种类及物理力学特性 425
12.6.2 不锈钢磨削加工特点 426
12.6.3 砂轮选择 427
12.6.4 磨削用量 427
第13章 磨削工艺中的新技术 428
13.1 数控磨削工艺 428
13.1.1 数控磨床及磨削加工中心磨削加工特点 428
13.1.2 数控加工工艺设计 430
13.1.3 数控磨削用量 432
13.1.4 数控工艺创成过程 432
13.2 磨削数据库 433
13.2.1 磨削数据库的系统目标 433
13.2.2 磨削数据库的开发策略 433
13.2.3 磨削数据库系统结构 434
13.2.4 磨削工艺生成模块 435
13.2.5 设计文档 436
13.3 磨削加工的计算机仿真 438
13.3.1 系统仿真的概念 438
13.3.2 磨削加工仿真流程总图 438
13.3.3 磨削仿真数据输入流程图 439
13.3.4 磨削模型 439
13.3.5 输出流程图 443
13.3.6 细长轴(筒)磨削过程中受力变形计算机仿真 443
13.3.7 纳米磨削过程中分子动力学计算机仿真试验 446
13.4 磨削加工的专家系统 450
13.4.1 机械系统的特征 451
13.4.2 专家型自律机械系统的基本概念 451
13.4.3 对象问题的设定和系统的适用范围 452
13.4.4 磨削加工准备工序系统框图 452
第14章 数控磨床 453
14.1 数控磨床 453
14.1.1 概述 453
14.1.2 MK1320型数控外圆磨床 454
14.1.3 MK6030型数控工具磨床 459
14.1.4 数控坐标磨床 465
14.2 磨削加工中心(GC)简介 468
14.2.1 磨削加工中心(GC)的定义及分类 468
14.2.2 磨削加工中心的优点与特点 468
14.2.3 支撑GC高度化的技术 469
14.2.4 GC32型磨削加工中心简介 469
14.2.5 GC在陶瓷加工中的应用 470
14.2.6 车削—磨削(L—G)复合加工中心 472
14.3 典型数控系统 472
14.4 CNC系统的软件 475
14.4.1 中断型结构型CNC软件总体结构 475
14.4.2 输入数据的处理 476
14.4.3 进给速度的控制 478
14.5 数控磨床伺服系统 479
14.5.1 直流主轴驱动系统 480
14.5.2 交流主轴电动机伺服系统 480
14.5.3 进给伺服系统 482
14.6 数控磨床检测元件 485
14.6.1 脉冲编码器 485
14.6.2 光栅 485
14.6.3 磁栅(R) 486
14.7 数控加工程序编制基础知识 487
14.7.1 程序编制的基本概念 487
14.7.2 程序编制内容和方法 490
14.7.3 程序编制方法 493
14.7.4 自动程序编制 494
14.8 磨床夹具 495
第15章 磨削中的精密测量技术 496
15.1 磨削中典型物理量的精密测量方法与仪器 496
15.1.1 常用硬度测量方法 496
15.1.2 磨削表面层显微硬度的测量方法 499
15.1.3 磨削烧伤的判别与检测 500
15.1.4 磨削残余应力的检测 507
15.2 精密磨削表面的典型测量系统简介 510
15.2.1 双频激光外差干涉仪及应用 510
15.2.2 圆度仪及圆度测量 516
15.2.3 三坐标测量机 517
15.2.4 激光测量技术 522
15.2.5 气动量仪测量技术 525
15.3 纳米表面测量技术 529
15.3.1 纳米级测量方法简介 529
15.3.2 Fabry-Perot标准具的测量技术 529
15.3.3 X射线干涉测量技术 530
15.3.4 扫描隧道显微测量技术 530
15.3.5 微观表面形貌的扫描探针测量和其他扫描测量技术 535
参考文献 537