图书介绍
简明电镀工艺手册pdf电子书版本下载
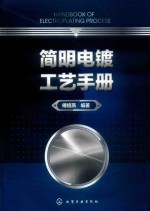
- 傅绍燕编著 著
- 出版社: 北京:化学工业出版社
- ISBN:9787122299673
- 出版时间:2018
- 标注页数:988页
- 文件大小:309MB
- 文件页数:1007页
- 主题词:电镀-技术手册
PDF下载
下载说明
简明电镀工艺手册PDF格式电子书版下载
下载的文件为RAR压缩包。需要使用解压软件进行解压得到PDF格式图书。建议使用BT下载工具Free Download Manager进行下载,简称FDM(免费,没有广告,支持多平台)。本站资源全部打包为BT种子。所以需要使用专业的BT下载软件进行下载。如 BitComet qBittorrent uTorrent等BT下载工具。迅雷目前由于本站不是热门资源。不推荐使用!后期资源热门了。安装了迅雷也可以迅雷进行下载!
(文件页数 要大于 标注页数,上中下等多册电子书除外)
注意:本站所有压缩包均有解压码: 点击下载压缩包解压工具
图书目录
第1篇 电镀基本概念和基础资料 1
第1章 电镀基本概念 1
1.1 概述 1
1.2 电极电位 1
1.3 电极的极化 4
1.4 过电位及氢过电位 5
1.4.1 过电位 5
1.4.2 氢过电位 5
1.5 析出电位 6
1.6 电化当量 7
1.6.1 常用金属及某些元素的电化当量 7
1.6.2 金属合金的电化当量 8
1.7 电镀溶液对镀层的影响 8
1.8 工艺操作条件对镀层的影响 9
1.9 电沉积时析氢对镀层的影响 10
1.10 基体金属对镀层的影响 11
1.11 分散能力和覆盖能力 12
1.11.1 概述 12
1.11.2 影响分散能力和覆盖能力的因素 12
1.12 电流效率 14
1.13 常用镀种对直流电源纹波系数的要求 15
1.14 镀层硬度 15
1.15 电镀基本计算 16
1.15.1 沉积金属质量、镀层厚度及电镀时间的计算 16
1.15.2 阴极电流密度及电流效率的计算 16
1.15.3 镀层沉积速度的计算 17
1.15.4 镀层金属沉积时间与阴极电流密度的关系 17
1.15.5 镀层金属的质量 18
1.16 电镀零件面积的计算 19
第2章 镀覆层选择及其厚度系列 20
2.1 镀覆层选择 20
2.1.1 概述 20
2.1.2 镀覆层选择考虑的因素 21
2.1.3 根据制品的用途选择金属镀覆层 21
2.1.4 互相接触金属的镀层选择 22
2.1.5 钢铁零件防护体系的选择 23
2.1.6 铝及铝合金零件防护层的选择 25
2.1.7 镁合金零件防护层的选择 25
2.1.8 铜及铜合金零件防护层的选择 25
2.1.9 钛合金零件防护层的选择 26
2.1.10 其他金属零件防护层的选择 26
2.2 镀覆层厚度系列 27
2.2.1 概述 27
2.2.2 锌镀层厚度系列及应用范围 28
2.2.3 镉镀层厚度系列及应用范围 30
2.2.4 铜镀层厚度系列及应用范围 32
2.2.5 锡镀层厚度系列及应用范围 33
2.2.6 镍镀层厚度系列及应用范围 33
2.2.7 工程用铬镀层厚度系列及应用范围 36
2.2.8 镍+铬和铜+镍+铬电镀层厚度系列 36
2.2.9 塑料上镍+铬电镀层厚度系列 42
2.2.10 铅镀层厚度系列及应用范围 43
2.2.11 铁镀层厚度系列及应用范围 43
2.2.12 银镀层厚度系列及应用范围 44
2.2.13 金镀层厚度系列及应用范围 45
2.2.14 锌合金铸件防护装饰性镀层的厚度 45
2.2.15 化学镀镍-磷合金镀层厚度系列 46
2.2.16 铜-锡合金镀层厚度系列 47
第3章 镀覆层标识方法 49
3.1 金属镀覆及化学处理标识方法 49
3.1.1 标识的组成部分 49
3.1.2 标识方法的排列顺序 49
3.1.3 金属镀覆方法及化学处理常用符号 50
3.2 典型镀覆层的标识示例 50
3.2.1 金属基体上镍+铬和铜+镍+铬电镀层标识 50
3.2.2 塑料上镍+铬电镀层标识 51
3.2.3 金属基体上装饰性镍、铜+镍电镀层标识 51
3.2.4 钢铁上锌电镀层、镉电镀层的标识 52
3.2.5 工程用铬电镀层标识 52
3.2.6 工程用镍电镀层标识 53
3.2.7 化学镀(自催化)镍-磷合金镀层标识 53
3.2.8 工程用银和银合金电镀层标识 54
3.2.9 工程用金和金合金镀层标识 54
3.2.10 金属基体上锡和锡合金镀层标识 55
第2篇 电镀单金属 56
第4章 电镀前处理 56
4.1 镀件镀覆前质量控制的技术要求 56
4.1.1 镀覆前金属零部件的一般要求 56
4.1.2 镀覆前消除应力的热处理要求 57
4.1.3 镀覆前表面粗糙度的要求 57
4.2 电镀前处理方法 58
4.3 机械前处理 58
4.3.1 喷砂 59
4.3.2 滚光 62
4.3.3 刷光 64
4.3.4 磨光 65
4.3.5 抛光 69
4.3.6 成批光饰 70
4.4 除油 75
4.4.1 概述 75
4.4.2 有机溶剂除油 76
4.4.3 化学除油 77
4.4.4 碱液除蜡 83
4.4.5 电化学除油 84
4.4.6 超声波清洗除油 85
4.4.7 擦拭除油和滚筒除油 86
4.5 浸蚀 86
4.5.1 概述 86
4.5.2 浸蚀常用的酸和缓蚀剂的作用及其功能 87
4.6 化学浸蚀 88
4.6.1 钢铁零件的化学浸蚀 88
4.6.2 不锈钢零件的化学浸蚀 91
4.6.3 铜及铜合金零件的化学浸蚀 92
4.6.4 铝及铝合金零件的化学浸蚀 93
4.6.5 锌及锌合金零件的化学浸蚀 95
4.6.6 镁及镁合金零件的化学浸蚀 95
4.6.7 其他金属零件的化学浸蚀 96
4.7 电化学浸蚀 97
4.8 去接触铜、除浸蚀残渣 99
4.9 工序间防锈 100
4.10 化学抛光 101
4.10.1 钢铁件的化学抛光 101
4.10.2 不锈钢件的化学抛光 102
4.10.3 铜及铜合金件的化学抛光 103
4.10.4 铝及铝合金件的化学抛光 104
4.10.5 其他金属件的化学抛光 105
4.11 电化学抛光 106
4.11.1 钢铁件的电化学抛光 106
4.11.2 不锈钢件的电化学抛光 107
4.11.3 铜及铜合金件的电化学抛光 108
4.11.4 铝及铝合金件的电化学抛光 109
4.11.5 镍及镍镀层的电化学抛光 110
第5章 镀锌 111
5.1 概述 111
5.2 氰化镀锌 111
5.2.1 概述 111
5.2.2 镀液组成及工艺规范 112
5.2.3 镀液中各成分的作用 114
5.2.4 工艺规范的影响 115
5.2.5 杂质的影响及处理方法 115
5.3 锌酸盐镀锌 116
5.3.1 概述 116
5.3.2 镀液组成及工艺规范 116
5.3.3 镀液中各成分的作用 119
5.3.4 工艺规范的影响 119
5.3.5 杂质的影响及处理方法 120
5.4 氯化钾镀锌 120
5.4.1 氯化钾镀锌的特点 121
5.4.2 镀液组成及工艺规范 121
5.4.3 镀液中各成分的作用 123
5.4.4 工艺规范的影响 125
5.4.5 杂质的影响及处理方法 125
5.5 氯化铵镀锌 126
5.5.1 概述 126
5.5.2 镀液组成及工艺规范 126
5.5.3 镀液中各成分的作用 127
5.5.4 工艺规范的影响 128
5.5.5 杂质的影响及处理方法 128
5.6 硫酸盐镀锌 129
5.6.1 镀液组成及工艺规范 129
5.6.2 镀液中各成分的作用 130
5.6.3 工艺规范的影响 130
5.7 除氢处理 131
5.8 锌镀层钝化处理 131
5.8.1 概述 131
5.8.2 锌镀层钝化处理方法 132
5.9 锌镀层铬酸盐钝化 132
5.9.1 铬酸盐钝化机理 132
5.9.2 高铬酸盐钝化 135
5.9.3 低铬酸盐钝化 136
5.9.4 超低铬酸盐钝化 139
5.9.5 军绿色钝化 141
5.9.6 黑色钝化 143
5.9.7 金黄色钝化 144
5.10 三价铬钝化 145
5.10.1 三价铬彩色钝化 145
5.10.2 三价铬蓝白色钝化 147
5.10.3 三价铬黑色钝化 149
5.11 无铬钝化 151
5.11.1 钛酸盐钝化 151
5.11.2 钼酸盐钝化 152
5.11.3 硅酸盐钝化 154
5.11.4 稀土盐钝化处理 154
5.11.5 植酸钝化处理 155
5.11.6 无铬钝化剂 155
5.12 不合格锌镀层的退除 156
第6章 镀镉 157
6.1 概述 157
6.2 氰化镀镉 158
6.2.1 镀液中各成分的作用 158
6.2.2 工艺规范的影响 159
6.2.3 杂质的影响及处理方法 160
6.3 硫酸盐镀镉 160
6.3.1 镀液组成及工艺规范 160
6.3.2 镀液中各成分的作用 161
6.3.3 工艺规范的影响 161
6.4 氨羧配位化合物镀镉 162
6.5 有机多膦酸盐(HEDP)镀镉 162
6.6 镉镀层的后处理 163
6.6.1 镉镀层的出光 163
6.6.2 镉镀层的钝化 163
6.7 除氢 164
6.8 不合格镀层的退除 164
第7章 镀锡 166
7.1 概述 166
7.1.1 锡镀层的要求和用途 166
7.1.2 镀锡的工艺方法 167
7.2 硫酸盐镀锡 167
7.2.1 镀液组成及工艺规范 168
7.2.2 镀液中各成分的作用 169
7.2.3 工艺规范的影响 170
7.2.4 杂质的影响及处理方法 171
7.3 甲基磺酸盐镀锡 171
7.3.1 镀液组成及工艺规范 171
7.3.2 镀液中各成分的作用 172
7.3.3 工艺规范的影响 173
7.3.4 杂质的影响及处理方法 173
7.4 氟硼酸盐镀锡 174
7.4.1 镀液组成及工艺规范 174
7.4.2 镀液中各成分的作用及溶液维护 174
7.5 碱性镀锡 175
7.5.1 镀液组成及工艺规范 175
7.5.2 镀液中各成分的作用 176
7.5.3 工艺规范的影响 176
7.5.4 杂质的影响及处理方法 176
7.6 晶纹镀锡 177
7.6.1 工艺方法及操作要点 177
7.6.2 镀液组成及工艺过程 177
7.7 锡镀层防变色处理 178
7.8 不合格锡镀层的退除 179
第8章 镀铜 180
8.1 概述 180
8.2 铜镀层的应用 181
8.3 预镀及预浸渍处理 181
8.4 镀铜种类及镀铜前处理工艺流程 183
8.5 氰化镀铜 184
8.5.1 镀液组成及工艺规范 185
8.5.2 镀液中各成分的作用 186
8.5.3 工艺规范的影响 188
8.5.4 杂质的影响及处理方法 188
8.6 硫酸盐酸性镀铜 189
8.6.1 概述 189
8.6.2 镀液类型、组成及工艺规范 189
8.6.3 镀液中各成分的作用 193
8.6.4 工艺规范的影响 195
8.6.5 杂质的影响及处理方法 196
8.6.6 光亮酸性镀铜后的除膜 196
8.7 焦磷酸盐镀铜 197
8.7.1 镀液组成及工艺规范 198
8.7.2 镀液中各成分的作用 200
8.7.3 工艺规范的影响 202
8.7.4 杂质的影响及处理方法 203
8.8 有机多膦酸(HEDP)镀铜 203
8.8.1 概述 203
8.8.2 镀液组成及工艺规范 204
8.8.3 镀液中各成分的作用 204
8.8.4 工艺规范的影响 205
8.9 柠檬酸盐镀铜 205
8.9.1 镀液组成及工艺规范 206
8.9.2 镀液中各成分的作用 207
8.9.3 工艺规范的影响 207
8.10 其他镀铜 208
8.10.1 草酸盐镀铜 208
8.10.2 乙二胺镀铜 209
8.10.3 酒石酸盐镀铜 210
8.10.4 商品镀铜溶液 211
8.11 不合格铜镀层的退除 212
第9章 镀镍 214
9.1 概述 214
9.2 镀镍添加剂 215
9.2.1 镀镍添加剂的分类 215
9.2.2 光亮镀镍添加剂的技术性能要求 217
9.2.3 镀镍添加剂中间体 218
9.3 普通镀镍 221
9.3.1 镀液组成及工艺规范 221
9.3.2 镀液中各成分的作用 222
9.3.3 工艺规范的影响 223
9.3.4 杂质的影响及处理方法 224
9.4 镀多层镍 225
9.4.1 多层镍的组合形式及耐蚀性 225
9.4.2 单层镍和双层镍体系 226
9.4.3 三层镍体系 227
9.4.4 四层镍体系 228
9.5 半光亮镀镍 228
9.5.1 镀液组成及工艺规范 228
9.5.2 半光亮镀镍用的添加剂 230
9.5.3 镀液的日常维护和管理 231
9.6 光亮镀镍 231
9.6.1 镀液组成及工艺规范 231
9.6.2 镀液的日常维护和管理 236
9.7 镀高硫镍 237
9.7.1 镀液组成及工艺规范 237
9.7.2 镀液的日常维护 239
9.8 封闭镀镍 239
9.8.1 概述 239
9.8.2 镀液组成及工艺规范 240
9.8.3 镀液的日常维护 242
9.9 镀高应力镍 242
9.9.1 概述 242
9.9.2 镀液组成及工艺规范 243
9.9.3 镀高应力镍的质量控制与管理 244
9.10 镀缎面镍 244
9.10.1 概述 244
9.10.2 镀液组成及工艺规范 245
9.10.3 镀液组成及工艺规范的影响 247
9.11 镀黑镍 248
9.11.1 镀液成分及工艺规范 248
9.11.2 镀液的日常维护和管理 249
9.12 镀枪色镍及其合金 250
9.12.1 概述 250
9.12.2 镀液组成及工艺规范 250
9.12.3 镀液成分及工艺规范的影响 252
9.12.4 镀液维护和去除杂质 252
9.13 柠檬酸盐镀镍 252
9.13.1 镀液组成及工艺规范 252
9.13.2 镀液的控制与维护 253
9.14 氯化物镀镍 253
9.14.1 高氯化物镀镍 253
9.14.2 强酸性全氯化物镀镍 254
9.15 氨基磺酸盐镀镍 254
9.15.1 镀液组成及工艺规范 255
9.15.2 镀液的控制与维护 255
9.16 深孔零件镀镍 255
9.16.1 镀液组成及工艺规范 256
9.16.2 添加剂的作用及工艺规范的影响 257
9.16.3 镀层处理 257
9.17 不合格镍镀层的退除 258
第10章 镀铬 260
10.1 概述 260
10.2 镀铬工艺的特点 261
10.3 镀铬用阳极 262
10.4 普通镀铬 263
10.4.1 概述 263
10.4.2 镀液组成及工艺规范 263
10.4.3 镀液成分的影响 265
10.4.4 工艺规范的影响 267
10.4.5 提高铬镀层结合力的措施 269
10.4.6 铬镀层的渗氢和除氢 271
10.4.7 杂质的影响及处理方法 272
10.5 防护-装饰性镀铬 273
10.5.1 概述 273
10.5.2 一般防护-装饰性镀铬 273
10.5.3 高耐蚀性-装饰镀铬 274
10.6 镀硬铬 275
10.6.1 概述 275
10.6.2 镀硬铬的工艺要求 275
10.6.3 镀液组成及工艺规范 276
10.7 滚镀铬 277
10.8 复合镀铬 279
10.8.1 复合镀铬与普通镀铬的比较 279
10.8.2 镀液组成及工艺规范 279
10.9 自动调节镀铬 280
10.10 快速镀铬 281
10.11 冷镀铬 282
10.12 四铬酸盐镀铬 282
10.13 双层镀铬 283
10.14 镀乳白铬 284
10.15 镀黑铬 285
10.15.1 概述 285
10.15.2 镀液组成及工艺规范 285
10.15.3 镀液中各成分的作用 287
10.15.4 工艺规范的影响 288
10.15.5 杂质的影响及处理方法 288
10.16 松孔镀铬 288
10.16.1 概述 288
10.16.2 松孔镀铬的加工方法 289
10.16.3 镀液组成及工艺规范 290
10.16.4 松孔铬镀层的影响因素 290
10.17 三价铬镀铬 292
10.17.1 概述 292
10.17.2 硫酸盐三价铬镀铬 293
10.17.3 氯化物三价铬镀铬 295
10.17.4 商品添加剂的三价铬镀铬 297
10.17.5 三价铬镀铬用的阳极 298
10.17.6 三价铬镀液中杂质的影响及去除方法 299
10.18 三价铬镀黑铬 300
10.19 低铬酸镀铬 301
10.20 稀土镀铬 303
10.21 不合格铬镀层的退除 304
第11章 镀铅 307
11.1 概述 307
11.2 氟硼酸盐镀铅 307
11.2.1 镀液组成及工艺规范 307
11.2.2 镀液中主要成分的作用 308
11.2.3 工艺规范的影响 309
11.2.4 杂质的影响及处理方法 309
11.3 甲基磺酸盐镀铅 309
11.3.1 镀液组成及工艺规范 310
11.3.2 镀液成分及工艺规范的影响 310
11.4 其他溶液镀铅 310
11.5 不合格镀层的退除 311
第12章 镀铁 312
12.1 概述 312
12.2 氯化物镀铁 312
12.2.1 概述 312
12.2.2 镀液组成及工艺规范 313
12.2.3 镀液成分和工艺规范的影响 314
12.2.4 氯化物低温镀铁技术 315
12.3 硫酸盐镀铁 316
12.4 氨基磺酸盐镀铁 317
12.5 氟硼酸盐镀铁 317
12.6 不合格镀层的退除 318
第13章 镀银 319
13.1 概述 319
13.2 氰化镀银 320
13.2.1 镀液组成及工艺规范 320
13.2.2 镀液中各成分的作用 322
13.2.3 工艺规范的影响 323
13.3 无氰镀银 324
13.3.1 硫代硫酸盐镀银 324
13.3.2 亚氨基二磺酸铵(NS)镀银 325
13.3.3 磺基水杨酸镀银 326
13.3.4 烟酸镀银 326
13.4 镀银的前处理 327
13.5 镀银的后处理 328
13.6 银镀层防变色处理 329
13.6.1 化学钝化 329
13.6.2 电解钝化 330
13.6.3 浸涂有机防变色剂 331
13.6.4 电泳涂覆层 332
13.6.5 已变色银镀层的处理 332
13.7 不合格银镀层的退除 333
第14章 镀金 334
14.1 概述 334
14.2 氰化镀金 335
14.2.1 镀液组成及工艺规范 335
14.2.2 镀液成分和工艺规范的影响 338
14.3 柠檬酸盐镀金 338
14.3.1 镀液组成及工艺规范 339
14.3.2 镀液成分和工艺规范的影响 340
14.4 亚硫酸盐镀金 341
14.4.1 镀液组成及工艺规范 341
14.4.2 镀液成分和工艺规范的影响 342
14.5 丙尔金镀金 343
14.5.1 镀液组成及工艺规范 343
14.5.2 镀液维护 344
14.6 商品添加剂的镀金工艺规范 344
14.7 不合格金镀层的退除 346
第15章 镀钯、镀铑、镀铂、镀铟 347
15.1 镀钯 347
15.1.1 镀液组成及工艺规范 347
15.1.2 溶液成分和工艺规范的影响 348
15.1.3 不合格钯镀层的退除 349
15.2 镀铑 350
15.2.1 硫酸型镀铑溶液 350
15.2.2 磷酸型镀铑溶液 351
15.2.3 氨基磺酸型镀铑溶液 352
15.2.4 不合格铑镀层的退除 352
15.3 镀铂 353
15.3.1 镀液组成及工艺规范 353
15.3.2 镀液成分和工艺规范的影响 354
15.3.3 不合格铂镀层的退除 355
15.4 镀铟 355
15.4.1 镀液组成及工艺规范 355
15.4.2 不合格铟镀层的退除 357
第3篇 电镀合金 358
第16章 电镀合金概论 358
16.1 概述 358
16.2 电镀合金的分类及用途 359
16.3 金属共沉积的基本条件 359
16.4 实现金属共沉积的措施 359
16.5 金属共沉积的类型 360
16.6 电镀合金的阳极 361
第17章 电镀防护性合金 362
17.1 概述 362
17.2 电镀Zn-Ni合金 362
17.2.1 碱性锌酸盐镀Zn-Ni合金 362
17.2.2 氯化物镀Zn-Ni合金 364
17.2.3 硫酸盐镀Zn-Ni合金 366
17.2.4 硫酸盐-氯化物镀Zn-Ni合金 367
17.2.5 钕铁硼永磁材料镀Zn-Ni合金 367
17.2.6 Zn-Ni合金镀层的钝化处理 368
17.2.7 Zn-Ni合金镀层的除氢处理 370
17.2.8 不合格Zn-Ni合金镀层的退除 370
17.3 电镀Zn-Fe合金 370
17.3.1 镀高铁Zn-Fe合金 371
17.3.2 镀低铁Zn-Fe合金 372
17.3.3 低铁Zn-Fe合金镀层的钝化处理 374
17.4 电镀Zn-Co合金 376
17.4.1 氯化物镀Zn-Co合金 376
17.4.2 碱性锌酸盐镀Zn-Co合金 377
17.4.3 硫酸盐镀Zn-Co合金 378
17.4.4 Zn-Co合金镀层的钝化处理 378
17.5 电镀Sn-Zn合金 379
17.5.1 氰化镀Sn-Zn合金 379
17.5.2 柠檬酸盐镀Sn-Zn合金 381
17.5.3 葡萄糖酸盐镀Sn-Zn合金 382
17.5.4 焦磷酸盐镀Sn-Zn合金 382
17.5.5 碱性锌酸盐镀Sn-Zn合金 383
17.5.6 Sn-Zn合金的钝化处理 383
17.5.7 不合格Sn-Zn合金镀层的退除 385
17.6 电镀Zn-Cd合金 385
17.6.1 氰化镀Zn-Cd合金 385
17.6.2 硫酸盐和氨基磺酸盐镀Zn-Cd合金 386
17.7 电镀Zn-Mn合金 386
17.8 电镀Zn-Cr合金 387
17.9 电镀Zn-Ti合金 389
17.10 电镀Cd-Ti合金 390
17.11 电镀Zn-Ni-Fe合金 391
17.12 电镀Zn-Fe-Co合金 393
17.13 电镀Zn-Co Mo合金 393
第18章 电镀装饰性合金 394
18.1 概述 394
18.2 电镀C u-Zn合金 394
18.2.1 概述 394
18.2.2 氰化镀Cu-Zn合金 395
18.2.3 酒石酸盐镀Cu-Zn合金 398
18.2.4 焦磷酸盐镀Cu-Zn合金 399
18.2.5 HEDP镀Cu-Zn合金 400
18.2.6 甘油-锌酸盐镀Cu-Zn合金 400
18.2.7 镀Cu-Zn合金的后处理 401
18.2.8 不合格Cu-Zn合金镀层的退除 402
18.3 电镀Cu-Sn合金 402
18.3.1 概述 402
18.3.2 高氰镀Cu-Sn合金 403
18.3.3 低氰镀Cu-Sn合金 407
18.3.4 焦磷酸盐镀Cu-Sn合金 408
18.3.5 柠檬酸盐镀Cu-Sn合金 410
18.3.6 不合格Cu-Sn合金镀层的退除 411
18.4 电镀Ni-Fe合金 411
18.4.1 概述 411
18.4.2 镀液组成及工艺规范 412
18.4.3 镀液成分及工艺规范的影响 414
18.4.4 不合格Ni-Fe合金镀层的退除 415
18.5 电镀Sn-Ni合金 415
18.5.1 概述 415
18.5.2 氟化物镀Sn-Ni合金 416
18.5.3 焦磷酸盐镀Sn-Ni合金 416
18.5.4 镀黑色光亮Sn-Ni合金 417
18.5.5 其他镀Sn-Ni合金 418
18.5.6 不合格Sn-Ni合金镀层的退除 419
18.6 电镀Sn-Co合金 419
18.7 电镀C u-Sn-Zn合金 421
18.7.1 镀银白色Cu-Sn-Zn合金 421
18.7.2 镀仿金Cu-Sn-Zn合金 422
18.7.3 仿金镀层的镀后处理 425
第19章 电镀功能性合金 426
19.1 概述 426
19.2 电镀可焊性合金 426
19.2.1 电镀Sn-Pb合金 426
19.2.2 电镀 Sn-Ce合金 430
19.2.3 电镀Sn-Bi合金 431
19.2.4 电镀Sn-Cu合金 433
19.2.5 电镀Sn-Ag合金 435
19.2.6 电镀Sn-Zn合金 436
19.2.7 电镀Sn-In合金 436
19.2.8 电镀可焊性三元合金 437
19.3 电镀耐磨性合金 438
19.3.1 电镀Cr-Ni合金 438
19.3.2 电镀Cr-Mo合金 439
19.3.3 电镀Ni-P合金 439
19.3.4 电镀Ni-W合金 441
19.4 电镀磁性合金 442
19.4.1 电镀Ni-Co合金 442
19.4.2 电镀Ni-Fe合金 444
19.4.3 电镀Co-W合金 445
19.4.4 电镀Co-Cr合金 446
19.4.5 电镀Co-P合金 447
19.4.6 电镀N i-P合金 447
19.4.7 电镀Ni-Co-P合金 448
19.5 电镀减摩性轴承合金 448
19.5.1 电镀Pb-Sn合金 448
19.5.2 电镀Pb-In、 Cu-In合金 449
19.5.3 电镀Ag-Pb合金 449
19.5.4 电镀Pb-Sn-Cu合金 450
19.6 不锈钢合金镀层 451
19.6.1 电镀Fe-Cr-Ni合金 451
19.6.2 电镀Cr-Fe、 Fe-Cr合金 452
第20章 电镀贵金属合金 453
20.1 概述 453
20.2 电镀金基合金 453
20.2.1 电镀A u-Co合金 454
20.2.2 电镀Au-Ni合金 455
20.2.3 电镀Au-Ag合金 455
20.2.4 电镀Au-Cu合金 456
20.2.5 电镀Au-Sb合金 457
20.2.6 电镀Au-Sn合金 458
20.2.7 不合格金合金镀层的退除 459
20.3 电镀银基合金 459
20.3.1 电镀Ag-Cd合金 459
20.3.2 电镀Ag-Sb合金 460
20.3.3 电镀Ag-Pb合金 461
20.3.4 电镀Ag-Sn合金 462
20.3.5 电镀Ag-Cu合金 463
20.3.6 电镀Ag-Ni和Ag-Co合金 463
20.3.7 不合格银合金镀层的退除 464
20.4 电镀钯基合金 465
20.4.1 电镀Pd-Ni合金 465
20.4.2 电镀Pd-Co、 Pd-Ag及Pd-Fe合金 467
20.5 电镀贵金属三元合金 467
20.5.1 电镀Au-Ag基三元合金 467
20.5.2 电镀Au-Sn基三元合金 468
第21章 电镀非晶态合金 470
21.1 概述 470
21.1.1 非晶态合金镀层分类 470
21.1.2 电镀非晶态合金的特性 470
21.1.3 电镀非晶态合金的用途 471
21.2 电镀镍基非晶态合金 472
21.2.1 电镀Ni-P非晶态合金 472
21.2.2 电镀Ni-W非晶态合金 473
21.2.3 电镀Ni-Mo非晶态合金 474
21.3 电镀铁基非晶态合金 475
21.3.1 电镀Fe-W非晶态合金 475
21.3.2 电镀Fe- Mo非晶态合金 476
21.3.3 电镀Fe-P非晶态合金 477
21.3.4 电镀Fe-Cr非晶态合金 477
21.4 电镀三元非晶态合金 478
21.4.1 电镀Ni-W-P非晶态合金 478
21.4.2 电镀Ni-Co-P、 Ni-Cr-P 非晶态合金 479
21.4.3 电镀Ni-W-B非晶态合金 480
21.4.4 电镀Fe-Ni-Cr非晶态合金 480
21.4.5 电镀C r-Fe-C非晶态合金 481
21.4.6 电镀Fe-Cr-P、 Fe-Cr-P-Co非晶态合金 481
第22章 电镀纳米合金 483
22.1 概述 483
22.2 电镀纳米镍基合金 483
22.2.1 电镀纳米Co-Ni合金 483
22.2.2 电镀纳米Ni-W合金 484
22.2.3 电镀纳米Ni-Cu合金 485
22.2.4 电镀纳米Ni-Mo合金 485
22.2.5 电镀纳米Ni-P合金 486
22.2.6 电镀纳米Ni-Fe合金 486
22.3 电镀纳米Zn-Fe合金 486
22.4 电镀纳米Fe-Ni合金 487
22.5 电镀纳米三元合金 487
22.6 电镀纳米复合镀层 488
22.6.1 电镀纳米镍复合镀层 488
22.6.2 电镀纳米镍合金复合镀层 489
22.7 电镀纳米镍镀层 490
第4篇 特种材料电镀 492
第23章 铝及铝合金的电镀 492
23.1 概述 492
23.1.1 铝及铝合金电镀的用途 492
23.1.2 铝及铝合金电镀的难点 493
23.1.3 电镀工艺流程 493
23.2 镀前处理 493
23.2.1 除油 493
23.2.2 浸蚀 495
23.2.3 重金属盐活化 496
23.3 中间处理 497
23.3.1 浸锌 497
23.3.2 浸重金属 499
23.3.3 电镀薄锌层 500
23.3.4 化学镀镍 501
23.3.5 阳极氧化处理 501
23.4 铝合金一步法镀铜 502
23.5 电镀 502
23.6 铝及铝合金件不合格镀层的退除 503
第24章 镁及镁合金的电镀 504
24.1 概述 504
24.1.1 镁合金的特性 504
24.1.2 镁合金电镀的难点 504
24.2 电镀工艺流程 505
24.3 镀前处理 505
24.3.1 除油 505
24.3.2 酸性浸蚀 506
24.3.3 活化 506
24.4 中间处理 507
24.4.1 浸锌 507
24.4.2 氰化预镀铜和中性预镀镍 508
24.4.3 焦磷盐预镀铜 509
24.4.4 预镀锌 509
24.4.5 浸锌后化学镀镍 510
24.4.6 直接化学镀镍 511
24.5 后续电镀工艺 512
24.5.1 镁合金的防护-装饰性电镀 512
24.5.2 镁合金的保护性电镀 514
24.6 镁合金件不合格镀层的退除 514
第25章 锌合金压铸件的电镀 516
25.1 概述 516
25.2 锌合金压铸件的电镀工艺流程 517
25.3 机械前处理 517
25.3.1 磨光 517
25.3.2 抛光 518
25.3.3 喷砂 519
25.4 除油 519
25.4.1 预除油 519
25.4.2 化学除油 520
25.4.3 电化学除油 521
25.5 弱浸蚀 522
25.6 中和、活化处理 522
25.7 预镀 523
25.7.1 预镀铜 523
25.7.2 预镀光亮黄铜 525
25.7.3 中性预镀镍 526
25.7.4 化学预镀镍 527
25.8 后续电镀 528
25.9 不合格镀层的退除 528
第26章 钛合金的电镀 530
26.1 概述 530
26.2 钛合金电镀工艺流程 530
26.3 化学除油和化学浸蚀 530
26.3.1 化学除油 530
26.3.2 化学浸蚀 531
26.4 电化学浸蚀 531
26.5 浸镍 532
26.6 浸锌和预镀锌 533
26.7 钛合金的电镀 533
26.8 镀后热处理 534
第27章 不锈钢的电镀 536
27.1 概述 536
27.2 不锈钢电镀工艺流程 536
27.3 前处理 536
27.4 活化和预镀 538
27.4.1 浸渍活化 538
27.4.2 阴极活化和阳极活化 539
27.4.3 活化与预镀同槽处理 539
27.4.4 阳极活化与预镀镍同槽处理 540
27.4.5 活化与预镀镍分槽处理 540
27.4.6 镀锌-退锌活化 541
27.5 电镀 541
27.6 不合格镀层的退除 541
第28章 粉末冶金件的电镀 542
28.1 概述 542
28.2 粉末冶金件的电镀工艺方法 542
28.3 封孔处理的工艺方法 542
28.3.1 封孔法的电镀工艺流程 542
28.3.2 封孔方法 542
28.3.3 镀前处理 544
28.3.4 后续电镀 545
28.4 中间镀层工艺方法 545
28.4.1 中间镀层法的电镀工艺流程 545
28.4.2 镀前处理 545
28.4.3 中间镀层 545
28.5 粉末冶金件直接电镀 546
28.5.1 电镀工艺流程 546
28.5.2 镀前处理 546
28.5.3 阳极黑色氧化 546
28.5.4 粉末冶金件直接氧化发黑 546
第29章 塑料电镀 548
29.1 概述 548
29.1.1 塑料电镀的特点 548
29.1.2 电镀塑料材料的选择 549
29.2 塑料电镀件的设计要求 549
29.3 塑料电镀件的成型工艺的要求 549
29.4 各种塑料的热变形温度 550
29.5 塑料镀前处理可选用的有机溶剂 550
29.6 塑料电镀的工艺流程 551
29.7 ABS塑料的电镀 551
29.7.1 消除内应力 551
29.7.2 除油 552
29.7.3 粗化 553
29.7.4 中和或还原 556
29.7.5 敏化 556
29.7.6 活化 556
29.7.7 还原和解胶 559
29.7.8 化学镀 560
29.7.9 电镀 562
29.7.10 ABS塑料直接电镀工艺 562
29.8 其他塑料的电镀 563
29.8.1 热塑性聚丙烯(PP)塑料的电镀 563
29.8.2 聚四氟乙烯(PTFE)的电镀 564
29.8.3 聚酰胺(尼龙)的电镀 565
29.8.4 酚醛(PF)塑料的电镀 565
29.8.5 环氧塑料及环氧玻璃钢的电镀 566
29.8.6 聚氯乙烯(PVC)的电镀 566
29.8.7 聚乙烯(PE)的电镀 567
29.8.8 聚甲基丙烯酸甲酯(PMMA)的电镀 568
29.8.9 聚砜(PSF)的电镀 568
29.9 不合格镀层的退除 569
第5篇 化学镀 570
第30章 化学镀镍 570
30.1 概述 570
30.2 化学镍镀层的性能 571
30.3 化学镀Ni-P合金 573
30.3.1 化学镀Ni-P合金的基本原理 573
30.3.2 化学镀Ni-P合金的分类 574
30.3.3 镀液组成及工艺规范 575
30.3.4 镀液组分及工艺规范的影响 579
30.3.5 脉冲化学镀Ni-P合金 582
30.4 化学镀Ni-B合金 583
30.4.1 概述 583
30.4.2 硼氢化钠镀Ni-B合金溶液 583
30.4.3 氨基硼烷镀Ni-B合金溶液 584
30.5 联氨(肼)作为还原剂的化学镀镍 586
30.6 化学镀镍工艺 587
30.6.1 高催化活性金属的化学镀镍 587
30.6.2 有催化活性金属的化学镀镍 587
30.6.3 非催化活性金属的化学镀镍 588
30.6.4 有催化毒性金属的化学镀镍 588
30.7 化学镀镍的后处理 588
30.8 不合格化学镀镍层的退除 590
30.9 化学镀镍基多元合金 590
30.9.1 化学镀Ni-W-P合金 590
30.9.2 化学镀Ni-Co-P合金 591
30.9.3 化学镀Ni-Cu-P合金 592
30.9.4 化学镀Ni-Mo-P合金 593
30.9.5 化学镀Ni-Sn-P合金 593
30.9.6 化学镀Ni-Fe-P合金 594
30.9.7 化学镀Ni-Cr-P合金 594
30.9.8 化学镀Ni-Re-P合金 595
30.9.9 化学镀Ni-P-B合金 595
30.9.10 化学镀Ni-W-B合金 595
第31章 化学镀铜和镀锡 597
31.1 化学镀铜 597
31.1.1 概述 597
31.1.2 化学镀铜基本原理 597
31.1.3 非甲醛化学镀铜溶液的种类 599
31.1.4 化学镀铜的溶液组成及工艺规范 599
31.1.5 各组分的作用和工艺规范的影响 602
31.1.6 化学铜镀层的后处理 604
31.1.7 不合格化学铜镀层的退除 605
31.2 化学镀锡 606
31.2.1 概述 606
31.2.2 浸镀锡(置换法) 606
31.2.3 化学镀锡(还原法) 608
第32章 化学镀银和镀金 610
32.1 化学镀银 610
32.1.1 概述 610
32.1.2 化学镀银溶液的组成和种类 610
32.1.3 甲醛化学镀银 611
32.1.4 酒石酸盐化学镀银 612
32.1.5 葡萄糖化学镀银 612
32.1.6 肼盐化学镀银 613
32.1.7 喷淋(镀)化学镀银 613
32.1.8 浸镀银(置换法) 614
32.2 化学镀金 615
32.2.1 概述 615
32.2.2 化学镀金溶液的组成 615
32.2.3 硼氢化物化学镀金 615
32.2.4 次磷酸盐化学镀金 616
32.2.5 肼盐化学镀金 617
32.2.6 二甲基氨基硼烷化学镀金 617
32.2.7 置换法浸镀金 618
32.2.8 无氰化学镀金 618
32.2.9 化学镀镍/置换镀金工艺 620
第33章 化学镀钯、铑、铂和钴 622
33.1 化学镀钯 622
33.1.1.概述 622
33.1.2 次磷酸盐化学镀钯 622
33.1.3 肼液化学镀钯 623
33.1.4 硼烷化学镀钯 624
33.1.5 不合格化学钯镀层的退除 624
33.2 化学镀铑 624
33.3 化学镀铂 625
33.4 化学镀钴及钴合金 625
33.4.1 概述 625
33.4.2 次磷酸盐化学镀钴 626
33.4.3 硼氢化钠化学镀钴 626
33.4.4 二甲基氨基硼烷化学镀钴 627
33.4.5 肼盐化学镀钴 627
33.4.6 化学镀钴基三元合金 628
第6篇 特种镀层镀覆工艺 630
第34章 刷镀 630
34.1 概述 630
34.1.1 刷镀作业系统装置 630
34.1.2 刷镀工艺特点和适用范围 630
34.2 镀笔(阳极) 632
34.2.1 镀笔的结构形式 632
34.2.2 阳极形状和材料 633
34.2.3 阳极包裹材料 634
34.3 刷镀电源 635
34.4 刷镀的镀层选择 637
34.5 刷镀的溶液种类 637
34.6 刷镀的预处理 638
34.6.1 电化学除油(电净) 638
34.6.2 活化 639
34.7 刷镀单金属 640
34.7.1 刷镀镍 641
34.7.2 刷镀铜 642
34.7.3 刷镀铁 643
34.7.4 刷镀锡 643
34.7.5 刷镀其他金属 644
34.8 刷镀合金 645
34.9 刷镀耐磨复合镀层 646
34.10 工艺规范及操作条件 647
34.10.1 镀液温度和工件温度 647
34.10.2 刷镀电压 647
34.10.3 阴阳极相对运动 647
34.10.4 被镀表面润湿状态 648
34.10.5 耗电系数 648
34.11 刷镀层的安全厚度 648
34.12 刷镀工艺流程 648
34.12.1 单一镀层的刷镀工艺流程 648
34.12.2 复合镀层的刷镀工艺流程 649
34.13 刷镀的有关计算 650
34.13.1 阴阳极相对运动速度的计算 650
34.13.2 刷镀溶液用量的估算 650
34.13.3 刷镀的电量、厚度、时间等的计算 650
第35章 复合电镀和化学复合镀 652
35.1 概述 652
35.1.1 复合镀常用的固体微粒 652
35.1.2 复合镀层的类型和应用 654
35.2 复合电镀的共沉积过程 654
35.3 复合电镀的工艺方法 655
35.4 防护与装饰性复合镀层 656
35.4.1 镍封镀层 656
35.4.2 缎面镍镀层 657
35.4.3 锌(锌合金)耐腐蚀复合镀层 658
35.5 耐磨性复合镀层 659
35.5.1 镍基耐磨复合镀层 660
35.5.2 铬基耐磨复合镀层 661
35.5.3 钴基耐磨复合镀层 662
35.5.4 铜基耐磨复合镀层 663
35.6 自润滑复合镀层 663
35.6.1 镍基自润滑复合镀层 664
35.6.2 铜基自润滑复合镀层 665
35.6.3 其他自润滑复合镀层 665
35.7 用于电接触材料的复合镀层 666
35.7.1 铜基电接触材料的复合镀层 666
35.7.2 银基电接触材料的复合镀层 667
35.7.3 金基电接触材料的复合镀层 667
35.8 高温耐磨与抗氧化的复合镀层 668
35.9 化学复合镀 669
35.9.1 化学镀耐磨复合镀层 669
35.9.2 化学镀自润滑复合镀层 670
35.9.3 化学镀其他复合镀层 671
35.10 不合格复合镀层的退除 672
第36章 脉冲电镀 674
36.1 概述 674
36.1.1 脉冲电镀的基本原理 674
36.1.2 脉冲电镀的特点 675
36.2 脉冲参数的选择 675
36.3 脉冲电镀电源 676
36.4 脉冲电镀单金属 678
36.4.1 脉冲镀锌 678
36.4.2 脉冲镀镍 678
36.4.3 周期换向脉冲镀铜 679
36.4.4 脉冲镀铬 679
36.4.5 脉冲镀银 680
36.4.6 脉冲镀金 681
36.4.7 脉冲镀钯和镀铂 682
36.4.8 不对称交流低温镀铁 683
36.5 脉冲电镀合金 683
36.5.1 脉冲电镀Zn-Ni合金 683
36.5.2 脉冲电镀铜基合金 684
36.5.3 脉冲电镀镍基合金 684
36.5.4 脉冲电镀其他二元合金 685
36.6 脉冲电镀耐磨复合镀镍 686
第37章 电铸 688
37.1 概述 688
37.2 电铸的基本要求 688
37.3 电铸用的芯模 689
37.3.1 芯模的类型和材料 689
37.3.2 电铸前芯模的预处理 691
37.4 电铸工艺 693
37.5 常用的电铸层材料 694
37.5.1 电铸铜 694
37.5.2 电铸镍 696
37.5.3 电铸铁 699
37.5.4 电铸Ni-Co合金 700
37.5.5 电铸Ni-Fe合金 700
37.5.6 电铸Ni-Mn合金 701
第7篇 金属转化处理工艺 702
第38章 钢铁的氧化处理 702
38.1 概述 702
38.2 钢铁碱性化学氧化 702
38.2.1 钢铁碱性化学氧化的成膜机理 702
38.2.2 化学氧化的溶液组成及工艺规范 703
38.2.3 溶液组成及工艺规范的影响 704
38.2.4 碱性化学氧化的后处理 705
38.3 钢铁酸性化学氧化 705
38.3.1 钢铁酸性化学氧化的成膜机理 705
38.3.2 酸性化学氧化的溶液组成及工艺规范 706
38.3.3 酸性化学氧化的工艺流程 707
38.4 不锈钢的化学氧化 707
38.4.1 不锈钢的黑色化学氧化 707
38.4.2 不锈钢的彩色化学氧化 708
38.4.3 不锈钢的钝化处理 709
38.4.4 不锈钢化学氧化的工艺流程 709
38.5 不合格氧化膜的退除 710
第39章 钢铁的磷化处理 711
39.1 概述 711
39.1.1 磷化处理的分类 711
39.1.2 磷化膜的用途 713
39.2 钢铁磷化的成膜机理 714
39.3 高温磷化处理 715
39.4 中温磷化处理 716
39.5 低温、常温磷化处理 718
39.6 黑色磷化处理 722
39.7 磷化液成分及工艺规范的影响 723
39.8 钢铁其他磷化处理 724
39.9 钢铁磷化工艺流程 726
39.10 不合格磷化膜的退除 728
第40章 铝和铝合金的氧化处理 730
40.1 概述 730
40.2 铝和铝合金的化学氧化 730
40.2.1 概述 730
40.2.2 碱性化学氧化处理 730
40.2.3 酸性化学氧化处理 731
40.2.4 化学氧化后处理 733
40.3 铝和铝合金的阳极氧化 734
40.3.1 概述 734
40.3.2 阳极氧化的一般原理 734
40.3.3 铝阳极氧化膜的组成和结构 736
40.3.4 硫酸阳极氧化 737
40.3.5 硬质阳极氧化 741
40.3.6 铬酸阳极氧化 744
40.3.7 草酸阳极氧化 745
40.3.8 磷酸阳极氧化 747
40.3.9 瓷质阳极氧化 748
40.3.10 微弧氧化 750
40.4 阳极氧化膜的着色 753
40.4.1 概述 753
40.4.2 化学浸渍着色 755
40.4.3 电解整体着色 759
40.4.4 电解着色 760
40.5 阳极氧化膜的封闭处理 764
40.5.1 高温水合封孔(闭) 765
40.5.2 水解盐封闭 766
40.5.3 重铬酸盐封闭 766
40.5.4 常温封闭 767
40.6 不合格氧化膜的退除 768
第41章 镁合金的氧化处理 769
41.1 概述 769
41.2 镁合金的化学氧化 769
41.2.1 化学氧化的工艺规范 769
41.2.2 局部化学氧化 771
41.2.3 氧化膜填充处理 771
41.2.4 镁合金三价铬及无铬转化膜处理 771
41.3 镁合金的阳极氧化 773
41.3.1 阳极氧化的工艺规范 773
41.3.2 工艺操作和维护 774
41.4 镁合金微弧氧化 774
41.5 不合格氧化膜的退除 775
第42章 铜和铜合金的氧化处理 776
42.1 概述 776
42.2 铜和铜合金的化学氧化 776
42.2.1 过硫酸钾氧化 776
42.2.2 氨水氧化 777
42.2.3 高锰酸钾氧化 778
42.2.4 硫化钾氧化 779
42.3 铜和铜合金的阳极氧化 779
42.4 铜和铜合金的化学钝化 780
42.5 铜和铜合金的化学着色 781
42.6 不合格氧化膜及钝化膜的退除 785
第43章 钛和钛合金的氧化处理 786
43.1 概述 786
43.2 钛和钛合金的化学氧化 786
43.3 钛和钛合金的阳极氧化 787
43.4 钛和钛合金的微弧氧化 787
43.5 钛和钛合金的着色 788
第8篇 镀层及镀液性能测试 789
第44章 镀层性能测试 789
44.1 概述 789
44.2 外观检测 789
44.2.1 检测方法和结果表示 789
44.2.2 表面缺陷、覆盖完整性和色泽检测 790
44.3 光泽性检测 791
44.4 镀层厚度的测定 793
44.4.1 磁性测厚仪测定法 793
44.4.2 涡流测厚仪测定法 795
44.4.3 分光束显微测定法 796
44.4.4 X射线光谱测定法 797
44.4.5 β射线反向散射法 799
44.4.6 化学溶解法 800
44.4.7 阳极溶解库仑法 801
44.4.8 金相显微镜法 806
44.4.9 扫描电子显微镜法 807
44.4.10 轮廓仪法 808
44.4.11 干涉显微镜法 809
44.4.12 计时液流法和计时点滴法 809
44.4.13 镀层厚度测定方法的选择 809
44.5 镀层结合强度的测定 810
44.5.1 镀层结合强度的定性检测方法 811
44.5.2 镀层结合强度的定量检测方法 813
44.5.3 适用于测定各种金属镀层结合强度的试验方法 813
44.6 镀层孔隙率的测定 814
44.6.1 贴滤纸测定法 814
44.6.2 浸渍测定法 816
44.6.3 气体测定法 817
44.6.4 电图像测定法 818
44.7 镀层硬度检测 818
44.7.1 锉刀硬度测定法 818
44.7.2 显微硬度测定法 819
44.8 镀层耐磨性能试验 821
44.9 镀层内应力的测试 823
44.9.1 弯曲阴极法 823
44.9.2 刚性平带法 824
44.9.3 螺旋收缩仪法 824
44.9.4 电阻应变仪测量法 825
44.9.5 电磁测定法 825
44.10 脆性的测试 825
44.10.1 杯突测定法 826
44.10.2 静压挠曲法 827
44.11 韧性的测试 828
44.12 延展性的测试 828
44.12.1 剥离镀层(镀层箔)的测试方法 829
44.12.2 连着基体的镀层测试方法 830
44.12.3 镀层延展性测试方法的选择 831
44.13 氢脆的测定 832
44.13.1 延迟破坏试验 832
44.13.2 缓慢弯曲试验 833
44.13.3 挤压试验 834
44.13.4 应力环试验 834
44.14 镀层表面粗糙度的测定 835
44.14.1 样板对照法 835
44.14.2 轮廓仪测量法 835
44.14.3 非接触式检测法 835
44.14.4 印模检测法 836
44.15 镀层钎焊性的测试 836
44.15.1 流布面积法 836
44.15.2 润湿时间法 836
44.15.3 蒸汽考验法 836
44.15.4 焊料润湿覆盖法 836
44.15.5 槽焊法 837
44.15.6 球焊法 837
44.15.7 钎焊性的检测仪器 837
44.16 金属镀层表面接触电阻的测定 839
44.16.1 电桥法 839
44.16.2 伏安法 839
44.16.3 印制板金属化孔镀层电阻的测定 839
44.17 镀层耐蚀性试验 840
44.17.1 概述 840
44.17.2 大气腐蚀试验 840
44.17.3 储存条件下的腐蚀试验 843
44.17.4 天然海水腐蚀试验 844
44.17.5 人工加速腐蚀试验——盐雾试验 845
44.17.6 腐蚀膏腐蚀试验(CORR试验) 849
44.17.7 盐溶液周浸腐蚀试验 850
44.17.8 二氧化硫腐蚀试验 853
44.17.9 硫化氢腐蚀试验 855
44.17.10 电解腐蚀试验(EC试验) 857
44.17.11 湿热试验 858
44.17.12 金属镀层经腐蚀试验后耐蚀性的评定 861
第45章 转化膜性能测试 864
45.1 概述 864
45.2 外观检测 864
45.3 厚度的测定 866
45.3.1 铝合金件阳极氧化膜厚度的测量 866
45.3.2 磷化膜质量的测量 867
45.4 耐磨性试验 868
45.4.1 耐磨耗试验法 868
45.4.2 落砂试验法 868
45.4.3 喷磨试验法 869
45.5 铝及铝合金阳极氧化膜其他性能试验 869
45.5.1 阳极氧化膜封孔质量的评定 869
45.5.2 铝及铝合金阳极氧化膜连续性的测定 870
45.5.3 铝及铝合金阳极氧化膜绝缘性的测定 871
45.5.4 铝及铝合金阳极氧化膜耐晒度的试验 871
45.5.5 铝及铝合金阳极氧化膜耐紫外光性能的测定 872
45.6 锌、镉镀层上铬酸盐转化膜试验方法 872
15.6.1 无色铬酸盐转化膜的测定 872
45.6.2 铬酸盐转化膜中六价铬的测定 872
45.6.3 铬酸盐转化膜中单位面积上六价铬含量的测定 873
45.6.4 铬酸盐转化膜中单位面积上总铬量的测定 873
45.6.5 有色铬酸盐转化膜附着力试验 873
45.6.6 铬酸盐转化膜单位面积上膜层质量的测定 873
45.6.7 铬酸盐转化膜的耐腐蚀性试验 874
45.7 耐蚀性试验 875
45.7.1 钢铁的氧化膜、磷化膜耐蚀性的测定 875
45.7.2 铝合金氧化膜耐蚀性的测定 875
45.7.3 镁合金氧化膜耐蚀性的测定 876
第46章 镀液性能测试 877
46.1 概述 877
46.2 pH值的测定 877
46.2.1 pH试纸测定 877
46.2.2 pH计测定 877
46.3 电导率的测定 879
46.4 电流效率的测定 881
46.5 镀液分散能力的测定 882
46.5.1 远近阴极测定法 882
46.5.2 弯曲阴极测定法 883
46.5.3 霍尔槽测定法 883
46.6 镀液覆盖能力的测定 884
46.6.1 直角阴极测定法 884
46.6.2 平行阴极测定法 884
46.6.3 管形内壁测定法 885
46.6.4 凹穴测定法 885
46.7 整平能力的测定 886
46.7.1 假正弦波测定法 886
46.7.2 V形沟槽测定法 886
46.7.3 粗糙度测定法 887
46.8 极化曲线的测试 887
46.8.1 概述 887
46.8.2 恒电流测定法 887
46.8.3 恒电位测定法 888
46.8.4 电化学分析仪测定法 889
46.9 表面张力的测定 890
46.9.1 最大气泡压力法 890
46.9.2 液滴测定法 891
46.10 霍尔槽试验 891
46.10.1 概述 891
46.10.2 霍尔槽结构及试验装置 892
46.10.3 霍尔槽阴极上的电流分布 892
46.10.4 霍尔槽试验方法 894
46.10.5 改进型霍尔槽 895
第9篇 污染治理及职业安全卫生 897
第47章 电镀清洁生产 897
47.1 概述 897
47.2 清洁生产的基本概念 897
47.2.1 清洁生产的定义 897
47.2.2 清洁生产与传统污染控制的比较 898
47.2.3 清洁生产的目标及技术方法 898
47.2.4 清洁生产审核 899
47.3 电镀清洁生产标准 899
47.4 实现电镀清洁生产的主要途径 903
47.5 实现电镀清洁生产所采取的措施 903
47.5.1 淘汰、限制重污染的化学品和生产工艺 904
47.5.2 替代电镀工艺或镀层 905
47.5.3 采用低温、低浓度处理工艺 905
47.5.4 前处理清洁生产工艺 906
47.5.5 提高资源综合利用率及降低能源消耗 906
47.6 加强企业管理和环境管理 906
47.7 搞好电镀车间设计 907
第48章 电镀节能减排 908
48.1 概述 908
48.2 电镀节能减排的基本原则 908
48.3 节电技术措施 910
48.4 节热及节气技术措施 911
48.5 电镀节水技术 911
48.5.1 改进清洗水槽的进水方式 911
48.5.2 喷淋清洗和喷雾清洗 912
48.5.3 多级逆流清洗 912
48.5.4 逆流清洗闭路循环系统 912
48.5.5 其他节水技术 913
48.6 电镀减排技术 913
48.6.1 采用无毒或低毒工艺 913
48.6.2 采用低浓度处理工艺 914
48.6.3 减少镀液带出量的措施 914
48.6.4 收回物料,减少排放 914
48.7 加强电镀生产过程管理 915
第49章 电镀“三废”处理 917
49.1 概述 917
49.1.1 电镀“三废”处理技术的确定和选用原则 917
49.1.2 电镀生产的主要污染物 917
49.2 废水处理 918
49.2.1 基本规定和要求 918
49.2.2 废水收集、水量和水质确定 919
49.2.3 废水处理方法 921
49.2.4 含铬废水处理 922
49.2.5 含氰废水处理 926
49.2.6 含镉废水处理 929
49.2.7 混合废水处理 931
49.3 废气处理 936
49.3.1 粉尘废气净化处理 937
49.3.2 铬酸废气净化处理 938
49.3.3 酸废气净化处理 940
49.3.4 氰化物废气净化处理 944
49.3.5 有机溶剂废气净化处理 944
49.4 废液、废渣及污泥的治理 945
49.4.1 废液处理和回收利用 946
49.4.2 废渣处置和利用 949
49.4.3 电镀污泥回收利用 949
49.4.4 电镀污泥无害化处理 952
第50章 职业安全卫生 954
50.1 概述 954
50.2 电镀行业职业危害因素 955
50.3 前处理作业安全卫生 956
50.3.1 机械前处理作业安全卫生 956
50.3.2 化学前处理作业安全卫生 956
50.4 电镀及化学处理作业安全卫生 957
50.4.1 槽液配制作业安全卫生 957
50.4.2 氰化电镀作业安全卫生 958
50.4.3 钢铁件氧化处理及其他作业安全卫生 958
50.5 操作人员的个人防护 959
50.6 电镀生产装置作业安全卫生 959
50.7 防机械伤害及噪声控制 960
50.8 危险化学品使用和储存的作业安全 960
50.9 安全卫生管理 961
参考文献 962
附录 963
附录A金属及其他无机覆盖层表面处理术语(GB/T 3138—2015) 963
附录B电镀污染物排放标准(引自GB 21900—2008) 978
附录C电镀行业标准及相关标准 983