图书介绍
铝塑型材挤压成形技术pdf电子书版本下载
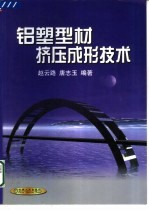
- 赵云路,唐志玉编著 著
- 出版社: 北京:机械工业出版社
- ISBN:7111013255
- 出版时间:2000
- 标注页数:320页
- 文件大小:15MB
- 文件页数:331页
- 主题词:
PDF下载
下载说明
铝塑型材挤压成形技术PDF格式电子书版下载
下载的文件为RAR压缩包。需要使用解压软件进行解压得到PDF格式图书。建议使用BT下载工具Free Download Manager进行下载,简称FDM(免费,没有广告,支持多平台)。本站资源全部打包为BT种子。所以需要使用专业的BT下载软件进行下载。如 BitComet qBittorrent uTorrent等BT下载工具。迅雷目前由于本站不是热门资源。不推荐使用!后期资源热门了。安装了迅雷也可以迅雷进行下载!
(文件页数 要大于 标注页数,上中下等多册电子书除外)
注意:本站所有压缩包均有解压码: 点击下载压缩包解压工具
图书目录
第1章 概论 1
1.1 铝塑型材的应用 1
1.2 铝型材的加工 1
1.3 塑料型材成形技术 2
1.3.1 挤塑成形工艺过程 2
1.3.2 挤塑模功能与作用 2
1.3.3 挤塑模设计需考虑的问题 3
1.3.4 挤塑模设计程序 5
第2章 铝塑型材产品设计 6
2.1 概述 6
2.2 铝型材截面设计 6
2.3 挤塑型材设计 8
2.3.1 管材设计 9
2.3.2 异型材设计通则 14
2.3.3 共挤复合型材设计 15
3.1.2 挤压筒的加热方式 18
3.1.1 挤压筒的结构形式 18
3.1 挤压筒的优化设计 18
第3章 铝型材挤压工具的优化设计 18
3.1.3 挤压筒内套的结构 20
3.1.4 挤压筒与模具的配合方式 20
3.1.5 挤压筒尺寸 21
3.1.6 挤压筒的强度计算 27
3.1.7 挤压筒的装配 36
3.1.9 挤压筒的合理使用及修理 37
3.1.8 挤压筒衬套的更换 37
3.2 挤压轴的优化设计 39
3.2.1 挤压轴的结构形式 39
3.2.2 挤压轴的尺寸确定 39
3.2.3 挤压轴的强度校核 40
3.3 挤压(穿孔)针的优化设计 42
3.3.1 挤压针种类 42
3.3.2 挤压针的结构形式与尺寸 43
3.3.3 挤压针的强度校核 45
3.4.2 挤压垫的尺寸 48
3.4 挤压垫的优化设计 48
3.4.1 挤压垫的结构 48
3.4.3 挤压垫的强度校核 50
3.4.4 固定挤压垫的设计 50
第4章 铝型材挤压模具设计 55
4.1 铝型材挤压模具的结构要素与设计原则 55
4.1.1 模具结构要素的设计 55
4.1.2 模具外形尺寸及其标准化 56
4.1.3 模具设计时应考虑的因素 57
4.1.4 模具设计的原则与步骤 58
4.1.5 模具设计的技术条件及基本要求 59
4.1.6 工作带的标注方法 60
4.2 铝型材挤压模具的类型及组装形式 62
4.2.1 挤压工具分类 62
4.2.2 挤压模具分类及特点 62
4.2.3 挤压模具的组装方式 64
4.3.1 模具结构设计 66
4.3 实心铝型材挤压模具的优化设计 66
4.3.2 棒材挤压模的设计 68
4.3.3 实心型材模的设计 69
4.3.4 导流模的设计 73
4.3.5 保护模的设计 74
4.3.6 水冷模与氮冷模的设计 76
4.4 空心铝型材挤压模具的优化设计 78
4.4.1 无缝圆管挤压模的设计 78
4.4.2 平面分流组合模的设计 82
4.5 民用建筑铝型材挤压模具的优化设计 90
4.5.1 民用建筑铝型材的特点 90
4.1.2 民用建筑铝型材模具的设计特点 90
4.6 工业铝型材挤压模具的优化设计 95
4.6.1 阶段变截面型材模的设计 95
4.6.2 带肋壁板型材模的设计 99
4.6.3 宽展模的设计 103
5.1 挤压型材用铝及铝合金 105
第5章 铝型材挤压工艺参数及其优化分析 105
5.2 铝合金型材挤压工艺流程 110
5.3 铝型材挤压工艺参数的设计 110
5.3.1 挤压工艺参数的选择 110
5.3.2 挤压毛料尺寸的选择 115
5.3.3 挤压工艺举例 118
5.3.4 铸锭尺寸偏差及质量要求 121
5.3.5 挤压温度 121
5.3.6 挤压速度 124
5.3.7 铝合金挤压型材主要缺陷及其成因和处理方法 128
第6章 塑料型材挤塑成形及材料参数 135
6.1 概述 135
6.1.1 挤塑成形工艺过程 135
6.1.2 成形功能与作用原理 135
6.2 挤塑机及性能 136
6.2.1 螺杆特性 136
6.2.2 挤塑机产量 136
6.3.1 螺纹联接 139
6.3 联接器设计 139
6.3.2 螺钉联接 140
6.3.3 卡箍联接 141
6.4 栅板与滤网设计 141
6.4.1 栅板设计 141
6.4.2 滤网压降 142
6.4.3 过滤器设计 142
6.5 塑料材料特性参数 143
6.5.1 流变学数据 143
6.5.2 热力学数据 145
第7章 实心型材成形技术 147
7.1 概述 147
7.2 塑料棒材模设计 147
7.2.1 棒材模结构设计 147
7.2.2 棒材模参数确定 148
7.3.2 定型模设计要点 150
7.3.1 定型模结构设计 150
7.3 棒材定型模设计 150
7.4 塑料焊条模设计 151
第8章 塑料管材成形技术 153
8.1 概述 153
8.2 管材成形模设计 154
8.2.1 成形模结构 154
8.2.2 成形段长度 157
8.2.3 管材模结构参数 158
8.3 管材定型模设计 159
8.3.1 定径方法 159
8.3.2 定径套尺寸及材料 160
第9章 塑料异型材成形技术 162
9.1 概述 162
9.2 异型材挤塑模类型 163
9.2.1 孔板式挤塑模 163
9.2.2 多级式挤塑模 163
9.2.3 流线型挤塑模 164
9.3 异型材挤塑模结构设计 165
9.3.1 口模尺寸 165
9.3.2 模具结构参数 166
9.4 异型材定型模设计 167
9.4.1 异型材定型方法 167
9.4.2 定型模结构设计 169
9.5 设计实例 174
第10章 塑料薄膜吹塑成形技术 176
10.1 概述 176
10.2 吹膜机头设计 176
10.2.1 吹膜机头类型 176
10.2.2 结构与工艺参数 177
10.2.3 机头结构设计 178
10.3 冷却定型装置设计 182
10.3.1 设计要求 182
10.3.2 冷却风环 182
10.3.4 内冷装置 183
10.3.3 水冷装置 183
第11章 中空吹塑型坯模设计 186
11.1 概述 186
11.2 型坯模技术参数 186
11.2.1 成形段长度 186
11.2.2 环隙尺寸 186
11.2.3 压降估算 187
11.3 型坯模结构类型 187
11.4 储料缸设计 188
11.4.1 分离式储料缸 189
11.4.2 一体式储料缸 190
第12章 塑料板片材成形技术 191
12.1 概述 191
12.2 平缝模结构设计 191
12.3.1 T形流道设计 192
12.3 平缝模流道设计 192
12.3.2 鱼尾形流道设计 198
12.3.3 衣架式流道设计 204
12.3.4 螺杆分配式流道设计 209
12.4 自动调节式平缝模 210
12.4.1 热螺栓自动调节式平缝模 210
12.4.2 微机控制平缝挤塑模 210
第13章 线缆包覆成形技术 212
13.1 概述 212
13.2 线缆包覆模类型 212
13.2.1 挤压式包覆模 212
13.2.2 套管式包覆模 212
13.3 包覆模结构设计 213
13.3.1 芯模几何设计 213
13.3.5 口模形状设计 214
13.3.4 口模对中设计 214
13.4 芯模分配系统设计 214
13.3.2 流道锥角设计 214
13.3.3 导向锥间隙设计 214
13.4.1 圆柱形芯模分配系统尺寸 215
13.4.2 截锥形芯模分配系统尺寸 217
13.5 交联聚乙烯包覆模设计 220
14.2 共挤塑模结构类型 222
14.2.1 模外复合共挤模 222
14.1 概述 222
第14章 多层型材成形技术 222
14.2.2 模内复合共挤模 223
14.2.3 多层复合共挤模 223
14.2.4 可控型坯共挤模 224
14.3 多层共挤流动模拟分析 224
14.3.1 对称多层流压降近似计算 225
14.3.2 共挤流动数值解 226
14.3.3 共挤流道中的速度和温度场 228
14.3.4 多层流动的不稳定性 230
15.1.2 复合管材的应用 232
15.1.1 复合管材的特性 232
第15章 铝塑复合管材成形技术 232
15.1 概述 232
15.2 复合管材原材料 233
15.2.1 树脂 233
15.2.2 粘合剂 233
15.2.3 铝带 234
15.3 复合管材成形加工 234
15.3.1 性能指标 234
15.3.2 成形工艺与产品性能 235
15.3.3 复合模具设计 236
15.3.4 铝层焊接技术 238
15.4 复合管的安装 239
第16章 塑料网材单丝及造粒技术 241
16.1 塑料网材成形技术 241
16.1.1 塑料网的构成 241
16.1.2 挤网模具结构 241
16.2 单丝技术 242
16.2.2 喷丝板参数 243
16.2.1 喷丝模结构 243
16.3 塑料造粒技术 244
16.3.1 造粒工艺与操作条件 244
16.3.2 口模板设计 245
第17章 挤塑模加热与压力测量 246
17.1 概述 246
17.2 加热功率计算 246
17.3 加热方式选择 247
17.4 温度控制与调节 248
17.5 压力测量 249
第18章 挤塑模力学设计 250
18.1 概述 250
18.2 挤塑模设计基本原则 250
18.2.1 挤塑模结构设计原则 250
18.2.2 流道构型设计原则 251
18.3 圆形流道挤塑模力学设计 251
18.3.2 支架支撑强度校核 252
18.3.1 口模径向允许变形量 252
18.3.3 联接螺钉计算 254
18.4 平缝形流道挤塑模力学设计 255
18.4.1 口模板厚度计算 255
18.4.2 联接螺钉计算 258
18.4.3 衣架式挤塑模结构尺寸 258
19.1.2 拆卸与清理 260
19.1.1 操作人员素质 260
19.1 塑料挤塑模 260
第19章 挤塑模使用与维护 260
19.1.3 装配与维护 261
19.2 铝型材挤压模 261
19.2.1 实心型材挤压模的修正 261
19.2.2 空心型材挤压模的修正 264
19.2.3 与模具修正有关的其它问题 268
第20章 铝塑型材挤塑模结构设计实例 276
20.1 铝型材挤压模具 276
20.1.1 铝合金大型异形空心型材挤压模设计方案解析 276
20.1.2 典型铝合金型材挤压模设计方案分析 279
20.1.3 大悬臂半空心型材模设计方案分析 283
20.1.4 双孔平面分流模设计方案分析 285
20.2 铝型材悬臂模具设计 290
20.2.1 导料板保护悬臂 291
20.2.2 前室保护悬臂 292
20.2.3 稳定销保护悬臂 295
20.2.4 悬臂危险截面的增强措施 296
20.2.5 损坏悬臂的修复 296
20.2.6 遮盖模 297
20.2.7 连体模 298
20.2.8 替代模 299
20.2.9 模具强度的计算 299
20.3 塑料型材挤塑模 300
20.3.1 RPVC管材模及真空定型模 300
20.3.2 可调压力管材模 300
20.2.7 窗用异型材及其定型模 302
20.3.6 衣架式流道平缝模 302
20.3.5 双型坯挤塑模 302
20.3.4 波纹管材模 302
20.3.3 自增强复合管材模 302
20.3.8 双色板材挤塑模 304
20.3.9 中空异型材定型模 304
20.3.10 芯层发泡棒材挤塑模 304
20.3.11 菱形网材挤塑模 304
20.3.12 3层内复合吹膜机头 307
21.2 挤压模具的工作条件与材料选用 309
21.1 工模具在铝挤压生产中的特殊地位 309
第21章 模具材料选用及热处理 309
21.3 挤塑模具钢 312
21.4 挤压工模具钢热处理 312
21.4.1 5CrMnMo、5CrNiMo、5CrNiMoV钢热处理 312
21.4.2 3Cr2W8V钢热处理 313
21.4.3 H13(4Cr5MoSiV1)钢热处理 313
21.4.4 4Cr3Mo2V(QR080)钢热处理 316
参考文献 318