图书介绍
轻金属材料加工手册 下pdf电子书版本下载
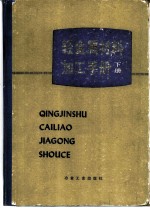
- 《轻金属材料加工手册》编写组编 著
- 出版社: 北京:冶金工业出版社
- ISBN:15062·3500
- 出版时间:1980
- 标注页数:893页
- 文件大小:51MB
- 文件页数:905页
- 主题词:
PDF下载
下载说明
轻金属材料加工手册 下PDF格式电子书版下载
下载的文件为RAR压缩包。需要使用解压软件进行解压得到PDF格式图书。建议使用BT下载工具Free Download Manager进行下载,简称FDM(免费,没有广告,支持多平台)。本站资源全部打包为BT种子。所以需要使用专业的BT下载软件进行下载。如 BitComet qBittorrent uTorrent等BT下载工具。迅雷目前由于本站不是热门资源。不推荐使用!后期资源热门了。安装了迅雷也可以迅雷进行下载!
(文件页数 要大于 标注页数,上中下等多册电子书除外)
注意:本站所有压缩包均有解压码: 点击下载压缩包解压工具
图书目录
第一节 概述 1
第二节 铝中气体的溶解及夹杂物和氧化膜的生成 1
目录 1
第五篇 轻合金熔炼与铸造 1
第一章 铝及铝合金的熔炼 1
一、铝中气体的溶解 2
二、非金属夹杂物及氧化膜的形成 6
三、金属杂质 8
一、熔体的氧化 9
第三节 熔体的氧化、烧损及其保护 9
三、熔体的保护 10
二、熔体的烧损 10
一、气体精炼法 11
第四节 铝及铝合金熔体的精炼和净化 11
二、熔剂精炼法 13
三、其它精炼方法 18
四、熔体的静置及过滤 19
五、熔体的精炼工艺 21
一、炉料及其组成 22
第五节 铝及铝合金的熔炼工艺 22
二、炉子准备 26
三、熔炼工艺过程 27
四、几种合金的熔炼特点 31
六、中间合金的生产 32
五、熔炼废品产生的原因及防止办法 32
七、废料的回收与复化 34
二、熔炼炉的类型及优缺点 36
一、对熔炼炉的基本要求 36
第六节 铝合金熔炼炉 36
三、火焰反射炉 37
四、感应式熔炼炉 41
五、电阻反射炉 45
一、铸锭的结晶 47
第一节 铸锭的结晶和组织 47
第二章 铝及铝合金的铸造 47
二、铸锭的结晶组织 55
三、疏松和偏析 62
二、铸造机 66
一、静置炉 66
第二节 铸造设备和工具 66
三、铸造工具 68
一、铸锭规格 76
第三节 铸锭工艺 76
二、铸造参数对铸锭质量的影响 77
三、铝及铝合金的铸造工艺 82
第四节 铝合金铸锭的水平连续铸造 93
一、电磁结晶槽的工作原理及结构 95
第五节 用电磁结晶槽的连续铸造 95
二、工艺要点及铸造过程 96
四、铸锭的表面和内部组织 97
三、铸锭的液穴形状和尺寸 97
六、铸锭的化学成分偏析 98
五、铸锭及加工制品的机械性能 98
一、铸锭的裂纹 99
第六节 铸锭缺陷 99
二、非金属夹杂物及氧化膜 104
三、金属间化合物 105
六、疏松 106
五、白斑 106
四、光亮晶粒 106
九、偏析浮出物 107
八、冷隔(或成层) 107
七、白点 107
十二、弯曲 108
十一、拉痕、拉裂 108
十、周期性波纹 108
二、铸锭的机械加工 109
一、铸锭的质量检查 109
十三、空心铸锭的偏心 109
第七节 铸锭的质量检查和机械加工 109
一、镁合金熔炼工艺概要 110
第一节 概述 110
第三章 变形镁合金的熔炼 110
二、镁合金的熔炼方法 111
一、镁与氧的相互作用 112
第二节 镁合金熔体与气体的相互作用 112
二、镁与氢的相互作用 113
五、氯气与镁及其合金组元的作用 115
四、镁与硫及SO2的相互作用 115
三、镁与氮的相互作用 115
二、镁合金熔剂的化学成分 116
一、对镁合金熔剂的要求 116
六、镁与B2O3的作用 116
第三节 熔剂、熔盐的选择和净化处理 116
三、熔剂净化效果的比较 117
四、镁合金熔剂用盐类的组成及性质 118
一、杂质的去除 121
第四节 镁合金中杂质的去除和变质处理 121
二、变质处理 122
一、镁合金的熔炼与精炼 123
第五节 镁合金的熔炼工艺 123
二、中间合金和熔盐的制备 127
三、废料复化 128
三、无铁芯工频感应电炉 129
二、坩埚炉 129
第六节 镁合金的熔炼设备 129
一、反射炉 129
二、镁合金锭的铸造方法 130
一、镁合金铸造的主要特点 130
第四章 镁合金的铸造 130
第一节 镁合金铸造的特点及方法 130
一、镁合金的铸造工艺制度 132
第二节 镁合金的铸造工艺 132
二、结晶槽和铸造漏斗 134
三、镁合金熔体的电磁搅动 135
四、保护气体——SO2 137
一、冷裂纹 139
第三节 镁合金的裂纹倾向性 139
二、热裂纹 140
第四节 镁合金铸锭的偏析 142
四、熔剂夹渣 143
三、带状气孔 143
第五节 镁合金铸锭的缺陷和废品 143
一、裂纹 143
二、冷隔 143
第六节 铸锭的机械加工 144
六、金属中间化合物 144
五、氧化夹杂 144
第七节 镁合金熔铸时的安全问题 145
第一节 概述 146
第五章 铝及铝合金板坯的连续铸轧 146
第二节 双辊下注式连续铸轧法 148
二、铸轧板坯的引出 150
一、连续铸轧工艺设计参数的选定 150
第三节 双辊下注式连续铸轧工艺 150
三、连续铸轧的工艺参数 151
二、铸轧机列 153
一、熔炼设备 153
第四节 铸轧设备及装置 153
三、浇铸系统 154
第五节 铸轧板坯的组织与性能 155
第六节 主要缺陷、废品的产生原因及消除方法 156
第一节 生产方法 157
第一章 生产方法及工艺流程 157
第六篇 板、带、箔材生产 157
第二节 工艺流程 158
第二章 轧制时的金属变形及轧制力计算 161
一、变形指数 162
第一节 轧制时的金属变形 162
二、变形区和咬人角 163
三、轧件的咬入条件 164
四、金属的流动 167
五、宽展 170
六、前滑 174
七、摩擦系数 178
八、变形速度 179
九、在压力加工状态下铝合金的塑性 180
十、轧制时的变形抗力 181
一、咬入弧上单位压力的分布 189
第二节 轧制力计算 189
二、轧制力的理论计算 194
三、轧制时的平均单位压力试验曲线 203
一、按单位能耗曲线确定电动机的力矩及功率 209
第三节 轧制时的力矩和功率计算 209
二、传动轧辊所需电机输出力矩的计算 210
三、轧制功及功率计算 217
一、考虑轧辊压扁和有张力时的平均单位压力计算 218
第四节 箔材轧制力计算 218
四、箔材轧制时的屈服强度 219
三、箔材轧制时的摩擦系数 219
二、箔材轧制时轧辊所承受的压力 219
五、箔材轧制力计算 220
二、铸锭的选择 221
一、热轧的主要特点 221
第三章 热轧 221
第一节 热轧的特点及铸锭选择 221
一、铸锭的铣面、铣边和蚀洗 223
第二节 轧前准备 223
二、铸锭和包铝板的蚀洗 225
三、铸锭的包铝和侧面包铝 226
二、合金的塑性图 229
一、合金的平衡相图 229
第三节 热轧制度的制定原则 229
五、热轧速度 232
四、变形抗力图 232
三、第二类再结晶图 232
六、加工率(压下量) 233
三、铸锭加热设备 234
二、铸锭轧制时的加热温度范围 234
第四节 铸锭的加热及温度范围 234
一、铸锭的加热要求 234
二、轧制制度 236
一、轧机的配置 236
第五节 轧机配置和轧制制度 236
第六节 热轧时的冷却和润滑 250
第七节 热轧辊型 252
第八节 热轧时的主要缺陷及消除办法 253
一、第一类再结晶图 254
第一节 制定冷轧制度的原则 254
第四章 冷轧 254
三、金属的塑性和道次加工率 255
二、轧制金属的性能和方向性 255
一、轧机的配置 256
二、冷轧轧制制度 256
四、轧制速度 256
第二节 轧机配置和压下制度 256
第三节 控制半硬制品机械性能的工艺方法 263
一、轧辊表面状态 264
第四节 冷轧时的辊型及其控制 264
二、辊型的选择和磨辊 265
三、辊型的配置方法 266
四、辊型的控制 267
第五节 带材轧制的张力 269
五、四重轧机辊型变化对板材与轧辊接触部分应力分布的影响 269
第六节 冷却和润滑 270
一、板带的测厚方法 273
第七节 板带的测厚与厚度自动控制 273
二、板带厚度的自动控制 274
第八节 冷轧的主要缺陷 275
第一节 中温轧制工艺概述 276
第五章 中温轧制 276
第二节 中温轧制制度 277
第三节 保证中温轧制顺利进行的几个主要条件 280
第六章 辊型 281
第一节 冷轧辊型挠度的计算 282
一、合适的轧制负荷 285
第三节 轧制负荷与辊型的关系及近似计算公式 285
第二节 轧件的最小允许宽度 285
二、轧制负荷对轧件断面尺寸的影响 287
三、轧制不同宽度轧件的合适负荷 288
第四节 热轧辊型的计算 290
四、近似计算公式 290
第五节 1700毫米二重式冷轧机辊型计算举例 292
第一节 变断面板材的轧制 294
第七章 几个特殊产品的轧制 294
第三节 双金属板的轧制 295
二、花纹板的轧制 295
第二节 壁板和花纹板轧制 295
一、壁板的轧制 295
第一节 卷材的剪切 296
第八章 精整 296
二、多辊矫直 298
一、滚平压光 298
第二节 板材的精整矫直 298
四、块片式精整机列 300
三、拉伸矫直 300
第五节 块片式精整方法产生的主要缺陷 301
第四节 板材检查、涂油和包装 301
第三节 卷材连续式热处理精整 301
一、发展概况 302
第一节 概述 302
第九章 铝箔生产 302
一、坯料准备和技术要求 303
第二节 箔材轧制 303
二、铝箔的用途 303
三、各国对铝箔厚度的划分 303
四、铝及铝合金箔材的生产工艺流程 303
二、纯铝箔材轧制工艺 306
三、高纯铝箔的生产 310
五、铝箔轧机 311
四、铝合金箔材的轧制工艺 311
一、控制箔材厚度的方法 314
第三节 箔材轧制时厚度的控制及测量 314
二、箔材厚度测量方法及测厚仪 316
第四节 箔材轧辊及辊型控制 319
一、对箔材轧辊的要求 320
二、轧辊的磨削 321
三、辊型控制 322
四、轧辊磨床 323
一、对箔材润滑剂的要求 324
第五节 箔材轧制用工艺润滑剂 324
三、常用工艺润滑剂 325
二、润滑剂特性 325
一、铝箔质量 326
第六节 铝箔的质量及其影响因素 326
二、影响铝箔质量的主要因素 327
一、箔材的合卷 331
第七节 箔材的合卷、分卷和清洗 331
三、箔材轧制时的缺陷及其产生原因 331
二、箔材的分卷 332
三、箔材的清洗 333
一、箔材的剪切 334
第八节 箔材精整 334
二、箔材的表面加工 336
三、箔材精整时所产生的缺陷 340
二、生产工艺流程 341
一、镁及镁合金变形的基本特征 341
第十章 镁及镁合金板材生产 341
第一节 镁及镁合金变形的基本特征及生产工艺流程 341
一、铸锭热轧前的准备 342
第二节 镁及镁合金厚板生产 342
二、热轧生产工艺 345
一、薄板生产方案 351
第三节 镁及镁合金薄板生产 351
二、板坯的加热 352
三、粗轧 353
四、中轧和精轧 354
五、叠轧 356
六、薄板常见的缺陷及消除方法 357
第四节 镁及镁合金轧制前轧辊的预热 358
二、轧辊的辊型 359
一、轧制时的冷却润滑 359
第五节 冷却润滑与轧辊辊型 359
第六节 镁及镁合金板材的成品退火 360
二、镁及镁合金的矫直 362
一、镁及镁合金的剪切 362
第七节 镁及镁合金板材的剪切与矫直 362
一、镁合金的酸洗 364
第八节 镁及镁合金板材的酸洗及防腐处理 364
二、镁合金的防腐处理 366
三、镁及镁合金板材涂油包装 371
二、正挤压和反挤压 373
一、挤压方法的分类 373
第七篇 型、棒、线材生产 373
第一章 生产方法及工艺流程 373
第一节 生产方法 373
三、挤压方法的优缺点 375
第二节 工艺流程 376
四、挤压生产的现状 376
二、挤压时金属的变形过程 381
一、挤压时金属的应力与变形 381
第二章 挤压时金属的变形及挤压力计算 381
第一节 挤压时金属的流动特点 381
一、弹性区 383
第二节 弹性区、缩尾、成层和挤压残料 383
二、缩尾和成层 384
一、挤压方法对金属流动的影响 388
第三节 影响金属流动的主要因素 388
三、挤压残料 388
四、挤压工具的影响 390
三、温度的影响 390
二、金属强度的影响 390
五、其它工艺参数的影响 391
二、粗晶环 392
一、挤压制品的组织 392
第四节 挤压制品的组织及性能 392
四、挤压效应 398
三、挤压制品的机械性能 398
第五节 挤压力的测定和计算 403
二、影响挤压力的主要因素 404
一、挤压力的实测方法 404
三、挤压力计算公式 405
二、铸锭尺寸的选择 416
一、品种、用途及生产方法 416
第三章 棒材及型材的挤压生产 416
第一节 棒材及普通型材的挤压工艺 416
三、铸锭的尺寸偏差及质量要求 423
四、挤压温度的选择 424
五、挤压速度的选择 426
六、工具准备 428
七、挤压制品的尺寸及表面控制 429
二、空心型材的挤压方法 430
一、品种和用途 430
第二节 空心型材的挤压生产 430
三、挤压工艺特点 432
二、阶段变断面型材的挤压方法 435
一、品种和用途 435
第三节 阶段变断面型材的挤压生产 435
三、挤压工艺特点 441
二、逐渐变断面型材的挤压方法 444
一、品种和用途 444
第四节 逐渐变断面型材的挤压生产 444
三、挤压工艺特点 446
四、其它工艺参数 447
二、壁板型材的挤压方法 448
一、品种和用途 448
第五节 壁板型材的挤压生产 448
三、壁板型材的挤压工艺 452
第六节 挤压生产中主要缺陷及废品的产生原因及消除方法 453
一、加热炉 455
第七节 挤压设备 455
二、挤压机 457
一、张力矫直 459
第一节 型、棒材的矫直 459
第四章 型、棒材的矫直、检查与包装 459
二、辊压矫直 461
三、压力矫直 465
四、手工矫直 466
二、取样 472
一、切头、尾 472
第二节 锯切及成品检查 472
四、成品检查 473
三、切成品 473
第三节 镁合金型、棒材的表面处理 474
一、木制包装箱的包装 475
第四节 挤压型、棒材的包装 475
第一节 模具 476
第五章 挤压工具设计 476
二、捆扎包装 476
一、棒材模具的设计 477
二、普通型材模具的设计 479
三、空心型材模具的设计 486
四、变断面型材模具设计 489
一、挤压轴尺寸的确定 494
第二节 挤压轴 494
二、挤压轴强度的校核 495
一、挤压筒的结构形式及尺寸规格 497
第三节 挤压筒 497
二、挤压筒的设计计算 498
三、挤压筒材料的选择 503
第四节 模支承、压型嘴及垫片 504
第五节 挤压工具用钢材 506
第一节 概述 508
第六章 线材生产 508
二、挤压线毛料 509
一、线毛料的生产方法和优缺点 509
第二节 线毛料的生产 509
三、轧制线毛料 510
四、铸造线毛料 512
一、实现拉伸的条件 514
第三节 线材拉伸基本原理 514
三、拉伸力计算 516
二、拉伸时的变形指标及其相互关系 516
一、铝合金线材拉伸特点 529
第四节 拉伸工艺 529
二、线毛料的准备 530
三、拉伸配模 531
四、润滑 534
一、拉伸工具 539
第六节 拉伸工具及设备 539
第五节 线材的缺陷种类及其产生原因 539
二、线材拉伸设备 545
三、线材拉伸的辅助设备 549
第一节 管材的品种规格及用途 553
第一章 生产方法及工艺流程 553
第八篇 管材生产 553
二、轻金属管材生产的特点 554
一、生产方法 554
第二节 管材的生产方法 554
二、管材变形指标计算 556
一、生产工艺制订步骤 556
第三节 生产工艺流程 556
三、工艺流程图 557
一、空心锭正向挤压 559
第一节 管材热挤压种类和金属流动特点 559
第二章 管材热挤压 559
二、全润滑挤压 560
三、穿孔挤压 562
五、组合模及舌形模挤压 564
四、反向挤压 564
一、管材挤压力的计算 566
第二节 挤压力和穿孔力 566
二、管材穿孔力的计算 567
三、作用于针上的前拽力计算 572
第三节 管材挤压工艺 573
一、铸锭的选择和技术标准 574
二、挤压温度 576
三、挤压速度 577
六、挤压操作技术要点及改进 578
五、润滑 578
四、挤压残料 578
第四节 挤压管材的尺寸偏差及表面质量 579
第五节 挤压管材的缺陷、废品种类及产生原因 581
一、挤压模 582
第六节 挤压工具和设备 582
二、挤压针 583
四、冲头(挤压残料分离器) 587
三、挤压垫片 587
第三章 冷挤压 589
二、挤压力计算 590
一、金属流动情况 590
第一节 金属流动情况和挤压力 590
一、冷挤压管材工艺流程 592
第二节 冷挤压生产工艺 592
三、挤压温度和速度 594
二、毛坯的准备 594
五、润滑 595
四、变形程度 595
二、冷挤压型、棒材的组织和性能 597
一、冷挤压管材的组织和性能 597
第三节 冷挤压制品的组织和性能 597
一、冷挤压工具 598
第四节 冷挤压用工具和设备 598
二、冷挤压设备 601
一、二辊式冷轧管(周期式) 603
第一节 管材轧制方法 603
第四章 管材轧制 603
二、多辊式冷轧管 605
三、多辊横向旋压管 606
四、横向三辊热轧管 608
一、二辊式轧管机轧制力计算 610
第二节 轧制力计算 610
二、多辊式轧管机轧制力计算 617
一、二辊式冷轧管机孔型设计 618
第三节 孔型设计 618
二、多辊式冷轧管机孔型设计 632
一、管毛料的准备 635
第四节 冷轧管工艺 635
二、冷轧管轧制工艺 636
三、冷轧管机的送料量 645
第五节 冷轧管的废品种类及其产生原因 647
四、冷轧管的润滑 647
一、二辊式冷轧管机的工具制造 649
第六节 冷轧管的工具制造 649
二、多辊式冷轧管机的工具制造 654
一、二辊式冷轧管机 657
第七节 轧管设备 657
四、横向三辊热轧轧管机 663
三、多辊横向旋压轧管机 663
二、多辊式冷轧管机 663
第五章 管材拉伸 667
一、无芯头拉伸(空拉) 668
第一节 管材拉伸方法 668
二、短芯头拉伸 670
三、游动芯头拉伸 671
五、拉伸扩径和压入扩径 672
四、长芯头拉伸 672
二、拉伸力计算 673
一、影响拉伸力的各种因素 673
第二节 拉伸力计算 673
一、管坯的准备 683
第三节 管材拉伸工艺 683
二、拉伸配模 685
二、整径模 699
一、拉伸模 699
第四节 管材拉伸时的废品种类及其产生原因 699
第五节 管材拉伸工具 699
三、芯头 701
第六节 管材拉伸设备 703
一、矫直 707
第一节 管材精整 707
第六章 管材的精整、检验和包装 707
二、锯切 710
二、成品管的检验 712
一、中间工序的检验 712
第二节 管材检验 712
第三节 管材成品包装 714
第一节 概述 715
第一章 生产方法和工艺流程 715
第九篇 锻压生产 715
二、自由锻和模锻生产方法的比较 716
一、水压机上锻造方法的分类 716
第二节 生产方法 716
三、水压机上比较常用的几种模锻方法 717
第三节 工艺流程 722
二、各类加工方法的特点 725
一、加工方法的分类 725
第二章 锻造和模锻的加工方法及热力学参数 725
第一节 锻造和模锻的加工方法 725
一、概述 730
第三节 锻造和模锻的热力学参数 730
第二节 铝、镁合金的加工特点 730
一、铝合金的加工特点 730
二、镁合金的加工特点 730
二、变形温度、变形速度和变形程度 732
一、概述 741
第二节 镦粗 741
第三章 自由锻造的基本工序及锻造工艺过程的拟订 741
第一节 概述 741
三、镦粗规则 744
二、镦粗过程工艺参数的计算方法 744
四、镦粗的主要方法 745
二、拔长过程工艺参数的计算方法 746
一、概述 746
第三节 拔长 746
四、平砧拔长对质量的影响 748
三、拔长规则 748
第四节 冲孔 750
第五节 在马架上扩孔(芯棒扩孔) 752
一、概述 753
第七节 锻造工艺过程的拟订 753
第六节 弯曲 753
二、锻件图的绘制 754
三、确定坯料的重量和尺寸 755
四、选择变形工艺及工具 756
第一节 概述 758
第四章 模锻件和模具的设计原理以及设备吨位的确定 758
五、确定工时定额 758
六、工艺卡片的编写 758
第二节 模锻件构造要素的确定 759
一、分模面 760
二、腹板厚度 761
三、模锻斜度 765
四、筋及圆弧半径 766
五、冲孔连皮及压凹 770
第三节 模锻件的余量和公差 776
一、余量 776
二、公差 776
三、模锻件的余量和公差计算举例 782
第四节 制订锻件图的其它问题 783
一、加工定位基准 783
二、测量硬度位置 783
三、确定性能试样的位置 783
四、印记位置 783
第五节 锻压设备的选择及其吨位的确定 784
一、锻压设备的选择 784
二、设备吨位的确定 784
一、终锻模膛的设计 789
第六节 终锻模膛和预锻模膛的设计 789
二、预锻模膛的设计 790
第七节 制坯工步的选择及坯料尺寸的确定 794
一、锻件的分类 794
二、饼类锻件制坯工步的选择及坯料尺寸的计算 795
三、杆类锻件工艺过程的制订及坯料的选择 796
第八节 制坯模膛(毛料模)的设计 800
一、水压机上的制坯模膛 800
第九节 模具装卡、锻模结构及模块标准 801
一、模具装卡 801
二、毛料模的设计 801
二、锻模结构 806
三、模块尺寸的确定和锻模标准 815
第一节 原坯料的种类 820
一、铸造坯料 820
第五章 锻造和模锻工艺 820
二、挤压坯料 822
三、轧制坯料 823
第三节 下料 824
二、坯料尺寸的确定 824
一、下料方法 824
二、圆锯下料 824
一、坯料的选择 824
第二节 原坯料的选择 824
第四节 加热及加热设备 825
一、坯料加热 825
三、定尺坯料的长度公差 825
二、模具加热 826
三、加热设备 827
一、概述 828
二、锻造方案 828
第五节 锻造工艺过程 828
四、获得均匀的锻件组织的方法 831
第六节 模锻工艺过程 831
三、锻造方案的选择 831
二、切边模的设计 833
一、切边方式及其特点 833
三、切边力的确定 833
第七节 切边 833
一、模膛润滑的目的及对润滑剂的要求 835
二、模膛润滑的方法 835
第八节 模膛的润滑 835
三、润滑剂的种类 836
二、蚀洗制度 837
一、表面清理的目的 837
三、修伤 837
第九节 模锻件及其中间坯料的表面清理和修伤 837
一、淬火 838
二、矫直 838
第十节 锻件的热处理及其矫直 838
第十一节 锻件检验及其主要缺陷和消除措施 839
一、锻件和模锻件的检查 839
三、时效 839
二、锻件和模锻件的主要缺陷及其消除措施 840
第十二节 典型工艺举例 842
一、自由锻工艺举例 842
二、模锻工艺举例 846
附录 856
附表 873