图书介绍
现代电子装联工艺过程控制pdf电子书版本下载
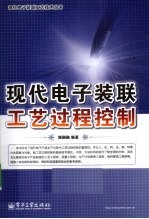
- 樊融融主编 著
- 出版社: 北京:电子工业出版社
- ISBN:9787121112966
- 出版时间:2010
- 标注页数:352页
- 文件大小:79MB
- 文件页数:366页
- 主题词:电子产品-装配-过程控制
PDF下载
下载说明
现代电子装联工艺过程控制PDF格式电子书版下载
下载的文件为RAR压缩包。需要使用解压软件进行解压得到PDF格式图书。建议使用BT下载工具Free Download Manager进行下载,简称FDM(免费,没有广告,支持多平台)。本站资源全部打包为BT种子。所以需要使用专业的BT下载软件进行下载。如 BitComet qBittorrent uTorrent等BT下载工具。迅雷目前由于本站不是热门资源。不推荐使用!后期资源热门了。安装了迅雷也可以迅雷进行下载!
(文件页数 要大于 标注页数,上中下等多册电子书除外)
注意:本站所有压缩包均有解压码: 点击下载压缩包解压工具
图书目录
第1章 现代电子装联工艺过程控制概论 1
1.1 工艺技术和工艺技术进步 1
1.2 工艺过程和工艺过程控制 3
1.3 工艺过程控制的要素和内容 4
1.3.1 工艺过程控制的要素 4
1.3.2 工艺过程控制的内容 4
1.3.3 控制项目和方法 7
1.3.4 数据和图表 8
1.3.5 产品生产与运营 9
1.4 SMT全过程控制和管理 10
1.4.1 概述 10
1.4.2 SMT全过程控制和管理 10
1.5 工艺过程控制中应注意的问题 13
1.5.1 要更多关注检测过程 13
1.5.2 动作和措施的执行 14
1.5.3 正确地分离变异原因 14
1.6 电子制造技术的发展 16
第2章 现代电子装联工艺过程的环境控制要求 18
2.1 现代电子装联工艺过程质量与环境 18
2.1.1 现代电子产品组装质量与环境的关系 18
2.1.2 DPMO与大气气候变化的统计关系 20
2.2 现代电子装联工艺过程对物理环境条件的要求 25
2.2.1 正常气象环境的定义 25
2.2.2 现代电子装联工艺过程对物理环境条件的要求 25
2.3 现代电子装联工作场地的静电防护要求 28
2.3.1 静电和静电的危害 28
2.3.2 电子产品制造中的静电 29
2.3.3 静电防护原理 30
2.3.4 静电监测仪器 30
2.3.5 现代电子装联工作场地的防静电技术指标要求 30
第3章 电子元器件、PCB及装联用辅料的互连工艺性控制要求 32
3.1 概述 32
3.2 电子元器件引脚(电极)用材料及其特性 32
3.2.1 对电子元器件引脚材料的技术要求 32
3.2.2 电子元器件引脚用材料 32
3.3 基体金属涂层的可焊性控制 35
3.3.1 可焊性 35
3.3.2 可焊性涂层的分类 35
3.3.3 可焊性镀层的可焊性评估 36
3.4 电子元器件引脚及PCB焊盘可焊性镀层的特性描述 37
3.5 电子装联工艺过程对PCB焊盘涂层及基材特性的控制要求 41
3.5.1 PCB焊盘涂层材料及特性 41
3.5.2 电子装联工艺过程对PCB基材特性的控制要求 45
3.6 常用电子元器件引脚镀层的典型结构 46
3.6.1 THT/THD类元器件引脚镀层结构 46
3.6.2 SMC/SMD类元器件引脚典型镀层结构 47
3.7 电子元器件引脚及PCB焊盘金属镀层的腐蚀(氧化) 52
3.7.1 金属腐蚀的定义 52
3.7.2 金属腐蚀的分类 53
3.8 引脚镀层可焊性的储存期控制 58
3.8.1 储存期对可焊性的影响 58
3.8.2 加速老化处理控制 59
3.9 电子元器件焊端镀层的可焊性试验 59
3.9.1 可焊性的定义 59
3.9.2 可焊性和可靠性 59
3.9.3 焊接过程中与可焊性相关的物理参数 60
3.9.4 可焊性测试 60
3.10 助焊剂、钎料和焊膏的组装工艺性控制 63
3.10.1 电子装联用助焊剂的工艺性控制要求 63
3.10.2 电子装联用钎料的工艺性控制要求 66
3.10.3 电子装联用焊膏的工艺性控制要求 68
3.10.4 如何选购和评估焊膏应用的工艺性 69
第4章 电子装联用元器件及辅料的全流程过程控制 71
4.1 通用元器件的全流程过程控制 71
4.1.1 通用元器件引线镀层耐久性要求 71
4.1.2 通用元器件的验收、储存及配送 71
4.2 潮湿敏感元器件全流程过程控制 72
4.2.1 名词定义 72
4.2.2 MSD的分类及SMT包装的分级 74
4.2.3 MSD的入库、储存、配送、组装工艺过程管理 77
4.3 静电敏感元器件全流程过程控制 81
4.3.1 定义、标识和分类 81
4.3.2 SSD入库、储存、配送和操作过程控制 84
4.4 温度敏感元器件全流程过程控制 87
4.4.1 术语定义和温度敏感元器件损坏模式 87
4.4.2 常见的温度敏感元器件 87
4.4.3 温度敏感元器件的入库、储存、配送和操作过程控制 88
4.5 PCB全流程过程控制 89
4.5.1 定义和分级 89
4.5.2 PCB的入库、储存、配送和操作过程控制 89
4.6 元器件引线、接线头、接线柱及导线可焊性控制 91
4.6.1 标准和分类 91
4.6.2 试验设备 92
4.6.3 试验方法 92
4.6.4 试验步骤 94
4.7 钎料、助焊剂的管理过程控制 98
4.7.1 引用标准 98
4.7.2 管理过程控制 98
4.8 焊膏的管理过程控制 100
4.8.1 标准及对焊膏管理的描述 100
4.8.2 焊膏管理过程的控制 101
4.9 SMT贴片胶全流程管理控制 104
4.9.1 标准、作用及性能要求 104
4.9.2 管理过程控制 105
4.10 电子装联用其他辅料的全程管理控制 106
4.10.1 UNDERFILL胶水 106
4.10.2 导热胶 107
第5章 电子装联生产线和线型工艺设计及控制 109
5.1 电子装联生产线概论 109
5.1.1 电子设备的制造过程 109
5.1.2 电子装联和电子装联生产线 109
5.2 电子装联工艺全过程控制和管理 110
5.2.1 电子装联工艺全过程控制驱动了工艺装备技术的发展 110
5.2.2 Ionics公司典型SMT生产线配置介绍 113
5.3 表面贴装组件(SMA)的生产流程 113
5.3.1 单块板PCB组装结构及生产流程 113
5.3.2 PCB拼板组装结构及生产流程 114
5.4 THT组装生产线体类型及其特点 118
5.4.1 目前流行的THT组装生产线体的类型 118
5.4.2 THT组装生产线体的流程参数设计和控制 119
5.5 SMT生产线体类型及其应用特点 121
5.5.1 SMT生产线体类型 121
5.5.2 适合于高密度组装的SMT生产线型 121
5.5.3 SMT组装生产线体的建线方案设计和控制 123
5.5.4 设备配置 124
5.6 电子产品制造中的静电防护 128
5.6.1 静电过载和静电释放损害的预防 128
5.6.2 EOS/ESD安全工作台/EPA 131
5.6.3 生产线设备防静电实例 132
5.7 5S管理 134
5.7.1 5S管理概述 134
5.7.2 5S管理的内容 135
5.7.3 5S实施和管理 138
第6章 现代电子装联工艺过程控制的技术基础和方法 140
6.1 现代电子装联工艺过程控制的特点 140
6.1.1 现代电子装联工艺过程控制概论 140
6.1.2 现代电子装联工艺过程控制的特点 140
6.1.3 精度与重复性的确定 140
6.2 现代电子装联工艺过程中所发生现象的规律性描述 141
6.2.1 随机事件 141
6.2.2 统计规律和概率 142
6.3 6σ与工艺过程控制 146
6.3.1 6σ在过程控制中的应用 146
6.3.2 过程符合6σ的能力 147
6.3.3 过程(工序)能力指数Cp 148
6.3.4 6σ在现代电子装联工艺过程控制中的应用 153
6.3.5 DPMO在电子装联板级组装中的应用 156
6.4 现代电子装联工艺过程控制中的统计过程控制(SPC) 160
6.4.1 SPC技术概述 160
6.4.2 SPC技术的内容 162
6.4.3 SPC控制图的原理、结构和作用 164
6.4.4 常用控制图介绍 167
6.4.5 控制图的修订和注意事项 171
6.4.6 SPC应用实例 172
第7章 元器件成型、插装及波峰焊接工艺过程控制 176
7.1 元器件成型的工艺过程控制 176
7.1.1 元器件成型的定义及其对产品生产质量的影响 176
7.1.2 元器件成型前的质量控制 176
7.1.3 元器件成型的基本参数要求 177
7.1.4 元器件成型设备 180
7.1.5 元器件成型的特殊问题——应力释放 187
7.1.6 元器件成型工艺过程控制 188
7.2 元器件在PCB上插装工艺过程控制 189
7.2.1 名词定义 189
7.2.2 插装的基本工艺要求 189
7.2.3 插装质量控制和目标 192
7.3 波峰焊接工艺窗口设计及其工艺过程控制 192
7.3.1 影响波峰焊接效果的四要素 192
7.3.2 无铅波峰焊接的工艺性问题 197
7.3.3 SMA波峰焊接的波形选择 197
7.3.4 波峰焊接工艺窗口设计 199
7.3.5 波峰焊接工艺过程控制 204
第8章 焊膏印刷模板设计、制造及印刷工艺过程控制 212
8.1 概述 212
8.2 焊膏印刷设备 212
8.2.1 焊膏印刷设备 212
8.2.2 选择焊膏印刷设备时应关注的问题 213
8.3 印刷模板设计的工艺性要求 213
8.3.1 模板设计的任务及应关注的问题 213
8.3.2 模板设计参数的控制要求 214
8.3.3 模板开孔侧壁的形态对焊膏释放的影响 219
8.3.4 焊盘面积的经验公式 221
8.4 模板加工技术对焊膏释放的影响 222
8.4.1 模板开孔形态对焊膏释放量的影响 222
8.4.2 模板制造技术及其对焊膏释放量的影响 222
8.5 焊膏的选择和参数控制 227
8.5.1 焊膏的选择 227
8.5.2 焊膏的应用环境要求 229
8.6 印刷用刮刀(刮板) 229
8.6.1 常用的刮刀(刮板)形式 229
8.6.2 刮刀的选用 230
8.6.3 金属刮刀的优点 231
8.6.4 刮刀结构形状对焊膏印刷中释放量的影响 231
8.7 焊膏印刷准备工序及印刷参数的选择和设定 232
8.7.1 焊膏印刷准备工序 232
8.7.2 印刷参数的选择和设定 234
8.8 焊膏印刷工艺过程控制 238
8.8.1 焊膏印刷工艺过程控制要素 238
8.8.2 焊膏印刷工艺过程控制方法 240
8.8.3 焊膏印刷工艺过程连续实时监测 243
8.8.4 保持PCB工艺文件的稳定性 243
8.9 焊膏印刷的质量控制要求及常见缺陷 244
8.9.1 焊膏印刷的质量控制要求 244
8.9.2 影响焊膏印刷不良的因素 245
8.9.3 焊膏印刷中常见的不良现象 248
8.9.4 印刷不良单板的处理 251
第9章 表面贴装工程及贴装工艺过程控制 252
9.1 表面贴装工程概述 252
9.1.1 表面贴装工程技术的发展及其特点 252
9.1.2 支撑SMA发展的元器件技术 252
9.2 现代封装技术的发展对贴装设备的适应性要求 257
9.2.1 高密度电路互连技术的发展对贴装机的精度要求 257
9.2.2 电子制造需求驱动了贴装设备技术不断创新 258
9.2.3 现代贴装设备的发展 259
9.3 贴装设备 260
9.3.1 常用的贴装机分类 260
9.3.2 典型机型简介 262
9.3.3 Multiflex线体 266
9.4 贴装机过程能力的验证 270
9.4.1 背景 270
9.4.2 贴装机过程能力的描述(IPC—9850简介) 271
9.4.3 期望的贴装机能力指数Cpk 272
9.5 贴装工艺质量要求 272
9.5.1 元器件贴装前的准备 272
9.5.2 贴装工艺质量要求 273
9.5.3 影响贴装质量的因素 276
9.6 元器件贴装工艺过程控制 278
9.6.1 元器件贴装工艺过程控制概述 278
9.6.2 贴装工序工艺过程控制 279
9.6.3 贴装工序工艺过程能力的测评及控制方法 280
9.7 在FPC上进行元器件贴装 280
第10章 SMT再流焊接工艺过程控制 282
10.1 再流焊接工艺要素分析 282
10.2 再流焊接温度曲线 284
10.2.1 再流焊接工艺过程中的温度特性 284
10.2.2 怎样设定再流焊接温度曲线 287
10.3 再流焊接工艺窗口设计 290
10.3.1 机器参数 290
10.3.2 过程记录参数 293
10.4 再流焊接工艺过程控制 293
10.4.1 再流焊接中需要控制的工艺要素 293
10.4.2 再流焊接工艺过程控制 293
10.5 再流焊接焊点质量的在线实时监控 295
10.5.1 再流焊点质量监控与工艺过程控制的相关性 295
10.5.2 如何评估再流焊点的完整性 295
10.5.3 再流焊点质量监控 296
10.5.4 在组装过程中对BGA器件焊点质量的监控 298
第11章 刚性印制背板组装互连技术及工艺过程控制 301
11.1 概述 301
11.1.1 刚性印制背板 301
11.1.2 刚性印制背板组装中所采用的接合、接续技术 303
11.2 压接技术 305
11.2.1 简介 305
11.2.2 压接连接机理 306
11.2.3 压接工艺过程控制 308
11.3 绕接技术 308
11.3.1 定义和应用 308
11.3.2 绕接的原理 309
11.3.3 绕接连接的可靠性 311
11.3.4 绕接的特点 313
11.3.5 绕接工艺 316
11.4 背板的波峰焊接 318
11.4.1 背板波峰焊接的难点 318
11.4.2 适合于背板波峰焊接的设备特点 319
第12章 电子组件防护与加固工艺过程控制 320
12.1 电子组件防护与加固工艺的内容 320
12.1.1 为什么要对电子组件进行防护加固 320
12.1.2 防护加固的目的和内容 326
12.2 防护加固的工艺措施及其控制 327
12.2.1 气候环境防护加固工艺措施 327
12.2.2 防热加固工艺措施 328
12.2.3 机械应力环境的防护加固工艺措施 329
12.2.4 无铅焊点在机械应力环境中的工艺可靠性问题 329
12.2.5 免清洗助焊剂在应用中的隐患 330
12.3 PCBA的防护与加固 332
12.3.1 敷形涂覆的目的和功能 332
12.3.2 常用的敷形涂层材料 333
12.3.3 对涂覆材料的要求 334
12.3.4 涂覆工艺环境的优化 334
12.3.5 敷形涂覆的工艺方法 335
12.3.6 敷形涂覆的典型工艺流程及应用中的工艺问题 336
12.3.7 多层涂覆 338
12.3.8 涂层质量要求 338
第13章 电子产品的可靠性和环境试验 339
13.1 电子产品的可靠性及可靠性增长 339
13.2 环境条件试验 339
13.3 气候、温度环境试验 341
13.3.1 高、低温度试验 341
13.3.2 温度冲击试验 341
13.3.3 低气压试验 341
13.3.4 湿热试验 342
13.3.5 霉菌试验 342
13.3.6 盐雾试验 343
13.4 力学环境试验 343
13.4.1 振动试验 343
13.4.2 加速度试验 344
13.4.3 冲击试验 344
13.4.4 模拟运输试验 344
13.4.5 真空试验 344
13.5 电子产品的老练 345
13.5.1 基本描述 345
13.5.2 常温老练 345
13.5.3 应力条件下的老练 346
13.6 表面组装焊点的失效分析和可靠性试验 346
13.6.1 概述 346
13.6.2 SMT焊点的可靠性和失效 346
13.6.3 统计失效分布概念 347
13.6.4 可靠性试验 347
13.6.5 其他试验 348
13.6.6 性能试验方法 348
13.6.7 无铅电子产品焊点的长期可靠性问题 351