图书介绍
金属材料制备工艺的计算机模拟pdf电子书版本下载
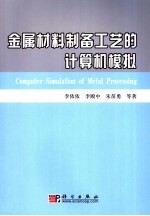
- 李依依,李殿中,朱苗勇等著 著
- 出版社: 北京:科学出版社
- ISBN:7030165985
- 出版时间:2006
- 标注页数:283页
- 文件大小:36MB
- 文件页数:294页
- 主题词:金属材料-制备-工艺学-计算机模拟
PDF下载
下载说明
金属材料制备工艺的计算机模拟PDF格式电子书版下载
下载的文件为RAR压缩包。需要使用解压软件进行解压得到PDF格式图书。建议使用BT下载工具Free Download Manager进行下载,简称FDM(免费,没有广告,支持多平台)。本站资源全部打包为BT种子。所以需要使用专业的BT下载软件进行下载。如 BitComet qBittorrent uTorrent等BT下载工具。迅雷目前由于本站不是热门资源。不推荐使用!后期资源热门了。安装了迅雷也可以迅雷进行下载!
(文件页数 要大于 标注页数,上中下等多册电子书除外)
注意:本站所有压缩包均有解压码: 点击下载压缩包解压工具
图书目录
1.1 材料制备工艺的基本概念和实例 1
1.1.1 材料制备工艺的基本概念 1
第一章 概论 1
1.1.2 钢铁生产工艺流程 2
1.1.3 我国钢铁工业的现状 7
1.2 材料制备工艺模拟的基本知识 8
1.2.1 材料模拟的基本概念 8
1.2.2 金属材料制备工艺的计算机模拟 14
1.2.3 工艺模拟的判据 15
1.3.1 铸造工艺模拟软件 16
1.3 材料制备工艺模拟常用软件 16
1.3.2 热轧带钢组织性能预报软件 18
1.3.3 塑性成形工艺模拟软件 20
参考文献 22
第二章 液态金属精炼过程的计算机模拟 23
2.1 金属熔体传输过程的基本方程与计算方法 23
2.1.1 描述金属熔体传输过程的基本方程 23
2.1.2 冶金反应器内金属熔体流场的计算方法 27
2.2.2 吹氩精炼钢包内气液两相区的描述 36
2.2 底吹氩精炼钢包内三维流动的计算机模拟 36
2.2.1 控制方程 36
2.2.3 三维数学模型的验证 38
2.2.4 单喷嘴喷吹钢包内流场模拟 40
2.2.5 多喷嘴喷吹钢包内流场模拟 41
2.3 浸入式喷枪喷吹金属熔池和AOD炉内三维流动的数值模拟 44
2.3.1 水平气体射流在液体中的行为特征 44
2.3.2 数学模型 45
2.3.3 浸入式喷枪喷吹熔池中的流动特征 46
2.3.4 AOD炉内的流动特征 47
2.4 液态金属熔池中的混合过程模拟 49
2.4.1 混合过程和混合时间的数理研究方法 49
2.4.2 精炼金属熔池混合过程的模拟分析 50
2.5 LF钢包精炼炉内夹杂物行为的计算机模拟 52
2.5.1 LF炉内夹杂物描述的理论模型 52
2.5.2 喷嘴布置对夹杂物去除的影响 54
2.6 RH真空精炼过程的计算机模拟 56
2.6.1 模型描述 56
2.6.2 RH真空装置内钢液的流动特征 58
2.6.3 RH真空精炼装置内钢液的循环流量 59
2.6.4 脱碳行为 60
2.6.5 脱碳的影响因素 61
参考文献 63
第三章 铸造工艺的计算机模拟 65
3.1 铸件充型及传热过程模拟 65
3.1.1 充型及传热过程的数理方程 66
3.1.2 充型及传热过程模拟 67
3.1.3 标准实验(benchmark test)的模拟 69
3.2.1 铸件凝固过程的三场耦合 70
3.2 铸件凝固过程中的三场耦合模拟与宏观偏析的定量预测 70
3.2.2 三场耦合模型 71
3.2.3 钢锭三场耦合的模拟计算 73
3.3 使用水平集方法模拟铸造双金属轧辊 75
3.3.1 冲洗法生产铸造双金属轧辊 75
3.3.2 数学模型 75
3.3.3 数值稳定性分析 76
3.3.4 计算结果与分析 76
3.4.2 铸钢支承辊充型过程的模拟 80
3.4 大型铸钢支承辊整体铸造工艺的计算机模拟 80
3.4.1 铸钢支承辊的整体铸造工艺 80
3.4.3 铸钢支承辊凝固过程模拟结果与分析 81
3.5 电磁离心铸造工艺模拟 84
3.5.1 电磁场、熔体流场和温度场的耦合 85
3.5.2 熔体流场与压力场模拟结果与分析 86
3.5.3 温度场的模拟结果与分析 88
3.5.4 电磁搅拌对离心铸造OCr17Mn14Mo2N不锈钢管坯显微组织的影响 89
参考文献 91
4.1.1 确定性方法 93
第四章 凝固过程微观组织模拟 93
4.1 凝固过程微观组织模拟方法 93
4.1.2 概率方法 95
4.1.3 相场方法 98
4.2 凝固过程数学模型 101
4.2.1 形核模型 101
4.2.2 晶体生长模型 104
4.3.1 元胞自动机与有限差分耦合 108
4.3 铸锭凝固过程中柱状晶与等轴晶的转变 108
4.3.2 模拟的基本步骤 110
4.3.3 铸锭凝固过程中柱状晶与等轴晶的转变 110
4.4 喷射成形中金属液滴凝固过程模拟 113
4.4.1 喷射成形中金属液滴凝固 113
4.4.2 模型的描述 114
4.4.3 液滴凝固过程模拟 116
参考文献 120
5.1 热轧带钢组织性能预报的基本模块 122
第五章 热轧带钢组织性能预报 122
5.2 板坯加热的奥氏体化过程及晶粒长大 123
5.2.1 板坯加热的奥氏体化过程 123
5.2.2 晶粒长大动力学参数的确定 125
5.3 轧制过程中的再结晶模拟 127
5.3.1 热轧温度模型 127
5.3.2 热形变过程中的再结晶 129
5.3.3 再结晶模型 132
5.3.4 热轧带钢再结晶的模拟 134
5.4 热轧带钢冷却过程的相变计算 135
5.4.1 热轧低碳钢冷却相变计算 136
5.4.2 卷取温度控制模型 140
5.4.3 计算结果与分析 142
5.5 铁素体晶粒尺寸预测 145
5.5.1 钢卷冷却过程的温度场模拟 145
5.5.2 铁素体晶粒尺寸模型 147
5.5.3 计算结果与分析 148
5.6 热轧带钢组织性能预报 150
5.6.1 物理冶金模型预报带钢性能 150
5.6.2 Rollan软件的应用 154
参考文献 156
第六章 奥氏体-铁素体转变的计算机模拟 158
6.1 等温奥氏体-铁素体相变的元胞自动机介观模拟 158
6.1.1 等温奥氏体-铁素体相变二维元胞自动机模型 158
6.1.2 等温奥氏体-铁素体相变元胞自动机模拟 163
6.2 等温相变过程中单个铁素体晶粒长大行为的模拟 170
6.2.1 等温相变过程中单个铁素体晶粒的长大模拟 170
6.2.2 单个铁素体晶粒的六种长大模式模拟 171
6.3.1 连续冷却奥氏体-铁素体相变元胞自动机模型 175
6.3 连续冷却奥氏体-铁素体相变元胞自动机模拟 175
6.3.2 连续冷却奥氏体-铁素体相变模拟 177
6.4 形变奥氏体-铁素体相变晶体塑性有限元-元胞自动机耦合模拟 183
6.4.1 晶体塑性形变模型 183
6.4.2 形变奥氏体-铁素体相变模型 186
6.4.3 晶体塑性有限元模型与元胞自动机模型的耦合 188
6.4.4 形变奥氏体-铁素体相变的晶体塑性有限元-元胞自动机耦合模拟结果 190
6.5 Fe-C二元系未形变奥氏体等温分解的蒙特卡罗法模拟 196
6.5.1 蒙特卡罗模型 197
6.5.2 单个晶粒中碳扩散过程的模拟 200
6.5.3 双晶粒体系中的等温奥氏体-铁素体相变模拟 203
6.5.4 未形变奥氏体等温分解过程中非平衡奥氏体-铁素体相界面状态的分析 206
6.5.5 未形变多晶奥氏体等温分解过程中奥氏体-铁素体相变模拟 212
6.6 Fe-C二元系等温热形变过程中形变诱导铁素体相变的蒙特卡罗法模拟 215
6.6.1 形变诱导铁素体相变 215
6.6.2 多态波茨模型 217
6.6.3 模拟结果与分析 221
6.7 深过冷轧制热力耦合有限元分析 235
6.7.1 钢板热轧过程界面换热系数的测定 236
6.7.2 热轧板表层超细晶形成过程分析 238
参考文献 242
第七章 塑性成形工艺模拟 246
7.1 体成形工艺模拟 246
7.1.1 体积成形工艺模拟 246
7.1.2 体积成形过程中的热力耦合模型 246
7.1.3 近β型钛合金的塑性成形过程模拟 247
7.1.4 NiTi形状记忆合金管件热挤压过程数值模拟 249
7.2.1 油底壳成形过程的三维有限元模拟 252
7.2 板材冲压成形过程的计算机模拟 252
7.2.2 镁合金板材筒形件拉深成形 261
7.2.3 板件液压成形 264
7.3 板成形回弹过程的计算机模拟 270
7.3.1 板成形回弹的计算方法及影响因素 270
7.3.2 汽车纵梁成形及回弹过程的模拟 272
参考文献 280
关键术语 281