图书介绍
微电子技术工程 材料、工艺与测试pdf电子书版本下载
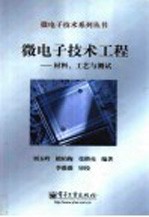
- 刘玉岭等编著 著
- 出版社: 北京:电子工业出版社
- ISBN:7120000217
- 出版时间:2004
- 标注页数:649页
- 文件大小:16MB
- 文件页数:665页
- 主题词:微电子技术
PDF下载
下载说明
微电子技术工程 材料、工艺与测试PDF格式电子书版下载
下载的文件为RAR压缩包。需要使用解压软件进行解压得到PDF格式图书。建议使用BT下载工具Free Download Manager进行下载,简称FDM(免费,没有广告,支持多平台)。本站资源全部打包为BT种子。所以需要使用专业的BT下载软件进行下载。如 BitComet qBittorrent uTorrent等BT下载工具。迅雷目前由于本站不是热门资源。不推荐使用!后期资源热门了。安装了迅雷也可以迅雷进行下载!
(文件页数 要大于 标注页数,上中下等多册电子书除外)
注意:本站所有压缩包均有解压码: 点击下载压缩包解压工具
图书目录
目录 1
第0章 绪论 1
0.1 微电子技术是社会信息化的基础 1
0.2 集成电路技术新发展 2
0.2.1 集成电路的分类 2
0.2.2 集成电路的发展趋势及其特点 3
0.2.3 微电子技术制造发展趋势 4
0.3 微电子技术新领域 7
0.3.1 微电子机械系统 7
0.3.2 纳米电子技术 8
0.3.3 超导微电子技术 9
0.3.4 有机微电子技术 10
参考文献 11
第1章 硅单晶材料的基本性质 13
1.1 硅半导体材料的物理性质 13
1.1.1 半导体的电子能带结构 13
1.1.2 半导体 15
1.1.3 硅单晶的光学性质 20
1.1.4 硅单晶的热性质 23
1.1.5 硅的机械性质 31
1.2 硅衬底材料的晶体缺陷 34
1.2.1 硅单晶的点缺陷 35
1.2.2 硅单晶中的线缺陷(位错) 40
1.2.3 硅单晶中的面缺陷(界面) 44
参考文献 49
第2章 超大规模集成电路硅衬底加工技术工程 53
2.1 超大规模集成电路衬底硅单晶的加工成型技术 53
2.1.1 单晶锭外形整理 53
2.1.2 切片 54
2.1.3 倒角 56
2.1.4 磨片 57
2.1.5 硅单晶研磨片的清洗 64
2.1.6 腐蚀 67
2.1.7 展望 69
2.2 超大规模集成电路硅衬底的抛光技术 70
2.2.1 硅衬底的边缘抛光 70
2.2.2 IC中硅衬底表面抛光 71
2.2.3 抛光液 77
2.2.4 抛光硅片表面质量与抛光工艺技术 79
2.2.5 展望 81
参考文献 81
第3章 硅气相外延技术工程 83
3.1 硅气相外延在IC技术发展中的作用 83
3.2 硅气相外延设备与基本化学反应 87
3.2.1 硅气相外延设备 87
3.2.2 硅气相外延的基本化学反应 89
3.3 外延生长动力学及外延层中浓度的分布 90
3.3.1 外延生长速率v与反应剂浓度Y的关系 91
3.3.2 两种极限生长情况及反应温度T对v的影响 92
3.3.3 气体流速与硅片位置对生长速率的影响 93
3.3.4 外延层中杂质浓度分布 94
3.4.1 硅烷热分解法外延 99
3.4 硅烷热分解法外延与选择外延 99
3.4.2 选择外延 100
3.5 外延层的缺陷 100
3.5.1 外延层缺陷种类及其成因分析 101
3.5.2 外延层缺陷检验方法 105
3.6 硅CVD外延自掺杂效应的分析研究 105
3.6.1 概述 105
3.6.2 理论分析 106
3.7 硅外延片滑移线产生因素的实验研究 108
3.7.1 理论分析 109
3.7.2 实验与结果 109
3.8.1 概述 112
3.7.3 实验结果的讨论 112
3.8 硅外延生长的工艺优化——反向补偿法 112
3.8.2 理论分析 113
3.8.3 实验和结果 114
3.8.4 结论 115
3.9 硅外延层的快速调温 115
3.9.1 硅外延层的快速调温化学气相沉积法 115
3.9.2 硅外延工艺中降低外延温度的现状及要求 116
3.10 外延片夹层的测试 117
3.10.1 外延片中的夹层 117
3.10.2 夹层的检测 117
3.11.1 基本原理 118
3.11 三探针电压击穿法测外延层电阻率 118
3.11.3 测试步骤 121
3.11.2 测量线路和装置 121
3.11.4 测试注意事项 122
3.11.5 测量精度 122
3.12 电容-电压法测硅外延层纵向杂质分布 123
3.12.1 测试基本原理 123
3.12.2 用高频Q表的测试方法和测试电路 126
3.12.3 测试步骤 127
3.12.4 测试数据的处理与杂质浓度的测定 127
3.12.5 测准条件与注意事项 128
3.12.6 利用C-V测试仪和汞探针测外延片杂质浓度简介 129
3.13.1 基本原理 130
3.13 二次谐波法测外延层杂质浓度 130
3.13.2 测试电路及其工作原理 132
3.13.3 仪器的标定 133
3.13.4 测试注意事项 135
3.14 外延层厚度的测量 136
3.14.1 层错法 137
3.14.2 红外干涉法 137
3.15 用RHEED方法分析半导体薄膜特性 139
3.15.1 概述 139
3.15.2 实验 140
3.16.1 概述 143
3.16 高精度X射线双晶衍射仪的原理及其应用 143
3.15.4 小结 143
3.15.3 实验结果与讨论 143
3.16.2 工作原理 144
3.16.3 X射线双晶衍射的优缺点 145
3.17 外延片的其他测试方法 145
3.18 小结与展望 146
参考文献 146
第4章 键合技术工程 149
4.1 键合的基本原理及基本要求 149
4.2 几种主要的键合方法 150
4.3.1 键合前晶片表面的表征 151
4.3.2 键合界面特性的表征测试 151
4.3 键合晶片的表征测试方法 151
4.4 键合技术在微电子中的应用 152
4.4.1 概述 152
4.4.2 用氧等离子体激活处理的低温硅片直接键合技术 153
4.4.3 ZnO陶瓷键合Cu电极技术 157
4.4.4 AlN薄膜室温直接键合技术 161
4.4.5 硅/锗/硅键合技术 164
4.4.6 热键合技术及其在激光方面的应用 168
4.4.7 微传感器制造中的硅-玻璃静电键合技术 172
4.4.8 微机械加工中的图形硅片键合技术 176
参考文献 182
第5章 微机械加工技术工程 185
5.1.1 腐蚀系统简介 188
5.1 各向异性腐蚀 188
5.1.2 腐蚀速率与晶体取向的关系 189
5.1.3 腐蚀速率与腐蚀液成分的关系 194
5.1.4 腐蚀速率与硅掺杂浓度的关系 196
5.1.5 各向异性自停止腐蚀技术 198
5.1.6 各向异性腐蚀的机制 201
5.1.7 各向异性腐蚀剂腐蚀出的微结构 207
5.1.8 各向异性腐蚀的应用 213
5.2 各向同性腐蚀 217
5.2.1 HF+HNO3腐蚀系统的腐蚀原理 217
5.2.2 影响半导体单晶电化学腐蚀速率的各种因素 218
5.2.3 腐蚀液成分配比对硅表面形貌及角、棱的影响 220
5.2.4 各向同性自停止腐蚀 223
5.3 阳极腐蚀 224
5.3.1 阳极腐蚀原理 224
5.3.2 影响阳极腐蚀的因素 226
5.3.3 采用阳极腐蚀的自停止腐蚀方法 228
5.4 电钝化腐蚀 229
5.4.1 电钝化腐蚀原理 229
5.4.2 制备n型硅膜的pn结自停止腐蚀方法 235
5.4.3 制备p型硅膜的脉冲电压方法 239
5.5 表面微机械加工技术 241
5.5.1 表面微机械加工的基本概念 241
5.5.2 表面微机械加工技术的应用 246
5.6.1 LIGA技术 249
5.6 LIGA与准LIGA技术工艺 249
5.6.2 LIGA技术的推广 250
参考文献 255
第6章 微电子器件氧化及钝化技术工程 259
6.1 二氧化硅的结构 260
6.1.1 二氧化硅网络 260
6.1.2 非桥键氧和氧空位 261
6.2 二氧化硅的性质 261
6.2.1 二氧化硅的物理性质 261
6.2.2 二氧化硅的化学性质 263
6.3 二氧化硅膜的制备及其原理 264
6.3.1 热生长氧化法 265
6.3.2 热氧化生长动力学 268
6.3.3 热氧化的规律 271
6.3.4 热分解沉积氧化膜法 277
6.3.5 其他氧化方法 279
6.3.6 生产中常见的几种质量问题 280
6.3.7 硅-二氧化硅界面缺陷 282
6.4 二氧化硅-硅界面的物理性质 284
6.4.1 热氧化时杂质在界面上的再分布 284
6.4.2 反型层现象 284
6.5 二氧化硅玻璃中的杂质 285
6.5.1 SiO2网络中的杂质 285
6.5.2 Revesz模型和结晶化 287
6.5.4 二氧化硅中Na+离子的影响 288
6.5.3 HCl氧化的作用 288
6.6 杂质在二氧化硅中的扩散 289
6.6.1 杂质在SiO2层中的扩散系数 289
6.6.2 二氧化硅掩蔽杂质扩散的可能性 291
6.6.3 掩蔽杂质扩散所需要的最小的SiO2层厚度 292
6.7 二氧化硅膜质量的检验 293
6.7.1 氧化层膜厚的测定 293
6.7.2 氧化膜缺陷的检测 297
6.8 表面钝化 297
6.8.1 SiO2-Si系统中的电荷 298
6.8.2 IC制程中的氮化硅钝化膜 312
6.8.3 三氧化二铝的钝化技术 314
6.8.4 低温钝化技术及半绝缘多晶硅钝化膜 319
参考文献 321
第7章 扩散与离子注入 323
7.1 扩散原理与模型 323
7.1.1 固体中的扩散模型 323
7.1.2 扩散机制 324
7.2 常用元素的扩散技术原理 329
7.2.1 电场加速的扩散 329
7.2.2 常用的砷、硼、磷扩散 330
7.2.3 扩散设备与扩散源 332
7.3 扩散的测量技术 334
7.3.1 结深和薄层电阻 334
7.3.2 剖面分布测量 335
7.4 离子注入技术与原理 338
7.4.1 原理 340
7.4.2 离子注入设备 342
7.4.3 工艺技术 348
7.4.4 应用 350
7.5 小结与展望 351
参考文献 352
第8章 IC制备中制版技术及原理 355
8.1 制版概述 355
8.1.1 制版意义 355
8.1.2 制版工艺流程简介 355
8.1.3 掩膜版的基本构造及质量要求 357
8.2.1 制版技术的光学原理 358
8.2 超微粒干版制备技术及原理 358
8.2.2 超微粒干版的显像原理 361
8.3 铬版制备技术 365
8.3.1 铬版的特点 365
8.3.2 铬版的制备 365
8.3.3 用铬版复印光刻版 367
8.3.4 铬膜质量的几点讨论 368
8.4 氧化铁版制备技术 369
8.4.1 化学气相沉积(CVD)法制备氧化铁版原理 370
8.4.2 涂敷法制氧化铁版原理 372
8.5 其他光刻制版技术 376
8.5.1 传统光学光刻及制版技术面临的挑战 376
8.5.2 后光学光刻及制版技术的发展 378
参考文献 383
第9章 IC制备中的图形转移技术及原理 385
9.1 光刻胶的光敏原理 386
9.1.1 光刻胶化学性质与作用 386
9.1.2 光刻胶涂布显影工艺 387
9.1.3 光刻胶涂布与显影设备 390
9.2 分辨率与焦距深度 390
9.3 光刻对准曝光设备 391
9.3.1 接触式对准机 391
9.3.2 间隙式对准机 392
9.3.3 投射式对准机 392
9.4.2 光刻胶厚度曲线(SwingCurve) 393
9.4 工艺参数条件设定 393
9.4.1 选择光刻胶 393
9.4.3 最佳焦距与曝光量 394
9.4.4 工艺空间(Process Window) 394
9.5 显影后的检查 395
9.6 线宽控制及对准检查 396
9.6.1 线宽控制 396
9.6.2 对准检查 398
9.7 变形照明及移相掩膜技术 399
9.7.1 变形照明(偏轴光源) 399
9.7.2 移相掩膜技术 401
9.8 图形转移工艺计算机模拟 403
9.9 邻近效应修正技术 404
9.10.1 电子束光刻技术 405
9.10 电子束光刻、X射线光刻技术 405
9.10.2 X射线光刻技术 408
参考文献 410
第10章 IC制备中的刻蚀技术 411
10.1 湿法刻蚀技术及原理 411
10.1.1 二氧化硅的湿法刻蚀 412
10.1.2 硅的刻蚀 413
10.1.3 氮化硅刻蚀 413
10.1.4 铝的刻蚀 413
10.1.5 铬的刻蚀 414
10.2.1 等离子体概述 415
10.2 干法刻蚀技术及原理 415
10.2.2 干法刻蚀用设备 419
10.2.3 半导体制备中常用材料的干法刻蚀介绍 422
10.2.4 终点检测(EndPointDetection) 428
10.3 刻蚀技术新进展 430
10.3.1 四甲基氢氧化铵湿法刻蚀 430
10.3.2 软刻蚀 431
10.3.3 约束刻蚀剂层技术 434
参考文献 435
第11章 IC制备中多层布线与全面平坦化技术与原理 437
11.1.1 从真空管到IC,再到大型集成电路的历程 438
11.1.2 化学机械抛光在大型集成电路制程上的必要性 438
11.1 化学机械抛光的发展及技术要求 438
11.1.3 平坦化方法与化学机械抛光 439
11.1.4 CMP的应用工程及要求条件 440
11.1.5 总结 444
11.2 超精密CMP机理 444
11.2.1 概述 444
11.2.2 CMP的要求事项 445
11.2.3 精密研磨法与研磨机制简介 445
11.2.4 CMP的各项要素 449
11.3 CMP的要素技术 450
11.3.1 CMP装置的技术 450
11.3.2 影响CMP质量与效率的研磨液 461
11.3.3 决定平坦化均匀度的研磨垫 468
11.3.4 CMP后的清洗技术 476
11.3.5 CMP中测定与工程种类的关系 483
11.4 铜布线 484
11.4.1 铜布线工艺 485
11.4.2 国际上的两种抛光液 487
11.4.3 一种新型碱性抛光液 489
11.4.4 有机碱的选择 491
11.4.5 多层布线铜CMP动力学 493
11.4.6 小结 494
11.5 CMP的发展 495
11.5.1 CMP技术的登场 495
11.5.2 CMP技术的困难 495
11.5.4 固定磨料的CMP 496
11.5.3 CMP的技术改良 496
11.5.5 结束语 497
参考文献 497
第12章 IC制备中的封装技术与原理 501
12.1 引言 501
12.1.1 微电子封装的发展 501
12.1.2 电子封装技术简介 502
12.1.3 封装类型 503
12.2 陶瓷封装 505
12.2.1 陶瓷封装简介 505
12.2.2 陶瓷封装材料 505
12.2.3 陶瓷封装的制备工艺 506
12.2.4 其他陶瓷封装材料及工艺 508
12.3 塑料封装 510
12.3.1 塑料封装的材料 510
12.3.2 塑料封装的制备工艺 512
12.3.3 塑料封装的可靠性试验 513
12.4 封装的化学原理 514
12.4.1 装架工艺化学原理 514
12.4.2 陶瓷金属化 516
12.4.3 塑料封装的化学原理 517
12.5 新型封装技术 524
12.5.1 倒装焊技术的发展历程及前景 524
12.5.2 系统级封装 526
12.5.3 下一代微型器件组装技术——电场贴装 527
12.5.4 技术新趋向 529
参考文献 530
第13章 IC制备中的金属处理技术与原理 533
13.1 金属化学气相沉积技术与原理 533
13.1.1 TiN金属化学气相沉积阻挡层 533
13.1.2 钨化学气相沉积 541
13.1.3 铜化学气相沉积 543
13.1.4 铝化学气相沉积 549
13.2 金属物理气相沉积技术与原理 550
13.2.1 改进阶梯覆盖率 550
13.2.2 铝插塞及平坦化过程 552
13.2.3 未来PVD的发展趋势 553
13.3 金属中的电迁移 554
13.3.1 电迁移的驱动力 555
13.3.2 有效电荷数的计算 557
13.3.3 电迁移的测量 558
13.3.4 金属超细线条中的电迁移 559
13.4 表面动力学过程 560
13.4.1 表面原子 560
13.4.2 原子团上的气相压力 561
13.4.3 原子团的“熟化”生长机理 563
13.4.4 原子团的聚合生长机理 566
13.4.5 表面台阶成核模型 567
13.5 电极制备 570
13.5.1 欧姆接触 570
13.5.2 蒸发与溅射 573
13.5.3 多层电极 582
13.5.4 键合 585
13.6 小结 587
参考文献 587
第14章 硅单晶性质的检测设备与技术 591
14.1 硅单晶缺陷的检测 591
14.1.1 选择性腐蚀的技术 591
14.1.2 电化学腐蚀条件及其反应 592
14.1.3 影响半导体单晶电化学腐蚀速率的各种因素 593
14.1.4 电化学腐蚀在半导体技术中的应用 596
14.1.5 光学显微镜的应用 597
14.2 导电类型的测量 597
14.2.1 导电类型的测量方法 598
14.2.2 测量条件的分析 599
14.3 电阻率的测量 600
14.3.1 两探针法 601
14.3.2 四探针法 601
14.3.3 涡电流法 605
14.3.4 扩展电阻探针法 606
14.3.5 C-V法 607
14.4 单晶晶向检测 610
14.4.1 晶向与半导体工艺的关系 610
14.4.2 X射线衍射法(X-ray Diffraction Method) 612
14.4.3 光点定向法 614
14.5.1 测量原理 616
14.5 氧浓度的测量 616
14.5.2 红外光谱仪种类 617
14.5.3 测量工艺和方法 619
14.5.4 测量条件和误差分析 619
14.6 非平衡少数载流子寿命的测量 621
14.6.1 概述 621
14.6.2 少子寿命的测量方法 622
14.7 超微量分析技术 626
14.7.1 感应耦合等离子质谱仪 627
14.7.2 石墨炉原子吸收光谱仪 628
14.7.3 全反射X射线荧光光谱仪 628
14.7.4 X射线电子能谱仪 628
14.7.6 扫描探针显微镜——原子力显微镜 630
14.7.5 X射线表面状态测量仪 630
14.7.7 俄歇电子能谱仪 632
14.7.8 扫描电子显微镜 632
14.7.9 透射电子显微镜 634
参考文献 637
附录A 硅单晶片材料及半导体工业常用名词的解释 641
附录B 硅在300K的物理常数 647
附录C 物理基本常数 648
附录D 长度单位转换表 648
附录E 压力单位转换表 649
附录F 能量单位转换表 649
附录G 力单位转换表 649