图书介绍
切削加工pdf电子书版本下载
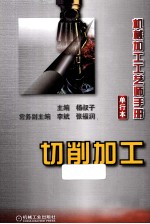
- 杨叔子主编;常治斌,鲍剑斌,汤漾平等副主编 著
- 出版社: 北京:机械工业出版社
- ISBN:9787111380320
- 出版时间:2012
- 标注页数:1158页
- 文件大小:230MB
- 文件页数:1173页
- 主题词:金属切削-生产工艺-技术手册
PDF下载
下载说明
切削加工PDF格式电子书版下载
下载的文件为RAR压缩包。需要使用解压软件进行解压得到PDF格式图书。建议使用BT下载工具Free Download Manager进行下载,简称FDM(免费,没有广告,支持多平台)。本站资源全部打包为BT种子。所以需要使用专业的BT下载软件进行下载。如 BitComet qBittorrent uTorrent等BT下载工具。迅雷目前由于本站不是热门资源。不推荐使用!后期资源热门了。安装了迅雷也可以迅雷进行下载!
(文件页数 要大于 标注页数,上中下等多册电子书除外)
注意:本站所有压缩包均有解压码: 点击下载压缩包解压工具
图书目录
第3篇 切削加工 3
第1章 车削 3
1.1 车削基本特征与加工范围 3
1.2 车削主要工艺参数 4
1.2.1 各种车刀的切削用量 4
1.2.2 车刀的磨钝标准与耐用度 14
1.2.3 车削速度、车削力和车削功率 14
1.3 车削精度 31
1.3.1 车削加工的经济精度与表面粗糙度 31
1.3.2 各种车床加工的质量问题与解决措施 36
1.4 车床 44
1.4.1 卧式车床 44
1.4.2 立式车床 48
1.4.3 转塔车床和回轮车床 53
1.4.4 仿形车床 61
1.4.5 卡盘多刀车床 64
1.4.6 单轴自动车床 67
1.4.7 多轴自动车床 70
1.5 车刀 73
1.5.1 车刀的类型与用途 73
1.5.2 车刀的前面形状和几何参数 74
1.5.3 断屑和卷屑 75
1.5.4 硬质合金焊接车刀 79
1.5.5 机械夹固式车刀 80
1.5.6 硬质合金可转位车刀 81
1.5.7 陶瓷、金刚石和立方氮化硼车刀 105
1.5.8 成形车刀 106
第2章 钻削、扩削、铰削 109
2.1 钻、扩、铰的特点及主要工艺参数 109
2.1.1 钻、扩、铰的特点 109
2.1.2 钻头、扩孔钻和铰刀的磨钝标准及耐用度 110
2.1.3 钻、扩、铰的切削用量、切削力和切削功率 110
2.2 钻、扩、铰加工机动时间的计算 159
2.3 钻、扩、铰的加工精度 161
2.4 钻、扩、铰加工中常见问题的产生原因和解决方法 162
2.5 深孔、小孔和微孔的钻削 169
2.5.1 深孔钻削 169
2.5.2 小孔和微孔的钻削 170
2.6 钻床 171
2.6.1 钻床的类型及适用范围 171
2.6.2 台式钻床 172
2.6.3 立式钻床 172
2.6.4 摇臂钻床 172
2.6.5 深孔钻床 176
2.6.6 数控钻床和钻削中心 179
2.7 孔加工刀具 182
2.7.1 孔加工刀具的类型与用途 182
2.7.2 麻花钻 182
2.7.3 硬质合金浅孔钻 197
2.7.4 扩孔钻和锪钻 198
2.7.5 铰刀 210
2.7.6 中心钻和扁钻 228
2.7.7 深孔钻 231
第3章 镗削 242
3.1 镗削的特点与类型 242
3.1.1 镗削的特点 242
3.1.2 镗削类型及适用范围 242
3.2 卧式镗床镗削 243
3.2.1 卧式镗床的工作范围 243
3.2.2 卧式镗床镗削时工件的定位方式 243
3.2.3 卧式镗床镗削时工件工艺基准面的找正方法 245
3.2.4 箱体类零件的镗孔方案 247
3.3 金刚镗床镗削(高速精镗) 247
3.3.1 金刚镗床镗削的特点 247
3.3.2 金刚镗床加工中应注意的问题 248
3.4 坐标镗床镗削 251
3.4.1 加工前的坐标换算与调整 251
3.4.2 坐标镗床的找正与测量 252
3.4.3 镗削空间斜孔时的角度计算 255
3.5 镗削用量 256
3.6 镗削精度 259
3.6.1 镗床的加工精度 259
3.6.2 影响镗削加工质量的因素与解决措施 260
3.6.3 提高镗孔精度的常用方法 264
3.7 典型表面和零件的镗削 264
3.7.1 同轴孔的镗削 264
3.7.2 大孔和长孔的镗削 265
3.7.3 阶梯孔和盲孔镗削 266
3.7.4 小孔镗削 267
3.7.5 内、外球面的镗削 268
3.7.6 铣镗床立柱底面的镗削 269
3.8 镗床 269
3.8.1 卧式铣镗床 269
3.8.2 坐标镗床 275
3.8.3 精镗床 278
3.8.4 深孔镗床和深孔钻镗床 278
3.9 镗刀 284
3.9.1 单刃镗刀 284
3.9.2 多刃镗刀 286
3.9.3 微调镗刀 287
3.9.4 复合镗刀 287
第4章 铣削 289
4.1 铣削特点、方式及加工范围 289
4.1.1 铣削特点 289
4.1.2 铣削方式 289
4.1.3 铣削精度和铣削效率 290
4.1.4 铣削加工的应用范围 297
4.2 铣削用量 300
4.2.1 铣削要素 300
4.2.2 铣削进给量 300
4.2.3 铣削速度、铣削力及铣削功率的计算 303
4.2.4 确定铣削用量和铣削功率的常用表格 305
4.3 提高铣削精度和铣削效率的方法 335
4.3.1 精铣 335
4.3.2 高效铣刀铣削 338
4.3.3 组合铣刀铣削 339
4.4 典型零件和表面的铣削加工 341
4.4.1 铣削花键轴 341
4.4.2 铣削长齿条 341
4.4.3 铣削凸轮 343
4.4.4 铣削曲面 345
4.4.5 铣削空间斜面 346
4.5 铣削发展趋势 348
4.6 铣床 348
4.6.1 升降台铣床 351
4.6.2 工具铣床、摇臂铣床和滑枕铣床 351
4.6.3 床身式铣床 351
4.6.4 龙门铣床和数控龙门镗铣床 351
4.6.5 仿形铣床和数控仿形铣床 360
4.7 铣刀 371
4.7.1 铣刀的类型与用途 371
4.7.2 高速钢尖齿铣刀 371
4.7.3 高速钢铲齿铣刀 389
4.7.4 套式铣刀 391
4.7.5 硬质合金铣刀 393
第5章 刨削、插削、锯削 415
5.1 刨削 415
5.1.1 刨削特点 415
5.1.2 刨削用量 415
5.1.3 刨削加工精度 423
5.1.4 提高刨削效率的主要方法 426
5.1.5 典型表面和零件的刨削加工 429
5.2 插削 435
5.2.1 插削的特点 435
5.2.2 插削用量 435
5.2.3 典型表面和零件的插削 437
5.3 锯削 441
5.3.1 锯削的特点 441
5.3.2 锯削用量、锯削速度和材料切除率 441
5.3.3 锯削加工精度与锯削中常见问题的解决方法 445
5.4 刨床、插床和锯床 447
5.4.1 刨床和插床 447
5.4.2 锯床 447
5.5 刨刀和插刀 459
5.5.1 刨刀的类型与用途 459
5.5.2 刨刀合理几何参数 460
5.5.3 先进刨刀 460
5.5.4 插刀的类型与选用 467
5.5.5 插刀主要几何角度的选择 468
第6章 拉削 469
6.1 拉削的特点、类型及方式 469
6.1.1 拉削的特点 469
6.1.2 拉削的类型 469
6.1.3 拉削的方式 471
6.2 拉削用量、拉削力和拉削机动时间 472
6.2.1 拉削速度的分组与选用 472
6.2.2 拉削进给量 474
6.2.3 拉削力 474
6.2.4 拉削机动时间 476
6.3 拉削切削液及其浇注方法 476
6.3.1 常用拉削切削液 476
6.3.2 切削液的浇注方法 477
6.4 拉削中常见缺陷的分析与解决方法 477
6.5 典型表面和零件的拉削加工 479
6.5.1 对拉削工件的工艺要求 479
6.5.2 汽车发动机轴瓦内圆表面拉削 479
6.5.3 循环球转向机螺母滚道的螺旋拉削 480
6.5.4 套管叉花键孔拉削 480
6.5.5 齿条拉削 480
6.5.6 渐开线凸轮轴拉削 482
6.6 拉床 482
6.6.1 拉床的类型及适用范围 482
6.6.2 立式拉床 485
6.6.3 卧式拉床 485
6.6.4 连续拉床 485
6.6.5 拉床发展趋势 485
6.7 拉刀 487
6.7.1 拉刀的类型 487
6.7.2 拉刀的结构和几何参数 487
6.7.3 拉刀的使用 491
第7章 磨削 492
7.1 磨削原理 492
7.1.1 磨削过程与切屑的形成 492
7.1.2 磨削基本参数 492
7.1.3 磨削力和磨削功率 494
7.1.4 磨削热和磨削温度 496
7.2 磨削的基本特征和磨削类型 497
7.2.1 磨削加工特点 497
7.2.2 磨削分类 497
7.2.3 磨削的经济加工能力 498
7.3 普通磨削用量的选择 498
7.3.1 砂轮速度的选择 498
7.3.2 工件速度的选择 499
7.3.3 纵向进给量的选择 499
7.3.4 背吃刀量ap的选择 499
7.3.5 光磨次数的选择 499
7.4 常见磨削方式的主要工艺参数 499
7.4.1 外圆磨削 499
7.4.2 内圆磨削 505
7.4.3 平面磨削 512
7.4.4 无心磨削 517
7.4.5 成形磨削 521
7.5 砂轮的修整 526
7.5.1 车削法修整 526
7.5.2 滚压法修整 528
7.5.3 磨削法修整 529
7.5.4 修整砂轮注意事项 529
7.5.5 超硬磨料砂轮的修整 529
7.6 磨削液 530
7.6.1 磨削液的种类 530
7.6.2 磨削液的选用 530
7.6.3 磨削液的过滤 535
7.7 磨削常见缺陷的原因 536
7.8 高效磨削 539
7.8.1 高速磨削 539
7.8.2 深切缓进给磨削 540
7.8.3 连续修整深切缓进给磨削 541
7.8.4 宽砂轮与多砂轮磨削 542
7.8.5 恒压力磨削 543
7.8.6 高速深切快进给磨削 543
7.8.7 砂带磨削 544
7.9 磨床 553
7.9.1 概述 553
7.9.2 外圆磨床 553
7.9.3 内圆磨床 564
7.9.4 平面磨床 572
7.9.5 专门化磨床 591
7.9.6 其他磨床 599
7.9.7 数控磨床 611
7.10 磨料磨具的选择 618
7.10.1 普通磨料磨具的选择 618
7.10.2 超硬磨料磨具的选择 624
7.10.3 涂覆磨具的选择 628
第8章 齿轮、蜗杆副、花键加工 633
8.1 圆柱齿轮加工 633
8.1.1 圆柱齿轮加工方法与工艺设计 633
8.1.2 滚齿 641
8.1.3 插齿 662
8.1.4 剃齿 671
8.1.5 珩齿 679
8.1.6 磨齿 687
8.1.7 冷挤齿 691
8.1.8 轮齿端倒角 693
8.1.9 重载齿轮加工工艺 695
8.1.10 齿轮加工CAPP 710
8.2 锥齿轮加工 723
8.2.1 概述 723
8.2.2 直齿锥齿轮加工 734
8.2.3 曲线齿锥齿轮切齿方法 741
8.2.4 锥齿轮研齿 757
8.2.5 锥齿轮检验及接触区修正 759
8.3 蜗杆副加工 765
8.3.1 蜗轮加工特点与主要工艺参数 765
8.3.2 蜗杆加工特点与主要工艺参数 772
8.3.3 特殊蜗杆副加工 779
8.4 花键加工 781
8.4.1 花键加工的特点 781
8.4.2 花键加工的主要方法 784
8.5 齿轮加工机床 822
8.5.1 概述 822
8.5.2 滚齿机 823
8.5.3 插齿机 832
8.5.4 剃齿机 836
8.5.5 珩齿机 839
8.5.6 磨齿机 839
8.5.7 花键轴铣床 846
8.5.8 数控齿轮加工机床 851
8.5.9 锥齿轮加工机床 855
8.6 齿轮刀具 868
8.6.1 齿轮铣刀 868
8.6.2 齿轮滚刀 871
8.6.3 插齿刀 877
8.6.4 剃齿刀 888
8.6.5 蜗轮刀具 894
8.6.6 锥齿轮刀具 898
8.6.7 非渐开线展成刀具 919
第9章 螺纹加工 927
9.1 螺纹加工的基本类型、特点及适用范围 927
9.2 丝锥攻螺纹、板牙套螺纹 930
9.2.1 普通螺纹丝锥攻螺纹 930
9.2.2 锥形丝锥攻螺纹 934
9.2.3 板牙套螺纹 935
9.3 螺纹车削 936
9.3.1 螺纹的车削特点与加工方式 936
9.3.2 螺纹车削工艺参数 939
9.3.3 螺纹切削的切削液选择 940
9.3.4 精车精密丝杠的工艺要点 941
9.3.5 螺纹车削时易产生的缺陷及改进措施 942
9.4 螺纹磨削 943
9.4.1 螺纹磨削的加工方式、特点及应用 943
9.4.2 磨削用量的选择 945
9.4.3 滚珠丝杠圆弧形螺纹磨削 945
9.4.4 螺纹磨削的注意事项 946
9.4.5 螺纹磨削常见缺陷及预防措施 946
9.5 螺纹加工机床 948
9.5.1 螺纹车床 948
9.5.2 螺纹铣床 948
9.5.3 螺纹磨床 949
9.5.4 攻丝机 949
9.5.5 滚丝机 949
9.5.6 搓丝机 951
9.6 螺纹刀具 952
9.6.1 螺纹刀具的类型和用途 952
9.6.2 螺纹车刀和梳刀 952
9.6.3 丝锥 954
9.6.4 板牙 972
9.6.5 螺纹铣刀 977
9.6.6 螺纹切头 980
9.6.7 螺纹滚压工具 988
第10章 精整和光整加工 999
10.1 珩磨 999
10.1.1 珩磨加工的原理和特点 999
10.1.2 珩磨头及珩磨油石的选用 999
10.1.3 珩磨主要工艺参数 1006
10.1.4 珩磨加工技术的发展 1011
10.2 研磨 1012
10.2.1 研磨加工的特点与经济精度 1012
10.2.2 研磨机理与运动轨迹 1013
10.2.3 研磨剂和研具的选用 1014
10.2.4 研磨主要工艺参数 1020
10.2.5 典型零件的研磨加工 1021
10.2.6 常见研磨故障及排除方法 1023
10.3 抛光 1025
10.3.1 概述 1025
10.3.2 固结磨料柔性磨具抛光 1026
10.3.3 自由磨料抛光 1027
第11章 精密和超精密加工 1037
11.1 概述 1037
11.1.1 精密和超精密加工的范畴 1037
11.1.2 精密和超精密加工的工作环境 1037
11.1.3 精密和超精密加工的工件材料 1038
11.1.4 常用的精密和超精密加工方法 1039
11.2 金刚石刀具超精密切削 1041
11.2.1 金刚石刀具超精密切削机理 1041
11.2.2 金刚石车刀的设计和刃磨 1042
11.2.3 金刚石刀具超精密车削工艺特点 1045
11.2.4 超精密车削的发展趋势 1046
11.3 精密和超精密磨削 1047
11.3.1 精密和超精密磨削机理 1047
11.3.2 精密磨削工艺参数 1047
11.3.3 超精密磨削工艺参数 1056
11.4 精密磨削实例 1057
11.4.1 外圆精密磨削实例 1057
11.4.2 内圆精密磨削实例 1058
11.4.3 平面精密磨削实例 1059
第12章 难加工材料的切削加工 1060
12.1 难加工材料的切削特点 1060
12.1.1 难加工材料的分类 1060
12.1.2 难加工材料的切削加工特点 1060
12.2 高强度钢的切削加工 1060
12.3 高锰钢的切削加工 1061
12.4 淬硬钢、冷硬铸铁及耐磨合金铸铁的切削加工 1062
12.5 不锈钢、高温合金的切削加工 1062
12.5.1 不锈钢、高温合金的切削加工特点 1062
12.5.2 不锈钢、高温合金的车(镗)削加工 1063
12.5.3 不锈钢、高温合金的铣削加工 1066
12.5.4 不锈钢、高温合金的钻削加工 1067
12.6 工程陶瓷的切削加工 1070
12.6.1 工程陶瓷材料的特性 1070
12.6.2 陶瓷材料脆性破坏机理 1070
12.6.3 几种工程陶瓷材料的切削加工 1070
12.6.4 陶瓷材料的离子束加热切削 1072
12.6.5 陶瓷材料的磨削加工 1072
12.7 其他难切材料的切削加工 1072
12.7.1 石材的切削加工 1072
12.7.2 复合材料的切削加工 1073
12.7.3 工程塑料的切削加工 1076
12.8 非金属材料加工用刀具 1077
12.8.1 木材加工刀具 1077
12.8.2 塑料加工刀具 1093
12.8.3 石材锯切设备及刀具 1103
第13章 高速切削加工 1106
13.1 高速切削概述 1106
13.1.1 高速切削的速度范围 1106
13.1.2 高速切削的优越性 1107
13.1.3 高速切削的切削力 1107
13.1.4 高速切削的切削热和切削温度 1107
13.1.5 高速切削的振动 1108
13.1.6 高速切削时刀具的摩擦、磨损特征 1109
13.1.7 高速切削的表面质量 1110
13.2 高速切削刀具 1112
13.2.1 高速切削刀具材料 1112
13.2.2 高速切削可转位刀片 1123
13.2.3 几种高速切削刀具 1129
13.2.4 高速切削刀柄系统 1133
13.3 高速切削机床 1136
13.3.1 高速切削加工机床的要求 1136
13.3.2 高速加工机床 1136
13.3.3 高速加工机床构造特征 1137
13.3.4 高速加工机床的控制系统 1145
13.3.5 高速加工机床的合理选择 1146
13.3.6 高速切削加工机床夹具的特点 1147
13.4 高速切削的应用 1147
13.4.1 铝合金的高速切削 1147
13.4.2 铸铁与钢的高速切削 1149
13.5 高速切削的安全性 1152
13.5.1 高速切削的安全性要求 1152
13.5.2 高速切削刀具系统的平衡 1153
参考文献 1154