图书介绍
航空制造工程手册 电机电器工艺pdf电子书版本下载
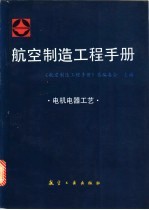
- 《航空制造工程手册》总编委会主编 著
- 出版社: 北京:航空工业出版社
- ISBN:7800468704
- 出版时间:1994
- 标注页数:608页
- 文件大小:24MB
- 文件页数:628页
- 主题词:
PDF下载
下载说明
航空制造工程手册 电机电器工艺PDF格式电子书版下载
下载的文件为RAR压缩包。需要使用解压软件进行解压得到PDF格式图书。建议使用BT下载工具Free Download Manager进行下载,简称FDM(免费,没有广告,支持多平台)。本站资源全部打包为BT种子。所以需要使用专业的BT下载软件进行下载。如 BitComet qBittorrent uTorrent等BT下载工具。迅雷目前由于本站不是热门资源。不推荐使用!后期资源热门了。安装了迅雷也可以迅雷进行下载!
(文件页数 要大于 标注页数,上中下等多册电子书除外)
注意:本站所有压缩包均有解压码: 点击下载压缩包解压工具
图书目录
第1篇 航空电机制造技术 1
第1章 航空电机产品概述 1
1.1 概述 1
1.2 航空电机产品的分类 1
1.2.1 电源电机分类 1
1.2.2 驱动电机分类 1
1.2.3 控制微电机分类 1
1.3 航空电机系列产品和工艺关键 1
1.3.1 电源电机系列产品和工艺关键 1
1.3.2 驱动电机系列产品和工艺关键 6
1.3.3 电动机构系列产品和工艺关键 7
1.3.4 控制微电机系列产品和工艺关键 7
1.4 航空电机制造技术的发展方向 9
第2章 电机零件毛坯的选择 10
2.1 航空电机零件毛坯的分类、特点和成形方法 10
2.1.1 毛坯分类 10
2.1.1.1 锻造毛坯的常用材料分类 10
2.1.1.2 铸造毛坯按成形方法分类 10
2.1.2 毛坯结构特点及成形方法比较 11
2.1.2.1 毛坯结构特点 11
2.1.2.2 毛坯成形方法比较 11
2.2 零件毛坯设计和工艺性的关系 13
2.2.1 合金材料的工艺性 13
2.2.1.1 可锻性 13
2.2.1.2 铸造性 14
2.2.2 分型面的影响 14
2.2.3 壁厚的影响 16
2.2.3.1 确定最小壁厚 16
2.2.3.2 合金的影响 17
2.2.3.3 充型能力的影响 18
2.2.3.4 型壁摩擦力的影响 18
2.2.3.5 铸型内气体的影响 18
2.2.4 细孔的影响 18
2.2.4.1 铸件上的内孔通道 18
2.2.4.2 无内衬和有内衬两种内孔通道 19
2.2.4.3 可溶型芯 19
2.2.5 尺寸精度和表面粗糙度的影响 19
2.2.5.1 尺寸精度的影响 19
2.2.5.2 表面粗糙度的影响 21
2.2.6 变形的影响 22
2.2.7 热处理、表面处理工艺的影响 22
2.2.7.1 热处理工艺的影响 22
2.2.7.2 表面处理工艺的影响 22
2.2.8 机械加工和质量要求的影响 22
2.2.8.1 流水线生产对毛坯的要求 22
2.2.8.2 加工余量和保证余量 22
2.3 电机零件毛坯的选择及其总体经济性 23
2.3.1 总体选择原则 23
2.3.2 影响毛坯成本的因素 23
2.3.3 毛坯工艺改进实例 24
第3章 航空电机零件的冲压 25
3.1 电机铁芯冲片制造 25
3.1.1 电机铁芯冲片分类 25
3.1.2 铁芯冲片制造要点 27
3.1.3 航空电机冲片的冲压方法 28
3.1.4 电机冲片条料的下料 28
3.1.5 电机冲片所需冲裁力的计算与设备的选用 29
3.1.5.1 电机冲片冲裁力的计算 29
3.1.5.2 电机冲片冲裁所需设备的选择 30
3.1.6 电机冲片毛刺的去除 31
3.2 电机空心零件的冲压 33
3.2.1 球顶筒形罩子零件的深拉延 36
3.2.2 电机壳体的电刷窗口的冲裁 37
3.3 电机零件的冷挤压 38
3.3.1 冷挤压变形程度与挤压力 40
3.3.2 轴零件挤筋代替滚花 44
3.3.3 冷挤压件质量分析及防止措施 45
3.4 航空电机零件的精冲 49
3.4.1 模具刃口带圆弧的精冲 50
3.4.2 小孔的精冲 51
3.4.2.1 凸模固定端面抗压强度的计算 51
3.4.2.2 凸模最小剖面抗压强度的计算 51
3.4.2.3 凸模纵向弯曲稳压性的验算 51
3.5 微薄零件的冲压 52
3.5.1 毛坯尺寸的确定 54
3.5.2 冲裁力的确定 55
3.5.3 切割模板高度的确定 55
第4章 电机零件的机械加工 57
4.1 轴类零件的加工 57
4.1.1 轴类零件的结构与功能 57
4.1.2 轴类零件毛坯的选择与加工余量 58
4.1.2.1 毛坯的选择 58
4.1.2.2 毛坯加工余量 58
4.1.2.3 工序间加工余量 58
4.1.3 轴类零件典型部位的加工 60
4.1.3.1 螺纹加工 60
4.1.3.2 圆弧和锥体加工 60
4.1.3.3 圆柱直齿渐开线花键加工 62
4.1.3.4 对数曲线型面加工 62
4.1.3.5 螺旋轴加工 63
4.1.3.6 表面强化处理 64
4.1.4 轴的特种检测 67
4.1.4.1 磨削烧伤检查 67
4.1.4.2 磁粉探伤 68
4.1.4.3 扭力试验 68
4.1.5 典型零件工艺过程 69
4.2 电机壳体和端盖零组件的加工 72
4.2.1 壳体零组件的加工 72
4.2.1.1 壳体零组件的结构 72
4.2.1.2 壳体毛坯的选择 73
4.2.1.3 壳体的热处理及表面处理 73
4.2.1.4 壳体的公差配合、形位公差和表面粗糙度要求 75
4.2.1.5 壳体零件工艺过程和工艺过程分析 77
4.2.1.6 壳体加工典型工装 81
4.2.2 端盖零组件的加工 84
4.2.2.1 端盖的结构(含毛坯) 85
4.2.2.2 端盖的热处理和表面处理 88
4.2.2.3 端盖加工工艺过程和典型工艺分析 88
4.2.2.4 端盖加工推荐的加工余量及切削参数 93
4.2.2.5 端盖加工常用工装 93
4.3 刷盒加工 95
4.3.1 刷盒的分类 95
4.3.2 刷盒孔加工方法和加工余量的选择 97
4.3.2.1 基本要求 97
4.3.2.2 刷盒方孔的加工方法 98
4.3.2.3 刷盒方孔加工余量及偏差 98
4.3.3 典型零件加工工艺 99
4.3.4 常见故障分析 100
4.3.5 刷盒方孔表面质量控制 101
4.4 磁极加工(整体) 101
4.4.1 换向极 101
4.4.2 整体磁极 102
4.5 杯形转子加工 102
4.5.1 功能和结构 102
4.5.1.1 轴的功能和结构 102
4.5.1.2 杯子的功能和结构 103
4.5.1.3 杯形转子的功能和结构 105
4.5.2 轴和杯子的加工 105
4.5.2.1 轴的加工 105
4.5.2.2 杯子的加工 107
4.5.3 杯形转子组件加工 107
4.5.3.1 杯形转子组件加工 107
4.5.3.2 杯形转子组件的压装工具 108
4.5.3.3 库存应注意的事项 109
第5章 永磁体加工 110
5.1 铸造磁钢零件的制造 110
5.1.1 化学成分和磁性能 110
5.1.2 熔模铸造磁钢零件 111
5.1.2.1 磁钢零件的结构分类 111
5.1.2.2 铸造磁钢的工艺过程及制造工艺 113
5.1.2.3 磁钢合金的真空熔炼 116
5.1.3 铸造磁钢零件的加工 118
5.1.3.1 铸造磁钢的加工工艺特性 118
5.1.3.2 铸造磁钢毛坯热处理前的初磨加工 118
5.1.3.3 按铸造磁钢用途不同划分的机械加工工艺 119
5.1.3.4 磁钢零件的磨削加工 119
5.1.3.5 电极加工和电化学加工方法 121
5.1.4 磁钢零件的质量检验 122
5.1.4.1 磁性能检验 122
5.1.4.2 外观及尺寸检验 122
5.1.4.3 静平衡和超速试验 122
5.1.5 印记、搬运、油封包装 123
5.2 稀土钴永磁体的制造 123
5.2.1 烧结稀土钴永磁体的制造 123
5.2.1.1 烧结稀土钴永磁体主要材料 123
5.2.1.2 烧结稀土钴永磁体的制造工艺 123
5.2.2 粘接稀土钴永磁体的制造 125
5.2.2.1 Sm2TM17类粘接磁体的制备工艺 125
5.2.2.2 粘接稀土钴永磁体的成形方法 126
5.2.3 化学成分及磁性能 127
5.2.4 稀土钴永磁体的机械加工 127
5.2.4.1 坯件要求 128
5.2.4.2 装夹方式 128
5.2.4.3 线切割加工的注意事项 128
5.2.5 可加工稀土钴永磁体 129
5.2.5.1 可加工稀土钴原材料纯度及合金成分 129
5.2.5.2 可加工稀土钴永磁体的定向凝固工艺和热处理工艺 129
5.2.5.3 可加工稀土钴永磁体的磁性能 129
第6章 航空电机铁芯的制造 131
6.1 电机铁芯种类 131
6.2 电机铁芯制造 133
6.2.1 铁芯码片与迭压 133
6.2.2 各种铁芯的典型工艺 134
6.2.2.1 圆(方)铆钉紧固铁芯 134
6.2.2.2 套筒外壳收口铁芯 135
6.2.2.3 电子束焊铁芯 135
6.2.2.4 铆钉扩铆定子铁芯 136
6.2.2.5 转子铁芯 136
6.3 电机铁芯V型扣铆 139
第7章 换向器制造 141
7.1 换向器结构、分类及特征 141
7.1.1 换向器结构 141
7.1.2 换向器分类 141
7.1.3 换向器结构特征 141
7.1.3.1 塑料换向器结构特征 141
7.1.3.2 钢套换向器结构特征 142
7.2 换向片拉制 143
7.2.1 换向片拉制工艺 144
7.2.1.1 换向片拉制工艺过程 144
7.2.1.2 换向片变形过程工艺尺寸确定 144
7.2.2 换向片拉制模具 145
7.2.2.1 固定式拉模 145
7.2.2.2 可调式拉模 145
7.2.3 换向片缺陷分析 146
7.2.4 换向片检验 146
7.3 锥形绝缘圈制造 147
7.3.1 锥形绝缘圈典型工艺过程 147
7.3.2 主要工艺参数的选择 147
7.3.2.1 下料尺寸的计算 149
7.3.2.2 烘压工序烘烤参数 149
7.4 塑料换向器制造 150
7.4.1 塑料换向器典型工艺 150
7.4.2 塑料换向器主要工艺参数选择 151
7.4.2.1 片间绝缘总厚度KS的计算 151
7.4.2.2 装环烘烤参数 152
7.4.2.3 塑压及烘烤参数 152
7.4.2.4 接地介电强度 152
7.4.2.5 挂锡及预热参数 152
7.4.2.6 动力定型及超速试验烘烤参数 153
7.4.3 典型工装 153
7.4.3.1 整体压环组 153
7.4.3.2 塑压模 154
7.5 钢套换向器制造 154
7.5.1 钢套换向器典型工艺过程 154
7.5.2 钢套换向器工艺参数选择 157
7.5.2.1 换向器毛坯外径的确定 157
7.5.2.2 装环工序压力计算 157
7.5.2.3 扩铆、拧螺母压力计算 157
7.5.2.4 拧螺母烘烤参数 158
7.5.2.5 铣接线槽形位误差 158
7.5.2.6 动力定型、超速试验时间的确定 158
7.5.3 钢套换向器典型工装结构 159
7.5.3.1 活压环结构 159
7.5.3.2 工艺衬套结构 159
7.5.3.3 分瓣夹具结构 159
7.5.3.4 拧螺母夹具结构 159
7.5.3.5 开合式支座结构 159
7.6 换向器质量检验 161
7.6.1 几何形状检验 161
7.6.2 绝缘强度检验 161
7.6.3 片间短路检验 161
7.7 换向器缺陷修复 162
7.8 换向器零件形位误差对组件质量的影响 162
第8章 集电环组件制造 164
8.1 集电环组件的分类及结构 164
8.1.1 集电环组件的分类及特点 164
8.1.2 集电环的分类及特点 165
8.2 集电环组件选用的材料 166
8.2.1 集电环材料 166
8.2.2 引出线材料 166
8.2.3 绝缘体材料 166
8.3 集电环组件的制造与工装 166
8.3.1 集电环和衬套的加工 166
8.3.1.1 集电环的加工 168
8.3.1.2 衬套的加工 169
8.3.2 集电环分组件的加工 169
8.3.2.1 集电环分组件加工工艺过程 169
8.3.2.2 集电环分组件加工技术要求 169
8.3.3 集电环组件的加工 169
8.3.3.1 套入式集电环组件的加工工艺过程 169
8.3.3.2 微型电机集电环组件加工工艺过程 170
8.3.3.3 带轴的集电环组件加工工艺过程 170
8.3.3.4 集电环模塑工艺典型操作要点 171
8.3.4 集电环组件模具主要设计结构 172
8.3.4.1 套入式集电环组件的典型模具结构 172
8.3.4.2 带轴的集电环组件的典型模具结构 173
8.4 集电环组件的质量检测 174
8.5 集电环组件常见缺陷及解决措施 175
第9章 定子、转子部件制造 176
9.1 绕线与嵌线 176
9.1.1 常用电磁线种类 176
9.1.2 线圈制造 177
9.1.2.1 主极线圈的制造工艺 177
9.1.2.2 换向极线圈与补偿线圈制造工艺 178
9.1.2.3 线圈电泳涂漆 180
9.1.2.4 电枢硬元件制造工艺 181
9.1.3 嵌线 184
9.1.3.1 嵌线前的准备 184
9.1.3.2 交流定子绕组的嵌线 185
9.1.3.3 转子绕组嵌线 186
9.1.4 转子绕组端部绑扎工艺 191
9.1.4.1 钢丝绑扎工艺要点 191
9.1.4.2 套钢环的工艺要点 192
9.2 绕组焊接工艺 192
9.2.1 航空电机绕组焊接特点及分类 192
9.2.1.1 航空电机绕组焊接特点 192
9.2.1.2 电机绕组焊接的分类 193
9.2.1.3 电机绕组焊接常用焊料 193
9.2.2 定子绕组接线头的焊接工艺 194
9.2.2.1 定子绕组接线头的软钎焊工艺 194
9.2.2.2 定子绕组接线头的硬钎焊工艺 194
9.2.3 直流电机换向器焊接工艺 194
9.2.3.1 换向器浸渍钎焊焊接工艺 194
9.2.3.2 换向器电阻钎焊焊接工艺 194
9.2.3.3 换向器氩弧焊焊接工艺 195
9.2.3.4 换向器点焊(热压焊)焊接工艺 197
9.3 定子装配 198
9.3.1 直流电机定子装配 198
9.3.1.1 直流小电机定子装配 198
9.3.1.2 直流大电机定子装配 199
9.3.2 变流机定子装配 199
9.4 转子精加工 199
9.4.1 转子精加工工艺过程 199
9.4.2 转子精加工工艺要点 200
9.4.2.1 加工余量的确定 200
9.4.2.2 转子精加工前的检查工作 200
9.4.2.3 铁芯轴径磨削加工工艺 200
9.4.2.4 铣云母槽加工工艺 201
9.4.2.5 换向器车削加工工艺 201
9.4.2.6 软轴装配工艺 202
9.5 转子平衡试验 202
9.5.1 转子不平衡的类型及校正方法 202
9.5.1.1 转子平衡条件及不平衡现象 202
9.5.1.2 静平衡与动平衡 203
9.5.1.3 不平衡量的表达方式 203
9.5.2 转子平衡试验方法 203
9.5.2.1 静平衡试验方法 203
9.5.2.2 动平衡试验方法 205
9.5.2.3 不平衡量的校正 206
9.6 质量检查 207
9.6.1 主要检查项目的设置 207
9.6.2 直流电机转子换向器焊接质量检查 208
9.6.3 主要检查项目的检测原理及方法 208
9.6.3.1 短路检测原理及方法 208
9.6.3.2 圈数检验工具的原理及使用方法 210
9.6.3.3 绝缘介电强度试验 211
第10章 绝缘处理 213
10.1 航空电机绝缘处理方法及工艺特点 213
10.1.1 绝缘处理的目的 213
10.1.2 绝缘漆的选择原则 214
10.1.3 绝缘处理方法及其工艺特点 214
10.1.3.1 零组件浸漆 214
10.1.3.2 工艺方法及特点 214
10.1.4 常用的绝缘处理设备 216
10.2 绝缘处理工艺技术 217
10.2.1 工艺过程 217
10.2.2 工艺参数的确定 217
10.2.2.1 预烘温度、时间的确定 217
10.2.2.2 固化温度、时间的确定 218
10.2.2.3 浸漆次数与粘度的确定 219
10.2.2.4 浸漆真空度、压力的确定 222
10.2.2.5 滴落浸漆工艺参数的确定 222
10.2.3 工艺操作要点 223
10.2.3.1 沉浸操作要点 223
10.2.3.2 滴浸操作要点 226
10.2.3.3 涂漆操作要点 226
10.2.3.4 绝缘漆的使用及贮存 227
10.2.4 绝缘处理中的常见故障及排除方法 227
10.2.5 绝缘处理中的安全技术措施 228
10.2.5.1 常见溶剂、稀释剂的特性 228
10.2.5.2 安全技术措施 229
10.3 绝缘处理质量检查 229
10.3.1 绝缘漆的质量检查 229
10.3.2 绝缘处理工艺过程中的质量检查 230
10.3.3 绝缘电阻的测量 230
10.4 绝缘材料的相容性 231
10.4.1 电机绝缘结构的基本组成 231
10.4.2 相容性试验方法及应用 231
10.4.2.1 相容性试验方法 231
10.4.2.2 电磁线与绝缘漆的相容性试验 232
10.4.2.3 绝缘结构中各组份间的相容性试验 233
10.4.3 电机绝缘结构相容性可靠性试验程序 235
第11章 电机的总装 236
11.1 电刷组件制造 236
11.1.1 组装 236
11.1.1.1 电刷的功能 236
11.1.1.2 电刷的分类 236
11.1.1.3 组装 236
11.1.2 焊接 239
11.1.3 弧度加工的要求 239
11.1.3.1 电刷弧度加工的要求 239
11.1.3.2 电刷弧度的加工方法 239
11.2 刷握装配 240
11.2.1 装配工艺 240
11.2.1.1 刷握装配工艺原则 240
11.2.1.2 刷握结构 240
11.2.1.3 刷握装配工艺过程 242
11.2.1.4 刷握装配工艺要点 243
11.2.1.5 刷握装配工具 244
11.2.2 弹簧压力调整 245
11.2.2.1 弹簧压力调整的工艺方法 245
11.2.2.2 弹簧压力调整工具 246
11.3 端盖装配 247
11.3.1 装配工艺 247
11.3.1.1 端盖装配的工艺过程 247
11.3.1.2 前端盖装配工艺要点 249
11.3.1.3 后端盖装配工艺要点 250
11.3.1.4 端盖装配常用辅助材料 254
11.3.1.5 端盖装配工具 254
11.3.2 刷盒校正 255
11.4 减速器及离合器装配 257
11.4.1 减速器装配 257
11.4.1.1 减速器结构特点 257
11.4.1.2 减速器装配工艺 258
11.4.2 离合器装配 259
11.4.2.1 离合器结构特点 259
11.4.2.2 离合器装配工艺 260
11.5 永久磁钢充磁、稳磁、退磁 261
11.5.1 永久磁钢的充磁 261
11.5.1.1 永久磁钢的充磁工艺 261
11.5.1.2 永久磁钢充磁的工艺要点 262
11.5.2 永久磁钢的稳磁 262
11.5.2.1 永久磁钢的稳磁工艺 262
11.5.2.2 永久磁钢稳磁工艺要点 263
11.5.3 永久磁钢的退磁 264
11.5.3.1 旋转退磁工艺 264
11.5.3.2 静止退磁工艺 265
11.6 电机总装配 265
11.6.1 总装工艺 265
11.6.1.1 总装工艺技术要求 265
11.6.1.2 电机总装工艺过程 266
11.6.1.3 电机总装的压装工艺 267
11.6.1.4 电机总装的螺装工艺 271
11.6.1.5 电机总装的销装工艺 275
11.6.1.6 收口工艺 278
11.6.1.7 电机装调质量故障特征、排除方法 279
11.6.2 工艺要点 281
11.6.2.1 电机的磨合 281
11.6.2.2 电机的轴向间隙检查 284
11.7 电机调整试验 286
11.7.1 直流电动机的调速 286
11.7.1.1 调节电枢回路电阻改变转速 287
11.7.1.2 调节励磁电流改变转速 287
11.7.1.3 移动电刷方向改变转速 288
11.7.2 直流电机换向火花和直流电动机输入电流的调整 288
11.7.2.1 直流电机换向火花、电动机输入电流的调整方法、要点 288
11.7.2.2 直流电机电刷位移对电机性能的影响 289
11.7.3 直流电机几何中性线的调整 289
11.7.3.1 移动刷握位置确定几何中性线 290
11.7.3.2 测量仪表沿换向器圆周表面移动确定几何中性线 290
11.7.3.3 调整要点 290
第12章 电机试验 291
12.1 试验目的和要求 291
12.1.1 试验目的 291
12.1.2 试验要求 291
12.2 试验类型 291
12.2.1 检查试验项目 291
12.2.2 型式试验项目 295
12.3 型式试验项目的技术要求和试验方法 296
12.3.1 电气性能试验项目的技术要求和试验方法 296
12.3.2 机械性能试验项目的技术要求和试验方法 298
12.3.3 环境性能试验项目的技术要求和试验方法 299
12.3.4 其它性能试验项目的技术要求 300
12.3.5 电机的寿命试验 300
第2篇 航空电器制造技术 301
第13章 概述 301
13.1 航空电器产品的分类 301
13.2 航空电器产品系列简介 302
13.2.1 电源控制电器 302
13.2.2 推进控制电器 302
13.2.3 防火电器 303
13.2.4 断路器 304
13.2.5 开关 304
13.2.6 灯具 304
13.2.7 电能变换电器 305
13.3 航空电器制造技术的发展趋势 305
第14章 电器零件制造 307
14.1 冲压制造工艺 307
14.1.1 精密冲压件 307
14.1.1.1 弹性零件的精密冲压 308
14.1.1.2 典型弹性零件冲压 309
14.1.1.3 小间隙光洁冲切 309
14.1.1.4 典型零件的级进冲切 311
14.1.2 弯曲件加工工艺 311
14.1.2.1 弯曲件展开长度计算 312
14.1.2.2 弯曲件模具凸模与凹模尺寸的确定 326
14.1.2.3 提高弯曲零件质量的措施 327
14.1.2.4 典型弯曲件加工工艺示例 328
14.1.3 拉深件加工工艺 334
14.1.3.1 拉深件的类型及工艺特点 334
14.1.3.2 拉深件的拉深工艺及计算 335
14.1.3.3 圆筒形拉深件的工艺计算 337
14.1.3.4 高矩形(正方截面)拉深件的工艺计算 341
14.1.3.5 拉深过程中的润滑与热处理 349
14.1.4 冷挤压件加工工艺 350
14.1.4.1 冷挤压件的工艺要求 350
14.1.4.2 小矩形外罩冷挤压加工工艺 351
14.1.4.3 小矩形外罩冷挤压的许用变形程度和冷挤压力计算 353
14.1.4.4 其他典型冷挤压零件加工工艺 355
14.2 精密零件的切削加工工艺 356
14.2.1 细长杆形零件的加工工艺 356
14.2.1.1 工件的装夹方法 356
14.2.1.2 细长轴用的车刀 358
14.2.1.3 切削用量 358
14.2.1.4 实例:心杆加工工艺方法 358
14.2.2 薄壁筒形零件的加工工艺 359
14.2.2.1 工件的装夹方法 359
14.2.2.2 刀具及切削用量 359
14.2.2.3 实例:衬筒加工工艺方法 360
14.3 特殊热处理 361
14.3.1 银镁镍合金簧片的内氧化热处理 361
14.3.1.1 银镁镍合金材料的性能 361
14.3.1.2 银镁镍合金软化退火处理 362
14.3.1.3 银镁镍合金内氧化热处理 362
14.3.1.4 内氧化温度、时间对银镁镍合金性能的影响 363
14.3.2 钯银铜镍合金强化热处理工艺 367
14.3.2.1 钯银铜镍合金接点制造 367
14.3.2.2 PdAgCuNi40-18-2合金的热处理 367
14.3.2.3 常见的缺陷及解决措施 368
14.3.3 铁镍软磁合金的热处理 368
14.3.3.1 热处理工艺的种类及目的 368
14.3.3.2 热处理前的准备 369
14.3.3.3 热处理规范及其选择 369
14.3.3.4 零件热处理后的故障及排除方法 373
14.4 玻璃封接工艺 374
14.4.1 玻璃封接件的技术要求 374
14.4.2 玻璃封接的分类 375
14.4.3 玻璃封接对材料的要求 376
14.4.3.1 封接用玻璃的基本要求和技术指标 376
14.4.3.2 封接用金属材料的基本要求和技术指标 377
14.4.4 玻璃封接工艺 377
14.4.4.1 封接前金属件的准备 381
14.4.4.2 封接玻璃毛坯制造 382
14.4.4.3 封接件的封接技术 382
14.4.4.4 封接件的后处理 383
14.4.4.5 封接件的表面处理 383
14.4.5 玻璃封接件的检测 384
14.5 陶瓷金属化工艺 385
14.5.1 陶瓷金属化工艺过程 385
14.5.2 陶瓷金属化配方 385
14.5.3 钼-锰法陶瓷金属化工艺要点 386
14.5.4 陶瓷金属化的缺陷及处理方法 387
14.6 特种零件的电镀 388
14.6.1 双金属元件电镀 388
14.6.2 金钴合金电镀 390
14.7 塑料制件工艺 393
14.7.1 塑料制件的设计 393
14.7.1.1 塑料制件结构及其工艺性要求 394
14.7.1.2 金属嵌件结构及其工艺性要求 397
14.7.1.3 塑料制件、金属嵌件结构的工艺尺寸及要求 398
14.7.2 塑料制件的成型工艺 400
14.7.2.1 热固性塑料成形 400
14.7.2.2 热塑性塑料注射成形工艺 410
14.7.2.3 热塑性塑料双色注射成形工艺 414
14.7.3 塑料制件的后处理 418
14.7.4 塑料制件的修整 419
14.8 标记工艺 420
14.8.1 移印工艺 420
14.8.1.1 油墨的选择及调配 420
14.8.1.2 工艺规范的选择 421
14.8.1.3 移印模制造 421
14.8.1.4 印制操作要求 421
14.8.1.5 常见移印质量问题及排除方法 421
14.8.2 丝网印刷工艺 423
14.8.2.1 丝网的制造 423
14.8.2.2 油墨的选择和调配工艺 424
14.8.2.3 工艺要点及质量要求 425
14.8.3 光学腐蚀工艺 425
14.8.3.1 铭牌工艺方法 425
14.8.3.2 信号牌、指示牌的工艺方法 425
14.8.4 刻字工艺 426
第15章 电器组件制造 427
15.1 触点的制造 427
15.1.1 航空电器的触点材料 427
15.1.2 触点的种类 428
15.1.3 触点的制造 430
15.1.4 触点表面的润滑与保护 432
15.1.5 触点制造中产生的缺陷及解决方法 432
15.2 线圈的制造 433
15.2.1 绕组的绕制方法 433
15.2.2 线圈的加工技术 434
15.2.3 绕线设备的选择 440
15.2.4 灌注 441
15.3 双金属元件的制造 443
15.3.1 双金属元件的分类 443
15.3.2 双金属元件制造的工艺过程 447
15.3.3 典型元件的成形 447
15.3.4 双金属元件的热处理 448
15.3.4.1 热处理参数的选择 448
15.3.4.2 典型热处理工艺曲线 449
15.3.5 双金属元件的焊接 449
15.3.6 常见缺陷及排除方法 450
15.4 热敏元件的制造 451
15.4.1 热敏体的结构 451
15.4.2 热敏体的制造工艺 452
15.4.2.1 热敏体制造的工艺过程 452
15.4.2.2 热敏元件制造的工艺要点 452
15.4.3 常见故障及排除方法 454
第16章 电器装配 455
16.1 航空电器的通用装配技术 455
16.1.1 引出线制备 455
16.1.1.1 常用引出线种类及适用范围 455
16.1.1.2 引出线制备过程 455
16.1.2 零组件连接 455
16.1.3 产品的灌封 456
16.1.4 磁性处理 457
16.1.4.1 磁钢磁性处理工艺过程 457
16.1.4.2 磁性处理工艺要点 457
16.1.5 引出线线束焊接与固定 458
16.1.6 调整试验 460
16.2 密封继电器的装配技术 462
16.2.1 清洗技术 466
16.2.1.1 漂洗 468
16.2.1.2 超声波清洗 468
16.2.1.3 三氯三氟乙烷清洗 469
16.2.1.4 氮吹 470
16.2.2 焊接技术 470
16.2.2.1 电容贮能点焊 471
16.2.2.2 电阻钎焊 471
16.2.2.3 微型火焰钎焊 473
16.2.3 气密性技术 474
16.2.3.1 高频感应钎焊 476
16.2.3.2 直流氩弧焊(半自动钨极氩弧焊) 480
16.2.3.3 微束等离子弧焊 480
16.2.3.4 真空电子束焊 481
16.2.3.5 激光焊 485
16.2.3.6 充气孔密封焊接 488
16.2.4 装配调整技术 489
16.2.4.1 主要调整参数 489
16.2.4.2 典型密封继电器的装配与调整 491
16.2.4.3 机械时效 493
16.2.4.4 装调中常见故障和检验方法 493
16.2.5 充氮技术 498
16.2.5.1 其空烘烤 498
16.2.5.2 氮气的净化及充氮 499
16.2.5.3 泄漏率测试 503
16.2.6 洁净技术 505
16.2.6.1 洁净技术的基本要求及技术措施 505
16.2.6.2 密封继电器洁净技术的应用 507
16.2.6.3 洁净度测试 508
16.2.7 可靠性筛选 509
16.2.7.1 筛选技术要求 509
16.2.7.2 筛选方法 509
16.2.7.3 筛选后的处理 511
16.2.7.4 筛选测试设备 511
第17章 电器试验 514
17.1 试验目的和要求 514
17.2 试验类型 514
17.2.1 检查试验项目 514
17.2.2 型式试验项目 516
17.3 型式试验项目的技术要求 519
17.3.1 电气性能试验 519
17.3.2 机械性能试验 523
17.3.3 环境性能试验 523
17.3.4 其他性能试验 524
17.3.4.1 微动开关基本性能的无接触测试 524
17.3.4.2 防撞灯有效光强的自动测试系统 524
17.3.5 寿命试验 526
第18章 防锈与包装 530
18.1 电机电器防锈与包装的常用材料 530
18.1.1 防锈与包装用纸 530
18.1.2 洗涤剂 530
18.1.3 防锈油脂 531
18.1.4 防锈水剂 532
18.1.5 有机薄膜 532
18.1.6 溶剂型可剥性塑料 533
18.1.7 热熔型可剥性塑料 534
18.2 电机电器的工序防锈 534
18.2.1 工序防锈的一般规定 534
18.2.2 防锈处理 535
18.2.2.1 防锈处理工艺程序及工艺方法 535
18.2.2.2 工序防锈常用方法及适用范围 535
18.2.2.3 防锈方法的特性对比 535
18.2.2.4 气相防锈材料使用方法 536
18.2.3 防锈设备 537
18.2.3.1 洗涤设备 537
18.2.3.2 防锈包装设备 537
18.3 电机电器的封存包装 538
18.3.1 封存包装分类 538
18.3.2 封存包装工艺 538
18.3.2.1 防潮包装 538
18.3.2.2 充氮封存 539
18.3.2.3 气相封存 540
18.3.2.4 出厂产品的封存包装 540
18.4 防锈包装的质量控制 541
18.5 产品常见锈蚀类别和预防措施 542
第3篇 航空火花塞制造技术 543
第19章 航空火花塞产品概述 543
19.1 航空火花塞的主要功能 543
19.2 航空火花塞和附件的分类与结构特点 543
19.2.1 航空火花塞的分类与结构特点 543
19.2.2 航空火花塞附件的分类与结构特点 543
19.3 催化点火器的结构特点 546
19.4 航空发动机的工作条件对火花塞制造的技术要求 546
19.5 航空火花塞制造技术的发展方向 547
19.5.1 半导体火花塞的发展方向 547
19.5.2 沿面间隙火花塞的发展方向 547
19.5.3 火花塞工艺的发展方向 547
第20章 航空火花塞陶瓷零件制造技术 548
20.1 航空火花塞陶瓷材料的基本特性和主要原料成份 548
20.1.1 航空火花塞陶瓷材料的基本特性 548
20.1.2 航空火花塞陶瓷材料的主要原料成份 548
20.2 航空火花塞陶瓷零件制造技术 549
20.2.1 航空火花塞陶瓷零件制造工艺过程 549
20.2.2 陶瓷备料 549
20.2.2.1 陶瓷备料工艺过程 549
20.2.2.2 陶瓷备料技术 549
20.2.3 陶瓷成型 551
20.2.3.1 陶瓷成型方法分类 551
20.2.3.2 陶瓷热压注成型常见废品种类及预防措施 555
20.2.4 陶瓷排蜡 556
20.2.4.1 排蜡技术 556
20.2.4.2 影响坯件排蜡的因素 557
20.2.4.3 坯件排蜡典型曲线 557
20.2.4.4 坯件排蜡填料种类及要求 557
20.2.4.5 排蜡坯件废品及预防 558
20.2.5 陶瓷烧成 558
20.2.5.1 陶瓷烧成方法分类 558
20.2.5.2 陶瓷烧成影响因素 558
20.2.5.3 陶瓷烧结过程三阶段 558
20.2.5.4 陶瓷H2炉焙烧技术要点 559
20.2.6 陶瓷零件精加工与正火处理 559
20.2.7 陶瓷施釉 559
20.2.7.1 釉的分类 559
20.2.7.2 釉中氧化物的功能选择 560
20.2.7.3 陶瓷用釉的典型制备技术 561
20.2.7.4 陶瓷施釉方法 562
20.2.8 陶瓷零件的验收 562
20.3 半导体陶瓷电阻制造技术 564
20.3.1 半导体陶瓷电阻制造工艺过程 564
20.3.2 半导体陶瓷电阻制造技术 564
20.3.2.1 备料技术 564
20.3.2.2 挤压成型技术 565
20.3.2.3 氨气电炉焙烧技术 565
20.3.2.4 坯件清理技术 566
20.3.2.5 涂银、烧银技术 566
20.3.2.6 压紧帽盖技术 566
20.3.2.7 施釉与釉烧技术 566
20.3.2.8 热稳定与电稳定处理 566
20.3.2.9 半导体陶瓷电阻验收 566
第21章 航空火花塞金属零件制造技术 567
21.1 航空火花塞金属零件材料的选择 567
21.1.1 主要材料选择原则 567
21.1.2 常用材料的特性和适用范围 567
21.2 螺纹加工 568
21.2.1 车制螺纹法 568
21.2.1.1 车刀的选择 568
21.2.1.2 工艺参数的选择 568
21.2.1.3 常见故障及原因分析 568
21.2.2 滚制螺纹法 569
21.2.3 攻制螺纹法 570
21.2.3.1 丝锥材料的选择 570
21.2.3.2 孔的预加工尺寸 570
21.2.3.3 冷却液的选择 570
21.2.4 铣削螺纹法 571
21.3 典型零件的加工方法 571
21.3.1 壳体的加工 571
21.3.1.1 壳体的结构特征 571
21.3.1.2 加工要点 572
21.3.1.3 典型零件加工要点 572
21.3.2 心杆和中心电极的加工 578
21.3.2.1 结构特征 578
21.3.2.2 典型零件加工过程 579
第22章 航空火花塞装配技术 581
22.1 航空火花塞的典型结构 581
22.2 航空火花塞的密封技术 581
22.2.1 密封剂密封 581
22.2.1.1 密封剂选择原则 581
22.2.1.2 密封剂的种类及工艺要点 581
22.2.2 机械密封技术 582
22.3 航空火花塞零部件的胶合固定技术 582
22.3.1 耐热水泥胶合剂的种类 582
22.3.2 耐热水泥稳定处理 582
22.4 典型航空火花塞装配技术 583
22.4.1 电蚀火花塞装配技术 583
22.4.1.1 电蚀火花塞绝缘体组件装配 583
22.4.1.2 电蚀火花塞总装 584
22.4.2 半导体火花塞装配技术 585
22.4.2.1 半导体火花塞绝缘体组件装配 586
22.4.2.2 半导体火花塞总装 587
22.5 导电杆装配技术 589
22.5.1 导电杆结构 589
22.5.2 导电杆绝缘体组件装配 589
22.5.3 导电杆壳体组件装配 590
22.5.4 导电杆总装配 593
第23章 航空火花塞试验 595
23.1 试验目的 595
23.2 试验要求 595
23.3 试验类型 595
23.4 试验项目与试验方法 596
23.4.1 检查试验项目和试验方法 596
23.4.1.1 检查试验项目 596
23.4.1.2 检查试验方法 596
23.4.2 型式试验项目和试验方法 600
23.4.3 航空火花塞附件的检查试验项目和试验方法 601
23.5 航空火花塞常用试验设备 602
23.6 航空火花塞试验中常见故障分析及处理方法 605