图书介绍
航空制造工程手册 弹性元件工艺pdf电子书版本下载
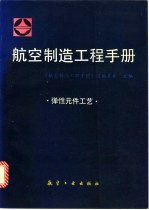
- 《航空制造工程手册》总编委会主编 著
- 出版社: 北京:航空工业出版社
- ISBN:7800468690
- 出版时间:1994
- 标注页数:445页
- 文件大小:34MB
- 文件页数:461页
- 主题词:
PDF下载
下载说明
航空制造工程手册 弹性元件工艺PDF格式电子书版下载
下载的文件为RAR压缩包。需要使用解压软件进行解压得到PDF格式图书。建议使用BT下载工具Free Download Manager进行下载,简称FDM(免费,没有广告,支持多平台)。本站资源全部打包为BT种子。所以需要使用专业的BT下载软件进行下载。如 BitComet qBittorrent uTorrent等BT下载工具。迅雷目前由于本站不是热门资源。不推荐使用!后期资源热门了。安装了迅雷也可以迅雷进行下载!
(文件页数 要大于 标注页数,上中下等多册电子书除外)
注意:本站所有压缩包均有解压码: 点击下载压缩包解压工具
图书目录
第1章 总论 1
1.1 概述 1
1.2 工艺对弹性元件性能的影响 3
1.2.1 试验批 3
1.2.2 原材料 3
1.2.3 冷加工 4
1.2.4 热处理 4
1.2.5 焊接 4
1.2.6 表面处理 4
1.2.7 组装工序 4
1.2.8 稳定工序 4
1.2.9 检测 4
1.3 弹性元件的特性 5
1.3.1 弹性特性 5
1.4 弹性元件的温度误差 6
1.3.2 非弹性特性 6
第2章 弹性元件用材料 8
2.1 弹性元件材料的选用 8
2.2 弹性元件材料的分类 9
2.3 弹簧常用钢材 9
2.4 不锈钢 14
2.5 铜合金 16
2.5.1 黄铜、锡青铜和硅青铜 20
2.5.2 铍青铜 22
2.6 精密弹性合金 24
2.6.1 高弹性合金 24
2.6.2 恒弹性合金 29
2.7 其他弹性合金 30
2.8 各国常用弹性材料牌号对照 32
2.9 非金属弹性材料 34
3.1.1.1 淬火和回火 35
3.1.1 弹簧钢弹性元件的热处理 35
3.1 弹性元件的热处理 35
第3章 弹性元件的热处理、表面处理及焊接 35
3.1.1.2 消除应力低温退火 37
3.1.1.3 时效处理 38
3.1.1.4 软化处理 38
3.1.2 铜合金弹性元件的热处理 39
3.1.2.1 黄铜的热处理 39
3.1.2.2 锡青铜的热处理 40
3.1.2.3 铍青铜的热处理 40
3.1.2.4 镍铜合金的热处理 43
3.1.3 不锈钢弹性元件的热处理 43
3.1.3.1 奥氏体不锈钢的热处理 43
3.1.3.2 马氏体不锈钢的热处理 44
3.1.3.3 马氏体时效不锈钢的热处理 44
3.1.4.1 铁-镍-铬基弥散强化型高弹性合金的热处理 45
3.1.4 精密弹性合金弹性元件的热处理 45
3.1.4.2 钴基高弹性合金的热处理 46
3.1.4.3 镍基弥散强化型高弹性合金的热处理 47
3.1.4.4 低碳高镍型超高强度马氏体时效钢的热处理 47
3.1.4.5 铁磁性弥散强化型恒弹性合金的热处理 47
3.1.4.6 其他弹性合金、高温合金和工业纯钛的热处理 49
3.2 弹性元件的表面处理 50
3.2.1 用途 50
3.2.1.1 弹性元件表面处理的用途 50
3.2.1.2 表面处理对弹性元件的影响 50
3.2.1.3 表面处理工艺的图纸标记 50
3.2.2 表面清理和强化 51
3.2.2.1 工艺性污物的清理 51
3.2.2.2 氧化皮的清理 52
3.2.2.3 喷丸 53
3.2.3.1 典型工艺流程 54
3.2.2.4 质量要求和故障排除 54
3.2.3 微量削减尺寸 54
3.2.3.2 化学法去尺寸工艺 55
3.2.3.3 电化学法去尺寸工艺 56
3.2.3.4 膜片和波纹管的去尺寸处理 57
3.2.3.5 弹性元件组合件的表面处理 59
3.2.3.6 光亮处理 60
3.2.3.7 质量要求和故障排除 60
3.2.4 电镀和化学镀 60
3.2.4.1 工艺目的和镀液类型 61
3.2.4.2 工艺配方 61
3.2.4.3 钢弹簧的电镀 62
3.2.4.4 质量要求和故障排除 62
3.2.5 化学转化膜 62
3.2.5.1 钢铁氧化 62
3.2.5.3 铜合金钝化 63
3.2.5.2 钢铁磷化 63
3.2.5.4 不锈钢钝化 64
3.2.5.5 质量要求和故障排除 64
3.2.6 有机涂层 64
3.2.6.1 涂料 64
3.2.6.2 粉末涂覆层 66
3.2.7 防锈 66
3.2.7.1 工序间防锈 66
3.2.7.2 防锈处理 67
3.2.7.3 储运中防锈 67
3.3 弹性敏感元件焊接工艺 68
3.3.1 对焊接工艺的基本要求 68
3.3.2 弹性材料的焊接性 69
3.3.3 低温钎焊 69
3.3.3.1 钎料与钎剂 69
3.3.3.2 接头形式 70
3.3.3.3 用电烙铁加热的手工钎焊 71
3.3.3.4 真空感应钎焊 72
3.3.3.5 弹簧管组合件的电阻钎焊 73
3.3.4 高温钎焊 74
3.3.4.1 手工火焰钎焊 74
3.3.4.2 膜盒中心杆的电阻钎焊 74
3.3.4.3 使用硬钎料的真空高温钎焊 75
3.3.5 电阻焊 76
3.3.5.1 点焊 77
3.3.5.2 凸焊 77
3.3.5.3 电阻缝焊 78
3.3.6 熔焊 80
3.3.6.1 接头形式及夹具设计 80
3.3.6.2 小电流钨极氩弧焊 83
3.3.6.3 微束等离子弧焊接 84
3.3.6.4 真空电子束焊接 85
3.3.6.5 熔焊的质量检验 87
3.3.7 弹性元件的封接 88
3.3.7.1 软钎料封接 88
3.3.7.2 贵金属钎料高温封接 89
3.3.7.3 熔焊封接 90
第4章 螺旋弹簧 92
4.1 用途、类型和特性 92
4.2 材料及许用应力 94
4.2.1 材料的选择 94
4.2.2 许用应力 98
4.3 设计计算 98
4.3.1 圆柱螺旋压缩和拉伸弹簧的设计 98
4.3.1.1 基本结构 98
4.3.1.2 基本计算公式 101
4.3.1.3 强度校核 107
4.3.2.1 基本结构 109
4.3.2 圆柱螺旋扭转弹簧的设计 109
4.3.2.2 基本计算公式 111
4.3.3 截锥螺旋弹簧的设计 113
4.3.3.1 基本结构 113
4.3.3.2 计算公式 114
4.3.4 典型工作图样 115
4.4 制造工艺 117
4.4.1 工艺特点 118
4.4.2 工艺技术准备 118
4.4.2.1 工作图样的审核 118
4.4.2.2 工艺规程的编制 120
4.4.3 绕制 123
4.4.3.1 有心绕制 124
4.4.3.2 无心绕制 130
4.4.4.1 压缩弹簧的端部加工 139
4.4.4 端部加工 139
4.4.4.2 拉伸弹簧的端部加工 143
4.4.4.3 扭转弹簧的端部加工 146
4.4.5 热处理 147
4.4.5.1 热处理类型 147
4.4.5.2 热处理的变形 147
4.4.5.3 常见缺陷及预防 151
4.4.6 表面处理 151
4.4.7 特殊处理 152
4.4.7.1 立定处理 152
4.4.7.2 强压处理 153
4.4.7.3 加温立定处理 156
4.4.7.4 喷丸处理 158
4.4.7.5 电化学抛光 158
4.5.1 制造精度与允许偏差 159
4.5 检查与试验 159
4.5.2.1 外观检验 164
4.5.2 外观及几何尺寸的检验 164
4.5.2.2 几何尺寸的检验 165
4.5.3 特性检验 167
4.5.3.1 压缩和拉伸弹簧的特性检验 167
4.5.3.2 扭转弹簧的特性检验 168
4.5.4 疲劳试验 170
4.5.5 模拟试验 171
4.6 失效分析 172
4.6.1 失效分析程序 172
4.6.2 断裂失效 172
4.6.3 永久变形 173
4.6.4 典型失效实例 174
5.1.1 碟簧的结构形式 177
5.1.2 A型碟簧计算 177
5.1 碟形弹簧的计算 177
第5章 碟形弹簧 177
5.1.3 B型碟簧计算 179
5.1.4 碟簧推荐尺寸系列 181
5.1.5 碟簧特性曲线 183
5.1.6 许用应力 184
5.2 碟形弹簧的制造工艺 185
5.2.1 碟簧制造的特点 185
5.2.2 碟簧的制造工艺流程 186
5.2.3 碟簧的典型制造工艺 186
5.2.3.1 备料 186
5.2.3.2 冲裁 187
5.2.3.3 机械加工 187
5.2.3.4 成形 189
5.2.3.6 热处理 190
5.2.3.5 支承面加工 190
5.2.3.7 喷丸处理 193
5.2.3.8 强压处理 193
5.2.3.9 表面处理 194
5.2.4 碟簧的检验 195
5.2.4.1 外观检验 195
5.2.4.2 尺寸及形位公差检验 195
5.2.4.3 负荷检验 195
5.2.5 碟簧质量故障分析 197
第6章 平面涡卷弹簧 198
6.1 游丝 198
6.1.1 游丝的设计 198
6.1.2 游丝的制造工艺流程 199
6.1.3.1 拉伸方法 200
6.1.3 拉丝 200
6.1.3.2 拉伸配模 202
6.1.3.3 变形率控制原则 203
6.1.3.4 拉伸用润滑剂 204
6.1.3.5 带材辗压前丝材直径的确定 204
6.1.3.6 拉伸用模具 205
6.1.3.7 线材拉伸设备 206
6.1.3.8 拉丝废品的产生原因及特征 209
6.1.4 辗压 210
6.1.4.1 轧机 210
6.1.4.2 轧制道次及工艺的确定 211
6.1.4.3 厚度测量及控制 212
6.1.4.4 冷轧带材常见缺陷及预防 213
6.1.5 游丝的成形 214
6.1.5.1 盘绕 214
6.1.5.3 定形 215
6.1.5.4 分解与修整 215
6.1.5.2 淬火(固溶处理) 215
6.1.6 稳定化处理 216
6.1.7 游丝的性能测量 216
6.1.7.1 特性测试 216
6.1.7.2 弹性后效测量 219
6.1.7.3 力矩非线性测量 220
6.1.8 游丝及铜座的组合——游丝连铜座 221
6.1.9 游丝的检验 221
6.1.9.1 外观及几何尺寸检验 221
6.1.9.2 游丝形状检验 222
6.1.9.3 电测及转速仪表用游丝的无磁性检查 222
6.1.9.4 铁青铜制游丝的脆性检查 222
6.1.9.5 游丝连铜座的装配质量检验 223
6.2 刷握弹簧 224
6.2.1 概述 224
6.2.2 设计与计算 225
6.2.3 选材和许用应力 227
6.2.4 弹簧的制造工艺流程及工艺分析 228
6.2.4.1 制造工艺流程 228
6.2.4.2 工艺分析 228
6.2.5 毛料制造 229
6.2.6 绕制 230
6.2.7 热处理 233
6.2.8 弹性和特性检验 233
6.2.9 强扭处理 235
6.2.10 常见故障的产生原因及解决办法 236
6.3 发条 237
6.3.1 发条的结构与计算 237
6.3.1.1 发条结构 237
6.3.1.2 发条计算 239
6.3.3.2 滚剪 240
6.3.3 材料精制及滚剪 240
6.3.3.1 精拉、精轧 240
6.3.2 制造工艺程序 240
6.3.1.3 发条用材料 240
6.3.4 热处理 241
6.3.4.1 连续退火 241
6.3.4.2 连续淬回火 242
6.3.5 拉边、磨边 243
6.3.5.1 拉边 243
6.3.5.2 磨边 243
6.3.5.3 拉边、磨边的质量检查 244
6.3.6 抛光、切断、弯钩 245
6.3.6.1 抛光 245
6.3.6.2 切断 245
6.3.7.2 S形发条的定形处理 247
6.3.7.1 端头退火、热化 247
6.3.7 端头退火、热化及定形 247
6.3.6.3 弯钩 247
6.3.8 卷绕 248
6.3.9 检验 249
6.3.9.1 外观及尺寸检查 249
6.3.9.2 力矩测量 249
6.4 恒力弹簧 249
6.4.1 设计与计算 250
6.4.2 材料选择 251
6.4.3 制造工艺流程 251
6.4.4 绕制 251
6.4.5 热处理 252
6.4.6 检验 252
6.4.7 常见故障产生的主要原因及解决办法 252
7.1.3 膜片、膜盒的选用原则 253
7.1.2 膜片、膜盒的用途 253
7.1.1 膜片、膜盒的分类 253
第7章 膜片与膜盒 253
7.1 概述 253
7.1.4 膜片、膜盒的典型结构及尺寸标注 254
7.1.5 膜片、膜盒的特性要求 256
7.1.6 集中力与有效面积 257
7.2 膜片型面的设计及特性计算 257
7.2.1 平膜片的设计计算 257
7.2.1.1 平膜片简介 257
7.2.1.2 平膜片“压力-位移”特性计算 258
7.2.1.3 平膜片有效面积计算 259
7.2.1.4 凸形膜片及其跳跃特性 259
7.2.1.5 方形膜片 260
7.2.2.1 波纹膜片的特点 261
7.2.2.2 膜片型面参数对“压力-位移”特性的影响 261
7.2.2 波纹膜片的设计计算 261
7.2.2.3 波纹膜片弹性特性曲线的近似计算公式 265
7.2.2.4 几种典型波纹型面的近似计算 267
7.2.2.5 压力与位移呈线性的膜片型面设计计算 270
7.2.2.6 非线性特性膜片型面选择与计算 271
7.2.2.7 按给定特性曲线设计波纹膜片型面 272
7.2.2.8 试验法设计波纹膜片型面 273
7.2.2.9 波纹膜片有效面积计算 275
7.2.2.10 波纹膜片的过载保护 276
7.2.2.11 设计膜片型面的一般原则 277
7.2.2.12 部分典型膜片型面及其特性曲线图例 278
7.3 金属膜片、膜盒制造工艺 287
7.3.1 几点说明 287
7.3.2 金属膜片、膜盒的典型工艺流程 288
7.3.2.1 基本规定 288
7.3.2.2 膜片、膜盒的典型工艺流程 288
7.3.3.1 条料精轧(辗压) 292
7.3.3 金属膜片、膜盒加工的主要工序 292
7.3.3.2 膜片成形 295
7.3.3.3 膜片热处理时效夹具 303
7.3.3.4 气密性检查 305
7.3.3.5 稳定处理 308
7.3.3.6 性能检测 310
第8章 波纹管及其组件 317
8.1 概述 317
8.1.1 结构参数 317
8.1.2 主要类型及特点 317
8.1.3 波形 319
8.1.4 多层波纹管 320
8.1.5 常用材料及选材原则 320
8.1.6 波纹管在航空器中的应用 321
8.2.1 结构参数 322
8.2 波纹管的结构参数、特性参数及计算 322
8.2.2 特性参数 323
8.2.3 设计计算 324
8.2.3.1 内容和要求 324
8.2.3.2 弹性特性、安全位移及残余变形 324
8.2.3.3 刚度和工作应力 326
8.2.3.4 有效面积 329
8.2.3.5 耐压强度、安全压力和工作压力 330
8.2.3.6 疲劳强度、工作寿命和可靠性 331
8.3 波纹管的制造工艺 334
8.3.1 无缝单层波纹管的典型工艺流程 334
8.3.2 管坯制造 335
8.3.2.1 多次拉伸法 335
8.3.2.2 旋压拉伸法 341
8.3.3 波纹成形 345
8.3.3.1 成形方法的比较和选取 345
8.3.2.3 轧制和焊接法 345
8.3.3.2 液压成形 346
8.3.3.3 滚压成形 352
8.3.3.4 滚压-液压成形 352
8.3.3.5 电沉积成形 353
8.3.3.6 化学沉积成形 355
8.3.4 整形和稳定 358
8.3.4.1 整形 358
8.3.4.2 稳定 358
8.3.5 性能检测 359
8.3.5.1 气密性检查及设备 359
8.3.5.2 刚度测量及其仪器 360
8.3.5.3 有效面积的测试及设备 361
8.3.5.4 残余变形百分率的测定 362
8.3.5.5 安全压力的测定及设备 362
8.4 波纹管组件的制造工艺 363
8.3.5.6 工作寿命、疲劳强度的试验及设备 363
8.4.1 压力波纹管组件制造工艺 364
8.4.1.1 典型工艺流程 364
8.4.1.2 典型工艺流程的主要控制要求 364
8.4.2 真空波纹管组件制造工艺 364
8.4.2.1 典型工艺流程 364
8.4.2.2 典型工艺流程的主要控制要求 365
8.4.3 充液、充气波纹管组件制造工艺 366
8.4.4 组合焊接 366
8.4.5 气密性检查 366
8.4.6 稳定处理及设备 366
8.4.7 工质的充灌 367
8.4.7.1 工质 367
8.4.7.2 充灌工艺控制及设备 368
8.4.8 性能检测 369
8.5.1 基本类型 370
8.5.2 基本性能 370
8.5 焊接波纹管 370
8.5.3 优点 371
8.5.4 设计计算 371
8.5.4.1 参数代号 371
8.5.4.2 计算公式 372
8.5.4.3 计算曲线图 373
8.5.4.4 刚度、非线性度的影响因素 373
8.5.4.5 常用材料 374
8.5.4.6 膜片型面选择 375
8.5.4.7 设计计算示例 376
8.5.5 制造工艺 377
8.5.5.1 膜片制造 377
8.5.5.2 焊接组合工艺 378
8.5.5.3 微束等离子焊接 381
8.5.5.5 检查试验 382
8.5.5.4 电子束焊接 382
第9章 压力弹簧管及其组件 384
9.1 压力弹簧管的结构形式及其应用 384
9.1.1 压力弹簧管在航空上的应用 384
9.1.2 压力弹簧管的分类 385
9.1.2.1 按外形结构分类 385
9.1.2.2 按截面形状分类 386
9.2 压力弹簧管常用材料 386
9.3 压力弹簧管工作原理及基本特性 387
9.3.1 压力弹簧管的工作原理 387
9.3.2 压力弹簧管的基本特性 387
9.3.2.1 压力-位移特性 387
9.3.2.2 比例极限与安全系数 388
9.3.2.3 灵敏度 388
9.3.2.4 弹簧管几何尺寸对特性的影响 388
9.4.1.1 C型薄壁弹簧管的计算 390
9.4 压力弹簧管的设计计算 390
9.4.1 C形弹簧管的设计计算 390
9.4.1.2 C型厚壁弹簧管的计算 391
9.4.2 螺旋形弹簧管的计算 392
9.5 压力弹簧管及其组件制造工艺 393
9.5.1 典型工艺流程 393
9.5.2 毛坯管制造 394
9.5.2.1 对毛坯管的技术要求 394
9.5.2.2 机械加工法 395
9.5.2.3 拉伸法 395
9.5.2.4 毛坯管的拉制 396
9.5.2.5 毛坯管的检测 396
9.5.3 弹簧管成形 399
9.5.3.1 压扁截面成形 399
9.5.3.2 热成形C形弹簧管 399
9.5.3.3 三轴弯管机成形 400
9.5.3.4 半自动弯管机成形 401
9.5.3.5 绕制螺旋形弹簧管 404
9.5.3.6 绕制双层螺旋形弹簧管 404
9.5.4 组件的装配 405
9.5.4.1 螺纹连接 405
9.5.4.2 组合焊接 406
9.5.4.3 熔焊 407
9.5.4.4 激光焊 407
9.5.4.5 自由端封焊 408
9.5.5 防锈处理 409
9.5.6 氧气组件的除油 410
9.5.7 组件的稳定处理 410
9.5.7.1 自然时效 410
9.5.7.2 温度稳定 410
9.5.8.2 位移和迟滞的检测 411
9.5.8.1 气密性检查 411
9.5.8 特性检测 411
9.5.7.3 机械稳定处理 411
9.5.8.3 刚度的检测 412
9.5.8.4 比例极限和安全系数的检测 412
第10章 弹性谐振元件 413
10.1 弹性谐振元件的特点、结构和应用 413
10.2 材料选择、热处理和稳定处理 414
10.3 振动筒 415
10.3.1 结构分类及特征 415
10.3.2 频率特性方程 416
10.3.2.1 固有振动频率 416
10.3.2.2 压力频率特性 416
10.3.3 振型分析 416
10.3.3.1 振动筒的振型 416
10.3.3.2 振型的选择 417
10.3.4 旋压拉伸制造工艺 418
10.3.4.1 典型工艺流程 419
10.3.4.2 对毛坯管的要求 419
10.3.4.3 工艺参数选择 420
10.3.5 车、磨制造工艺 420
10.3.5.1 工艺、结构特点 420
10.3.5.2 工艺流程 421
10.3.5.3 工装夹具 421
10.3.5.4 设备及要求 421
10.3.5.5 制造缺陷及防止措施 422
10.3.6 振动筒的检测 422
10.3.6.1 几何参数检测 422
10.3.6.2 性能测试 422
10.3.7 绝对压力振动筒组件 424
10.3.7.1 组件结构 424
10.3.7.2 焊接组合工艺 424
10.4.1 结构分类及特征 426
10.3.7.3 真空度及焊缝检测 426
10.4 振动膜片 426
10.4.2 频率特性方程 427
10.4.3 整体结构振动膜片 428
10.4.3.1 结构形式及特点 428
10.4.3.2 制造工艺 428
10.4.4 焊接结构振动膜片 430
10.4.4.1 结构形式及特点 430
10.4.4.2 制造工艺 430
10.4.5 振动膜片的检测 432
10.4.5.1 几何参数检测 432
10.4.5.2 性能参数测量 432
10.4.6 绝对压力振动膜片组件 433
10.4.6.1 组件结构 433
10.4.6.2 焊接组合工艺 433
10.5.1 振动梁 435
10.5.1.1 频率特性方程 435
10.5 其他结构形式的金属弹性谐振元件 435
10.4.6.3 组件检测 435
10.5.1.2 制造工艺 436
10.5.2 双谐振音叉 436
10.5.3 振动弦 437
10.6 非金属弹性谐振元件 437
10.6.1 石英弹性谐振元件 438
10.6.1.1 振动模式及结构 438
10.6.1.2 原材料的选择 438
10.6.1.3 石英振梁的制造工艺及专用设备 438
10.6.2 硅弹性谐振元件 440
10.6.2.1 元件的特征 441
10.6.2.2 微机械加工技术 441
10.6.2.3 制造实例 442
参考文献 444