图书介绍
机械可靠性与故障分析pdf电子书版本下载
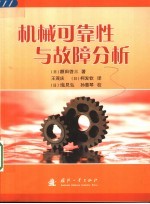
- (日)额田启三著;王茂庆,柯发庆译 著
- 出版社: 北京:国防工业出版社
- ISBN:7118042366
- 出版时间:2006
- 标注页数:298页
- 文件大小:17MB
- 文件页数:318页
- 主题词:结构可靠性;机械-故障诊断
PDF下载
下载说明
机械可靠性与故障分析PDF格式电子书版下载
下载的文件为RAR压缩包。需要使用解压软件进行解压得到PDF格式图书。建议使用BT下载工具Free Download Manager进行下载,简称FDM(免费,没有广告,支持多平台)。本站资源全部打包为BT种子。所以需要使用专业的BT下载软件进行下载。如 BitComet qBittorrent uTorrent等BT下载工具。迅雷目前由于本站不是热门资源。不推荐使用!后期资源热门了。安装了迅雷也可以迅雷进行下载!
(文件页数 要大于 标注页数,上中下等多册电子书除外)
注意:本站所有压缩包均有解压码: 点击下载压缩包解压工具
图书目录
第1章 可靠性活动的目的 1
1.1 可靠性就是在用户中所产生的价值 1
目录 1
第1部分 可靠性技术的本质 1
1.2 可靠性为什么成为问题 3
1.4 排除技术人员的主观臆断 4
1.3 要考虑故障后的状态 4
2.1.2 可靠性工作和定量化的关系 6
2.1.1 常用的可靠性定量化指标 6
第2章 数理统计在可靠性实际工作中的应用 6
2.1 可靠性定量化的具体目的 6
2.1.4 定量化目的和要求的特性 7
2.1.3 定量化的目的和本质 7
2.2.2 函数的利用 8
2.2.1 对统计理论的误解 8
2.2 关于函数的见解 8
2.2.3 时间t以外的变量 9
2.2.7 重视故障模式的信息而不仅是故障概率数值 11
2.2.6 故障概率的表达 11
2.2.4 单一模式、单一机制及单一函数的应用原则 11
2.2.5 整机产品的故障概率特性 11
2.3.4 从分布形式推定故障原因的可能性 12
2.3.3 实际工作中指数分布和威布尔分布并用 12
2.3 指数分布和威布尔分布 12
2.3.1 广泛使用的指数函数(指数分布) 12
2.3.2 在最简化的场合下使用指数分布 12
2.4.1 为什么使用威布尔分布 13
2.4 实际工作所必要的函数处理 13
2.3.5 受阿仑纽斯公式支配的电子零部件的故障 13
2.4.2 威布尔分布应当用于不可修产品 15
2.4.3 威布尔概率纸图形的主要性质 16
2.5.1 描点 24
2.5 威布尔概率纸的描点和图形解读 24
2.5.3 复合模式的分析和分离 26
2.5.2 形状参数m的作图解法 26
2.6.2 机械产品的寿命 27
2.6.1 小样本量的故障数n 27
2.5.4 改进可靠性的效果 27
2.6 故障概率的含义、误差和审定 27
2.6.5 故障率的置信区间值 28
2.6.4 故障率的计算 28
2.6.3 对机械产品分析需要高概率值的累计故障概率F数据 28
2.6.6 关于故障率递增型的考虑 29
2.6.7 可靠性管理中常用的故障率λ的含义 30
2.7.2 获得现场信息的问题 32
2.7.1 获得现场信息的必要性 32
2.7 现场故障信息的获得和处理 32
2.7.3 现场信息的获得、传达及信息质量的问题 33
2.7.5 应收集的原始资料的斟酌和整理 34
2.7.4 现场数据收集的原理 34
2.7.6 分析处理原始信息的方针 37
2.7.7 批量的集合 38
2.8.1 数据混合的形态 39
2.8 将故障模式分离后描点 39
2.7.8 关于现场数据的小结 39
2.8.3 各种处理方法 40
2.8.2 数据抽出的方法 40
2.9 机械的可靠性试验计划 44
2.10 现场数据和可靠性试验结果的比较 45
3.1.1 构成故障的三要素 49
3.1 故障的本质 49
第3章 机械故障的本质 49
3.1.2 三要素的关系 50
3.2.1 故障和损坏的区别 51
3.2 故障和损坏 51
3.3.1 故障连锁的性质 53
3.3 故障的连锁 53
3.2.2 静态故障和动态故障 53
3.3.3 切断连锁的进展 55
3.3.2 故障连锁的形式 55
3.4 挥发性故障和非挥发性故障 57
3.5 耗损性故障 58
3.6.2 与缓冲功能的关系 59
3.6.1 基本性质 59
3.6 冲击破坏性故障 59
3.7.1 疲劳破坏的现象 60
3.7 疲劳破坏 60
3.6.3 冲击破坏的表现形式 60
3.7.4 疲劳故障的处理 61
3.7.3 周知的事实 61
3.7.2 突发性 61
3.8.1 事例 63
3.8 以腐蚀为诱因的破坏 63
3.9.2 支配磨损的因素 64
3.9.1 磨损的性质 64
3.8.2 腐蚀的防止 64
3.8.3 不锈钢未必不生锈 64
3.9 因磨损造成的故障 64
3.11 因振动引起的故障 65
3.10.4 难以屈服的材料 65
3.10 因屈服造成的故障 65
3.10.1 材料的基本性质 65
3.10.2 弹簧中的屈服 65
3.10.3 压力计感压管的屈服 65
3.12.3 功能降低故障的故障机制 66
3.12.2 故障率受故障状态定义的影响 66
3.12 功能降低故障 66
3.12.1 定义 66
3.13 轻微故障 68
3.12.6 功能降低故障在可靠性技术中的位置 68
3.12.4 功能降低故障和失效安全设计 68
3.12.5 功能降低故障的查出 68
4.1.1 基本定义 69
4.1 关于质量的两种学说 69
第4章 对质量管理和可靠性管理的关系的理解 69
4.2.1 实施对策的方法、部署不同 70
4.2 根据狭义定义区分缺陷和故障 70
4.1.2 根据异常发生的时期进行区别 70
4.2.2 互相交叉并存的质量和可靠性管理 71
4.2.3 为什么需要考虑到这种混合的区别 72
4.2.4 早期发生的故障中有难以区别的中间区域 74
4.3.1 质量可测定、可通过直接管理得到保证 75
4.3 缺陷和故障的性质本质不同 75
4.2.5 站在用户的立场考虑早期故障的影响 75
4.4.1 质量保证试验 76
4.4 可靠性试验和质量保证试验的差异 76
4.3.2 可靠性不能直接测定,而靠间接管理来保证 76
4.3.3 对可靠性工作错误地使用了质量管理的手法 76
4.4.4 磨合运行 77
4.4.3 老化、筛选 77
4.4.2 可靠性试验 77
4.4.7 机械产品可靠性试验的问题所在 78
4.4.6 质量保证试验和可靠性试验的比较 78
4.4.5 可靠性监控试验 78
4.5.1 生产过程管理的重点是质量管理 79
4.5 实际工作中的质量管理和可靠性管理的关系 79
4.5.2 关于“规范”的说明 81
5.1.1 以模块化为前提的分析 83
5.1 可靠性模块的理解 83
第5章 与可靠性分析有关的机械的构成和功能 83
5.2.1 对零部件、单元的分解或组合 84
5.2 从分层结构处理问题的角度考虑 84
5.1.2 在实际工作中的 84
分析 84
5.3.2 将联结看成一个零部件 85
5.3.1 单件 85
5.2.2 电子产品与机械产品的分解之差 85
5.3 基础零部件 85
5.4.2 对机械产品进行定量分析 86
5.4.1 电子产品和机械产品可靠性单元处理的不同之处 86
5.4 将产品分解为可独立分析的可靠性单元组合 86
5.5.1 可修产品和不可修产品的定义 87
5.5 可修产品和不可修产品 87
5.4.3 故障分析的实施 87
5.5.3 零部件、单元的寿命特性 88
5.5.2 修理对象 88
5.5.6 威布尔分布只限于不可修产品使用 89
5.5.5 更换方式和故障概率 89
5.5.4 长期观测的可修产品的故障概率 89
5.5.8 MTBF、MTTF 90
5.5.7 采用累积故障概率的对数H、时间对数的坐标纸对可修产品进行分析 90
5.6.3 待机系统可靠性的数学模型 91
5.6.2 待机系统的可靠性 91
5.6 待机系统 91
5.6.1 待机系统的定义 91
5.6.4 待机系统故障的性质 92
5.6.5 组装到非待机系统中的待机系统 93
6.1 维修的概念 95
第6章 维修 95
6.2.2 必须进行完善的维修的理由 96
6.2.1 现实意义 96
6.2 维修的必要性 96
6.2.4 维修要求的变化 97
6.2.3 维修的条件不是固定的、而是变化的 97
6.3.2 从作业的形态看维修的形态 98
6.3.1 参与人员 98
6.3 维修的种类 98
6.3.4 维修作业的内容 99
6.3.3 按产品种类区分的维修的性质 99
6.4.1 预防维修和事后维修 101
6.4 维修内容和可靠性的关系 101
6.4.2 考虑到维修的产品的设计 102
6.5.2 维护、修理的实例 103
6.5.1 修理能否在现场进行 103
6.5 修理和更换的分离 103
6.5.3 由用户进行维修 104
6.6 维修性故障(由维修引起的故障) 105
6.8.1 制造厂家应关注维修 106
6.8 维修和制造厂家的关系 106
6.7 通过改善维修来提高可靠性 106
6.9 维修记录 107
6.8.2 关于维修消耗品的考虑 107
6.10.1 作为可靠性评价目标的可用率 108
6.10 停机时间的管理 108
6.10.2 DT的要素 109
6.11 维修的特殊性质 110
6.10.3 DT管理和改善 110
6.12 用户修理与假冒零部件 111
7.1.2 环境对电子产品和机械产品的影响的比较 112
7.1.1 产品的开发方式和可靠性工作的考虑 112
第7章 环境和机械故障 112
7.1 环境和机械的关系 112
7.1.4 环境的社会要素 113
7.1.3 环境的分类 113
7.2.3 低温 116
7.2.2 盐害 116
7.2 在中国应注意的周围环境要素 116
7.2.1 由黄沙带来的细微尘埃 116
7.2.4 超载 117
7.3.1 对应环境状态的产品可靠性标准 118
7.3 可靠性工作对环境问题的处理 118
7.4 机械产品对周围环境的影响 119
7.3.4 安全环境 119
7.3.2 对策的多样化 119
7.3.3 环境的多样化 119
7.5 环境问题和安全问题的关系 120
8.1.2 单个产品的安全性 121
8.1.1 系统安全性和单个产品的安全性 121
第8章 产品安全性 121
8.1 产品安全性与质量、可靠性工作的关系 121
8.1.3 安全性管理的特点 122
8.2.2 人在安全性方面的弱点 124
8.2.1 人是涉及的对象 124
8.2 安全性问题的基础 124
8.3 与人有关的安全性(模式) 127
8.5 产品废弃后的安全性 129
8.4.2 相同使用者使用的不同的类似产品的安全水平 129
8.4 公平地实现安全性 129
8.4.1 相同产品的不同制造厂家之间的安全性差别 129
8.6.1 订货方应采取的手段 130
8.6 对系统安全的观察 130
8.6.2 制造厂家一方应采取的手段 131
8.7 安全性只靠产品是无法维持的 132
8.9 发生安全问题时的处理 133
8.8 具体的安全性管理工作 133
1.2.1 信息是可靠性工作的基础 136
1.2 从外部信息来了解现在产品的可靠性程度 136
第2部分 理解工厂的可靠性工作 136
第1章 理解可靠性工作的内容 136
1.1 可靠性工作的出发点 136
1.1.1 可靠性工作的原则 136
1.1.2 适合工厂体制的工作方法 136
1.3 工厂内可靠性工作实施规范的设计 137
1.2.2 从外部收集信息的方法 137
1.4.1 设计的三要素 138
1.4 设计 138
1.5.1 故障分析在可靠性工作中所占的地位 140
1.5 故障分析 140
1.5.3 回收故障品实物的问题 141
1.5.2 首先回收故障品实物 141
1.5.5 不同国情在回收故障品实物方面的差异 142
1.5.4 无法回收故障品实物 142
1.5.6 实施故障分析 143
1.5.7 故障模式影响分析,故障树分析 144
1.5.8 设计评审 147
1.5.9 公共的机械产品故障分析机构 148
1.6.1 定义与目的 149
1.6 质量管理数据的可追溯性 149
1.6.2 区分设计与质量管理的问题 150
1.8.1 应予确认的条件 151
1.8 确认设计条件 151
1.7 故障发生与故障原因探求的逻辑推理顺序 151
1.8.2 设计原因的确认方法 152
1.9 故障原因确定后的处理 153
1.8.3 确认实际载荷 153
1.10 持久性的工作 155
1.10.3 不断完善可靠性工作 156
1.10.2 保持稳定的可靠性 156
1.10.1 通过长期计划解决问题 156
2.1.2 分析必要的工厂职能的程序概要 157
2.1.1 一般条件的再确认 157
第2章 可靠性工作的目标、产品性质与企业体制的匹配 157
2.1 分析自己工厂具备的必要条件 157
(条件1) 158
2.2.1 产品的设计环境 158
2.2 决定可靠性改善难易度的两要素 158
2.2.5 确认适合的工厂体制水平 159
2.2.4 解决各难易度所需的工厂体制 159
2.2.2 产品的制造、使用业绩(使用履历环境) 159
2.2.3 难易度的判定 159
2.3.3 中小机械企业在产品设计的基本条件准备方面存在精疏之差 160
2.3.2 解决容易的故障与困难的故障 160
2.3 条件匹配与否决定可靠性工作的成败 160
2.3.1 工作要取得成功,需要适合的体制水平 160
2.5 可靠性工作的专门机构与职责分工 161
2.4.2 实行计划与改善体制 161
2.4 可靠性工作的方针 161
2.4.1 对解决故障问题能力的判断 161
2.6.3 以朋友相待,说服进行改进 162
2.6.2 难以说服进行改进的理由 162
2.6 与外部协作企业的交涉能力 162
2.6.1 协作企业的实体 162
2.7 可靠性工作中设计部门的问题 163
2.6.4 不能说服对方时的处理 163
2.7.1 研究所担任开发设计 164
2.7.4 企业规模的问题 165
2.7.3 关键词是竞争力 165
2.7.2 通过技术合作、合营,转让设计 165
3.1.1 放眼全局,谋求合理的推进管理 167
3.1 有效地推进实现可靠性管理 167
第3章 可靠性工作是信息处理工作 167
3.1.4 可靠性的逻辑推理过程 168
3.1.3 把可靠性工作看成一个系统工程 168
3.1.2 可靠性工作项目的定义 168
3.3 作为可靠性工作项目成果的信息的性质 169
3.2 信息的质量问题 169
3.1.5 从信息组织的角度来看可靠性计划 169
3.3.1 可靠性工作项目所输出的信息的多面性和不确定性 170
3.3.2 多面性、不确定性的斟酌 171
3.3.3 实际工作中对信息不确定性的处理 172
3.3.4 各种信息的性质 173
3.3.5 信息的互补性 175
3.4.2 不健全的信息系统 176
3.4.1 与人体对应的可靠性信息系统 176
3.4 健全的信息系统 176
4.1.2 美国MIL标准,MIL手册,宇宙航空局标准 178
4.1.1 来历不同的标准造成应用的混乱 178
第4章 认识MIL-STD、ISO—9000等国际标准 178
4.1 国际标准概要 178
4.1.3 ISO—9000系列 180
4.2.1 标准在中国的应用 181
4.2 对标准的认识 181
4 1.4 IEC-300 181
4.1.5 QS—9000 181
4.2.3 作为标准形式的可靠性数值 182
4.2.2 中国的中小机械企业如何与国际标准协调 182
4.2.5 关注实际的可靠性 183
4.2.4 企业对标准的认识 183
1.2.1 进行新设计时 186
1.2 以设计标准化为背景的防泄漏设计 186
第3部分 机械故障分析的基本知识 186
第1章 泄漏及防泄漏 186
1.1 泄漏问题 186
1.1.1 忠实于理论 186
1.1.2 依据泄漏的容许量,管理的严格程度不同 186
1.3.1 流体种类 187
1.3 泄漏问题的对象 187
1.2.2 对设计条件不明确的现行产品的改进 187
1.2.3 基本结构不适合 187
1.3.5 容许的泄漏量 188
1.3.4 引起泄漏变化的要素 188
1.3.2 流体的特性 188
1.3.3 影响泄漏问题的使用条件 188
1.3.7 泄漏的影响 189
1.3.6 泄漏量的数值化 189
1.4.2 接触材料 190
1.4.1 静态密封和动态密封 190
1.3.8 泄漏的检出 190
1.4 防泄漏的基本结构 190
1.5 防泄漏理论的简单说明 191
1.4.3 接触压力的产生机构 191
1.5.2 静态型密封的诊断 193
1.5.1 静态型密封 193
1.5.4 填料密封 196
1.5.3 锥管螺纹连接 196
1.5.5 O形环 198
1.6 泄漏问题的特殊性质 199
1.5.6 轴封 199
2.1.1 问题所在 201
2.1 螺栓联结的可靠性问题 201
第2章 螺栓联结 201
2.1.2 螺栓松动的现象 202
2.2.1 为使螺栓不产生松动,对螺纹面形状的要求 203
2.2 螺栓的松动 203
2.2.2 针对螺纹形状原因的防松对策 204
2.2.3 螺栓长度、退刀槽等结构引起的松动 205
2.2.4 振动引起的松动 207
2.2.5 适当的拧紧 208
2.2.6 防松动措施 209
2.3 螺栓松动的诊断 210
2.4.2 飞机用的螺栓 211
2.4.1 起重用吊环螺栓 211
2.4 对可靠性要求高的螺栓 211
2.6.2 现实地加以对应 212
2.6.1 相互矛盾的条件 212
2.5 螺栓直径对松动的影响 212
2.6 采购螺栓时的矛盾 212
3.1.2 弹簧是故障的根源 214
3.1.1 弹簧作为独立的可靠性单元 214
第3章 弹簧 214
3.1 弹簧的质量、可靠性问题 214
3.1.4 弹簧制造厂家管理困难的原因 215
3.1.3 标准化的困难 215
3.2.1 屈服 216
3.2 弹簧的故障模式 216
3.1.5 解决的途径 216
3.2.3 折断 217
3.2.2 弹簧颤振 217
3.2.4 电镀处理而致的折断 218
3.3 诊断和对策 219
3.2.5 滚轧板簧的折断 219
3.5 弹簧可靠性的评价 220
3.4.4 铍青铜弹簧 220
3.4 特殊的弹簧材料 220
3.4.1 析出硬化型不锈钢弹簧 220
3.4.2 不锈钢冷加工弹簧 220
3.4.3 磷青铜弹簧 220
3.8 产品制造厂家的弹簧质量管理 221
3.7 弹簧的标准化 221
3.6 弹簧安装部位的结构 221
3.9 备件的保管 222
4.2.1 故障的性质 223
4.2 轴承可靠性问题的特殊性 223
第4章 轴承及其润滑 223
4.1 掌握轴承及其润滑系统故障的方法 223
4.3 使用环境的变迁 224
4.2.2 注意使用环境的变化趋势 224
4.4 润滑方式 226
4.5 适当的润滑油 227
4.7 润滑油脂的性质 228
4.6 旋转摩擦扭矩 228
4.8.3 设计中的降级使用 229
4.8.2 存在质量的差距 229
4.8 滚珠轴承 229
4.8.1 完全标准化的商品 229
4.8.5 滚珠轴承的偏心 230
4.8.4 滚珠轴承使用上的问题 230
4.8.8 滚珠轴承的故障对策 231
4.8.7 滚珠轴承故障的诊断 231
4.8.6 滚珠轴承的推力 231
1.2.1 市场调查 234
1.2 公司整体的可靠性计划 234
第4部分 初期可靠性工作的事例 234
第1章 Komatsu公司(旧小松制作所)的事例 234
1.1 提出可靠性计划的背景和动机 234
1.1.1 当时处境 234
1.1.2 自力建立与外国技术对抗的技术 234
1.3 本事例的经验教训 235
1.2.4 建立全公司的可靠性系统 235
1.2.2 设定分析结果的目标 235
1.2.3 结果 235
1.4.2 企业体制 236
1.4.1 重视现场信息情报 236
1.4 笔者的意见 236
2.2 改进前的状况 237
2.1 产品对象的性质 237
第2章 冷冻装置用压缩机的改良 237
2.3.2 分析过程 238
2.3.1 根据手头不完全的资料进行数据分析 238
2.2.1 现场信息情报的收集情况 238
2.2.2 故障分析的实情与实施有效的对策 238
2.2.3 原因追究和对策的状况 238
2.3 着手分析 238
2.5.1 挥发性故障的分析经验不足 240
2.5 本事例的经验教训 240
2.4 对策 240
2.6 改进后的工厂可靠性系统 241
1.1.1 在最初阶段不期待完善 242
1.1 制订阶段性发展计划 242
第5部分 工厂可靠性工作的实际经验 242
第1章 可靠性工作的准备 242
1.2 自我评价本公司可靠性工作实施能力 243
1.1.3 计划 243
1.1.2 首先评价现状和自身水平 243
1.3 工作着手前的准备计划 244
1.4.2 故障概率的计算 245
1.4.1 最初的故障信息的质量 245
1.4 故障的重现及故障状态的把握 245
1.4.5 事故信息的分析 246
1.4.4 可修产品的累积故障概率对数曲线的描点 246
1.4.3 利用威布尔分析反推零部件的故障模式 246
1.5.3 根据故障模式的形态、功能及发生时期进行分类 247
1.5.2 进行故障模式分类 247
1.5 调查结果的整理和分类 247
1.5.1 故障品(相同类型品)映像的再现 247
1.5.5 进行这种复杂繁琐的分类和说明 250
1.5.4 故障的关系图 250
1.6.2 选择对策的限制取决于工厂的能力 251
1.6.1 根据故障模式进行粗略区分 251
1.6 根据对策的可能性决定实施程序 251
1.6.4 综合表的实例 254
1.6.3 确认分类的合适程度 254
1.6.5 综合计划的重要性 256
1.7 准备工作的结束 256
第2章 故障分析的实行 257
2.1 分析故障时的障碍 257
2.1.1 困难和捷径 257
2.1.2 损伤部位与真正原因所在的不一致 257
2.1.3 尽可能配备高水平的故障分析技术 258
2.1.4 中立的支援机构 258
2.2 故障分析的程序 258
2.2.1 建立故障分析的逻辑 258
2.2.2 模拟或确认 259
2.3 故障分析的实际业务 259
2.3.1 利用仪器对微细异物进行分析 259
2.3.2 表面、断裂面、外观的观察 260
2.3.3 使用力流程图进行分析 262
2.4 小结 266
2.4.1 全面分析故障原因和模式 266
2.3.4 功能下降 266
2.4.2 硬件及软件的原因 267
2.4.3 引导明确对策的判定 267
3.1.2 可靠性改进过程中的副作用 268
3.1.1 定义 268
3.1.3 疑似副作用 268
3.1 副作用的性质和推敲分析的必要性 268
第3章 副作用的斟酌和管理 268
3.2 副作用的机制 269
3.2.1 材料变更的副作用 269
3.2.2 改变断面尺寸的副作用 270
3.2.3 改变结构方式的副作用 270
3.3.1 副作用检查的特殊性 271
3.3 副作用的确认和监视 271
3.3.2 监视 271
3.2.5 改变管理方式的副作用 271
3.2.4 作为副作用的挥发性故障 271
3.4 与价值分析副作用管理的关系 272
选择对策形式 273
4.1.1 由经营的顶层领导来 273
4.1.2 实施的形式与应予处理的故障性质的关系 273
4.1 对策的选择和实施的原则 273
第4章 对策的选择和实施 273
4.1.3 实施形式的选择 274
4.1.4 实施的方式 274
4.2 实施内容 275
4.2.1 实施内容的注意点 275
4.2.2 推敲对策的有效性 276
4.2.3 实施对策的顺序 277
4.3 综合实施 277
4.5.1 持续性 278
4.5 对策的持续性 278
4.5.2 在实际工作中深化持续性 278
4.4 害怕牺牲血本的消极对策 278
4.5.4 持续性实施的深度 279
4.5.5 通过反复积累,促进提高持续性 279
4.5.3 实施持续性的效果 279
附录1 关于特殊的概念、用语 281
1.1 需要说明的概念 281
附录 281
1.2 本书专门使用的用语说明 283
1.2.1 估计的可靠性 283
1.2.2 挥发性故障、非挥发性故障 284
1.2.3 疑似初始故障 284
1.2.4 疑似副作用 285
1.2.5 趋近分析 285
1.3.1 共因模式故障 286
1.3.2 缺陷 286
1.3 特殊的外来语 286
1.3.3 Stress与Mechanical Stress 287
1.4 实际应用威布尔分布时的注意事项 288
1.3.6 故障率与故障概率的区别 288
1.4.1 考虑故障数n的误差影响 288
1.3.5 累积故障率与累积故障概率的区别 288
1.3.4 磨损与耗损性故障 288
1.4.2 考虑参数m的误差的场合 289
2.1 关于本书的用语 290
2.2 用语的索引 290
附录2 用语集 290
2.3 外来语用语集 291
附录3 推荐书籍 297
附录4 引用资料的文献目录 298