图书介绍
中国材料工程大典 第23卷 材料焊接工程 下pdf电子书版本下载
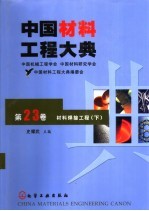
- 史耀武主编;中国机械工程学会,中国材料研究学会,中国材料工程大典编委会编 著
- 出版社: 北京:化学工业出版社
- ISBN:7502573259
- 出版时间:2006
- 标注页数:1148页
- 文件大小:149MB
- 文件页数:1162页
- 主题词:材料科学;金属材料-焊接
PDF下载
下载说明
中国材料工程大典 第23卷 材料焊接工程 下PDF格式电子书版下载
下载的文件为RAR压缩包。需要使用解压软件进行解压得到PDF格式图书。建议使用BT下载工具Free Download Manager进行下载,简称FDM(免费,没有广告,支持多平台)。本站资源全部打包为BT种子。所以需要使用专业的BT下载软件进行下载。如 BitComet qBittorrent uTorrent等BT下载工具。迅雷目前由于本站不是热门资源。不推荐使用!后期资源热门了。安装了迅雷也可以迅雷进行下载!
(文件页数 要大于 标注页数,上中下等多册电子书除外)
注意:本站所有压缩包均有解压码: 点击下载压缩包解压工具
图书目录
第4篇 材料焊接 1
1.1 常见焊接用碳钢及碳钢铸件的成分和性能 3
1 常见焊接用碳钢的认识 3
第1章 碳钢的焊接 3
2.1 焊条 10
2 碳钢焊接用材料 10
1.2 碳钢焊接适用的工艺方法及所用焊接材料的进展 10
2.2 埋弧焊焊丝和焊剂 14
2.3 CO2气保护焊用焊丝 16
2.4 其他辅料 19
4.1 低碳钢 20
4 碳钢的焊接工艺 20
3 碳钢的焊接性 20
4.2 中碳钢 26
5.1 焊条 27
5 碳钢焊接材料牌号对照 27
4.3 高碳钢 27
5.3 焊剂 29
5.2 焊丝 29
1 铸铁 30
第2章 铸铁的焊接 30
2.1 焊接接头分区、成分组织及性能 31
2 铸铁的焊接性 31
2.2 焊接裂纹 33
3.2 非铸铁型焊缝的电弧冷焊 34
3.1 铸铁型焊缝焊接工艺、方法 34
3 铸铁焊接工艺、方法及材料 34
3.3 铸铁焊接材料 35
4.1 灰铸铁的电弧焊 40
4 灰铸铁的焊接 40
4.2 灰铸铁的气焊 45
4.4 灰铸铁的火焰粉末喷焊 47
4.3 灰铸铁的火焰钎焊 47
5.1 球墨铸铁焊接性 48
5 球墨铸铁的焊接 48
5.2 球墨铸铁的电弧焊 49
6 蠕墨铸铁的焊接 53
8 白口铸铁的焊补 54
7 可锻铸铁的焊接 54
2.1 管线钢的发展 55
2 管线钢的焊接 55
第3章 低合金高强度钢的焊接 55
1 低合金高强度钢的发展 55
2.2 管线钢的焊接性 56
2.3 管线钢的焊接工艺 58
3.1 超细晶粒钢焊接热影响区的晶粒长大 59
3 400 MPa级超细晶粒钢的焊接 59
3.2 400 MPa级超细晶粒钢板的电弧焊接 63
3.3 400 MPa级超细晶粒钢板的激光焊接 72
3.4 400 MPa级超细晶粒碳素钢筋的焊接 79
4.2 800 MPa级新一代钢焊接热影响区组织变化规律 87
4.1 弛豫热处理(RPC)超细组织钢的成分及组织特征 87
4 800 MPa级超细晶粒钢的焊接性 87
4.3 鞍钢20 mm厚RPC钢板焊接接头组织与性能 93
4.4 RPC超细组织低合金钢的激光焊接研究 97
5 船舶用低合金高强钢的焊接 104
1.2 耐热钢的应用范围 105
1.1 耐热钢的种类 105
第4章 耐热钢的焊接 105
1 概述 105
2.1 低合金耐热钢的化学成分、力学性能和热处理状态 106
2 低合金耐热钢的焊接 106
1.3 对耐热钢焊接接头性能的基本要求 106
2.2 低合金耐热钢的焊接特点 108
2.3 低合金耐热钢的焊接工艺 109
2.4 低合金耐热钢接头性能的控制 112
2.5 低合金耐热钢焊接实例 114
3.1 中合金耐热钢的化学成分和力学性能 116
3 中合金耐热钢的焊接 116
3.2 中合金耐热钢的焊接特性 117
3.3 中合金耐热钢的焊接工艺 119
3.4 中合金耐热钢焊接接头的力学性能 121
3.5 中合金耐热钢焊接实例 123
4.1 高合金耐热钢的化学成分和力学性能 125
4 高合金耐热钢的焊接 125
4.2 高合金耐热钢的焊接特性 132
4.3 高合金耐热钢的焊接工艺 135
4.4 高合金耐热钢接头的性能 141
4.5 高合金耐热钢焊接实例 144
1.1 不锈钢的分类 146
1 不锈钢的分类及其特性 146
第5章 不锈钢的焊接 146
1.2 不锈钢的化学成分 147
1.3 不锈钢的力学性能 150
1.4 不锈钢的物理性能 152
1.5 不锈钢的耐蚀性能 153
1.6 不锈钢的耐热性能 155
2.1 焊接接头的耐蚀性 156
2 不锈钢的焊接性 156
1.7 不锈钢的组织 156
2.2 焊接接头的热裂纹 157
2.3 焊接接头的冷裂纹 158
3.1 不锈钢的焊接方法 159
3 不锈钢的焊接方法和焊接材料 159
2.4 焊接接头的脆化 159
3.2 不锈钢的焊接材料 160
4.2 奥氏体不锈钢焊接工艺特点 176
4.1 奥氏体不锈钢焊接时的主要问题 176
4 奥氏体不锈钢的焊接 176
5.1 马氏体不锈钢焊接时的主要问题 181
5 马氏体不锈钢的焊接 181
4.3 奥氏体不锈钢焊接实例 181
5.2 马氏体不锈钢焊接工艺特点 182
6.1 铁素体不锈钢焊接时的主要问题 184
6 铁素体不锈钢焊接工艺特点 184
5.3 马氏体不锈钢焊接实例 184
6.2 铁素体不锈钢焊接工艺特点 186
7.1 双相不锈钢的特点及焊接性分析 187
7 铁素体-奥氏体双相不锈钢的焊接 187
7.4 双相不锈钢焊接实例 188
7.3 Cr25型双相不锈钢焊接工艺要点 188
7.2 Cr18型双相不锈钢的焊接要点 188
8.2 时效半奥氏体不锈钢焊接要点 189
8.1 时效不锈钢的类型 189
8 时效不锈钢的焊接 189
8.3 时效马氏体不锈钢焊接要点 190
8.4 时效奥氏体不锈钢焊接要点 191
1.2 高温合金的强化方法及合金元素的作用 192
1.1 高温合金的发展及应用概况 192
第6章 高温合金的焊接 192
1 概述 192
1.4 高温合金的力学性能 193
1.3 高温合金的牌号和化学成分 193
2.1 高温合金焊接接头的裂纹敏感性 199
2 高温合金的焊接性 199
2.2 焊接接头组织的不均匀性 201
3.1 钨极惰性气体保护电弧焊 202
3 高温合金的惰性气体保护电弧焊 202
2.3 焊接接头的等强性 202
4.1 等离子弧焊 212
4 高温合金的高能束焊接 212
3.2 熔化极惰性气体保护电弧焊 212
4.2 电子束焊 213
4.3 激光焊 214
5.1 电阻点焊 215
5 高温合金的电阻焊 215
5.2 电阻缝焊 217
5.3 闪光焊 221
6.6 接头组织与力学性能 222
6.5 接头缺陷及防止 222
6 摩擦焊 222
6.1 焊接特点 222
6.2 接头设计 222
6.3 焊前准备 222
6.4 焊接工艺 222
7.1 钎焊 223
7 高温合金的钎焊和扩散焊 223
7.2 大间隙钎焊 230
7.4 过渡液相扩散焊 232
7.3 固相扩散焊 232
1.2 铝及铝合金的熔焊 234
1.1 铝及铝合金概述 234
第7章 铝、镁及其合金的焊接 234
1 铝及铝合金的焊接 234
1.3 铝及铝合金的钎焊 267
1.4 铝及铝合金的固相焊接 272
1.5 铝及铝合金的电阻焊 274
2.1 镁及镁合金概述 276
2 镁及镁合金的焊接 276
2.2 镁及镁合金的熔焊 278
2.4 镁及镁合金的钎焊 284
2.3 镁及镁合金的电阻焊 284
2.7 镁及镁合金焊接技术安全 285
2.6 镁及镁合金的螺柱焊 285
2.5 镁及镁合金的搅拌摩擦焊 285
2.4 β钛合金 286
2.3 α+β钛合金 286
第8章 钛及其合金的焊接 286
1 概述 286
2 钛合金的分类 286
2.1 工业纯钛 286
2.2 α和近α钛合金 286
3.2 焊接相变引起的性能变化 289
3.1 间隙元素沾污引起脆化 289
3 钛及其合金的焊接性 289
4.2 焊前清理 291
4.1 焊接材料 291
3.3 裂纹 291
3.4 气孔 291
3.5 相对焊接性 291
4 焊接材料和工艺 291
4.4 钨极气体保护电弧焊 292
4.3 焊接或钎焊中的保护 292
4.6 等离子弧焊 293
4.5 熔化极气体保护电弧焊 293
4.7 真空电子束焊 294
4.10 电阻焊 295
4.9 摩擦焊 295
4.8 激光焊 295
4.13 扩散焊和扩散钎焊 296
4.12 高频焊 296
4.11 闪光焊 296
4.14 钎焊 297
6.1 退火 298
6 焊后热处理 298
5 焊缝缺陷及补焊工艺 298
5.1 焊缝缺陷 298
5.2 补焊工艺 298
7.1 压力容器的焊接 299
7 钛及钛合金的焊接实例 299
6.2 淬火-时效处理 299
6.3 时效处理 299
6.4 热处理制度的选取 299
7.4 整流器叶片钎焊 300
7.3 30万吨合成氨设备用工业纯钛焊接 300
7.2 管材对接 300
2.2 熔焊用材料 301
2.1 熔焊方法的选择 301
第9章 铜及其合金的焊接 301
1 铜及铜合金的焊接性 301
2 铜及铜合金的熔焊方法 301
2.3 熔焊工艺注意事项 303
3.2 铜及铜合金的软钎焊 304
3.1 铜及铜合金的硬钎焊 304
3 铜及铜合金的钎焊 304
1.2 钨的焊接方法 306
1.1 钨的焊接性 306
第10章 难熔合金的焊接 306
1 钨的焊接 306
2.2 钼的焊接方法 307
2.1 钼的焊接性 307
2 钼的焊接 307
3.4 钒、铌、钽及其合金的其他焊接方法简述 308
3.3 钒、铌、钽及其合金的电子束焊 308
3 钒、铌、钽及其合金的焊接 308
3.1 钒、铌、钽及其合金的焊接性 308
3.2 钒、铌、钽及其合金的钨极惰性气体保护焊 308
3.2 银及其合金的压力焊 310
3.1 银及其合金的熔化焊 310
第11章 稀贵有色金属的焊接 310
1 稀贵有色金属的特点 310
2 稀贵有色金属的焊接性 310
3 银及其合金的焊接 310
5.1 铂及其合金的熔焊 311
5 铂及其合金的焊接 311
3.3 银及其合金的钎焊 311
4 金及其合金的焊接 311
4.1 金及其合金的熔焊 311
4.2 金及其合金的压焊 311
4.3 金及其合金的钎焊 311
5.3 铂及其合金的钎焊 312
5.2 铂及其合金的压焊 312
1.1 异种金属焊接性特点 313
1 概述 313
第12章 异种金属焊接 313
1.2 异种金属焊接的冶金问题 314
2.1 异种钢焊接的应用及其分类 317
2 异种钢焊接 317
1.3 异种金属焊接工艺特点 317
2.2 同类型组织的异种钢焊接 318
2.3 不同类型组织的异种钢焊接 319
3.1 钢与铜及其合金的焊接 320
3 钢与有色金属焊接 320
3.3 钢与铝及其合金的焊接 321
3.2 钢与镍及其合金的焊接 321
3.5 钢与难熔金属及其合金的焊接 322
3.4 钢与钛及其合金的焊接 322
4.2 铜与其他有色金属的焊接 323
4.1 铝与其他有色金属的焊接 323
4 异种有色金属焊接 323
4.3 异种难熔金属的焊接 324
4.4 难熔金属与其他有色金属的焊接 325
1.2 工程结构陶瓷及陶瓷基复合材料的种类、性能及用途 326
1.1 概述 326
第13章 陶瓷的连接 326
1 工程结构陶瓷的种类、性能及应用 326
3.1 直接钎焊法 329
3 陶瓷连接的方法 329
2 陶瓷材料的焊接性问题 329
2.1 陶瓷材料焊接的一般问题 329
2.2 陶瓷基复合材料的连接问题 329
3.3 陶瓷的过渡液相连接 330
3.2 陶瓷的固相扩散连接 330
3.4 反应成形法连接陶瓷 332
4.2 无压固相反应连接 333
4.1 钎焊 333
4 陶瓷基复合材料的连接方法 333
4.4 其他连接方法 334
4.3 微波连接 334
1.3 Fe-Al系金属间化合物 335
1.2 Ti-Al系金属间化合物 335
第14章 金属间化合物的连接 335
1 金属间化合物的类型和特征 335
1.1 Ni-Al系金属间化合物 335
2.1 Ni3Al合金的焊接 336
2 Ni-Al系金属间化合物的连接 336
3.1 Ti3Al合金的连接 337
3 Ti-Al系金属间化合物的连接 337
2.2 NiAl合金的连接 337
3.2 TiAl合金的连接 338
4 Fe-Al系金属间化合物的连接 341
1.2 复合材料的特点 342
1.1 复合材料的分类 342
第15章 复合材料的连接方法 342
1 复合材料的分类及特点 342
2.2 金属基复合材料的连接 343
2.1 金属基复合材料的制备 343
1.3 复合材料的应用 343
2 金属基复合材料的连接 343
3.1 树脂基复合材料的连接特性 348
3 树脂基复合材料的连接 348
4 C/C复合材料的连接 349
3.2 树脂基复合材料的连接 349
5 陶瓷基复合材料的连接 350
1 概述 351
第16章 塑料的焊接 351
3.1 热气焊 352
3 塑料焊接方法 352
2 塑料焊接的特点 352
3.2 热工具焊 355
3.3 挤塑焊 358
3.4 超声波焊 359
3.5 摩擦焊 360
3.6 振动焊 362
3.7 高频电焊 363
3.8 激光焊 364
4.1 塑料焊接缺陷的检测 365
4 塑料焊接质量检验 365
3.9 焊接方法选择 365
4.2 塑料焊接接头力学性能的测试 366
5.1 塑料管道 369
5 塑料焊接的应用 369
5.3 塑料衬里 370
5.2 塑料容器 370
5.4 其他应用 371
1.3 堆焊中需注意的几个问题 372
1.2 堆焊在生产中的应用 372
第17章 金属材料的堆焊 372
1 概述 372
1.1 堆焊及其类型 372
2.1 堆焊工艺方法 373
2 金属材料堆焊 373
2.3 堆焊金属的使用性能 374
2.2 堆焊材料的形状 374
2.4 堆焊合金的分类 375
2.5 铁基堆焊合金 376
2.6 其他堆焊合金 392
2.7 堆焊合金的选择 402
参考文献 404
第5篇 焊接生产过程自动化 409
1 现代焊接自动化技术与装备的主要特点与我国发展概况 411
第1章 焊接生产自动化现状与发展 411
2.1 专用型自动弧焊设备 412
2 焊接自动化弧焊设备分类 412
3.1 天然气管道的自动化焊接技术 413
3 典型产品的自动化焊接技术 413
2.2 焊接机器人 413
3.2 储罐自动化焊接技术 415
3.3 船舶焊接自动化技术 420
3.4 机器人焊接集箱管接头技术 421
4.2 进一步发展焊接自动化的关键技术 422
4.1 发展方向 422
4 焊接生产自动化发展方向与关键技术 422
2.1 弧焊过程信息的传感 425
2 焊接过程的信息及传感方法 425
第2章 焊接过程信息检测技术 425
1 概论 425
2.2 电阻焊信息的传感 430
2.3 激光焊接的信息传感 432
2.5 摩擦焊的信息传感 433
2.4 电子束焊接的信息传感 433
3.2 工业化的焊接质量监测系统 434
3.1 焊接过程传感信息的判读 434
2.6 钎焊过程的信息传感 434
3 焊接过程信息的处理与分析 434
1 焊缝自动跟踪技术 435
第3章 焊接过程质量自动控制技术 435
1.1 传统附加式传感器及其在焊缝跟踪中的应用 436
1.2 视觉传感器及其在焊缝跟踪中的应用 437
1.3 电弧传感器及其在焊缝跟踪中的应用 443
1.4 智能机器人视觉系统 447
2.1 焊接熔滴控制技术研究进展 453
2 焊缝成形质量控制技术及其应用 453
2.2 焊接熔池几何形状检测与控制 456
2.3 焊接过程热输入控制 461
2.4 熔深检测与控制 463
2.5 焊接过程综合性能评价专家系统 466
3 焊接缺陷无损检测技术简介 469
3.1 焊接缺陷的超声波自动检测技术 470
3.2 焊接缺陷的X射线自动探伤技术 471
1 焊接自动化设备设计步骤与设计要点 473
第4章 焊接生产自动化设备设计要点与实例分析 473
2.1 球罐全位置焊接机器人设计 474
2 自动化焊接设备整机设计实例 474
2.2 汽车后桥壳自动焊设备设计 477
3.1 大直径钢薄壁长筒体自动焊装置设计 480
3 自动焊接设备的改造设计实例 480
2.3 全位置自动焊机构设计 480
3.2 抽油机驴头圆弧焊专机设计 481
3.3 罐体新型探臂焊车研制 482
4.1 弧焊设备通用一元化调节微机系统设计 483
4 自动焊设备微机控制系统设计实例 483
4.2 翅片管自动焊机微机控制系统设计 484
4.3 螺旋焊缝自动跟踪系统设计 487
1 焊接机器人产品分类及性能特点 490
第5章 焊接机器人及其工程应用 490
2.1 焊接机器人 491
2 焊接机器人系统配置 491
2.2 弧焊机器人系统焊接装置 492
2.4 焊接机器人系统的外围设备 494
2.3 点焊机器人系统焊接装置 494
3 焊接机器人路径规划 496
3.2 焊接机器人路径自主规划 497
3.1 焊接机器人无碰路径规划 497
4.1 柔性制造单元(FMC)和柔性制造系统(FMS)的定义及特性 499
4 焊接柔性制造单元(WFMC)和焊接柔性制造系统(WFMS) 499
4.3 焊接柔性制造系统(WFMS) 500
4.2 焊接柔性制造单元(WFMC) 500
5.1 焊接机器人工作站的一般设计原则 501
5 焊接机器人工程应用及其若干举例 501
5.3 焊接机器人工作站举例 502
5.2 焊接机器人生产线的设计原则 502
5.4 焊接机器人生产线举例 505
参考文献 508
第6篇 焊接结构设计 511
2.1 设计的基本要求 513
2.2 设计的基本原则 513
第1章 焊接结构设计的原则与方法 513
1 焊接结构的特点 513
2 焊接结构设计的基本要求和基本原则 513
3.1 许用应力设计法 514
3 焊接结构设计的基本方法 514
3.2 可靠性设计法 515
3.3 许用应力、安全系数和强度设计值 517
2.1 静载条件下的结构设计 521
2 结构形状的选定与设计 521
第2章 焊接结构设计基础 521
1 材料的选择 521
2.2 动载条件下的结构设计 526
3.1 焊接的可达性 529
3 考虑可达性的结构设计 529
3.2 焊缝质量检验的可达性 530
4.1 考虑受力合理的细部设计 531
4 焊接结构设计中的细部处理 531
4.2 避免或减小应力集中的结构细部处理 533
4.4 防止层状撕裂的结构措施 534
4.3 焊接结构中肋板设计的细节处理 534
1.2 弧焊接头的组成 537
1.1 弧焊接头的基本类型 537
第3章 焊接接头的设计 537
1 概述 537
2.2 搭接接头 539
2.1 对接接头 539
1.3 弧焊接头的基本特点 539
2 常用焊接接头的工作特性 539
2.5 电阻点焊接头 541
2.4 角接接头 541
2.3 T形接头和十字接头 541
3.2 坡口焊缝的设计 542
3.1 设计与选择焊接接头需考虑的因素 542
3 焊接接头构造的设计与选择 542
3.3 角焊缝的设计 544
3.5 标准的坡口形状和尺寸 545
3.4 部分熔透的焊缝设计 545
4.2 焊接接头的许用应力设计法 546
4.1 工作焊缝与联系焊缝 546
4 焊接接头的静载强度计算 546
4.3 焊接接头的极限状态设计法 551
5.1 概述 555
5 焊接接头的疲劳强度计算 555
5.2 焊接接头疲劳强度计算方法 556
6.1 焊缝符号 561
6 焊缝符号及其在图样上的标注 561
6.3 焊缝符号在图样上的标注方法 562
6.2 焊接方法在图样上的表示代号 562
6.4 各国焊缝基本符号对照 564
6.5 焊缝符号的尺寸、比例及简化表示法 566
6.6 焊缝无损检测符号及其在图样上的标注 573
1.3 焊接梁的设计与计算 576
1.2 梁的构造形式 576
第4章 基本焊接构件的设计与计算 576
1 焊接梁 576
1.1 梁的功能与作用力 576
1.4 焊接梁结构设计实例 586
2.1 柱的类型及其截面形式 593
2 焊接柱 593
2.2 焊接柱的设计与计算 594
2.3 焊接柱的构造要求 603
2.4 焊接柱结构设计实例 604
3.1 桁架的工作特点和结构特点 607
3 焊接桁架 607
3.2 焊接桁架的设计与计算 609
3.3 焊接钢桁架的节点设计与计算 611
3.4 焊接桁架结构设计实例 619
4.1 焊接刚架的一般特点 622
4 焊接刚架 622
4.2 门式焊接刚架结构的设计与计算 625
2.1 箱体的结构 631
2 减速器箱体焊接结构 631
第5章 机体的焊接结构 631
1 概述 631
2.2 箱体的致密性 633
2.3 实例 635
3.1 机床床身的焊接结构 637
3 机床基础件焊接结构 637
3.2 机床立柱的焊接结构 640
3.3 机床横梁的焊接结构 641
4.1 概述 642
4 锻压设备机身焊接结构 642
4.2 开式压力机的C形机身的焊接结构 643
4.3 框架式机身的焊接结构 644
4.4 组合式机身的焊接结构 645
5.2 低速船用柴油机机体的焊接结构 652
5.1 机体的工作特点及其设计要求 652
5 柴油机机体焊接结构 652
5.3 机车用柴油机体的焊接结构 653
6.2 立式电机机座的焊接结构 656
6.1 卧式电机机座的焊接结构 656
6 电机机座焊接结构 656
2.1 轮缘 658
2 轮式旋转体焊接结构 658
第6章 旋转体焊接结构 658
1 概述 658
2.2 轮辐 659
2.3 轮毂 660
2.5 轮式旋转体焊接结构设计实例 661
2.4 轮缘、轮辐和轮毂的连接 661
3.1 筒身 662
3 筒式旋转体焊接结构 662
4.1 汽轮机、燃气轮机转子的焊接结构 663
4 转子焊接结构 663
3.2 端盖 663
3.3 筒身、端盖和轴颈的连接 663
4.2 电机转子的焊接结构 664
5.1 整体式焊接转轮 665
5 水轮机转轮的焊接结构 665
6.2 风机叶轮的焊接结构 666
6.1 转轴的焊接结构 666
5.2 分瓣式焊接转轮 666
6 其他旋转体焊接结构 666
6.3 汽车轮心的焊接结构 667
1.2 压力容器的分类 668
1.1 压力容器的工作特点和基本要求 668
第7章 压力容器焊接结构 668
1 概述 668
1.4 压力容器中的应力分类及对其限制 669
1.3 压力容器设计的内容、准则和方法 669
2.1 设计压力与设计温度 670
2 钢制压力容器主要受压元件的强度计算 670
2.4 壁厚附加量 671
2.3 安全系数与许用应力 671
2.2 设计载荷 671
2.6 主要受压元件的强度计算 672
2.5 焊缝系数 672
3.1 常用钢材 673
3 钢制压力容器用的钢材和焊接材料 673
3.2 焊接材料 674
4.1 圆筒形容器 680
4 焊接压力容器常用的结构形式 680
4.2 球形容器 681
5.1 设计要点 682
5 压力容器常用焊接接头的设计 682
5.2 容器壳体的对接接头设计 684
5.4 接管、凸缘、法兰与壳体的焊接接头设计 687
5.3 平封头与筒体的焊接接头设计 687
5.5 管板与圆筒体的焊接接头设计 690
5.6 管子与管板连接的接头设计 694
6.1 悬挂式支座的焊接结构 695
6 支座与容器连接的结构设计 695
6.4 鞍式支座的焊接结构 696
6.3 裙式支座的焊接结构 696
6.2 支承式支座的焊接结构 696
6.6 多层容器与支座的连接结构 697
6.5 柱式支承的焊接结构 697
1.1 薄板及其工作特点 698
1 概述 698
第8章 薄壁焊接结构 698
1.2 薄壳及其工作特点 699
1.3 薄壁杆及其工作特点 701
2.1 薄壁结构设计要点 702
2 薄壁结构设计要点及连接 702
2.2 薄壁结构的连接 704
3.2 轿车车身的焊接结构 705
3.1 汽车车身及其结构特点 705
3 汽车中的薄壁焊接结构 705
3.3 客车车身焊接结构 707
3.4 货车车身焊接结构 708
3.5 电阻点焊薄壁结构设计注意事项 710
4.4 车顶焊接结构 712
4.3 侧墙焊接结构 712
4 铁路车辆中的薄壁焊接结构 712
4.1 客车车体的组成及其工作特点 712
4.2 底架焊接结构 712
4.5 侧墙与底架和车顶的连接 713
5.2 典型板架焊接结构设计 714
5.1 船体结构及其特征 714
5 船舶中的薄壁焊接结构 714
6.1 水工闸门简介 720
6 水利工程中的薄壁焊接结构 720
6.2 闸门的工作特点及其结构特征 722
6.4 闸门焊接结构的典型实例 723
6.3 闸门结构设计的基本要求 723
参考文献 729
第7篇 焊接结构制造 731
1.2 焊接生产发展趋势 733
1.1 焊接结构的特点 733
第1章 焊接结构制造工艺 733
1 概述 733
2.1 生产过程和工艺过程 734
2 制造工艺基础 734
2.2 工艺过程的组成 735
2.3 生产类型与特征 736
2.4 生产纲领和工艺文件 737
3.2 钢材的矫正 742
3.1 钢材预处理 742
3 焊接结构生产中的备料加工 742
3.3 划线、放样及号料 745
3.4 钢材的下料 746
3.6 钢材的弯曲及成形 748
3.5 钢材边缘的加工 748
3.7 钢材的制孔 749
4.1 焊接工艺分析原则 750
4 焊接结构生产工艺分析 750
4.2 焊接工艺分析方法 751
4.3 方案论证与生产准备 753
4.4 提高劳动生产率 754
4.5 桥式起重机主梁生产工艺分析 755
5.1 焊接工艺评定程序 758
5 焊接工艺评定与规程编制 758
6.1 焊前清理 759
6 焊接结构的装配与焊接 759
5.2 焊接工艺评定的规则 759
5.3 焊接工艺规程的编制 759
6.2 结构装配工艺 760
6.3 结构焊接工艺 762
6.4 焊接热处理 763
6.5 焊接过程检验 764
7.1 梁系结构的装焊工艺问题 766
7 典型焊接结构制造工艺 766
7.2 壳体结构的装焊工艺问题 768
7.3 桁架的装焊工艺问题 771
7.4 管子结构的装焊工艺问题 772
7.5 机器结构的焊接工艺问题 774
1.2 焊接工程应用软件的用途和分类 777
1.1 计算机技术与焊接生产信息化 777
第2章 焊接生产专家系统和CAPP 777
1 焊接工程应用软件概述 777
2 焊接专家系统的结构和原理 778
2.1 专家系统的基本特征 779
2.3 专家系统的知识获取与表示 780
2.2 专家系统的一般结构 780
2.4 专家系统的推理机制 782
2.5 专家系统的适用领域与分类 783
3.2 焊接专家系统的现状和典型应用 784
3.1 焊接专家系统的发展概况 784
3 焊接专家系统的发展和典型应用 784
3.3 焊接专家系统的发展趋势 790
4.1 焊接专家系统的开发与评价方法 791
4 焊接专家系统开发技术及其实例 791
4.2 压力容器焊接工艺专家系统 793
5.1 CAPP系统的发展 798
5 计算机辅助焊接工艺规划CAPP系统 798
5.3 CAPP系统的开发模式 799
5.2 CAPP系统的类型和特征 799
5.4 CAPP系统的发展趋势 800
6.2 焊接CAPP系统的开发 801
6.1 焊接结构件的装焊工艺特征 801
6 焊接CAPP系统的开发及实例 801
6.3 计算机辅助焊接工艺规划WCAPP系统 802
1.2 数据库技术的新进展 808
1.1 数据库技术的产生与应用 808
第3章 焊接数据库系统 808
1 焊接数据库系统的发展和应用 808
1.3 焊接数据库系统的发展 812
1.4 焊接数据库系统的典型应用 813
2.1 关系数据库系统基本原理及其设计 818
2 焊接数据库应用系统分析和开发 818
2.3 典型数据库管理系统 819
2.2 结构化数据库查询语言SQL 819
2.4 典型应用程序开发工具 820
2.5 焊接数据库应用系统设计及开发 822
3.1 系统需求分析 824
3 焊工技术档案管理系统 824
3.4 面向对象的事件驱动程序设计 825
3.3 数据库结构分析与设计 825
3.2 系统的总体结构 825
3.5 系统功能的实现 826
4.2 系统总体结构 828
4.1 系统需求分析 828
4 车身装焊质量信息管理系统 828
4.3 基本功能模块 829
4.4 工序质量统计分析与过程控制和诊断 830
1.3 焊接工艺装备的设计原则和应注意的问题 834
1.2 焊接工艺装备在焊接生产中的作用 834
第4章 焊接工艺装备 834
1 概论 834
1.1 焊接工艺装备的组成及分类 834
2.1 焊接工装夹具的分类与组成 835
2 焊接工装夹具 835
2.4 焊接工装夹具设计方案的确定 836
2.3 对焊接工装夹具的设计要求 836
2.2 焊接工装夹具的特点 836
2.5 焊件所需夹紧力的构成及计算 837
2.7 焊接工装夹具的精度与焊接结构制造精度等的关系 840
2.6 焊件的定位、定位器及夹具体 840
2.8 夹紧机构 842
3.1 焊接变位设备的分类及其应具备的性能 872
3 焊接变位设备 872
3.2 焊接变位机 873
3.3 焊接滚轮架 879
3.4 焊接翻转机及回转台 885
3.5 焊接操作机 888
3.6 电渣焊立架 895
3.7 焊工升降台 896
4.2 部分焊接工序设备及机具的性能与参数 898
4.1 设备用途及工艺目的 898
4 焊接工序设备 898
5.1 焊件变位设备的运动精度及保证措施 899
5 焊接机器人用的焊件变位设备 899
5.2 焊件变位设备及其在柔性加工单元中的布置 901
1.2 清洁生产的定义和原则 906
1.1 焊接清洁生产的意义和内容 906
第5章 焊接安全与清洁生产 906
1 焊接清洁生产 906
1.5 我国焊接清洁生产现状 907
1.4 清洁生产技术和方法 907
1.3 清洁生产的实施途径 907
2.1 焊接烟尘的污染 908
2 焊接中的污染及卫生防护 908
2.3 降低污染的措施 910
2.2 焊接中的其他污染 910
3 焊接安全生产 912
3.1 气焊与气割安全 913
3.2 电焊安全 919
3.3 特殊焊接作业安全 921
2 焊接标准体系现状 924
1 概述 924
第6章 标准与法规 924
3.1 基础标准部分 933
3 材料焊接的通用准则 933
3.3 焊接试验及检验标准 937
3.2 焊接材料标准 937
参考文献 939
第8篇 焊接生产质量管理与无损检测 943
2.3 ISO9000族的构成 945
2.2 质量管理的发展 945
第1章 焊接生产的质量管理 945
1 概述 945
2 质量管理和质量管理体系 945
2.1 定义 945
2.4 质量管理的八项基本原则 946
2.5 质量管理体系 947
3.1 焊接质量技术要求 948
3 焊接生产质量管理 948
3.2 ISO3834-2“完整质量要求”节选 949
4.1 我国锅炉压力容器制造监督管理、制造许可、产品安全性能监督检验的规定 951
4 焊接企业质量管理要求实例 951
3.3 ISO9000族与ISO3834间的关系 951
4.2 德国标准DIN6700《轨道车辆及其部件的焊接——第2部分:部件分级、焊接企业的认证、一致性的评定》简介 955
4.3 德国标准DIN18800-7钢结构——生产实施和焊接企业资格认证(2002.9) 959
1 概述 962
第2章 焊接结构的无损检测方法 962
2.5 射线透照布置 964
2.4 增感屏的选择 964
2 焊缝射线照相 964
2.1 射线照相原理 964
2.2 射线源的选择 964
2.3 射线胶片的选择 964
2.7 射线照相的像质计灵敏度与裂纹的检出率 967
2.6 射线照相检验级别 967
2.9 底片上缺陷影像的识别 969
2.8 焊缝射线照相的一般程序 969
2.10 射线照相底片的评定——GB/T 3323标准附录摘要 971
2.11 国外焊缝射线照相标准 973
2.13 射线照相新技术——实时成像技术和工定CT技术 974
2.12 焊缝射线照相工艺卡 974
3.2 超声波探伤的探头 975
3.1 超声波探伤原理和分类 975
3 焊缝超声波探伤 975
3.3 超声波探伤仪器 976
3.5 超声波探伤灵敏度 977
3.4 检验级别 977
3.6 焊缝超声波探伤的一般程序 978
3.11 国外焊缝超声波探伤标准 979
3.10 缺陷的评定——GB/T 11345—1989标准摘要 979
3.7 平板对接焊缝的超声波探伤 979
3.8 其他焊接结构的超声波探伤 979
3.9 缺陷信号的特征及测量 979
3.13 焊缝超声波探伤的新进展 983
3.12 超声波探伤工艺卡 983
4.2 磁化方法和规范 985
4.1 磁性探伤的原理与分类 985
4 焊缝的磁性探伤 985
4.4 磁粉及磁悬液 987
4.3 磁粉探伤设备 987
4.5 磁粉探伤灵敏度试片(块) 988
4.8 磁痕的观察与评定 989
4.7 磁粉探伤的操作程序 989
4.6 缺陷引起的漏磁场 989
4.9 国外焊缝磁粉探伤标准 990
4.11 磁性探伤的新技术 991
4.10 磁粉探伤工艺卡 991
5.1 渗透探伤的原理与分类 992
5 焊缝的渗透探伤 992
5.2 渗透探伤剂与灵敏度试块 993
5.5 国外渗透探伤标准 994
5.4 痕迹的解释与缺陷评定 994
5.3 渗透探伤的一般操作程序 994
5.7 渗透探伤的新技术 995
5.6 渗透探伤工艺卡 995
6.3 涡流探伤技术和过程 996
6.2 涡流探伤系统和探头 996
6 焊缝的涡流探伤 996
6.1 涡流探伤的原理 996
6.7 涡流探伤技术的新发展 997
6.6 探伤结果的评定 997
6.4 对比试样 997
6.5 涡流探伤的一般操作程序 997
7.2 金属磁记忆检测 998
7.1 声发射 998
7 焊缝无损检测的新方法 998
7.3 红外热成像检测 999
7.4 长途输送管道的检测设备 1000
3.1 按国内相关标准及规程实施的焊接技术培训 1001
3 焊接培训在我国的发展情况 1001
第3章 焊接资质人员培训与资格认证 1001
1 概述 1001
2 国际焊接培训体系简介 1001
4.1 国际焊接工程师、技术员、技师、技士(IWE/IWT/IWS/IWP)四类人员培训规程 1002
4 国际焊接人员培训规程 1002
3.2 引入国际上先进的焊接培训体系 1002
3.3 焊接培训与国际接轨 1002
4.2 国际焊接质检人员和国际焊工(IWIP/IW)培训规程 1004
5.1 中国职业焊接技能鉴定规范 1010
5 我国国内焊接人员培训及考试部分规程 1010
5.2 我国锅炉压力容器管道焊工考试与管理规则 1013
6.1 国际资质焊接人员培训在我国的开展情况 1019
6 国际资质焊接人员培训在我国的开展情况及作用 1019
6.2 国际培训及资格认证工作作用 1020
第9篇 焊接结构服役与再制造 1021
1.3 断口形貌 1023
1.2 断裂机制 1023
第1章 焊接结构的断裂及安全评定 1023
1 断裂分类及术语 1023
1.1 断裂性质 1023
2 焊接结构的工作特点及防断设计 1024
2.1 典型的脆性事故举例 1024
2.2 断裂机理及设计准则 1025
2.3 与防断设计准则相关的试验方法 1026
2.4 影响结构断裂的因素 1043
3 基于“合于使用”原则的断裂评定 1046
3.1 “合于使用”原则及其发展 1046
3.2 面型缺陷的评定 1048
第2章 焊接结构的疲劳与寿命 1063
1 疲劳断裂过程及特性 1063
2 疲劳载荷 1064
2.1 应力循环特性与应力幅的概念及其相互的关系 1064
2.2 应力分类 1066
2.3 应力强度因子方法 1072
3.1 以标称应力表征的典型焊接结构件及接头的疲劳强度 1076
3 疲劳强度 1076
3.2 按热点应力决定构件疲劳强度 1093
4 断裂力学在焊接结构疲劳裂纹扩展中的应用 1095
3.4 结构件疲劳强度的修正 1095
4.1 裂纹的亚临界扩展 1095
3.3 按缺口应力给定的构件疲劳强度 1095
4.2 疲劳裂纹扩展特性da/dN-△K曲线的一般关系 1096
4.3 疲劳裂纹扩展寿命的估算 1096
5.1 方法 1098
5.2 数据统计 1098
5 根据试验方法测定焊接构件的疲劳强度 1098
6 疲劳设计 1099
7.2 改善方法的应用 1101
7.1 综述 1101
7.3 方法 1101
7 提高疲劳强度的技术 1101
1 焊接结构的腐蚀失效 1107
1.1 焊接接头腐蚀破坏的基本形式 1107
第3章 焊接结构的环境失效 1107
1.2 焊接结构在自然环境下的腐蚀 1108
1.3 焊接结构的局部腐蚀 1109
2 介质环境作用下的断裂与疲劳 1113
2.1 应力腐蚀破裂 1113
2.2 环境氢脆 1117
2.3 腐蚀疲劳 1120
3 焊接接头抗腐蚀性的评定及提高抗腐蚀性的措施 1121
3.1 焊接接头的腐蚀试验 1121
3.2 常见焊接接头的抗蚀性 1122
3.3 提高焊接接头抗蚀性的途径 1123
3.4 焊接结构的表面防护 1123
4.1 高温下焊接接头的组织变化 1125
4.2 焊接接头的高温性能 1125
4 焊接接头的耐热性 1125
4.3 焊接接头的高温蠕变 1126
4.4 焊接接头的高温氧化 1127
4.5 焊接接头的热疲劳 1128
5 环境加速焊接结构失效典型事例及其分析 1128
1.1 再制造工程的概念 1130
1 再制造工程概述 1130
1.2 再制造工程的地位、作用和影响 1130
第4章 焊接结构的再制造与延寿技术 1130
1.3 再制造工程的国外发展现状 1132
1.4 再制造工程的国内发展现状 1132
1.5 再制造工程的巨大效益 1133
1.6 再制造加工工艺及费用分析 1133
2.1 废旧产品的再制造性评价 1135
2.2 废旧产品的失效机理和寿命评估 1135
2 再制造工程的设计基础 1135
2.3 废旧产品的再制造建模 1136
2.4 面向再制造的产品设计 1136
3 焊接结构再制造延寿的关键技术 1137
3.1 热喷涂技术 1137
3.2 电刷镀技术 1138
3.3 表面粘涂技术 1139
4 焊接结构再制造延寿技术应用实例 1140
4.1 电弧喷涂技术在海洋船只钢板防腐延寿中的应用 1140
3.4 堆焊技术 1140
4.2 油田储罐再制造延寿 1143
4.3 绞吸挖泥船绞刀片再制造技术及应用 1144
4.4 发酵罐内壁火焰喷涂塑料再制造延寿应用 1145
参考文献 1147