图书介绍
精密和超精密机床控制技术pdf电子书版本下载
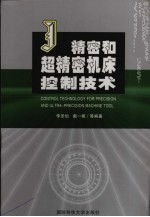
- 李圣怡,戴一帆,解旭辉等编著 著
- 出版社: 长沙:国防科技大学出版社
- ISBN:9787810995603
- 出版时间:2008
- 标注页数:426页
- 文件大小:17MB
- 文件页数:442页
- 主题词:数控机床-控制系统
PDF下载
下载说明
精密和超精密机床控制技术PDF格式电子书版下载
下载的文件为RAR压缩包。需要使用解压软件进行解压得到PDF格式图书。建议使用BT下载工具Free Download Manager进行下载,简称FDM(免费,没有广告,支持多平台)。本站资源全部打包为BT种子。所以需要使用专业的BT下载软件进行下载。如 BitComet qBittorrent uTorrent等BT下载工具。迅雷目前由于本站不是热门资源。不推荐使用!后期资源热门了。安装了迅雷也可以迅雷进行下载!
(文件页数 要大于 标注页数,上中下等多册电子书除外)
注意:本站所有压缩包均有解压码: 点击下载压缩包解压工具
图书目录
第一章 超精密车床进给系统建模及经典控制1.1 超精密车床控制技术研究的概述 1
1.2 KD250型试验超精密车床简介 3
1.2.1 机床的结构特点 3
1.2.2 机床的伺服控制位置检测 4
1.2.3 试验超精密机床的控制特性实验 7
1.3 超精密车床进给系统建模与辨识 16
1.3.1 电气传动部分的建模 18
1.3.2 机械传动部分的建模 20
1.3.3 系统的传递函数 21
1.4 超精密车床进给系统频域特性测试 22
1.4.1 系统频率响应测试的实施 23
1.4.2 超精密车床进给系统模型参数频域辨识 27
1.5 超精密车床进给系统模型参数时域辨识 29
1.5.1 时域模型表示 29
1.5.2 测试信号的产生 29
1.5.3 系统模型参数的MLS辨识 30
1.6 超精密车床进给系统模型的频域分析 32
1.7 系统模型的转换和处理 36
1.7.1 连续和离散传递函数的相互转换 36
1.7.2 高阶传递函数的简化处理 38
1.8 超精密车床进给经典控制策略 41
1.8.1 基于模型的PID调节器参数整定 42
1.8.2 基于过程特征参数的PID调节器参数整定 46
1.8.3 速度/加速度前馈控制器设计 50
1.8.4 伪微分反馈控制器设计 53
1.8.5 变增益PID“+”速度前馈控制器设计 55
1.9 控制参数的优化 63
1.9.1 综合性能指标 63
1.9.2 优化算法和波形 64
1.9.3 控制参数的优化 68
参考文献 71
第二章 超精密机床的数控系统的设计与研究2.1 数控系统硬件和运动控制器技术的综述 73
2.1.1 运动控制器技术 73
2.1.2 运动控制器在超精密机床CNC系统中的应用 80
2.2 超精密车床数控内核和特殊插补软件的研究 84
2.3 KDMC系列运动控制器设计 88
2.3.1 运动控制器的基本功能原理与结构 90
2.3.2 运动控制器的软件设计 96
2.3.3 上位机软件的设计 105
2.4 PMAC多轴运动控制器及应用 107
2.4.1 PMAG的功能与特点 108
2.4.2 基于COM标准系统管理软件的开发 112
2.4.3 PMAC实时软件 118
2.5 超精密数控系统在线圆弧插补算法 126
2.5.1 两维空间曲线在线圆弧插补算法与误差分析 126
2.5.2 轮廓加工的刀具半径补偿 131
2.5.3 超精密数控系统中双圆弧伸缩步长插补算法 132
2.5.4 列表曲线的三次B样条拟合处理 136
2.6 复杂曲线或曲面的双圆弧逼近 141
2.6.1 双圆弧逼近复杂曲线的基本理论 141
2.6.2 双圆弧逼近任意函数曲线的程序段数目计算 145
2.6.3 双圆弧逼近复杂曲线示例 146
2.6.4 Spiral曲线的双圆弧逼近 147
2.6.5 Spiral曲线的单边圆弧逼近及误差计算 151
2.6.6 Spiral曲线的近似最优双圆弧逼近 153
2.6.7 Spiral曲线近似最优双圆弧逼近示例 155
参考文献 157
第三章 超精密加工的多轴耦合与解耦控制策略3.1 轮廓误差及其来源 163
3.2 伺服系统动态特性对轮廓加工精度的影响分析 165
3.3 轮廓误差交叉耦合控制(Cross-Coupling Control-CCC) 168
3.3.1 轮廓误差模型 170
3.3.2 CCC控制器的实现 171
3.3.3 机床耦合轮廓控制器性能分析 173
3.4 同步控制 178
3.5 细插补运动控制 180
3.6 轮廓误差控制仿真结果 184
参考文献 185
第四章 基于QFT的超精密轨迹跟踪控制器的设计 185
4.1 超精密机床进给机构控制要求及QFT控制方法特点 187
4.2 QFT控制方法设计原理 189
4.2.1 线性系统跟踪问题的QFT控制器设计原理 189
4.2.2 QFT方法在采样控制系统中的应用 196
4.2.3 基于QFT的非线性时不变系统的控制器设计 198
4.3 超精密机床进给系统QFT控制器的设计 200
4.3.1 控制系统结构 200
4.3.2 确定系统不确定性 202
4.3.3 确定控制系统设计指标 202
4.3.4 控制器G的设计 204
4.3.5 前置滤波器F的设计 207
4.3.6 稳定性分析 207
4.3.7 控制系统分析 208
4.4 基于QFT的复合控制策略 211
4.4.1 前馈控制器 211
4.4.2 带复位功能的积分控制器 213
4.4.3 QFT控制试验 216
4.5 关于QFT控制器设计的讨论 218
参考文献 219
第五章 超精密机床伺服进给系统的摩擦控制5.1 超精密机床伺服进给系统stick/slip摩擦的仿真模型 222
5.1.1 超精密机床伺服进给系统stick/slip摩擦产生的机理 222
5.1.2 超精密机床伺服进给系统stick/slip摩擦运动仿真模型 227
5.2 超精密机床伺服进给系统stick/slip摩擦运动特性分析 231
5.2.1 模型的有效性分析 231
5.2.2 模型动力学分析 232
5.3 超精密机床伺服进给系统摩擦非线性对机床性能的影响 236
5.3.1 超精密机床伺服进给系统的结构 237
5.3.2 Stick/Slip摩擦非线性对机床位置精度的影响 237
5.3.3 Stick/Slip摩擦非线性对机床跟踪特性的影响 239
5.3.4 超精密CNC机床轮廓精度测试 240
5.4 基于神经网络的超精密机床伺服进给系统非线性模型 243
5.4.1 神经网络学习算法 243
5.4.2 超精密机床伺服进给系统前馈神经网络训练 245
5.5 超精密机床伺服进给系统摩擦控制技术研究 250
5.5.1 摩擦控制与补偿的基本思想和方法 250
5.5.2 模糊滑模智能控制 253
参考文献 266
第六章 压电陶瓷驱动微进给伺服控制系统 270
6.1 微进给伺服刀架实现方法概述 270
6.2 压电陶瓷驱动微进给伺服刀具控制系统设计 273
6.2.1 压电陶瓷微位移器的工作原理 273
6.2.2 柔性铰链结构 275
6.2.3 直流高压驱动电源设计 278
6.2.4 其他直流高压驱动电源简介 281
6.3 微动伺服系统的实验研究 284
6.3.1 微进给系统性能测试 284
6.3.3 微动装置闭环特性测试研究 287
6.4 两坐标双重伺服轮廓误差补偿实验研究 290
6.4.1 超精密车削加工机床的双重伺服控制系统 290
6.4.2 双重伺服控制理论的数学论证 295
6.4.3 两坐标双重伺服轮廓误差补偿实验研究 298
6.5 压电陶瓷磁滞非线性分析及建模 303
6.5.1 概述 303
6.5.2 Preisach—Krasnoselkii模型 304
6.5.3 压电陶瓷建模的实验研究 311
6.6 压电陶瓷微进给执行器典型控制方法 319
6.6.1 线性化动态模型与控制 319
6.6.2 非线性动态数据系统(NLDDS)建模与控制 325
6.6.3 超精密加工中压电陶瓷刀具位置的自学习控制 332
参考文献 341
第七章 直线电机伺服刀架及机床溜板伺服系统7.1 直线电机驱动概述 346
7.1.1 直线电机直接驱动的特点 346
7.1.2 直线电机的类型 348
7.2 高频响、大刚度音圈电机及伺服刀架 354
7.2.1 音圈电机伺服刀架结构及动力学模型 355
7.2.2 伺服刀架的半闭环控制 359
7.2.3 伺服刀架闭环控制的传统设计 364
7.3 高频响、大刚度伺服刀架的H∞控制研究 369
7.3.1 H∞控制概述 369
7.3.2 非圆车削系统模型特点 375
7.3.3 高频响伺服刀架的H∞控制器研究 381
7.3.4 基于内模原理的H∞重复控制器 392
7.4 直线电机机床溜板伺服系统 397
7.4.1 超精密加工中的慢速刀具伺服系统 397
7.4.2 永磁直线同步电机实验平台简介 402
7.4.3 永磁直线同步电机建模 404
7.4.4 永磁直线同步电机控制实验 409
参考文献 422