图书介绍
Mastercam X2数控编程经典学习手册pdf电子书版本下载
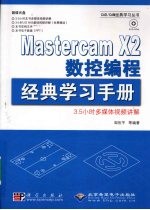
- 阎伍平等编著 著
- 出版社: 北京:科学出版社
- ISBN:9787030252463
- 出版时间:2009
- 标注页数:454页
- 文件大小:122MB
- 文件页数:468页
- 主题词:数控机床-加工-计算机辅助设计-应用软件,Mastercam X2
PDF下载
下载说明
Mastercam X2数控编程经典学习手册PDF格式电子书版下载
下载的文件为RAR压缩包。需要使用解压软件进行解压得到PDF格式图书。建议使用BT下载工具Free Download Manager进行下载,简称FDM(免费,没有广告,支持多平台)。本站资源全部打包为BT种子。所以需要使用专业的BT下载软件进行下载。如 BitComet qBittorrent uTorrent等BT下载工具。迅雷目前由于本站不是热门资源。不推荐使用!后期资源热门了。安装了迅雷也可以迅雷进行下载!
(文件页数 要大于 标注页数,上中下等多册电子书除外)
注意:本站所有压缩包均有解压码: 点击下载压缩包解压工具
图书目录
第1篇 Mastercam加工基础第1章 数控加工基础 2
1.1 数控机床概述 2
1.1.1 数控机床概念 2
1.1.2 数控机床的特点 2
1.1.3 数控机床的组成 3
1.1.4 数控机床的发展 3
1.2 数控编程基本概念 3
1.2.1 数控编程的概念 3
1.2.2 自动编程概念和特点 4
1.2.3 自动编程的内容与步骤 4
1.3 编程基础 5
1.3.1 字符与字的功能 5
1.3.2 程序格式 7
1.4 数控加工工艺 8
1.4.1 数控加工工艺的内容 8
1.4.2 数控加工工艺的特点 8
1.4.3 工序与工步的划分 9
1.4.4 确定走刀路线 9
1.4.5 零件的安装与夹具的选择 10
1.4.6 刀具的选择与切削用量的确定 11
1.4.7 对刀点与换刀点的确定 11
第2章 Mastercam概述 13
2.1 安装 13
2.2 Mastercam X2功能介绍 18
2.3 界面介绍 20
2.4 帮助 21
2.5 退出软件 22
第3章 建模基础 23
3.1 文件的管理 23
3.1.1 创建新文件 23
3.1.2 打开文件 24
3.1.3 合并文件 25
3.1.4 保存文件 25
3.1.5 输入/输出目录 26
3.2 属性设置 27
3.2.1 工作区背景颜色的设置 27
3.2.2 设置系统颜色 28
3.2.3 设置图层 30
3.2.4 设置特征属性 31
3.2.5 改变属性 32
3.3 对象分析 35
3.3.1 图素属性分析 35
3.3.2 分析点坐标 36
3.3.3 两点间距 36
3.3.4 分析面积/体积 37
3.3.5 串联分析 38
3.3.6 外形分析 39
3.3.7 角度分析 40
3.3.8 动态分析 40
3.3.9 曲面检测 41
3.3.10 实体检测 42
3.4 绘制曲面曲线 42
3.4.1 指定边界 42
3.4.2 所有边界 43
3.4.3 缀面边线 43
3.4.4 曲面流线 44
3.4.5 动态绘线 44
3.4.6 绘制剖切线 44
3.4.7 曲面曲线 45
3.4.8 分模线 46
3.4.9 相交线 46
第4章 加工设置 48
4.1 设置加工刀具 48
4.1.1 从刀具库中选择刀具 48
4.1.2 修改刀具库刀具 49
4.1.3 自定义新刀具 50
4.1.4 设置刀具参数 51
4.2 设置加工工件 53
4.2.1 设置工件尺寸及原点 53
4.2.2 设置工件材料 54
4.3 加工仿真模拟 55
4.3.1 刀具路径模拟 55
4.3.2 实体加工模拟 56
4.3.3 后处理设置 57
4.4 加工通用参数设置 57
4.4.1 高度设置 57
4.4.2 补偿设置 58
4.4.3 转角设置 60
4.4.4 外形分层 61
4.4.5 深度分层 61
4.4.6 进/退刀向量 63
4.4.7 过滤设置 65
第2篇 Mastercam铣床加工第5章 外形铣削加工 68
5.1 外形铣削 68
5.1.1 设置外形参数 69
5.1.2 2D外形倒角铣削加工 70
5.1.3 斜插加工 72
5.1.4 残料加工 73
5.1.5 3D加工 73
5.2 2D外形铣削加工综合应用 74
5.2.1 绘制二维图形 74
5.2.2 刀具路径的编制 76
5.2.3 材料设置 79
5.3 外形铣削加工实例 80
5.3.1 绘制二维图形 81
5.3.2 刀具路径编制 82
5.3.3 材料设置 85
5.3.4 二维绘图 86
5.3.5 刀具路径的编制 87
第6章 二维挖槽加工 90
6.1 2D标准挖槽加工 90
6.1.1 2D标准挖槽加工步骤 90
6.1.2 2D挖槽参数 91
6.1.3 粗切/精修的参数 92
6.1.4 岛屿及挖槽区 97
6.2 使用岛屿深度 98
6.3 挖槽平面加工 101
6.4 残料加工 102
6.5 开放式挖槽 103
6.6 挖槽综合应用实例 104
6.6.1 二维图形绘制 104
6.6.2 刀具路径的编制 106
6.6.3 材料设置及模拟加工 109
6.7 挖槽加工实例 111
6.7.1 图形绘制 111
6.7.2 标准挖槽 113
6.7.3 开放式挖槽 116
6.7.4 材料设置和实体模拟 119
第7章 钻孔加工 122
7.1 钻孔加工参数 122
7.1.1 钻孔类型 122
7.1.2 刀尖补偿 124
7.1.3 深度补偿 125
7.2 钻孔点的选择方式 126
7.2.1 手动方式 126
7.2.2 自动方式 126
7.2.3 图素选点 127
7.2.4 视窗选点 127
7.2.5 栅格阵列钻孔点 128
7.2.6 圆周阵列钻孔点 128
7.2.7 限定圆弧 129
7.2.8 钻孔点排序 129
7.3 钻孔加工综合实例 131
7.3.1 二维图形的绘制 131
7.3.2 对D12孔进行钻孔加工 135
7.3.3 对D20的孔进行钻孔加工 137
7.3.4 对D32的孔进行钻孔加工 139
7.3.5 对D48的孔进行钻孔加工 142
7.3.6 设置材料及模拟加工 144
第8章 面铣加工 146
8.1 面铣加工参数 146
8.1.1 深度设置 147
8.1.2 Z轴分层铣深 147
8.1.3 切削方式设置 147
8.1.4 刀具超出量 148
8.1.5 自动计算角/粗切角度 148
8.1.6 步进量 148
8.1.7 两切削间的位移方式 148
8.2 面铣加工实例 149
第9章 雕刻加工 153
9.1 雕刻加工 153
9.1.1 粗切方式 154
9.1.2 加工顺序 154
9.1.3 切削参数 154
9.2 线条雕刻加工实例应用 155
9.2.1 二维图形绘制 156
9.2.2 线条雕刻加工刀具路径 157
9.2.3 雕刻加工模拟 160
9.3 凸字雕刻加工实例应用 162
9.3.1 凸字雕刻加工刀具路径 162
9.3.2 雕刻加工模拟 165
9.4 凹字雕刻加工实例应用 167
9.4.1 凹字雕刻刀具路径的编制 167
9.4.2 凹字雕刻加工工件设置及模拟 169
第10章 二维加工综合应用 171
10.1 外形铣削加工 171
10.2 挖槽刀具路径 174
10.3 加工模拟 177
第11章 曲面加工参数 178
11.1 刀具路径参数设置 178
11.2 曲面加工参数 180
11.3 进/退刀向量 181
11.4 校刀长位置 182
11.5 加工曲面/干涉面/加工范围 183
11.6 预留量设置 183
11.7 刀具切削范围 184
11.8 切削深度 184
11.9 间隙设定 186
11.10 进阶设定 190
11.11 限定深度 192
第12章 曲面粗加工 193
12.1 平行粗加工 193
12.1.1 粗加工平行铣削参数 193
12.1.2 平行粗加工实例一 196
12.1.3 平行粗加工实例二 202
12.1.4 平行粗加工实例三 208
12.2 放射状粗加工 213
12.2.1 放射粗加工参数 213
12.2.2 放射状凹形工件加工实例 214
12.2.3 放射状凸形工件加工实例 219
12.3 投影加工 223
12.3.1 曲线投影加工实例 224
12.3.2 NCI投影加工实例 228
12.3.3 点集投影加工实例 233
12.4 挖槽粗加工 237
12.4.1 挖槽粗加工参数 237
12.4.2 凹槽形挖槽加工实例 241
12.4.3 岛屿形挖槽加工实例 246
12.4.4 凸形挖槽加工实例 251
12.4.5 挖槽粗加工综合应用 256
12.5 残料粗加工 262
12.5.1 残料加工参数 262
12.5.2 残料加工实例 265
12.6 钻削式加工 269
12.6.1 钻削式加工参数 269
12.6.2 钻削式加工实例 270
第13章 曲面精加工 275
13.1 平行精加工 275
13.1.1 平行精加工参数 275
13.1.2 平行精加工实例 276
13.2 放射状精加工 281
13.2.1 放射状精加工参数 281
13.2.2 放射精加工实例 282
13.3 投影精加工 286
13.3.1 投影精加工参数 286
13.3.2 投影精加工实例 287
13.4 曲面流线精加工 292
13.4.1 曲面流线加工菜单 292
13.4.2 流线精加工参数 294
13.4.3 流线精加工实例 295
13.5 等高外形精加工 299
13.5.1 等高外形精加工参数 299
13.5.2 沿Z轴等分等高外形精加工实例 302
13.5.3 沿外形曲线等分等高外形精加工实例 306
13.6 陡斜面精加工 310
13.6.1 陡斜面精加工参数 310
13.6.2 陡斜面精加工实例 312
13.7 浅平面精加工 317
13.7.1 浅平面精加工参数 317
13.7.2 浅平面精加工实例 319
13.8 交线清角精加工 323
13.8.1 交线清角精加工参数 323
13.8.2 交线清角精加工实例 324
13.9 残料清角精加工 328
13.9.1 残料清角精加工参数 329
13.9.2 残料清角的材料参数 330
13.9.3 残料清角精加工实例 330
13.10 环绕等距精加工 334
13.10.1 环绕等距精加工参数 334
13.10.2 环绕等距精加工刀具路径实例 335
13.11 熔接精加工 339
13.11.1 熔接精加工参数 339
13.11.2 熔接精加工实例 341
第14章 刀具路径转换 345
14.1 刀具路径转换参数 345
14.1.1 平移转换参数 346
14.1.2 旋转转换参数 347
14.1.3 镜像转换参数 347
14.2 刀具路径转换实例 348
14.2.1 刀具路径规划 348
14.2.2 平移转换刀具路径 349
14.2.3 旋转转换刀具路径 350
14.2.4 镜像转换刀具路径 351
14.2.5 实体加工模拟 352
第15章 凹模加工综合应用 354
15.1 凹模加工特点 354
15.2 凹模加工实例 354
15.2.1 刀路规划 355
15.2.2 挖槽粗加工 355
15.2.3 小刀挖槽加工 358
15.2.4 等高外形精加工 360
15.2.5 平行精加工 362
15.2.6 实体加工模拟 364
第16章 凸模加工综合应用 366
16.1 凸模加工特点 366
16.2 凸模加工实例 366
16.2.1 刀具路径规划 366
16.2.2 挖槽粗加工 367
16.2.3 D6刀具挖槽加工 370
16.2.4 等高外形精加工 371
16.2.5 浅平面精加工 373
16.2.6 平面挖槽加工 375
16.2.7 实体加工模拟 378
第3篇 Mastercam车床加工第17章 数控车削加工基础 380
17.1 数控车削的概念、特点及应用 380
17.1.1 数控车削的概念 380
17.1.2 数控车削的特点 380
17.1.3 数控车削的应用 380
17.2 车床坐标系 381
17.2.1 车床坐标轴 381
17.2.2 机床原点、参考点、工件原点 381
17.2.3 机床坐标系、编程坐标系和工件坐标系 381
17.2.4 坐标系的建立 382
17.2.5 对刀操作 382
17.3 数控车削工艺 383
17.3.1 分析零件图 383
17.3.2 尺寸处理 384
17.3.3 数控车削加工进给路线的确定 384
17.4 设置车削刀具 384
17.4.1 从刀具库选择刀具 385
17.4.2 修改刀具库刀具 386
17.4.3 自定义新刀具 389
17.4.4 删除刀具库刀具 393
17.4.5 设置刀具参数 394
17.5 设置加工工件及模拟 396
17.5.1 设置加工工件 396
17.5.2 加工模拟 400
17.5.3 后置处理 401
第18章 粗车削 403
18.1 粗车削参数设置 403
18.1.1 粗车步进量和预留量 404
18.1.2 车削方式 405
18.1.3 补偿设置 405
18.1.4 进/退刀向量设置 407
18.1.5 进刀参数 410
18.1.6 半精车 411
18.2 粗车削实例 412
18.2.1 粗车刀具路径 412
18.2.2 车槽加工刀具路径 416
18.2.3 材料设置和刀具路径模拟 421
第19章 精车削 424
19.1 精车削加工参数 424
19.1.1 精车步进量和预留量 424
19.1.2 补偿设置 425
19.1.3 进退刀向量 425
19.1.4 进刀参数设置 426
19.1.5 过滤设置 426
19.1.6 圆角和倒角设置 427
19.2 精车削实例 429
第20章 径向车削和车端面 435
20.1 径向车削的切槽选项 435
20.1.1 1 Point(点) 436
20.1.2 2点 436
20.1.3 3 Lines(线) 436
20.1.4 Chain(串联) 437
20.2 径向车削外形参数 437
20.3 径向粗车参数 439
20.4 径向精车参数 440
20.5 径向精车实例 441
20.6 车端面参数 446
20.7 车端面实例 448
附录1 数控机床标准G代码 453
附录2 数控机床标准M代码 454