图书介绍
航空制造工程手册:特种加工pdf电子书版本下载
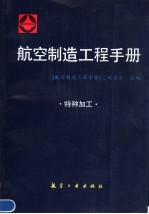
- 《航空制造工程手册》总编委会主编 著
- 出版社: 北京:航空工业出版社
- ISBN:7800466809
- 出版时间:1993
- 标注页数:733页
- 文件大小:46MB
- 文件页数:751页
- 主题词:
PDF下载
下载说明
航空制造工程手册:特种加工PDF格式电子书版下载
下载的文件为RAR压缩包。需要使用解压软件进行解压得到PDF格式图书。建议使用BT下载工具Free Download Manager进行下载,简称FDM(免费,没有广告,支持多平台)。本站资源全部打包为BT种子。所以需要使用专业的BT下载软件进行下载。如 BitComet qBittorrent uTorrent等BT下载工具。迅雷目前由于本站不是热门资源。不推荐使用!后期资源热门了。安装了迅雷也可以迅雷进行下载!
(文件页数 要大于 标注页数,上中下等多册电子书除外)
注意:本站所有压缩包均有解压码: 点击下载压缩包解压工具
图书目录
1.1 特种加工技术的发展 1
1.2 特种加工技术的特点 1
第1章 概述 1
1.3 特种加工技术的分类 2
1.4 特种加工技术应用范围 3
1.5 特种加工技术在航空工业中的应用及其发展趋势 7
1.6 本分册的内容 12
2.1.1 分类及特征 13
2.1 概论 13
第2章 电解加工 13
2.1.2 应用范围 20
2.1.3 国内外应用现状及发展动态 21
2.2.1 电解加工的电极反应 24
2.2 电解加工基本原理 24
2.2.2 电解加工与法拉第定律 25
2.2.3.1 术语及常用电极的标准电极电位 26
2.2.3 电解加工的极化效应 26
2.2.3.4 极化与电流效率 29
2.2.3.3 极化与分解电压 29
2.2.3.2 极化的形成及影响因素 29
2.2.4 阳极的活化、钝化和超钝化 31
2.2.3.5 分解电压与电流效率的测定方法 31
2.3.1.1 组成、分类和选型 34
2.3.1 总体论述 34
2.2.5 极化对电解加工的影响 34
2.3 电解加工设备 34
2.3.1.2 设备主要规格的选取 36
2.3.1.3 电解加工设备的总体要求 38
2.3.2.1 电解加工机床的组成、技术要求及主要部件结构的选取 39
2.3.2 机床 39
2.3.2.2 叶片电解加工机床 44
2.3.2.4 立式单头电解加工机床 50
2.3.2.3 大型卧式单头电解加工机床 50
2.3.2.5 电解磨削机床 51
2.3.3.1 基本要求 54
2.3.3 电解加工电源及短路保护系统 54
2.3.3.2 分类、特征及应用范围 55
2.3.3.3 可控硅整流电源及斩波器 56
2.3.3.4 快速短路保护系统 58
2.3.4.1 组成 59
2.3.4 电解液系统 59
2.3.4.2 功能及基本要求 60
2.3.4.3 电解液主泵 61
2.3.4.5 恒温系统 63
2.3.4.4 电解液槽 63
2.3.4.6 电解液净化装置 64
2.3.5.1 组成及功能 65
2.3.5 自动控制系统 65
2.3.5.2 加工间隙参数的采样和控制 66
2.3.5.3 加工循环的自动控制 67
2.3.5.4 电解加工控制系统类型 69
2.4.1.2 电解液的分类 70
2.4.1.1 电解液的作用及对电解液的基本要求 70
2.4 电解加工工艺 70
2.4.1 电解液 70
2.4.1.4 常用电解加工材料的电解液配方 72
2.4.1.3 几种常用的电解液 72
2.4.2.2 间隙公式 73
2.4.2.1 间隙的作用及其影响因素 73
2.4.2 加工间隙 73
2.4.2.3 间隙与电场、流场 74
2.4.2.5 间隙的几何形状及概算 78
2.4.2.4 间隙的分布与大小的选择 78
2.4.3.1 概述 81
2.4.3 流场 81
2.4.3.2 三种基础流场的分析 83
2.4.3.3 平面与孔加工流场 84
2.4.3.4 叶片电解加工流场 85
2.4.4.1 工具阴极的分类 86
2.4.4.工具阴极及夹具 86
2.4.4.2 工具阴极的设计 88
2.4.4.3 工具阴极的制造 104
2.4.4.4 电解加工夹具 105
2.5.1.1 混气电解加工的特点 107
2.5.1 混气电解加工 107
2.5 提高电解加工精度的措施 107
2.5.1.2 混气腔的设计 109
2.5.2.2 脉冲电流加工的分类 111
2.5.2.1 原理、特点、应用范围 111
2.5.2 脉冲电流加工 111
2.5.2.3 脉冲电流加工工艺及实例 112
2.6.1.1 分类、特证、应用范围 115
2.6.1 叶片加工 115
2.6 电解加工在航空工业中的应用 115
2.6.1.2 典型加工实例 117
2.6.1.3 叶片电解加工常见疵病、故障及排除 119
2.6.2.1 二维不变截面整体叶轮、定子叶栅叶片型面加工 120
2.6.2 整体叶轮加工 120
2.6.2.2 变截面扭转整体叶轮型面加工 122
2.6.2.3 疵病、故障及排除 123
2.6.3.1 分类、特证及参数 124
2.6.3 小孔加工 124
2.6.3.2 典型加工零件 125
2.6.4 机匣加工 127
2.6.3.3 加工故障及排除 127
2.6.4.1 加工方法概述 128
2.6.4.2 电解液及工艺参数选用 129
2.6.5.1 电解加工表面质量的特点 130
2.6.5 电解加工的表面质量与疲劳强度 130
2.6.4.3 加工尺寸范围及加工精度 130
2.6.5.2 影响表面质量的因素及改善表面质量的措施 131
2.6.5.3 电解加工对疲劳强度的影响及提高电解加工零件疲劳强度的方法 134
2.7.1 电解去毛刺及尖边倒圆 137
2.7 其他类型电解加工工艺 137
2.7.1.1 原理及工艺 138
2.7.1.2 应用实例 139
2.7.2.2 基本工艺规律 142
2.7.2.1 用途、特点 142
2.7.2 电解抛光 142
2.7.2.3 电抛光表面疵病、原因、质量措施 144
2.7.2.4 应用举例 146
2.7.3.1 概述 149
2.7.3 电解磨削 149
2.7.3.2 电解液 151
2.7.3.3 主要工艺参数 152
2.7.3.4 应用实例 154
2.7.3.5 电解磨削导电磨轮 158
2.8.1.1 电解液对环境的污染 159
2.8.1 电解加工的环境污染及环境保护 159
2.8 技术安全 159
2.8.2 电解泥的提炼 160
2.8.1.2 对大气的污染 160
附表 161
3.1.1.1 电火花成形穿孔加工 167
3.1.1 分类 167
第3章 电火花加工 167
3.1 概述 167
3.1.1.4 电火花展成加工 168
3.1.1.3 电火花线电极加工 168
3.1.1.2 电火花磨削加工 168
3.1.3.1 电参数 169
3.1.3.极间放电状态及检测 169
3.1.2 机理 169
3.1.3.4 极间放电状态的检测 172
3.1.3.3 脉冲能量 172
3.1.3.2 脉冲分类 172
3.2.1 电火花成形加工机系列 173
3.2 电火花成形加工设备 173
3.2.2 主机结构特点、形式、性能 175
3.2.2.1 主轴头 176
3.2.2.2 工作台 177
3.2.3.1 脉冲电源 178
3.2.3 电源 178
3.2.3.2 数控电源 179
3.2.4.1 控制过程参数对工艺指标的影响 180
3.2.4 控制系统 180
3.2.4.4 控制功能 182
3.2.4.3 控制方式分类 182
3.2.4.2 控制系统的目标 182
3.2.5.1 工作液的作用 186
3.2.5 工作液及其循环过滤系统 186
3.2.5.3 添加剂 187
3.2.5.2 常用工作液 187
3.2.5.5 工作液的过滤 188
3.2.5.4 工作液循环系统 188
3.2.6.2 平动头 190
3.2.6.1 电极夹头 190
3.2.6 辅助设备及附件 190
3.2.7.1 主控制系统 191
3.2.7 数控电火花成形机 191
3.2.7.2 机械系统与运动控制 192
3.2.7.3 电源 194
3.3.1 工具电极形式 196
3.3 工具电极 196
3.2.7.4 辅助控制功能 196
3.3.2.1 工具电极常用材料 197
3.3.2 工具电极材料 197
3.3.2.2 电极材料的选择 199
3.3.3.1 电极损耗定义 202
3.3.3 工具电极损耗 202
3.3.3.2 影响电极损耗的因素 204
3.3.4.1 工具电极设计 206
3.3.4 工具电极设计与制造 206
3.3.4.2 工具电极的制造 211
3.3.5.1 工具电极的工艺基准校正 214
3.3.5 工具电极的安装 214
3.3.5.2 工具电极的装夹 215
3.3.5.3 工具电极对工件的找正 217
3.4.1.1 电火花穿孔加工 220
3.4.1 电火花加工工艺类型 220
3.4 电火花加工工艺 220
3.4.1.2 型腔电火花加工 225
3.4.1.3 电火花加工规准 231
3.4.1.4 精密、细微零件电火花加工 235
3.4.2.1 金属材料的热物理性能 239
3.4.2 不同材料电火花加工特点 239
3.4.2.2 其他材料电火花加工特点 240
3.4.3.1 加工精度概念 241
3.4.3 电火花加工精度 241
3.4.3.2 影响电火花加工精度的因素 242
3.4.4.1 电火花加工表面粗糙度 244
3.4.4 电火花加工表面完整性 244
3.4.4.2 电火花加工表层 247
3.4.4.3 电火花加工表层的物理性能 250
3.4.4.4 电火花加工表面缺陷的避免 254
3.4.4.5 电火花加工表面后置处理 255
3.4.5 电火花加工速度和加工稳定性 256
3.4.5.1 电火花加工速度的表示方法 256
3.4.5.2 影响加工速度的因素 257
3.4.5.3 加工稳定性 260
3.5.1 电火花表面强化原理 261
3.5 电火花强化 261
3.5.3.3 强化层的显微硬度 262
3.5.3.2 强化层表面形貌 262
3.5.2 电极材料 262
3.5.3 电火花表面强化层特性 262
3.5.3.1 强化层厚度 262
3.5.3.6 强化层的残余应力 263
3.5.3.5 强化层的耐磨性及耐蚀性 263
3.5.3.4 强化层的红硬性 263
3.5.4 电火花强化工艺 264
3.5.5 影响电火花强化层厚度的因素 265
3.6 电火花磨削 269
3.7.1.1 加工方案 271
3.7.1 整体叶轮叶片电火花加工 271
3.7 电火花加工实例 271
3.7.1.2 电极设计 272
3.7.2 栅网小孔的整体电火花加工 273
3.7.1.3 加工工艺 273
3.7.3.1 航空发动机喷油嘴的加工 274
3.7.3 小孔电火花加工在航空发动机中的应用 274
3.7.3.2 航空发动机叶片等零件小孔加工 275
3.7.4.1 技术要求 276
3.7.4 伞齿轮精锻模电火花加工 276
3.7.5.1 技术要求 277
3.7.5 叶轮注射模电火花加工 277
3.7.4.2 加工要点 277
3.7.6 工艺美术品凹模型腔电火花加工 278
3.7.5.3 加工要点 278
3.7.5.2 加工前准备 278
3.7.8.3 电火花加工方案 279
3.7.8.2 工艺性分析 279
3.7.7 电火花磨削加工实例 279
3.7.7.1 弹簧夹头磨削 279
3.7.7.2 偏心钻套磨削 279
3.7.8 外支承弹性环深窄槽电火花加工 279
3.7.8.1 加工对象 279
3.7.9.3 工艺装备 280
3.7.9.2 工艺性分析 280
3.7.8.4 工艺措施 280
3.7.9 滑油导管深盲孔电火花加工 280
3.7.9.1 加工对象 280
3.8.1 电气安全 281
3.8 生产技术安全 281
3.7.9.4 加工工艺 281
3.7.10 液压伺服阀节流孔电火花加工 281
3.7.10.1 加工对象 281
3.7.10.2 工艺性分析 281
3.7.10.3 工艺措施 281
3.8.2.2 电火花加工中火灾的预防 282
3.8.2.1 电火花加工中火灾产生的条件 282
3.8.2 火灾的防止 282
3.8.3.1 电火花加工中有害气体的产生及组成 284
3.8.3 有害气体及通风净化 284
3.8.2.3 初期火灾的扑灭 284
3.8.3.3 通风净化 285
3.8.3.2 有害气体对人体的危害 285
4.1.1 工作原理、分类及特征 287
4.1 概述 287
第4章 电火花线切割加工 287
4.1.2.2 高速走丝机的“疏松接触式”放电过程 288
4.1.2.1 低速走丝机的放电特点 288
4.1.2 低速走丝机和高速走丝机的加工机理 288
4.1.3 高速走丝和低速走丝线切割对比 289
4.1.5 工艺指标及影响因素 290
4.1.4.2 适用领域 290
4.1.4 工艺特点和适用领域 290
4.1.4.1 工艺特点 290
4.2.2.1 机床的分类 292
4.2.2 机床概况 292
4.2 高速走丝电火花线切割加工 292
4.2.1 工艺特点 292
4.2.2.2 机床型号系列和参数表 293
4.2.3.1 机床主机主要部件的结构 294
4.2.3 机床主机 294
4.2.2.3 机床的组成 294
4.2.3.2 导轮组合件 296
4.2.3.3 机床电器控制 298
4.2.3.4 夹具类型、结构及特点 300
4.2.3.5 附件 301
4.2.4.1 脉冲电源的分类 303
4.2.4 脉冲电源 303
4.2.3.6 机床精度检验要求 303
4.2.4.2 几种波形的参数范围及加工性能 304
4.2.4.3 几种典型脉冲电源电路 306
4.2.4.4 自适应控制脉冲电源 307
4.2.5.1 数控系统的类型 308
4.2.5 数控系统 308
4.2.5.4 微型计算机数控系统(CNC) 309
4.2.5.3 计算机群控系统 309
4.2.5.2 程序控制系统 309
4.2.6.1 机床的使用条件 314
4.2.6 机床的使用条件及其安装要求 314
4.2.7.1 工作液 315
4.2.7 工作液和电极丝 315
4.2.6.2 机床的安装 315
4.2.7.2 电极丝 316
4.2.8.1 工艺指标的评定 318
4.2.8 基本工艺规律 318
4.2.8.2 常用工件材料的种类及加工性 319
4.2.8.3 影响工艺指标的因素 320
4.2.9.1 对工件图纸进行审核与分析 323
4.2.9 加工工艺 323
4.2.9.2 工艺准备 325
4.2.9.3 工件的加工 329
4.2.10.1 编程细则 331
4.2.10 程序编制 331
4.2.10.3 手工编程 332
4.2.10.2 编程前的准备工作 332
4.2.10.4 自动编程 333
4.2.11.3 模具及成形电极加工 348
4.2.11.2 航空零件加工 348
4.2.11 应用实例 348
4.2.11.1 锥度零件的加工 348
4.2.11.4 超厚零件线切割加工 351
4.2.11.6 回转端面曲线型面的加工 353
4.2.11.5 异形孔喷丝板的加工 353
4.3.1 机床概况 354
4.3 低速走丝电火花线切割加工 354
4.3.2.1 机床主机主要部件 355
4.3.2 机床主机 355
4.3.2.2 高精度机床的结构特点 357
4.3.3.1 电源特点 358
4.3.3 脉冲电源 358
4.3.2.3 机床精度检验要求 358
4.3.2.4 主要技术规格 358
4.3.3.2 常用电路形式 360
4.3.3.3 实用电路举例 362
4.3.4.1 系统组成 363
4.3.4 数控系统 363
4.3.4.2 几项通用标准 364
4.3.4.3 计算机数控(CNC)装置 366
4.3.4.4 伺服进给方式 369
4.3.6.1 工作液 372
4.3.6 工作液和电极丝 372
4.3.5 机床的使用条件及其安装要求 372
4.3.5.1 机床的使用条件 372
4.3.5.2 机床的安装 372
4.3.6.2 电极丝 374
4.3.7.2 影响切割速度的因素 376
4.3.7.1 机床的工作精度检验 376
4.3.7 机床的工作精度检验及影响工艺指标的因素 376
4.3.7.3 影响表面粗糙度和表面变质层的因素 377
4.3.7.4 影响加工精度的因素 378
4.3.8.1 加工过程 381
4.3.8 加工工艺 381
4.3.8.2 减少工件材料变形的措施 382
4.3.8.3 多次切割 383
4.3.8.4 加工条件的选择 385
4.3.8.5 锥度切割 391
4.3.8.6 断丝故障和加工缺陷及其解决办法 393
4.3.8.8 断芯的自动处理 395
4.3.8.7 改善表面层质量的其他措施 395
4.3.9.1 ISO代码编程 396
4.3.9 程序编制 396
4.3.9.2 命令词和命令程序 406
4.3.9.3 自动编程 409
4.3.10.1 集成电路引线框架冷冲模 423
4.3.10 应用实例 423
4.3.10.2 高精度粉末冶金模和挤压模 425
4.3.10.3 成形刀具和电火花成形加工用电极 427
4.3.10.4 零件加工 428
4.3.10.5 超行程工件的加工 429
5.1.1 概述 431
5.1 激光加工 431
第5章 高能束加工 431
5.1.1.1 激光的产生 434
5.1.1.2 激光特性 435
5.1.1.3 激光加工原理 437
5.1.1.6 激光加工的应用 441
5.1.1.5 激光加工的分类 441
5.1.1.4 激光加工的特点 441
5.1.2.1 加工设备的组成及功用 443
5.1.2 激光加工设备 443
5.1.2.2 激光器 444
5.1.2.3 主光路 447
5.1.2.4 机床本体 450
5.1.2.5 辅助系统 453
5.1.2.6 国内外激光加工设备举例 456
5.1.3 激光加工工艺 459
5.1.3.1 激光打孔工艺 460
5.1.3.2 激光切割工艺 476
5.1.3.3 激光表面改性工艺 495
5.1.4.1 激光打孔应用实例 502
5.1.4 激光加工应用实例 502
5.1.4.2 激光切割应用实例 508
5.1.5 安全与防护 512
5.1.5.1 激光的危害 512
5.1.5.2 安全防护 514
5.2.1.1 电子束加工的基本原理 517
5.2.1 概述 517
5.2 电子束加工 517
5.2.2 电子束加工设备 518
5.2.1.3 电子束加工的特点和应用 518
5.2.1.2 电子束加工的分类 518
5.2.2.2 电子束打孔机 520
5.2.2.1 电子束焊机 520
5.2.2.3 电子束曝光机 524
5.2.2.6 电子束加工设备的维护和保养 527
5.2.2.5 电子束加工设备常用故障及产生原因 527
5.2.2.4 电子束铣切机 527
5.2.3.2 电子束打孔 530
5.2.3.1 电子束焊接(参见《焊接》分册) 530
5.2.3 各种电子束加工方法及工艺特点 530
5.2.3.3 电子束表面改性处理 535
5.2.3.4 电子束熔炼 538
5.2.3.5 电子束曝光 539
5.2.3.6 电子束铣切 548
5.2.3.7 电子束镀膜 549
5.2.3.8 电子束加工中的缺陷及产生的原因 550
5.2.4.2 化纤喷丝头打孔 551
5.2.4.1 喷气发动机燃烧室罩打孔 551
5.2.4 电子束加工应用实例 551
5.2.4.4 电子束表面熔化处理应用实例 552
5.2.4.3 人造革打透气孔 552
5.2.5 电子束安全防护 553
5.2.4.5 带材的电子束退火 553
5.3.1 等离子喷涂原理、分类及特点 554
5.3 等离子喷涂技术 554
5.3.2.2 喷枪 555
5.3.2.1 等离子喷涂设备的组成 555
5.3.2 等离子喷涂设备 555
5.3.2.3 送粉器 556
5.3.2.4 直流电源 557
5.3.2.5 控制系统(控制柜) 558
5.3.3.1 等离子喷涂粉末材料的要求 559
5.3.3 粉末材料 559
5.3.2.6 热交换器 559
5.3.3.2 粉末材料的发展 560
5.3.3.4 几类粉末材料的熔点、密度和显微硬度 561
5.3.3.3 MMoCrSi和MCrAIY粉末的化学成分 561
5.3.3.5 粉末材料的质量保证 562
5.3.4.2 除油工序 563
5.3.4.1 凹切工序 563
5.3.4 等离子喷涂工艺流程 563
5.3.4.5 等离子喷涂工序 564
5.3.4.4 预热工序 564
5.3.4.3 表面粗化(喷砂)工序 564
5.3.5.2 等离子喷涂的工艺参数选择 565
5.3.5.1 等离子喷涂过程的重要参数 565
5.3.4.6 涂层加工工序 565
5.3.5 等离子喷涂工艺参数 565
5.3.6.2 涂层性能及测试 567
5.3.6.1 涂层性能分类 567
5.3.5.3 等离子喷涂常用材料的工艺参数表 567
5.3.6 等离子喷涂涂层性能与质量控制 567
5.3.6.3 涂层质量的控制 575
5.3.7.1 真空等离子喷涂(VPS)技术 576
5.3.7 等离子喷涂新技术 576
5.3.7.3 水等离子喷涂 578
5.3.7.2 惰性气氛等离子喷涂 578
5.3.8.1 涂层应用范围及经济技术效益 579
5.3.8 等离子喷涂涂层应用 579
5.3.8.2 等离子喷涂涂层分类及其典型应用 580
5.3.8.3 涂层的去除 585
5.3.9 等离子喷涂常见故障及排除方法 586
5.4.1.1 等离子弧焊接的原理、分类和特点 587
5.4.1 等离子弧焊接 587
5.4 等离子弧焊接与切割 587
5.4.1.2 等离子弧焊接设备 588
5.4.1.3 等离子弧焊接工艺 592
5.4.2.1 等离子弧切割的原理及特点 594
5.4.2 等离子弧切割 594
5.4.2.2 等离子弧切割设备 595
5.4.2.3 等离子弧切割工艺 597
6.1.3.1 化学铣切加工的特点 600
6.1.3 化学铣切加工的基本特征 600
第6章 化学铣切加工 600
6.1 概述 600
6.1.1 化学铣切加工的基本原理 600
6.1.2 化学铣切加工的分类 600
6.1.4 化学铣切加工的常用术语 601
6.1.3.2 化学铣切加工的优点及局限性 601
6.2.1.4 测试设备 602
6.2.1.3 刻型设备 602
6.2 化学铣切加工设备及工装 602
6.2.1 化学铣切加工设备 602
6.2.1.1 溶液槽 602
6.2.1.2 涂敷保护涂料的设备和固化设备 602
6.2.2.2 化铣样板的设计和制造标准 605
6.2.2.1 化学铣切样板 605
6.2.2 化学铣切加工工装 605
6.2.2.3 样板侧向腐蚀量的计算 606
6.3.2 铝及铝合金化学铣切加工的一般要求 609
6.3.1 铝及铝合金化学铣切加工的分类 609
6.3 铝及铝合金的化学铣切 609
6.3.3.1 清洁处理 610
6.3.3 铝合金化学铣切加工工艺 610
6.3.3.2 涂敷保护涂料并固化 613
6.3.3.3 刻型 614
6.3.3.4 化学铣切加工 615
6.3.3.6 去除保护涂层 619
6.3.3.5 去污处理 619
6.3.4 铝合金化学铣切缺陷及排除方法 620
6.3.5 提高铝合金化学铣切加工表面质量的途径 622
6.3.6 影响铝合金化学铣切加工的主要因素和加工疵病产生的原因及其预防措施 623
6.3.7 化学铣切加工对铝合金机械性能的影响 626
6.4.1 不锈钢和镍基合金化学铣切加工工艺 629
6.4 其他金属材料的化学铣切加工工艺 629
6.4.2 钛合金化学铣切加工工艺 631
6.4.3 其他合金的化学铣切腐蚀加工工艺规范 633
6.5 化学铣切保护涂料 634
6.6.1 去除结构中的废重 635
6.6 化学铣切加工在航空航天工业中的应用 635
6.6.2 化学铣切加工在整体结构中的应用 637
6.6.4 用于铣切难于机械加工的材料 639
6.6.3 加工锥度工件 639
6.7.1 人身技术安全 640
6.7 技术安全 640
6.6.5 化学铣切加工在挤压型材上的应用 640
6.7.3 腐蚀溶液再生技术的应用 642
6.7.2 烟雾的处理 642
6.7.4 腐蚀溶液的中和处理 644
7.1.1.2 工艺特点及应用 646
7.1.1.1 加工原理 646
第7章 其他特种加工 646
7.1 磨粒流加工工艺及设备 646
7.1.1 概述 646
7.1.2.1 加工设备 648
7.1.2 加工设备、磨流介质和夹具(限制器) 648
7.1.2.2 磨流介质 651
7.1.2.3 夹具(限制器) 652
7.1.3.1 磨流介质参数的选择 656
7.1.3 工艺参数选择指南 656
7.1.3.2 挤压力的合理选择 659
7.1.3.4 加工参数选择实例 662
7.1.3.3 其他影响因素 662
7.1.3.5 机床故障与加工缺陷分析 663
7.1.4 磨粒流加工后的表面质量 665
7.1.5 磨粒流工艺应用实例 666
7.2.1.1 纯水射流切割原理 672
7.2.1 纯水射流切割原理、工艺特点及应用 672
7.2 高压水射流切割技术 672
7.2.1.2 纯水射流切割工艺特性 674
7.2.1.3 纯水射流切割的应用 676
7.2.2.1 磨料水射流切割原理 678
7.2.2 磨料水射流切割原理、切割参数及应用 678
7.2.2.2 影响水射流切割质量的因素 681
7.2.2.3 磨料水射流切割的应用 685
7.2.3.1 纯水射流切割系统的组成 689
7.2.3 高压水射流切割系统 689
7.2.3.2 磨料水射流切割系统 691
7.2.3.3 高压水射流切割机 692
7.2.4.1 高压水射流的发展概况 696
流 696
7.2.4 高压水射流技术的发展和新型射 696
7.2.4.2 新型射流 697
7.2.4.3 高压水射流技术的应用前景 699
7.3.1.1 加工原理 700
7.3.1 概述 700
7.3 光化学加工 700
7.3.1.3 分类及应用范围 701
7.3.1.2 工艺特点 701
7.3.2 光化学加工主要工艺过程及要点 702
7.3.2.1 掩膜版制作 703
7.3.2.3 抗蚀层制作方法 707
7.3.2.2 零件表面预处理 707
7.3.2.4 化学腐蚀与电成形 716
7.3.3 光化学加工应用实例 724
7.3.2.5 除胶 724
参考文献 731