图书介绍
全面现场改善pdf电子书版本下载
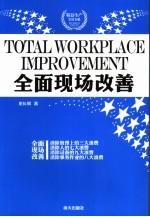
- 史长银著 著
- 出版社: 深圳:海天出版社
- ISBN:7806977600
- 出版时间:2006
- 标注页数:283页
- 文件大小:21MB
- 文件页数:304页
- 主题词:制造工业-工业企业管理:生产管理
PDF下载
下载说明
全面现场改善PDF格式电子书版下载
下载的文件为RAR压缩包。需要使用解压软件进行解压得到PDF格式图书。建议使用BT下载工具Free Download Manager进行下载,简称FDM(免费,没有广告,支持多平台)。本站资源全部打包为BT种子。所以需要使用专业的BT下载软件进行下载。如 BitComet qBittorrent uTorrent等BT下载工具。迅雷目前由于本站不是热门资源。不推荐使用!后期资源热门了。安装了迅雷也可以迅雷进行下载!
(文件页数 要大于 标注页数,上中下等多册电子书除外)
注意:本站所有压缩包均有解压码: 点击下载压缩包解压工具
图书目录
第一章 现场改善基础 1
一、现场改善概述 2
1.什么是现场改善 2
2.改善和管理的区别 2
3.现场改善的要点 4
4.现场改善的作用 5
二、现场改善的内容 6
1.材料存放和搬运 6
3.现场工作改善 7
2.生产线工位合理设置 7
4.作业流程改善 8
5.工厂物流改善 8
6.现场质量与交期改善 9
7.现场成本改善 10
8.现场安全与作业环境改善 10
9.现场管理者能力改善 11
第二章 物料存放与搬运 12
一、选择最佳的方法存放物料 13
1.物料存放与搬运对生产的影响 13
2.从工作区清走不常使用的东西 13
3.不要将物料直接放在地面上 16
4.使用多功能存放架存放工件和产品 17
二、尽量减少和缩短搬运工序 24
1.将使用频繁的物品就近放置 24
2.尽量使用可移动的存放器具 26
3.让工具动起来 30
三、合理地搬运物料 31
1.防止无效搬运 31
2.充分利用重力进行少消耗的搬运 31
4.提高物料的搬运活性和搬运速度 32
3.充分利用机械实现“集装搬运” 32
5.选择最好的方式节省体力消耗 33
四、减少并有效地进行起重操作 34
1.起重物体时别超过必要的高度 34
2.在适当的高度范围内移动物料 35
第三章 生产线工位合理设置 37
一、改善工作台布置使物料、工具更方便拿取 38
1.工人站立和坐下能够触及的合适距离 38
2.工作台上的工具摆放 40
3.几种合理的工作台操作实例 42
1.作业方法标准化改善的着眼点 45
二、开展作业方法标准化的改善 45
2.作业动作标准化改善方法 46
3.作业流程标准化改善方法 52
4.作业工序活性化设置方法 53
三、使用各种省力工具和方法来移动工件 54
1.固定加工件提高效率 54
2.现场作业中几个省力的方法 54
四、彻底消除现场操作失误造成的损失 55
1.杜绝现场误操作从细节着眼 55
2.消除现场误操作的几种方法 55
第四章 现场工作改善 59
一、带着怀疑的眼光重新审视每一天的工作 60
1.形成认真执行每一项工作的现场作业氛围 60
2.把握合理安排现场工作的原则 61
3.养成按计划做事的习惯 61
二、从作业的整体时间上进行改善 63
1.产品制造时间 63
2.从作业速度上开始改善 65
三、降低标准作业时间 66
1.标准作业时间的内容 66
2.标准作业时间的计算 67
1.灵活使用每日作业实绩表 68
2.现场巡查的方法 68
四、带上工具与问题巡查现场 68
3.现场巡查的项目内容 69
4.现场巡查必带的七种工具 71
五、提升员工工作改善的能力 72
1.培养员工的动手能力 72
2.员工工作改善能力培养的五个内容 74
第五章 作业流程改善 76
2.制造作业流程的管理方法 77
一、制造作业流程改善 77
1.什么是制造作业流程 77
3.工作程序要明确 79
4.日程计划管理 80
5.突发赶工作业应对方法 83
二、细分作业工序设定作业目标 84
1.使用工作项目分配表 84
2.给每一个作业员工设定作业目标 85
三、利用各种创意方法改善作业流程 85
2.“逆向思维”型 86
1.合并重组型 86
3.创意活动要领 87
4.创意改善活动的新方法 88
第六章 工厂物流改善 92
一、工厂物流的定义及分类 93
1.工厂物流的定义 93
2.工厂物流的分类 93
3.经济批量采购法 94
2.转移库存法 94
1.采购供应物流的定义 94
二、工厂采购供应物流 94
4.订货点采购法 97
5.定期订货采购法 98
6.建立采购的准时供应体制 98
7.建立采购的及时供应体制 100
8.采购作业的六“适”原则 101
9.采购过程导致供货周期延长的四个原因 102
三、工厂仓库保管物流 103
1.工厂仓库保管的定义 103
2.工厂储存保管的作用 104
3.工厂仓库管理的八个薄弱环节 105
4.零库存管理方法 109
5.物料入库管理方法 110
6.物料在库管理方法 112
7.物料出库管理方法 114
8.仓库呆废料的处理方法 115
9.低减库存的ABC法 116
四、工厂装卸搬运物流 117
1.工厂装卸搬运的定义 117
2.工厂发生装卸搬运的场所及改善方法 118
3.工厂不合理装卸搬运产生的原因 119
4.搬运费用全面调查 120
5.制定工厂装卸搬运操作细则 125
五、工厂生产物流 128
1.生产物流的定义 128
2.生产物流的特点 129
3.生产物流的改善方法 130
六、工厂回收与废弃物物流 133
1.回收与废弃物物流的定义 133
2.回收与废弃物物流的改善方法 134
1.工厂物流成本构成及改善方法 135
七、工厂物流成本改善 135
2.工厂物流成本管理的盲点 138
3.工厂物流成本改善的10/17法 139
第七章 现场质量与交期改善 140
一、品质改善的定义及作用 141
1.品质改善的定义 141
2.品质改善的作用 141
3.开展品质改善的要点 143
二、现场发生不良的因素 144
1.生产机器与设备出现异常 144
2.原材料品质不稳或变化 145
3.作业方法的变化 146
4.作业员工技能水平 147
5.作业环境的不适合 147
6.管理上的不科学 147
三、防止现场不良发生的方法 148
1.要求品质稳定先求人员稳定 148
2.建立品质管理的标准化体系 149
3.现场品质改善的SQC(统计品质管理)活动 150
4.不要常换原料的供应商 150
5.建立机器设备的自主保全制度 151
6.彻底消除现场作业环境的脏乱现象 153
1.QCC(品管圈)活动 154
四、全面品质改善的方法 154
2.品质不良原因查核表 155
3.品质不良分析柏拉图 156
4.品质不良要因改善鱼骨图 157
5.生产不良推移图揭示 158
6.不良品发生率实物展示 159
五、交期改善的定义及作用 160
1.交期改善的定义 160
六、现场导致交期延迟的因素 161
1.工序物流不畅 161
3.开展交期改善的要点 161
2.交期改善的作用 161
2.生产计划不周全 162
3.生产进度不明确 162
4.交期监督不力 163
七、防止交期延误的方法 163
1.让物料流动起来 163
2.编制生产大中小日程计划 164
3.及时跟进生产进度 165
1.改善生产中的瓶颈工序 166
八、现场交期改善的方法 166
4.每天最少巡场三次 166
2.提高基层作业员工的交期意识 167
3.交期延误责任到人 167
4.改善生产中的“等待” 167
5.交期改善“舍卒保帅”法 168
6.交期改善需要的干劲与行动 169
第八章 成本改善与消除现场27大浪费 170
1.成本改善的定义 171
一、成本改善的定义及作用 171
2.成本改善的作用 172
二、成本改善的方法 173
1.改进工作质量低减成本 173
2.提高生产力低减成本 173
3.降低库存低减成本 175
4.压缩生产工序低减成本 175
5.减少设备停机时间节省成本 175
6.缩短交货期降低成本 175
1.因设备故障产生的浪费 176
2.段取调整产生的浪费 176
三、消除设备的9大浪费现象 176
3.品质故障产生的浪费 177
4.物流浪费 178
5.治工具切换浪费 178
6.设备启动产生的浪费 179
7.设备点点停导致的浪费 180
8.速度低下造成的浪费 181
9.不良废弃的浪费 181
2.作业员动作上的浪费 182
1.停止等待产生的浪费 182
四、改善作业人员的7大浪费 182
3.生产布局不合理产生的浪费 183
4.作业编排不均衡导致的浪费 184
5.作业标准不适当产生的浪费 184
6.不良品修理产生的浪费 185
7.人员违纪导致的浪费 185
五、管理上的3大浪费 186
1.非生产浪费 186
2.管理停止的浪费 186
六、消除事务作业的8大浪费 187
1.事务管理上的浪费 187
3.实施计划产生的浪费 187
2.作业流程上的浪费 188
3.业务效率上的浪费 188
4.物流布局上的浪费 188
5.作业动作上的浪费 189
6.员工作业熟练度上的浪费 189
7.业务调整的浪费 190
8.作业不良的浪费 190
9.改善事务浪费的MK卷纸分析法 190
第九章 现场安全与作业环境改善 197
一、现场安全改善的定义及作用 198
1.现场安全改善的定义 198
2.现场安全改善的要点 198
3.现场安全改善的作用 198
4.现场安全改善的范围 199
二、设备安全改善方法 200
1.机械外部表面安全化 200
2.设备构造部分安全化 201
3.机械性能安全化 201
4.设备操作安全化 202
5.保养修理安全化 203
6.安全装置的安全化 204
7.设备安全检查方法 205
三、作业安全改善方法 208
1.现场作业引发安全事故原因分析 208
2.制定现场安全作业标准 208
3.明确现场管理者的安全管理职责 209
四、开展现场无事故活动的改善 211
1.现场无事故活动的定义及作用 211
2.现场无事故活动的三大原则 212
4.现场无事故活动改善的指差呼称法 213
3.现场无事故活动的三大支柱 213
五、作业环境改善方法 214
1.推行5S活动 214
2.明确现场清扫对象和清扫基准 217
3.开展每日三分钟5S活动 220
4.改善作业环境的CLEAN-UP作战法 221
5.CLEAN-UPⅠ—干净 222
6.CLEAN-UPⅡ—整齐 223
7.CLEAN-UPⅢ—完好 224
第十章 现场管理者能力改善 225
2.现场管理者到底要干些什么 226
1.那些人才是现场管理者 226
一、现场管理者的定位及职责 226
二、现场管理者的X和Y理论 229
1.具有X意识的现场管理者 229
2.具有Y意识的现场管理者 229
三、现场管理者的三种类型 231
1.王爷型的现场管理者 231
2.单纯勤劳型的现场管理者 231
四、现场管理者必须掌握的三种技能 232
1.让属下心服的作业技能 232
3.例外管理型的现场管理者 232
2.提高效率的管理技能 233
3.凝聚团队的人际技能 234
五、现场管理者能力改善的方法 234
1.不断地学习培养灵活的思考能力 234
2.以企业经营者的态度工作 236
3.必须掌握一定的统计方法 237
4.先有计划再去做 238
5.合理安排工作的技巧 240
6.控制工作内容和速度的能力 240
7.正确指导员工的方法 240
第十一章 全面现场改善的思路与方法 243
1.改善提案制度的定义及作用 244
2.改善提案对员工的八大效果 244
一、改善提案制度 244
3.改善提案对企业的八大效果 245
4.现场管理者在改善提案中的任务 246
5.优秀改善提案的标准 246
6.改善提案的范围 246
1.勤用大脑 247
2.先从意识上进行革新 247
二、全面现场改善的思路 247
3.必须热爱自己所从事的工作 248
4.从进步中寻求创意 249
5.培养独立思考的能力 249
6.从细小浪费不合理处开始改善 250
三、全面现场改善的方法 250
1.第一步:现状把握 251
2.第二步:设定目标 254
3.第三步:要因解析 255
4.第四步:研讨对策 256
5.第五步:计划实施 257
6.第六步:效果确认 258
7.第七步:效果巩固 259
第十二章 全面现场改善推行步骤 261
一、全面现场改善推行六大步骤简介 262
1.改善的着眼点 262
2.现状调查 262
3.改善构想的整合 262
4.做成改善方案 262
5.实施改善方案 262
1.带着问题看现状 263
2.从作业中的无序和混乱处着眼 263
二、第一步:寻找改善着眼点 263
6.确认改善效果 263
3.对现场4M进行彻底的检查 264
三、第二步:现状调查 265
1.从不同的角度观察现场工作 265
2.尽量将问题细化、量化、层次化 266
3.使用5W2H手法调查作业效率 267
4.分析作业流程内容的IE手法 268
5.利用QC手法分析现状 272
2.只处理变化的部分 278
1.从相反的角度看现状 278
四、第三步:改善构想的整合 278
3.适当的组合与分离 279
4.适当的集中与分散 279
5.对问题放大或缩小 279
6.调换作业的顺序看一看 279
7.找到共同点与差异点 279
2.做好事前的准备工作 280
1.寻求上司的支持与认可 280
五、第五步:实施改善方案 280
10.能否附加或剔除 280
9.能否排除 280
8.看看能不能代替 280
3.规定每个人的工作内容 281
4.制订改善实施日程计划表 281
5.实施过程中出现的问题及时处理 281
6.接受上司及下属的建议 282
六、第六步:确认改善效果 282
1.确认的目的是为了发掘新的改善 282
2.发掘新改善的方法 282
3.发掘新改善的步骤 283